What is Maintenance Management, Why is It Important?
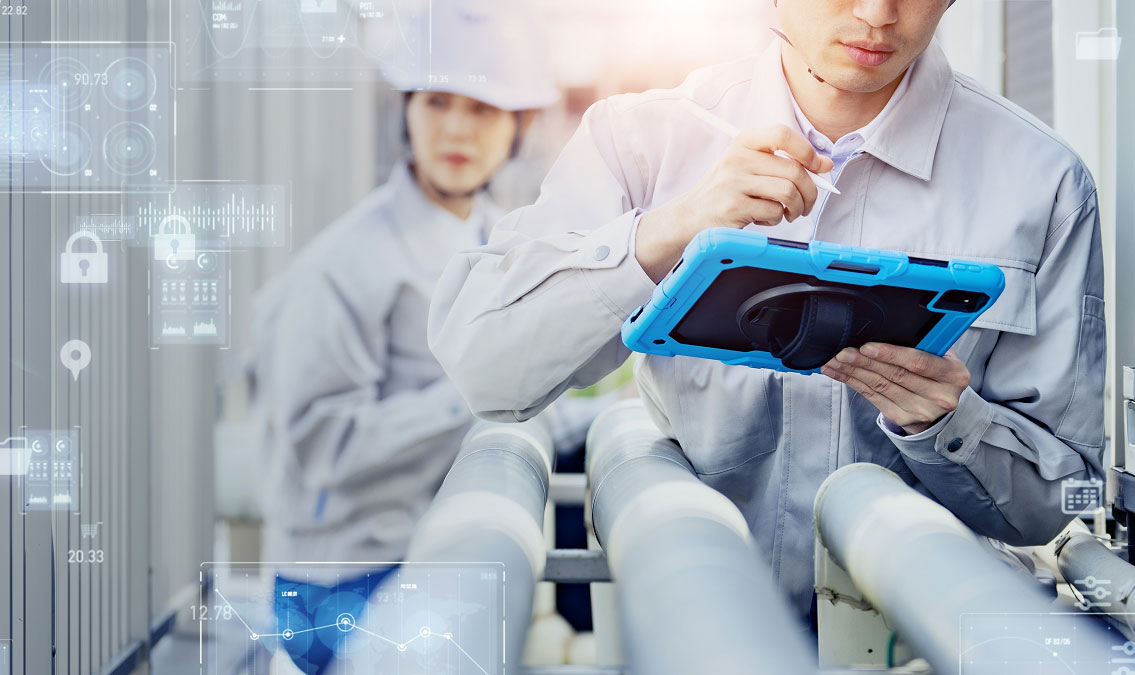
Maintenance management is crucial across a broad range of industries, from manufacturing to energy and utilities, healthcare, warehousing and logistics, defense, education, and more. It’s an essential business function for improving operational efficiency, safety, and equipment longevity.
Whether you’re a seasoned maintenance manager seeking to refine your strategies or a newcomer aiming to grasp the basics, this article provides valuable insights and practical advice.
From exploring the different types of maintenance (e.g., preventive, predictive, corrective, etc.) to discussing the latest technological trends and software in the field, the guide is packed with data-driven insights and expert recommendations to help you reduce maintenance costs and increase efficiency.
Maintenance management is the process of overseeing and coordinating all tasks related to the maintenance and upkeep of facilities, equipment, machinery, and other assets within an organization. This includes creating maintenance schedules, coordinating maintenance activities, managing spare parts inventory, and ensuring that all equipment is properly maintained to prevent breakdowns and prolong its lifespan.
Effective maintenance management helps to minimize downtime, reduce costs, and ensure that all assets are operating at peak efficiency. It’s an essential function for any organization that relies on equipment and machinery in its operations.
Based on data from Plant Engineering
Organizations utilize various strategies, practices, and tools for maintenance management. According to Plant Engineering’s 2021 Industrial Maintenance Report:
Both preventive maintenance and predictive maintenance are expected to grow substantially in the coming years. The global preventive maintenance software market size was valued at $786.9 million in 2020 and is projected to reach $1.675 billion by 2027, with a CAGR of 11.4% from 2024 to 2027.
The global predictive maintenance market was valued at $9.6 billion in 2023 and is expected to reach $10.5 billion in 2024, according to Future Market Insights. The market is projected to grow at a CAGR of 10.9% from 2024 to 2034, reaching $80.2 billion in 2034. Predictive maintenance is increasingly used across a variety of sectors, including aerospace, energy, manufacturing, transportation, and defense, among others. Companies are increasingly striving to reduce maintenance costs and minimize downtime, and predictive maintenance makes it possible to optimize maintenance activities by monitoring equipment health and
addressing minor problems before failures occur. Growing adoption of artificial intelligence, machine learning, IoT, and cloud computing further drives demand.
Let’s review some of the most common maintenance strategies.
Corrective maintenance, also called reactive maintenance, is the traditional approach to maintenance management. With this approach, maintenance is performed when a piece of equipment or machinery has failed.
Corrective maintenance includes tasks such as:
Reactive maintenance can involve unplanned downtime and emergency repairs, so it tends to be more disruptive to operations and more costly compared to proactive forms of maintenance.
Not all failures can be prevented or predicted, so corrective maintenance is an essential component of maintenance management, even when other forms of maintenance are utilized.
However, by implementing other maintenance strategies, such as preventive maintenance, companies can reduce the likelihood and frequency of breakdowns and equipment failures and extend the useful lifespan of equipment.
Preventive maintenance involves performing maintenance on equipment before failures occur. It’s typically based on time or usage intervals—the time since maintenance was last performed or the amount of time the equipment has actively operated.
