What is Warehouse Management: The Definitive Guide
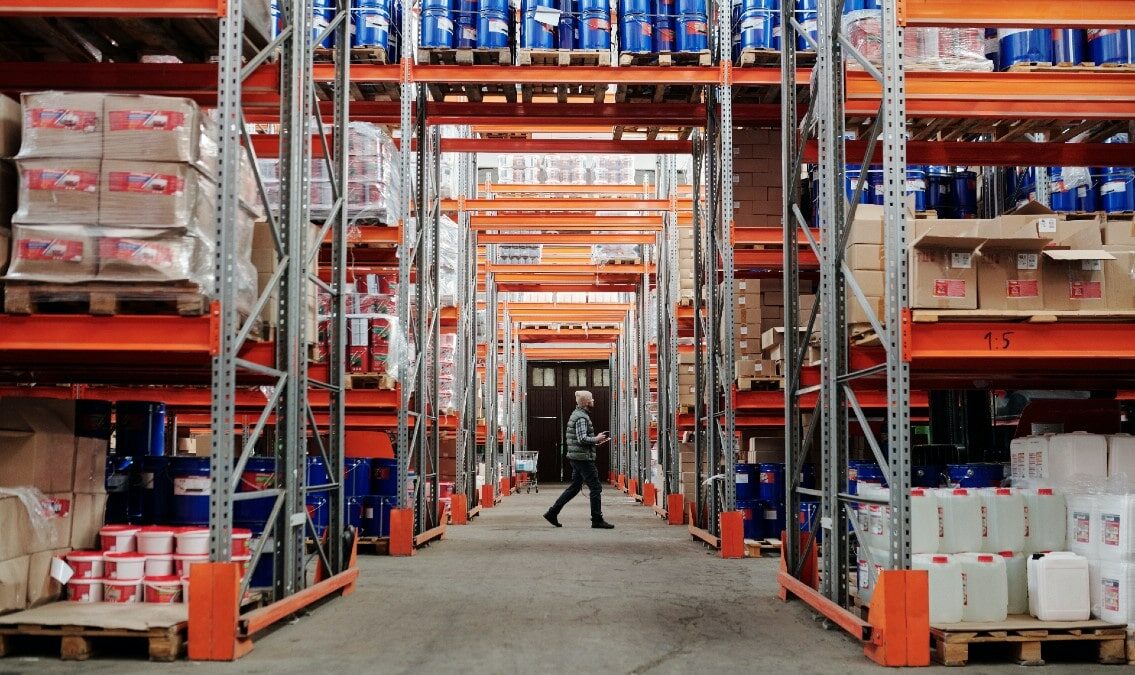
Warehouse management is a crucial aspect of any business that deals with inventory. Efficient warehouse management can lead to increased productivity, profitability, and customer satisfaction. However, poor warehouse management can result in wasted time, money, and resources.
In this guide, we’ll discuss the importance of effective warehouse management, key warehouse management processes and challenges, digital transformation in the warehousing industry, and warehouse management technologies that can optimize your warehouse operations.
Warehouse management is the process of efficiently controlling and overseeing all operations within a warehouse, including receiving, storing, and distributing goods while optimizing space, labor, and resource utilization. All warehouse processes and functions must work together seamlessly to ensure effective and efficient operations.
The goal of warehouse management is to ensure that goods are stored safely and efficiently, inventory is accurately tracked, and orders are fulfilled promptly and accurately, contributing to overall supply chain effectiveness.
Effective warehouse management not only supports day-to-day operations but also contributes to the strategic success of the entire supply chain, impacting everything from inventory accuracy and customer satisfaction to operational costs and compliance.
The primary role of a warehouse is to provide storage space for goods and materials, and the need for warehouse space is growing. In fact, 87% of decision-makers in warehousing, logistics, and retail are in the process of, or planning to expand warehouses by 2024.