Preventive maintenance includes tasks such as:
By regularly servicing and inspecting equipment before issues arise, businesses can avoid costly breakdowns and downtime. Preventive maintenance also helps to optimize equipment performance and extend the operational lifespan of machinery and equipment assets.
Preventive maintenance requires careful planning and scheduling to ensure that maintenance activities are carried out efficiently and effectively.
Predictive maintenance, also known as condition-based maintenance, uses sensors and monitoring devices to gather data on the condition of equipment. This data is analyzed to predict when equipment is likely to fail, so organizations can take proactive steps to prevent it.
Predictive maintenance includes tasks such as:
By using data and analytics to predict when maintenance is needed, businesses can proactively address issues before they become major problems. This can reduce downtime, lower maintenance costs, and improve overall operational efficiency.
Predictive maintenance relies on high-quality, high-volume data and can require a large initial investment in sensors, IoT devices, data storage, and analytics software. However, with careful planning, the long-term benefits are substantial.
According to UpKeep, the use of predictive maintenance increased from 47% in 2017 to 51% in 2018. At the time of the survey, 80% of manufacturing plants used preventive maintenance, and more than 50% of plants used predictive maintenance with analytical tools.
Based on data from Mordor Intelligence
The use of predictive maintenance continues to grow. According to Mordor Intelligence, the machine condition monitoring market is valued at an estimated $1.25 billion in 2024. It’s expected to grow at a CAGR of 9.65% over the next five years, reaching $1.97 billion by 2029.
In addition to the increased adoption of predictive maintenance strategies, growth in the machine condition monitoring market is driven by the increased demand for remote monitoring due to digital transformation across industries, as well as advancements in IoT and AI technologies that enhance monitoring capabilities.
Prescriptive maintenance goes a step further than predictive maintenance. It involves the use of advanced analytics, machine learning algorithms, and artificial intelligence to analyze data from various sources and not only predict potential issues but also prescribe specific maintenance actions to address those issues and optimize the maintenance process.
These recommendations could include recommendations on the best time to perform maintenance, the specific maintenance tasks to be carried out, and the optimal allocation of resources to perform those tasks. Prescriptive maintenance aims to optimize maintenance decisions in real time, improving operational efficiency and reducing costs.
Prescriptive maintenance involves tasks such as:
This strategy helps organizations minimize downtime, extend the useful lifespan of equipment, improve safety, and optimize maintenance costs.
Reliability-centered maintenance (RCM) ensures that a system continues to operate as intended and meets its users’ needs. This maintenance approach focuses on preserving the functions of equipment or machinery by analyzing potential failure modes and their consequences.
Reliability-centered maintenance involves tasks such as:
By identifying the most critical components and scheduling maintenance tasks accordingly, organizations can optimize their maintenance practices and reduce the risk of costly breakdowns. RCM helps to extend the useful lifespan of assets, improve operational efficiency, and increase the organization’s overall productivity.
Total productive maintenance (TPM) is a proactive approach to maintenance that aims to maximize the efficiency of production equipment. It emphasizes the importance of involving all employees in the maintenance process, encouraging operators to take responsibility for the upkeep of their equipment and perform routine maintenance to prevent breakdowns.
Total productive maintenance involves activities such as:
Implementing TPM requires a concerted effort from all levels of an organization, from senior management to frontline operators. By creating a culture of proactive maintenance and employee involvement, organizations can minimize downtime, reduce maintenance costs, and improve overall performance.
To help you stay on top of all your maintenance activities, we created these expert checklists:
Screenshot from NIST
Maintenance costs vary significantly by geographic region and industry, making it difficult to estimate them accurately. Estimates also vary among researchers, as varying metrics are used to calculate costs. For instance, one study estimates that maintenance costs make up 15% to 70% of the cost of goods produced, while another indicates that maintenance accounts for 37.% of the total cost of ownership.
According to Plant Engineering’s 2021 Industrial Maintenance Report, 41% of plants allocate more than 10% of their annual operating budget to maintenance tasks, services, and equipment, while 46% allocate up to 10%:
Maintenance costs are unquestionably high, but the consequences of inadequate maintenance are even more significant. According to Plant Engineering’s Purchasing Considerations for Maintenance Management Software report, released in November 2022, the average cost of unplanned downtime is $108,708. More than one-third of respondents (38%) reported that the cost of unplanned downtime is less than $50,000 per hour at their facility, while 8% reported costs of more than $300,000 per hour.
Based on data from Plant Engineering
In its 2021 report, Plant Engineering also asked respondents about the leading causes of unscheduled downtime in their plants. Aging equipment was identified as the leading cause by 42% of respondents, an increase from 34% in 2020. Other leading causes of unscheduled downtime include:
According to Plant Engineering’s 2021 Industrial Maintenance Report, plants spend an average of 33 hours per week on maintenance-related tasks. Here’s the specific breakdown of the number of hours plants spend on maintenance-related tasks, according to Plant Engineering’s survey:
According to UpKeep, equipment that is run to the point of failure can cost 10 times as much as one that is regularly maintained, and every $1 worth of maintenance deferred can result in a $4 capital renewal cost.
Using preventive and predictive maintenance strategies can help companies realize significant cost savings, reduced downtime, and other benefits. UpKeep reports that predictive maintenance can save 8-12% over preventive maintenance and up to 40% over reactive maintenance.
A 2020 report released by the National Institute of Standards and Technology (NIST) evaluated the costs of machinery maintenance and losses resulting from inadequate maintenance strategies in discrete manufacturing (NAICS 321-339, excluding NAICS 324 and 325) among U.S. manufacturers. According to the report, “Machinery maintenance expenditures for NAICS 321-339 (excluding 324 and 325) were estimated to be $57.3 billion for 2016. Losses due to preventable maintenance issues amounted to $119.1 billion.”
The report further explains, “The top 25 % of those establishments relying on reactive maintenance was associated with 3.3 times more downtime than those in the bottom 25 %. They were also associated with 16.0 times more defects, 2.8 more lost sales due to defects from maintenance, 2.4 times more lost sales due to delays from maintenance, and 4.9 times more inventory increases due to maintenance issues.”
The $119.1 billion in losses due to preventable maintenance issues included:
Among the U.S. manufacturers included in this study, an estimated 134.1 injuries and 0.4 deaths were associated with maintenance issues. This equals an estimated 16.03 injuries and 0.05 deaths per million employees.
Manufacturers in this study employing advanced maintenance strategies in 2016 gained:
Based on data from NIST
Manufacturers that relied primarily on preventive and predictive maintenance, defined as less than 50% reactive maintenance, realized significant benefits. The top 50% of manufacturers using predictive maintenance strategies experienced:
On average, manufacturers that invested more heavily in preventive or predictive maintenance experienced:
Maintenance management benefits your organization in multiple ways and can significantly impact its overall success. Here are some of the biggest benefits of implementing an effective maintenance management program.
Maintenance management is crucial for ensuring that all equipment is functioning optimally. However, there are several challenges associated with maintenance management that organizations often face in their day-to-day operations.
Organizations often face financial limitations that can affect their ability to perform necessary maintenance. With a limited budget, maintenance managers may not have access to the resources and tools needed to maintain equipment and facilities effectively. This can lead to delays in repairs, increased downtime, and ultimately, reduced productivity.
One of the biggest risks of budget constraints in maintenance management is the temptation to defer maintenance activities to cut costs. While this may provide short-term savings, it can lead to bigger issues in the long run. Deferred maintenance can result in equipment failures, safety hazards, increased repair costs, and reduced equipment lifespans.
Budget constraints can also limit the ability of maintenance managers to invest in new technologies and training programs that could improve maintenance efficiency and reduce costs in the long term. Without proper investment, maintenance teams may struggle to keep up with the latest industry trends and best practices.
Balancing preventive maintenance with reactive maintenance is one of the main challenges in maintenance management. As described earlier in this guide, preventive maintenance involves scheduling regular maintenance tasks to prevent equipment breakdowns, while reactive maintenance involves fixing equipment only when it breaks down.
Finding the right balance between the two can be challenging. It can be difficult to predict when equipment will fail, making it hard to determine the appropriate maintenance schedule. This can result in either over-maintaining equipment, leading to increased costs, or under-maintaining equipment, resulting in more frequent breakdowns.
Resource allocation can also be a challenge when balancing preventive and reactive maintenance. Organizations must allocate resources efficiently to ensure that both types of maintenance are carried out effectively. With limited resources and competing priorities, this can be difficult.
Having the right spare parts on hand is essential for minimizing downtime and keeping equipment running smoothly. However, managing and tracking spare parts inventory can be complex and time-consuming, especially for organizations with a large number of assets.
A typical maintenance department may have hundreds or even thousands of different parts in inventory, each with its own unique part number, supplier, and quantity on hand. Manually tracking all of these parts can lead to errors in inventory counts and ordering.
Supplier lead times and delivery reliability add to the challenge. If a part is on backorder or delayed in delivery, it can impact equipment uptime and maintenance schedules. Therefore, maintenance managers must maintain good relationships with reliable suppliers and have contingency plans for obtaining parts quickly when needed.
Demand for parts can also be unpredictable. Equipment breakdowns can happen at any time, resulting in a sudden need for parts that may not be in stock. This can lead to emergency ordering, which can be costly and time-consuming.
On the other hand, obsolete or excess inventory is also problematic. Parts can become obsolete if equipment is upgraded or replaced, leading to parts sitting on the shelf unused.
Excess inventory ties up capital and takes up valuable storage space. Therefore, maintenance managers should regularly review inventory levels and dispose of obsolete parts.
Implementing a robust inventory management system and regularly auditing spare parts can help ensure that the right parts are available when needed and minimize downtime when unexpected problems occur.
Asset tags and barcode labels facilitate inventory control and assist maintenance technicians in finding the right parts when they’re needed. For example, Warehouse Rack Labels make it easy for maintenance workers to quickly locate the correct storage locations for specific parts.
Container, Pallet, LPN, Tote, and Tray Bar Code Labels can be used to label storage containers. Maintenance technicians can easily identify a specific part and the equipment it’s compatible with by simply scanning a barcode label.
Managing aging infrastructure while minimizing downtime and ensuring safety is also a prominent challenge in maintenance management. As equipment and facilities age, they may require more frequent and costly maintenance.
Aging infrastructure is more prone to deterioration and breakdowns, which require costly repairs and replacements. This can strain budgets and resources, making it difficult for maintenance managers to keep up with the maintenance needs of aging infrastructure.
Additionally, many older infrastructure systems were built using technology and materials that are now considered obsolete or inefficient. This can make it difficult to find replacement parts and skilled workers who are familiar with outdated technology, leading to longer repair times and higher costs.
Aging infrastructure can also be a safety hazard. As infrastructure systems deteriorate over time, they can become less reliable and more prone to failure. This can pose a danger to the public, as well as to workers responsible for maintaining the infrastructure.
Effective maintenance requires careful planning and scheduling to minimize disruptions to operations. Balancing regular maintenance activities with unexpected repairs and ensuring that work is completed within specified timeframes can be difficult.