Efficient warehouse management ensures goods are stored in a way that maximizes space utilization, minimizes storage costs, and keeps inventory organized. It involves tracking inventory levels, orders, and deliveries in real-time, which can reduce the chances of overstocking or stockouts. In turn, this contributes to improved inventory accuracy, reduced holding costs, and faster order fulfillment.
A well-organized warehouse can more easily adapt to changes in demand, inventory levels, and processing technologies, which supports business growth and the ability to respond to market changes or expansion opportunities.
Warehouse management is complex, involving various processes, considerations, and variables that must work together seamlessly to ensure efficient operations. Let’s examine the key elements of effective warehouse management.
Effective inventory management leads to streamlined warehouse operations, reducing the time and effort required to receive, store, and retrieve goods and preventing costly errors. As a result, orders are fulfilled faster, and employees are more productive because they spend less time managing overstock or locating items.
Proper warehouse inventory management also helps minimize the costs associated with overstocking and understocking. By maintaining optimal inventory levels, businesses can reduce holding costs, including storage, insurance, and taxes, and also minimize losses from expired or obsolete stock.
Warehouses typically use one of two primary inventory control methods and one (or more) of several inventory management methods. Inventory control can be either perpetual or periodic:
To support these inventory control methods, warehouses use a variety of inventory management strategies to ensure that the right products are in stock at the right time.
Strategy | Key Features |
---|---|
Just-In-Time (JIT) Inventory |
|
First-In, First-Out (FIFO) |
|
Last-In, First-Out (LIFO) |
|
Economic Order Quantity (EOQ) |
|
Some of the most common inventory management strategies include:
By optimizing the use of available space, businesses can store more items efficiently within the same square footage. This is especially important for companies with a large variety of inventory or those experiencing growth in product demand.
Effective space utilization strategies, such as high-density storage solutions, can significantly increase warehouse capacity without the need for physical expansion.
Optimized warehouse space utilization also helps create safer working environments by reducing clutter and ensuring clear pathways. This not only minimizes the risk of accidents but also reduces the likelihood of product damage due to improper storage or handling.
In addition to maximizing the use of available space, a warehouse’s layout and design can significantly impact its efficiency and productivity. An optimal warehouse layout and thoughtful design impact virtually every aspect of warehousing, from inventory management to order fulfillment processes.
Factors to consider when setting up a warehouse include the location of storage areas, aisle width, shelving systems, and workflow patterns to reduce travel time and improve order fulfillment efficiency. A logical, systematic organization of inventory supports better tracking and management, reducing errors, and improving accuracy. This leads to better inventory visibility, making it easier to manage stock levels, reorder points, and identify discrepancies.
Clear pathways, properly marked and sufficiently wide aisles, and the thoughtful placement of emergency exits and safety equipment contribute to a safer working environment. This not only helps in preventing accidents but also ensures compliance with safety regulations.
Advancements in technology and warehouse automation have revolutionized warehouse management. Implementing barcode systems, RFID technology, automated storage and retrieval systems, and WMS software can enhance inventory accuracy, increase efficiency, and reduce operational costs.
Effective inventory management is crucial for optimizing storage space and ensuring the timely fulfillment of orders. Advanced WMS and inventory management technologies, paired with technologies like barcode scanners and RFID, provide real-time visibility into inventory levels, movements, and trends. This enables more accurate forecasting, reduces the risk of stockouts or overstocking, and allows for more precise demand planning.
These technologies also improve the accuracy of inventory tracking, order picking, and replenishment tasks. By automating data capture and processing, they reduce the likelihood of human error, which can lead to order inaccuracies, returns, and customer dissatisfaction.
Automation technologies, such as robotic picking systems, automated conveyors, and sortation systems, significantly speed up the processing of goods through the warehouse. These systems can operate around the clock, handling tasks at a speed and consistency unmatched by human labor, thus increasing overall productivity.
Smart warehouse technologies also streamline the order fulfillment process, from picking and packing to shipping and returns. For example, automated warehouse systems can select the optimal routes and methods for picking, while technology-driven sorting systems ensure that orders are accurately assembled and dispatched. This not only speeds up order processing but also improves customer satisfaction with timely deliveries.