For instance, equipment can break down unexpectedly, requiring immediate maintenance. This can disrupt planned maintenance schedules and require maintenance teams to prioritize and reschedule tasks at the last minute. Limited resources create another problem when it comes to maintenance scheduling and planning. Maintaining an effective balance between daily operations and scheduled
maintenance can be challenging due to budget constraints, manpower shortages, and time constraints.
Many industries have strict regulatory requirements for maintenance activities to ensure safety and compliance with industry standards. Meeting these compliance requirements adds an additional layer of complexity to maintenance planning and scheduling, as maintenance activities need to be carefully documented and executed in accordance with regulations.
Effective communication is essential for coordinating maintenance activities, prioritizing work orders, and sharing important information about equipment and facilities.
In many organizations, different departments and teams operate in silos, focusing solely on their own goals and objectives. Communication and collaboration between departments can be hindered by this siloed approach, making it difficult to coordinate maintenance activities efficiently.
Each department within an organization may have its own priorities and goals, which can sometimes conflict with those of other departments—especially when those teams have to share limited resources. This can create tension and make it challenging to align efforts and resources toward common maintenance objectives.
Effective cross-functional training helps to improve coordination across teams and departments by giving employees a solid understanding of each other’s roles and responsibilities. Additionally, implementing a computerized maintenance management system (CMMS) or other maintenance management software can help streamline communication and improve collaboration between maintenance teams and other departments.
Ensuring that maintenance teams have the right skills, training, and resources to perform their jobs effectively is essential for maintaining a high level of equipment reliability, but workforce management can be challenging.
Maintenance teams typically consist of technicians with varying skill levels, experience, and expertise. To manage a diverse team, you need good communication, coordination, and supervision to ensure everyone is working towards the same goal.
A breakdown or emergency can disrupt a planned maintenance schedule and require quick adjustments to the workforce. It can be challenging for maintenance managers to manage resources efficiently and effectively in such situations.
Finding and retaining qualified technicians can be difficult, especially in industries where there is a shortage of skilled labor. As technology develops, organizations must ensure that technicians are skilled and trained to perform their tasks efficiently. However, training is time-consuming and expensive. Recruitment and training issues can lead to understaffing and increased workloads for existing staff. A comprehensive training program, regular performance reviews, and ongoing support and feedback can improve workforce management and maximize maintenance teams’ effectiveness. Upskilling your existing workforce can also ensure that technicians are up-to-date with the latest
technologies. We’ll discuss the challenges associated with technology advancements in more detail below.
Keeping up with advancements in maintenance technologies (such as predictive maintenance tools and management software) requires investment and training. However, integrating new technologies can improve efficiency and reduce costs in the long run.
New advancements in technology are constantly being developed, making it difficult for maintenance managers to stay current with the latest tools and systems. Additionally, the cost of implementing new technologies, such as upgrading equipment and software, can be prohibitive for some organizations.
As discussed above, training employees on how to use and maintain new technologies can be time-consuming and costly. Some employees may resist change and be resistant to learning new systems, further complicating the adoption of new technologies.
Keeping up with technology advancements in maintenance management requires a commitment to ongoing training and professional development, as well as a willingness to embrace change and adapt to new technologies.
Ensuring that maintenance activities comply with relevant safety standards and regulations is critical. This includes managing risks associated with maintenance work and ensuring that equipment meets safety requirements.
Organizations must comply with numerous regulations and standards to ensure the safety of their maintenance operations. These regulations can be complex and constantly changing.
Many maintenance workers—including existing team members and new hires—may not receive adequate training on safety procedures and compliance requirements. This can lead to lapses in safety protocols and increase the risk of accidents and non-compliance.
Additionally, pressure to meet tight deadlines and keep equipment running smoothly can lead to shortcuts being taken in safety procedures or compliance measures, increasing the risk of accidents and regulatory violations.
Organizations may face budget constraints and resource limitations when it comes to implementing and maintaining safety programs. This can make it challenging to invest in necessary safety equipment, training, and compliance measures.
Maintenance activities often involve the use of hazardous materials, chemicals, and equipment that can have adverse effects on the environment if not properly managed and disposed of. Balancing environmental concerns with maintenance needs requires careful planning and adherence to environmental regulations.
Maintenance activities can result in the generation of waste materials such as oil, grease, and other pollutants that can contaminate soil, water, and air if not handled correctly. It can also increase the consumption of energy and resources, contributing to greenhouse gas emissions and overall environmental degradation.
Implementing sustainable practices in maintenance management, such as energy-efficient equipment and processes, as well as proper waste management practices, can help mitigate these environmental impacts.
Environmental regulations are constantly evolving and becoming increasingly stringent. Maintaining compliance with environmental laws requires continuous monitoring and updating of maintenance practices to ensure they meet the necessary standards.
Having an effective maintenance management plan in place is crucial for the success and efficiency of any organization. By properly maintaining equipment, machinery, and facilities, companies can minimize downtime, reduce costs, and maximize productivity.
Implementing an effective maintenance management plan involves strategic planning, resource allocation, and continuous improvement to ensure that equipment and facilities are maintained at optimal levels. Here’s a step-by-step approach to developing and implementing a successful maintenance management plan:
Maintenance management metrics and key performance indicators (KPIs) help your organization track and measure the effectiveness of its maintenance operations. Maintainers can use these metrics to identify areas for improvement, optimize resource utilization, and maximize equipment lifespan.
First, let’s differentiate maintenance management metrics and maintenance management KPIs. While the terms are commonly used interchangeably, there are differences between the two:
The distinction can vary depending on the organization’s focus and the context in which the measure is used. The following KPIs provide valuable insights into the effectiveness of various aspects of your maintenance program.
Mean Time To Repair is a KPI used in maintenance management to measure the average time it takes to repair an asset or piece of equipment after a failure.