These benefits have a direct impact on profitability. In fact, companies that are able to process orders in under 30 minutes are 1.67 times more likely to demonstrate 50%+ profitability growth.
Labor costs are one of the largest expenses in warehouse operations. In fact, 70% of 3PLs reported an increase in labor costs in 2023, but despite rising costs, 64% indicated they plan to expand their workforce in the coming year.
Based on data from Extensiv
These costs can be better controlled through effective labor management, such as reducing overtime expenses by balancing workloads more evenly and improving the efficiency of employees to reduce the need for hiring temporary staff.
Additionally, understanding and optimizing the factors that affect labor costs can lead to more strategic decisions regarding staffing and operational design. Fortunately, there are numerous strategies that can help improve labor management practices in the warehouse setting, such as:
Some of the benefits of effective labor management include:
Implementing demand forecasting tools and techniques can help warehouses respond proactively to changing market conditions and customer demands, and it can significantly impact other warehouse management processes.
By analyzing historical sales data, market trends, and customer demand patterns, warehouses can better anticipate inventory needs and adjust stocking levels accordingly. This helps ensure that the right amount of inventory is kept on hand to meet customer demand without overstocking, which ties up capital and increases storage costs, or understocking, which can lead to stockouts and lost sales.
It enables a balance between carrying costs and the cost of missing sales opportunities due to a lack of inventory. By anticipating high-demand periods, companies can optimize the warehouse layout and organization to accommodate an influx of inventory or adjust storage for slow-moving items.
Demand forecasting also influences labor planning and allocation. By predicting busy periods, warehouse managers can schedule the right number of workers to handle increased volumes, ensuring productivity and service levels are maintained without incurring unnecessary labor costs during slower periods.
Ultimately, the goal of warehouse management is to meet customer demands and expectations. By prioritizing customer satisfaction, warehouses can build loyalty, improve retention rates, and enhance their reputation in the market.
Maintaining a safe working environment and ensuring compliance with regulatory requirements are essential aspects of warehouse management. Accidents and incidents in the warehouse can lead to significant operational disruptions, affecting productivity and the ability to meet customer demands.
By prioritizing safety and compliance, warehouses can minimize the occurrence of such disruptions, ensuring smoother, more reliable operations. Implementing safety protocols, displaying proper warehouse safety signage, conducting regular inspections, and providing proper training on equipment operation and handling hazardous materials can help prevent accidents and injuries.
Additionally, warehouses must adhere to industry regulations and standards to avoid fines, penalties, and legal risks. These local, national, and international regulations are designed to ensure safe and fair working conditions and cover aspects such as occupational health and safety, hazardous materials handling, fire safety, and labor practices.
Accidents and non-compliance can be costly, leading to medical expenses, legal fees, compensation claims, fines or penalties, and increased insurance premiums. Proactively managing safety and compliance helps minimize these costs, contributing to the financial health of the business.
Providing accurate and timely order fulfillment, offering flexible delivery options, and ensuring product quality can help warehouses exceed customer expectations and drive business growth.
Because warehouse management is complex, there are many challenges and obstacles that can hinder your operations. Here’s a look at the most common warehouse management challenges and how to overcome them.
External factors such as global pandemics, natural disasters, geopolitical tensions, and trade disputes can lead to supply chain disruptions, impacting warehouse operations, efficiency, and the ability to meet customer demand.
Disruptions can lead to unexpected shortages or surpluses of products, making inventory management more complex. Warehouses may struggle with overstocking due to canceled orders or delays in production, or understocking because of interrupted supplies, affecting their ability to fulfill customer orders.
Significantly increased lead times for receiving goods are also a common consequence of supply chain disruptions. This affects the warehouse’s ability to replenish stock in a timely manner, impacting order fulfillment and customer satisfaction. Extended lead times can also complicate the management of perishable goods or items with a short shelf life.