To calculate MTTR, the total downtime for a specific asset or equipment is divided by the total number of repairs conducted during a specific time period. The formula for MTTR is:
MTTR = Total Downtime / Total Number of Repairs
For example, if a machine experiences a total downtime of 10 hours due to a failure and requires 2 repairs during that time, the MTTR would be calculated as:
MTTR = 10 hours / 2 repairs = 5 hours
A lower MTTR indicates that maintenance teams are efficient in identifying and resolving equipment failures, leading to quicker repairs and reduced downtime. On the other hand, a high MTTR may indicate inefficiencies in maintenance procedures, lack of resources, or equipment reliability issues that need to be addressed.
MTBF is a measure of the average time between failures of a piece of equipment or a system. It is an important indicator of equipment reliability and can help maintenance managers make informed decisions about maintenance schedules and equipment replacement.
MTBF helps to identify equipment that may be prone to failures, enabling maintenance teams to take proactive measures to prevent downtime and reduce maintenance costs. By tracking MTBF over time, managers can also assess the effectiveness of maintenance strategies and make adjustments as needed.
By understanding how long a piece of equipment typically goes between failures, managers can schedule maintenance tasks accordingly. For example, if a piece of equipment has an MTBF of 500 hours, maintenance tasks can be scheduled at regular intervals before the equipment is expected to fail.
To calculate MTBF, divide the total amount of time that a piece of equipment is operational by the number of failures that have occurred:
MTBF = (Time Asset Has Been In Use – Unplanned Downtime Due to Breakdown) / Total Number of Breakdowns
The result is the average time between failures. For example, if a piece of equipment has been operational for 1,000 hours and has experienced 10 failures, the MTBF would be 100 hours.
Preventive Maintenance Compliance measures the percentage of scheduled preventive maintenance tasks that have been completed on time. It provides valuable insights into how well the plan you’ve established is being followed.
Most organizations aim for a PMC of 90% or greater. To calculate PMC, use the following equation:
PMC = (Number of Executed Tasks / Number of Planned Tasks) x 100
This metric is used to track the maintenance work that has been identified and/or scheduled but hasn’t yet been completed. These tasks can include repairs, inspections, replacements, and other maintenance activities. It includes all types of maintenance (preventive, predictive, prescriptive, and corrective).
Quantifying your maintenance backlog requires identifying open work orders, estimating the time required to complete all tasks, and converting it into a measure of time that’s relevant to your organization.
For example, if your maintenance team can complete 100 hours of work per week and you have 400 hours in your backlog, your backlog is equivalent to four weeks of work. The maintenance backlog can be reported as:
Unplanned machine downtime is a measure of the amount of time an asset is out of operation due to an unexpected problem or breakdown. Unplanned downtime can significantly impact production, increase maintenance costs, and disrupt supply chains.
In contrast, planned downtime occurs during scheduled maintenance, upgrades, or other predictable disruptions that are part of regular operations.
To calculate unplanned machine downtime, log instances when a machine stops operating unexpectedly, including any stoppage that was not scheduled. Record the length of time the machine remained non-operational (from the time the machine stopped to the time it returns to normal operation).
Add these times to determine the total duration of unplanned downtime events over a specific period, such as daily, weekly, or monthly. You may also want to consider the lost production volume or other financial costs associated with downtime using one of the following equations:
Total Downtime x Production Rate (Units Per Hour)
Or
Total Downtime x Average Revenue Per Unit of Production Time
Unplanned downtime can be measured for individual machines, groups of machines, or for all an organization’s equipment assets.
Maintenance costs as a percentage of the estimated replacement value of an asset provides a benchmark to determine if the amount being spent on maintenance is reasonable relative to the asset’s value.
A higher percentage might indicate excessive maintenance costs, possibly due to aging equipment requiring more frequent repairs. On the other hand, a lower percentage might suggest underinvestment in maintenance, which could lead to increased failure rates and operational risks.
To calculate this metric, you need the following figures:
Then, use the following formula:
Maintenance Cost as a % of ERV = (Total Maintenance Costs / Estimated Replacement Value) x 100
This is also called Maintenance Cost as a Percentage of Replacement Asset Value (RAV).
This ratio helps organizations understand how much they are investing in maintaining an asset compared to the cost of purchasing a new one, providing insight into the economic efficiency of their maintenance strategies.
Another approach to determining whether it makes sense to repair or replace an asset is to simply compare the cost to repair to the cost to replace an asset. The cost to repair is the expected annual cost of maintenance on the existing equipment. To determine the cost to replace, use the following formula:
Cost To Replace = (Cost of Replacement / Replacement Asset’s Lifetime) + Expected Annual Cost of Maintenance
For example,
Imagine you have an industrial machine with annual maintenance costs of $500. A new machine costs $8,000 and is expected to last 10 years, with annual maintenance costs of $300.
Cost to Repair (annually) = $500
Cost to Replace (annually) = ($8,000 / 10 years) + $300
Cost to Replace (annually) = $800 + $300 = $1,100
In this scenario, the annual cost to replace the machine, $1,100, is higher than the annual cost to repair the existing one, $500. Despite the higher upfront cost of replacement, in this case, it might not make financial sense to replace the machine if the goal is to minimize annual expenditures.
However, the decision might differ if other factors such as improved efficiency, lower energy consumption, or critical reliability issues of the old machine are considered.
Overall Equipment Effectiveness (OEE) is a comprehensive metric used in manufacturing to measure the effectiveness of a production process. It identifies the percentage of manufacturing time that is truly productive.
An OEE score of 100% means you’re manufacturing only high-quality parts, as fast as possible, with no stop time. The ideal OEE score is considered to be 85%.