Additionally, supply chain disruptions often lead to unpredictable changes in consumer demand. Warehouses may find it challenging to forecast demand accurately, leading to difficulties in inventory control. This unpredictability can result in stockouts of high-demand items or excess inventory of others.
Managing these disruptions requires flexibility, robust contingency planning, and effective communication with suppliers and logistics partners. The ability to rapidly adjust operations, adopt contingency plans, and invest in technologies and processes that enhance flexibility are also helpful in mitigating the impact of supply chain disruptions.
Based on data from Kardex
The skills gap in warehouse management refers to the disparity between the skills that employers need and the skills that the available workforce possesses. This gap has become increasingly prominent with the rapid advancement of technology and the evolving landscape of the supply chain industry.
However, finding candidates with the right mix of technical know-how, experience in modern warehousing operations, and soft skills (such as problem-solving and adaptability) can be difficult and competitive.
Without the necessary skills, employees may struggle to perform their roles effectively, leading to reduced productivity and efficiency. Mistakes and slower processing times can become more common, affecting order fulfillment rates, inventory accuracy, and overall service levels. A workforce that lacks the skills to operate equipment correctly or follow modern safety practices can also lead to an increased risk of accidents and injuries.
A skills gap can also make it challenging to implement and optimize new technologies such as robotics, automation, and artificial intelligence if employees lack the expertise to operate new systems or adapt to new processes.
To bridge the skills gap, companies often need to invest more in training and development programs. While necessary, these programs can be costly and time-consuming. They also require an ongoing commitment to keep staff updated with the latest technologies and practices, diverting resources from other operational areas.
Low visibility in warehouse operations refers to the lack of transparency and real-time information regarding the movement, status, and location of goods within the warehouse and throughout the supply chain. This lack of visibility can stem from several factors, including outdated technology, manual processes, disjointed systems, and the absence of integrated software solutions.
Without clear visibility, tracking inventory levels accurately is challenging, leading to discrepancies between physical stock and inventory records. This can result in overstocking, stockouts, increased carrying costs, and inaccurate demand forecasting.
Coordinating the receiving, storing, picking, and shipping processes also becomes cumbersome and prone to errors, slowing down operations and increasing the likelihood of mistakes, such as incorrect shipments or delays.
Inefficiencies created by a lack of visibility result in additional costs, such as:
Improving visibility in warehouse management involves investing in modern technology solutions such as warehouse management systems (WMS), adopting barcode or RFID tracking, integrating systems across the supply chain, and leveraging data analytics for better decision-making. Enhanced visibility enables warehouses to operate more efficiently, improve customer service, reduce costs, and adapt more quickly to changes in the marketplace.
Based on data from Kardex
Process delays in warehousing refer to any slowdown or interruption in the standard operational workflows, from receiving goods at the warehouse to storing, picking, packing, and finally shipping them to the destination.
These delays can stem from various sources, including manual handling errors, equipment failures, inefficient layout and organization, poor inventory management, and inadequate technology support.
Process delays can lead to other challenges, such as:
Mitigating process delays requires a comprehensive approach, including the adoption of technology solutions like warehouse management systems (WMS), process automation, optimizing warehouse layout and workflows, performing regular equipment maintenance, and ongoing training and development of staff.
Damaged products can affect operational efficiency, financial performance, and customer satisfaction. For instance, damaged goods can impact inventory levels and accuracy, further complicating inventory management. Inventory records must be adjusted to account for damaged products, which can be time-consuming and lead to stockouts or overstocking of other items.
Handling damaged products also increases labor costs, as workers spend time identifying, documenting, and moving damaged goods to a designated area. There are also costs associated with disposing of or attempting to salvage damaged products, as well as the cost of replacing these goods to maintain inventory levels.
Another consequence of damaged products is increased returns, which requires an efficient reverse logistics process. Handling returns, assessing the damage, and deciding on the appropriate action (e.g., repair, replace, scrap) require additional resources and can strain the warehouse operations.