OEE provides a single number that reflects the effectiveness of your equipment and processes by combining three different factors: Availability, Performance, and Quality.
Availability = Operating Time / Planned Production Time
Performance = Total Count of Products / (Operating Time x Ideal Cycle Time)
Quality = Good Count / Total Count
To calculate the Overall Equipment Effectiveness metric, multiply these three factors:
OEE = Availability x Performance x Quality
SMCP indicates how much scheduled maintenance work is critical to prevent operational disruptions and ensure safety. A high SMCP suggests that a significant portion of the maintenance schedule is vital for the functioning of the organization, which may indicate high reliance on certain equipment or systems.
A maintenance task is typically considered critical if delaying it or failing to perform it could lead to severe operational disruption, safety incidents, or significant financial loss. Monitoring SMCP helps in managing risks associated with equipment failure and optimizing the allocation of maintenance resources.
To calculate SMCP, use the following formula:
SMCP = (Number of Critical Maintenance Tasks / Total Number of Scheduled Maintenance Tasks) x 100
Asset Utilization Rate measures the efficiency with which a business uses its assets to generate revenue. It indicates the percentage of time that assets are actually in use compared to the time they are available for use.
High asset utilization rates typically suggest that a company is effectively using its assets to produce goods or services. Lower rates, on the other hand, may indicate underused resources or inefficiencies in the production process.
To calculate the Asset Utilization Rate, use the following formula:
Asset Utilization Rate = (Actual Operating Time / Available Operating Time) x 100
The Safety Incidents Rate is a crucial metric used in workplace health and safety management to quantify the frequency of accidents or safety incidents within a given period, typically in relation to the number of hours worked. It provides insights into the overall safety performance of an organization and helps to identify areas where safety improvements are needed.
When calculating the Safety Incidents Rate, it’s important to use a standardized measure to compare the rate over time and across organizations. Typically, the Safety Incidents Rate is calculated per 100,000 hours worked. To calculate it, use the following formula:
Safety Incidents Rate = (Number of Safety Incidents / Total Hours Worked) x 100,000
Maintenance Cost Per Unit measures the cost associated with maintaining equipment or other assets relative to the number of units produced. It provides valuable insights into the efficiency of maintenance expenditures and helps organizations optimize their production costs.
To calculate Maintenance Cost Per Unit, use the following formula:
Maintenance Cost Per Unit = Total Maintenance Costs / Total Units Produced
Distribution by Types of Maintenance Performed is a metric used in maintenance management to classify and report the various types of maintenance activities performed over a specific period. This classification helps organizations understand how their maintenance efforts are allocated across different strategies, such as preventive, predictive, corrective, and condition-based maintenance.
By analyzing the distribution of maintenance types, companies can better manage their maintenance resources, improve planning, and potentially increase the overall reliability and efficiency of their equipment.
To calculate the Distributioni by Types of Maintenance Performed, record all maintenance activities performed during the reporting period, and classify them by type. Then add all recorded maintenance activities.
Then, use the following formula for each type of maintenance to determine the percent of maintenance activities of each type performed during the reporting period:
Percent of [Type] Maintenance = (Number of [Type] Maintenance Activities Performed / Total Number of Maintenance Activities) x 100
Work Order Cycle Time is a measurement of the time it takes to complete a maintenance work order from the moment it’s created until it’s closed. It’s an important metric for evaluating the efficiency of maintenance operations and the responsiveness of the maintenance team.
Lower cycle times generally indicate a more efficient process, which can lead to higher equipment availability and reliability. Higher cycle times can indicate bottlenecks or a shortage of labor or other resources.
The formula to calculate Work Order Cycle Time is simple:
Work Order Cycle Time = End Time – Start Time
To get a broader view of your maintenance efficiency, calculate the average cycle time across multiple work orders over a specified period. You might also want to analyze cycle times by type of maintenance, criticality of equipment, or team/technician to identify patterns or areas for improvement.
Inventory Turnover Ratio is a measure indicating the frequency with which maintenance inventory (e.g., spare parts, supplies) is used and replenished within a given period. It helps organizations understand how effectively they’re managing the inventory that supports its maintenance operations.
Maintaining maintenance inventory efficiently can help reduce carrying costs, minimize obsolescence waste, and ensure the availability of critical parts when needed, preventing excessive downtime.
To calculate Inventory Turnover Ratio, you need two figures:
Average Maintenance Inventory = (Beginning Inventory + Ending Inventory) / 2
Once you have these figures, calculate the Inventory Turnover Ratio using the following formula:
Inventory Turnover Ratio = MRO Expenditure / Average Maintenance Inventory
In maintenance management, overtime is a valuable metric that can help organizations understand the efficiency and effectiveness of their maintenance operations. High levels of overtime can indicate problems such as insufficient staffing, unexpected equipment failures, or inefficient work processes, all of which can increase operational costs and affect overall productivity.
To calculate Overtime, use the following formula:
Overtime Hours = Actual Hours Worked – Standard Hours
Overtime can be calculated by employee, department, or the organization as a whole.
It’s also useful to analyze overtime data over different periods (weekly, monthly, yearly) to identify trends and patterns. This analysis can help in forecasting future staffing needs and adjusting work schedules to optimize resource utilization.
Maintenance management software enables organizations to streamline maintenance operations, prioritize tasks, and make data-driven decisions to optimize asset performance.
Many modern maintenance management software solutions allow managers to easily calculate, monitor, and report on the KPIs discussed in the previous section.
Research indicates that more organizations are embracing digitalization and adopting technologies and software to streamline and optimize maintenance management.