Managing damaged goods effectively requires careful handling, tracking, and decision-making. Strategies such as improving packaging, enhancing employee training on handling goods, adopting technology for better inventory and warehouse management, and establishing clear procedures for dealing with damaged goods can help minimize these challenges.
Controlling warehouse operational costs, such as labor, energy, equipment, and technology investments, while maintaining high levels of efficiency and service is a prominent warehouse management challenge. Every facet of warehouse management can impact costs, including the challenges discussed above, making it crucial to continuously seek ways to optimize operations and reduce waste.
There are a variety of strategies that can help to control warehouse costs, such as:
By focusing on efficiency and strategic planning, warehouses can manage and even reduce operational costs while maintaining or improving service levels.
Optimizing your warehouse operations requires strategic planning. Follow these steps to develop and implement an effective warehouse management plan.
By implementing barcodes in your warehouse, you can track inventory levels in real-time, automate data entry processes, and improve order fulfillment accuracy.
Warehouse signs such as Camcode’s Hanging Retro-Reflective Bar Code Labels can be scanned from distances over 50 feet with long-range scanners, allowing workers to easily scan signs and identify key areas from forklifts and other equipment, while Warehouse Aisle Signs provide the ideal solution for identifying rack and shelf ends.
Based on data from Grandview Research
Digital transformation involves the integration of digital technologies into all areas of warehouse operations, and it’s well underway in the warehouse sector. In fact, the global warehouse management systems (WMS) market size was valued at $3.94 billion in 2023 and is expected to expand at a CAGR of 19.5% from 2024 to 2030, and 80% of organizations in warehousing, logistics, and retail are planning to invest in new technologies to stay competitive.
Digital transformation includes a variety of technology solutions, including:
Digital transformation offers myriad benefits, from increasing operational efficiency to improving decision-making processes, reducing errors and waste, increasing flexibility and scalability, and improving customer satisfaction.
However, it’s not just about adopting technologies but also leveraging those technologies effectively to streamline and enhance operations. When executed well, digital transformation enables warehouses to gain a competitive edge.
There are four main types of warehouse management software companies utilize today.
Type | Key Features |
---|---|
Warehouse Management Systems (WMS) |
|
Enterprise Resource Planning Systems (ERP) |
|
Warehouse Execution Systems (WES) |
|
Warehouse Control Systems (WCS) |
|
Warehouses often employ multiple types of software solutions, which can be configured to seamlessly share data and work together to streamline operations. A WES or WCS typically feeds information into the WMS, which in turn feeds data into the ERP.
Let’s take a closer look at each of these types of warehouse management software and how they’re used.
Warehouse management systems (WMS) are among the most commonly deployed types of software in modern warehouses. They are designed to support and optimize warehouse functionality and distribution center management. A WMS facilitates everyday operations by managing inventory levels, optimizing picking and shipping processes, and providing tools for monitoring workforce performance.
WMS can be costly and time-consuming to implement, due to the need to train staff and integrate the software with other systems. In fact, 52% of companies not currently utilizing a WMS say the cost of these systems is a significant barrier to adoption. However, 26% of WMS users report massive time savings, which illustrates the high potential ROI of adopting such systems.
Warehouse management systems offer numerous advantages, such as enhancing inventory accuracy through real-time tracking, improving order fulfillment speed and accuracy, and increasing warehouse efficiency by optimizing space and labor utilization.
The key features and capabilities of WMS include:
ERP software integrates various business processes and functions into a single comprehensive system to streamline processes and information across the organization. In the context of warehousing, ERP systems manage inventory in conjunction with other business processes like accounting, HR, procurement, and sales.
These systems can be costly to implement and maintain. Implementation is time-consuming, and it can temporarily disrupt operations. In some cases, ERP systems offer more features than the typical warehouse needs, which can make the system cumbersome for staff to use.