Based on data from Plant Engineering
Plant Engineering surveyed plant engineers, managers and maintenance professionals on the purchase and use of maintenance management systems in its 2022 Purchasing Considerations for Maintenance Management Software report. According to the report, most respondents use CMMS or EAM software in their facilities:
Based on data from Plant Engineering
In an earlier report from 2021, Plant Engineering found that while 54% of plants reported using CMMS and 16% reported using EAM software at the time of the survey, a surprising number of plants relied on more basic systems and tools to monitor or manage maintenance:
However, facilities are also employing more advanced maintenance management tools. In addition to the above, 44% of respondents reported using an automated maintenance schedule, 16% reported using EAM, and 8% reported using Industrial IoT, SaaS, or cloud computing systems.
Type of Software | Key Functionalities |
---|---|
Computerized Maintenance Management Software (CMMS) |
|
Enterprise Asset Management (EAM) Software |
|
Facility Management Software |
|
Predictive Maintenance (PdM) Software |
|
Reliability-Centered Maintenance (RCM) Software |
|
Maintenance Scheduling Software |
|
Asset Performance Management (APM) Software |
|
There are several types of maintenance management software that help organizations effectively manage their assets and equipment, each with unique features and capabilities.
Let’s take a closer look at the most common types of maintenance management software and how they support maintenance operations.
Computerized Maintenance Management Software (CMMS) is the most traditional form of maintenance management software. It’s widely used in industries such as manufacturing, healthcare, facilities management, and transportation, among others.
CMMS solutions help organizations organize and track maintenance activities more effectively, reducing downtime, increasing equipment lifespan, and reducing costs. It allows maintenance managers to create and assign work orders, track inventory and spare parts, and generate reports on maintenance performance.
Key capabilities of CMMS include:
EAM software helps organizations manage the lifecycle of their physical assets across various departments, locations, and facilities. Unlike simpler systems such as Computerized Maintenance Management Systems (CMMS), which focus primarily on maintenance scheduling and tracking, EAM provides broader functionalities that cover the entire range of asset management activities.
The primary goal of enterprise asset management software is to maximize the lifespan and value of assets while minimizing costs and downtime. It helps businesses keep track of their assets, schedule maintenance and repairs, manage inventory, and analyze data to make informed decisions about asset usage and resource allocation.
Key capabilities of EAM include:
Facility management software encompasses a wide range of functionalities that help facility managers ensure that their buildings are operating efficiently, safely, and cost-effectively.
It helps organizations reduce costs through efficient space utilization, energy management, and preventive maintenance, minimizing energy costs and reducing the need for costly repairs.
Key capabilities of facility management software include:
Predictive maintenance (PdM) software uses advanced analytics and machine learning algorithms to predict when equipment failures are likely to occur. By analyzing data from sensors and other sources in real-time, PdM software can help organizations proactively maintain and repair their machinery before it breaks down, saving time and money in the long run.
PdM software also enables companies to optimize their maintenance schedules by identifying trends and pattenrs in equipment performance through historical data analysis and real-time condition monitoring.
Key capabilities of PdM software include:
Reliability-Centered Maintenance (RCM) software is tailored specifically to support the reliability centered maintenance methodology. This software helps organizations understand the potential causes of asset failure and prioritize maintenance based on safety, operational, and economic consequences, allowing organizations to allocate resources more effectively.
RCM integrates with sensors and monitoring systems to track asset performance and conditions in real-time and suggests the most appropriate maintenance tasks based on the asset’s risks and failure modes. By focusing on the maintenance activities that have the most impact on reliability and safety, RCM helps to avoid unnecessary maintenance activities, thus reducing maintenance costs.
RCM can be integrated with other software solutions for a more comprehensive approach to maintenance management.
Key capabilities of RCM include:
Maintenance scheduling software is a type of application specifically designed to assist organizations in planning, coordinating, and tracking maintenance activities to ensure they are completed efficiently and on time. It plays a crucial role in both minimizing equipment downtime and maximizing productivity by ensuring that all maintenance tasks are systematically organized and executed according to a set schedule.
Maintenance scheduling software automatically schedules maintenance tasks based on preset intervals, usage metrics, or condition-monitoring data. It can integrate data from preventive and predictive maintenance strategies to optimize the timing and scope of scheduled maintenance activities. This software also helps to optimize resource allocation to ensure that all tasks are covered without overloading resources.
Key capabilities of maintenance scheduling software include:
Asset performance management software is designed to optimize the performance, reliability, and availability of physical assets throughout their lifecycle. This type of software helps organizations monitor and manage the health of their equipment and infrastructure to reduce downtime, increase longevity, and improve overall operational efficiency.
APM enables organizations to shift from costly reactive maintenance strategies to more cost-effective predictive and reliability-centered maintenance approaches. It provides comprehensive data and analytics that enables organizations to make informed decisions related to their asset management strategies.
Key capabilities of APM include:
A maintenance manager fulfills a vital role between a maintenance director or another top-level executive and the supervisors and technicians who perform the bulk of the service work. The role requires a unique mix of technical skills and business acumen to see the big picture while also addressing day-to-day issues and needs.
Given the complexities of maintenance work activities that take place at many companies, the job responsibilities of a maintenance manager can cover a broad scope. Some of the significant areas of focus include:
A maintenance manager can wear many hats, and there are some similarities with the responsibilities of a facilities manager or asset manager. As a leadership position, many technical and soft skills are also desired in a maintenance manager. Some of the most sought-after skills are:
A maintenance manager must balance a company’s performance goals with the realities of equipment capabilities. In highly specialized industries that serve a large number of customers, such as aerospace and healthcare, the stakes are even higher. This is the main reason why a good balance between soft skills and technical knowledge is required to be an effective maintenance manager.