That said, ERP systems offer a holistic view of the entire organization’s operations, including warehousing. This can be beneficial for decision-making thanks to the ability to integrate and analyze data from multiple departments, such as finance, human resources, sales, and procurement. By automating business processes, ERP systems can significantly boost productivity and efficiency.
The key features and capabilities of ERP systems include:
A warehouse execution system manages and automates the execution of warehouse operations, including the movement, storage, and sorting of goods within a warehouse. It often works in real-time to coordinate tasks across different systems and equipment, such as conveyors and robotics.
Initial setup and customization of WES can be resource-intensive. The scope of WES can overlap with WMS and WCS systems, which can create redundancies and confusion for staff operating these systems.
However, many WES solutions have a modular design, allowing warehouses to implement the functions they need and scale up or add modules and capabilities as their operations grow. These solutions are highly customizable and can be configured to support specific warehouse operational workflows, rules, and policies.
WES solutions offer numerous advantages, such as increasing operational efficiency by dynamically optimizing tasks, enhancing order processing speed by automating workflows, and reducing labor costs through improved labor allocation and automation.
The key features and capabilities of WES include:
A warehouse control system directly controls material handling equipment within the warehouse, such as conveyors, sorters, automated storage and retrieval systems (AS/RS), and robotics. It provides the interface for real-time equipment decision-making, ensuring the efficient movement of goods.
WCS solutions are primarily beneficial for warehouses that have implemented a high level of automation. Implementing WCS may require a significant investment in compatible equipment.
When properly configured and integrated with other systems, a WCS solution helps to improve the efficiency and throughput of automated equipment. It can also reduce manual errors in material handling and can improve safety by optimizing equipment operation. Like WES, WCS solutions often have a modular design, making it easy to expand or reconfigure as the warehouse’s needs change or as new equipment is added.
The key features and capabilities of WCS include:
Most types of warehouse management software can be deployed as standalone (on-premise) solutions or as cloud-based solutions. Here’s a look at these deployment options and their advantages and disadvantages.
Standalone or on-premise warehouse management software is installed and runs on the company’s own servers and computing infrastructure. It requires significant upfront investment in hardware and software, as well as ongoing expenses for maintenance and IT staff.
On-premise warehouse management software offers greater control over the system and its data. Warehouses can also customize the software to suit their unique operational requirements and integrate it with existing systems.
Because the system’s performance isn’t reliant on internet connectivity, on-premise solutions offer high-performance capabilities and uptime. This can be especially beneficial for warehouse operations in which even a minimal delay can have serious consequences.
On-premise solutions can offer better security, as well, because the data is stored on-site and managed directly by the company’s IT department. Of course, this depends on the effectiveness of the company’s security controls and its overall security posture.
One downside of standalone, on-premise warehouse management software is the high upfront costs, including infrastructure, software licensing, and implementation services. Solutions deployed on-premise also require a dedicated IT staff to manage software updates, hardware maintenance, and troubleshooting, which results in higher ongoing costs.
On-premise solutions are often challenging to scale as the business grows. It often requires additional hardware purchases and potential system downtime for upgrades.
Cloud-based warehouse management software is hosted on the vendor’s servers and accessed over the internet. This Software as a Service (SaaS) model involves a subscription fee, typically based on the level of use or number of users, without the need for significant hardware investment.
These systems can support the fast-paced fulfillment economy and offer real-time visibility, making them appealing for warehouses leveraging the power of data analytics. The cloud-based warehouse management systems market segment had the highest revenue share in 2023, and it’s expected to become the fastest-growing segment, with a CAGR of 20.1% from 2024 to 2030.
Cloud-based warehouse management software can be implemented rapidly and has lower upfront costs compared to on-premise solutions, as it doesn’t require large investments in hardware and software. As a result, cloud-based systems are often more accessible for small to medium-sized businesses. However, there are ongoing subscription fees.
These solutions are also easily scalable to accommodate business growth or fluctuating demand, often with simple adjustments to the subscription plan.
Because the vendor manages software updates and maintenance, ensuring that the system is always up to date with the latest features and security patches, there’s no need for the warehouse to maintain a dedicated IT staff to manage the system. That said, data is stored off-site, which can lead to data privacy and security concerns, depending on the vendor’s security measures and compliance standards.
Additionally, cloud-based solutions can be accessed from anywhere with an internet connection, which supports remote work and real-time data access across multiple locations. However, that benefit can also pose challenges, as the system is dependent on a fast and reliable internet connection. Connectivity issues can impact access and performance.
Adopting smart warehouse technologies can lead to substantial improvements in operational efficiency, accuracy, and productivity. They also enable warehouses to gain several significant competitive advantages, including faster order processing times, reduced operational costs, and enhanced customer satisfaction.
Staying up-to-date with technological trends and assessing their applicability and return on investment is crucial for warehouse operations looking to stay ahead in a rapidly changing industry. Here’s a look at some of the most innovative warehouse technologies in 2024.
Automated Material Handling Equipment (AMHE) and software encompass a broad range of tools, machines, systems, and software applications designed to automate the processes of moving, protecting, storing, and controlling materials and products throughout a warehouse, distribution center, or manufacturing facility.
AMHE includes equipment such as:
As we discussed earlier in this guide, software solutions such as Warehouse Control Systems (WCS), Warehouse Management Systems (WMS), and Warehouse Execution Systems (WES) can integrate with this equipment and control and optimize their operation.
Automated systems can operate continuously without breaks, fatigue, or slowdowns, significantly speeding up the material handling process. This makes AMHE ideal for performing repetitive, labor-intensive tasks previously done by humans.
It can also be easily scaled up or down to accommodate fluctuations in demand without hiring additional permanent or temporary staff, reducing the need for a large labor force and mitigating the impact of labor shortages.
Additionally, by taking over physically demanding and dangerous tasks, automated equipment also reduces the risk of workplace injuries and associated costs and compliance issues.
Software like WES, WCS, and WMS can determine the most efficient routes and methods for picking, storing, and moving items, reducing wasted man hours and effort. By reducing the chances of human error in inventory management, order picking, and other processes, AMHE leads to higher accuracy and lower return rates.
Machine learning (ML) and artificial intelligence (AI) are advanced features found in many modern warehouse management software solutions that enhance efficiency, accuracy, and decision-making. These technologies leverage data analysis and predictive models to automate and optimize various warehouse operations.
For example, AI can optimize picking routes and strategies (e.g., zone, wave, or batch picking) based on the layout of the warehouse and the location of items. This minimizes travel time, speeds up the picking process, and reduces human error.
AI-powered tools can also predict labor needs based on order volumes, inventory levels, and other operational parameters. They dynamically allocate tasks to workers based on skill sets, workloads, and efficiency, improving overall workforce productivity.
ML and AI also play an important role in robotics and automation, driving the operation of robotic systems such as AGVs, AMRs, and robotic picking arms. These robots can learn and adapt to new tasks or changes in the environment, working alongside human workers to reduce manual labor and improve safety.
The Internet of Things (IoT) leverages interconnected devices and sensors to collect, transmit, and analyze data in real time. This interconnectedness enables more intelligent, efficient, and responsive warehouse operations, such as real-time tracking of goods, equipment condition monitoring, and environmental monitoring within the warehouse.
For example, IoT devices such as RFID tags and sensors provide real-time visibility into inventory levels, reducing the chances of stockouts or overstocking. They enable precise tracking of goods throughout the warehouse, improving inventory accuracy and facilitating just-in-time inventory practices.
Additionally, IoT sensors can collect data such as temperature and humidity levels, which is imperative for warehouses that store perishable goods or goods requiring a temperature-controlled environment, such as pharmaceuticals and sensitive electronics.
IoT sensors can also track the location and usage of warehouse equipment like forklifts, pallet jacks, and containers. This information helps in optimizing the use of assets, preventing theft or loss, and planning maintenance schedules to reduce downtime.
These sensors can also monitor equipment conditions in real time and predict failures before they occur. This allows for predictive maintenance, minimizing unexpected downtime and extending the lifespan of equipment.
IoT devices generate vast amounts of data, which can be analyzed to gain insights into operational trends, patterns, and bottlenecks and support more informed decision-making and strategic planning.
Used for automated inventory checks, drones can quickly scan barcodes or RFID tags in hard-to-reach areas, significantly reducing the time and resources (including labor costs) required for inventory management. Also called unmanned aerial vehicles (UAVs), drones can help maintain real-time inventory visibility, enabling more accurate stock control and reducing the likelihood of stockouts or overstock.
Drones can also inspect areas that may be hazardous to human workers, such as confined spaces or areas with extreme temperatures.
Additionally, drones can be equipped with cameras to provide a bird’ s-eye view of warehouse operations and collect detailed data, which can help identify bottlenecks and areas for improvement.
Voice-directed picking (VDP) is a technology-driven method used in warehouse operations where workers receive verbal instructions via a headset connected to a warehouse management system (WMS). This system guides them through their tasks, particularly for picking items to fulfill orders.
By providing direct, step-by-step instructions, VDP systems eliminate the need for workers to repeatedly look at lists or screens, which helps to streamline and speed up the order-picking process. Voice instructions also reduce the likelihood of human error, improving picking accuracy and reducing the costs of returns and rework.
VDR systems can guide workers through optimized picking routes, which minimizes unnecessary movement. This, coupled with the hands-free, eye-free operation of these systems, which allows workers to be more aware of their surroundings, can reduce traffic congestion in aisles and improve safety.
Voice-directed picking systems are often intuitive, which allows for rapid training and onboarding. This is especially beneficial for warehouses hiring temporary staff. In addition, their ease of use contributes to greater worker satisfaction.
Electronic data interchange (EDI) is a standardized method for transferring and synchronizing data such as purchase orders, invoices, shipping notices, and inventory updates between businesses and their suppliers, customers, logistics providers, and other partners.
EDI eliminates the inconsistency in document formatting among various companies by enforcing a standardized format, eliminating the confusion that can lead to data entry errors. It also automates the exchange of documents and data, allowing for faster and more accurate execution of transactions.
Because documents are exchanged nearly instantaneously, warehouses can respond quickly to orders, inventory needs, and other demands, enhancing service levels and boosting customer satisfaction. The accurate and timely exchange of required documentation can also aid in maintaining compliance with industry standards and regulatory requirements.
There’s a growing demand for more sustainable practices that reduce the environmental impact of warehouse operations, making energy management and sustainability technologies appealing to many companies that want to gain a competitive advantage. Technologies like solar panels, energy-efficient lighting, and smart heating, ventilation, and air conditioning (HVAC) systems reduce the environmental impact and operational costs.
Green warehousing practices encompass a range of strategies and technologies, such as:
These practices contribute to environmental sustainability and offer significant benefits for warehouse management, including cost savings, improved efficiency, and enhanced reputation.
The six core functions and steps of the warehouse management process are:
The 5S method is a lean warehousing methodology for maintaining a clean, well-organized facility to facilitate more efficient operations and make problems apparent so that they can be readily addressed. The 5S principles in warehouse management include:
The most common processes in warehouse operations include:
The four main flows in a warehouse include the flow of goods, the flow of information, cash flow, and value flow. The flow of goods refers to the physical movement of products in, through, and out of the warehouse, while the information flow is the movement and management of data related to customers, inventory, and orders.
Cash flow in the warehouse refers to the financial transactions associated with buying, holding, and selling inventory. Value flow in the warehouse refers to the addition of value to products by assembling, customizing, or packaging them.
Our sales engineers are experts in automatic asset tracking, tagging and identification,a nd can answer all your questions. Get in touch now.
Lets Talk ›Enter your information and get a free checklist of the top questions to answer and tips to plan a successful asset tagging project for any warehouse management system implementation.