It’s only with close cross-departmental collaboration that companies can create a robust maintenance management program. Maintenance work should never take place in a vacuum, and it’s vital for managers to solicit feedback from technicians, operators, and other staff that interact with equipment.
Current trends in maintenance management are largely centered on technology. As more sophisticated technologies become available, a growing number of organizations are embracing these tools to optimize asset performance and extend the useful lifespan of equipment while minimizing maintenance costs.
Here’s a closer look at the current trends in maintenance management.
As maintenance becomes more data-driven, facilities are increasingly adopting smart sensors that monitor conditions in real-time to preemptively address potential issues. This involves tracking vibrations, temperatures, and other indicators to predict and prevent equipment failures.
Along with this, predictive maintenance continues to gain popularity. Predictive maintenance, as described previously, is a shift from corrective maintenance and even goes beyond preventive maintenance.
Rather than waiting for equipment to fail and dealing with the consequences of unplanned downtime, predictive maintenance uses sensors and monitoring systems to analyze equipment performance and predict when maintenance is needed. There’s a growing adoption of techniques that range from basic anomaly detection to sophisticated models predicting the remaining useful life (RUL) of machinery.
Augmented reality (AR) and virtual reality (VR) are being utilized to enhance training and maintenance procedures. AR can significantly reduce errors and increase efficiency by providing real-time, on-the-job guidance. Technicians receive overlay visual prompts and step-by-step instructions while they work, which helps in reducing guesswork and streamlining complex tasks.
It can also help reduce the costs associated with traditional training methods, such as creating physical mock-ups or taking equipment offline for training purposes. This provides a safe and controlled environment where maintenance personnel can learn and practice skills without the risk of damaging equipment or causing operational downtime.
Additionally, training in a virtual environment allows maintenance personnel to experience and react to potential hazardous situations in a controlled and risk-free setting. This better prepares them for real-world scenarios, enhancing overall safety.
A related trend to immersive technologies, digital twins are virtual models designed to accurately reflect a physical object, system, or process. They’re used to simulate, predict, and optimize the performance and maintenance of physical assets through real-time data updates and analytics. This technology enables detailed analysis and testing without the risks and costs associated with manipulating the actual assets.
Digital twins support predictive maintenance by simulating how equipment will perform under various conditions and predicting when it might fail. Organizations can also simulate different maintenance scenarios to find the most cost-effective approach without having to experiment on the actual equipment.
Simulating equipment performance in a virtual environment allows potential issues to be identified and resolved before they become hazardous in the real world. This significantly enhances safety for both the equipment and the operators.
Organizations are increasingly taking a more holistic approach to maintenance management, integrating maintenance with other business practices, such as supply chain management, production planning, and human resources.
This integration allows for smoother operations across departments. For example, linking maintenance data with ERP systems can streamline the procurement of spare parts and inventory management, reducing downtime and operational delays.
By having maintenance data feed into broader business analytics, organizations can gain more comprehensive insights into how maintenance activities impact overall business performance. This holistic view supports better strategic decision-making and helps in prioritizing maintenance tasks based on their impact on business operations.
Additionally, linking maintenance management with production systems allows for real-time adjustments in production planning based on the current status of equipment. This helps maximize asset utilization and minimizes disruptions due to equipment failures.
Remote equipment monitoring refers to the use of sensors and network technology, such as IoT devices, to track the performance and condition of machinery from a distance. This technology collects data such as temperature, vibration, and output levels, which is then transmitted to centralized systems where it can be monitored and analyzed in real time.
Monitoring equipment remotely reduces the need for physical inspections, which can be costly, time-consuming, and sometimes hazardous. This can significantly cut down travel and labor costs, especially for businesses operating over large geographic areas or difficult-to-access locations.
It also allows companies to identify potential safety hazards before they pose a risk to operations or personnel, enhancing workplace safety and aiding in compliance with regulatory standards.
Remote equipment monitoring is part of a broader shift towards smarter, more connected industrial operations known as the Industrial Internet of Things (IIoT). As technology continues to advance, the adoption of remote monitoring is expected to increase, driving efficiencies and competitive advantage in maintenance management across various industries.
Robots and automated systems can operate continuously and perform tasks with precision that might be difficult to achieve manually. This leads to improvements in the quality of maintenance work and reduces human error, thereby increasing the overall reliability of equipment.
Robots can also access areas that are difficult or unsafe for humans, ensuring that maintenance can be performed without compromising safety. Although the initial investment in robotics may be high, over time, they can reduce labor costs and minimize costly downtime by ensuring maintenance is done promptly, correctly, and safely.
Additionally, these systems can be scaled up or down based on the needs of the business. As operations expand, additional robots can be seamlessly integrated into the maintenance routines without the need for extensive training that would be necessary for human workers.
The trend towards using 3D printing for on-demand parts in maintenance management is driven by its potential to enhance operational efficiency, reduce costs, and improve service response times. It enables the production of parts only when needed, significantly reducing the need for large inventories of spare parts. This not only saves on storage space but also reduces capital tied up in stock that might become obsolete.
Plus, the ability to print parts on-site or nearby reduces the waiting time associated with ordering and shipping replacement parts from suppliers. This rapid response capability is crucial for industries where downtime is extremely costly.
3D printing also allows for the customization of parts to meet specific requirements without the need for costly retooling. It also supports the maintenance of older equipment where original parts may no longer be available from manufacturers.
As 3D printing technology continues to advance, its adoption is expected to grow, establishing it as a critical tool in modern maintenance strategies.
Collaboration and knowledge management in maintenance management involve the systematic sharing and organization of information, expertise, and communication across various levels of an organization. This strategy ensures that valuable maintenance insights and operational knowledge are not only shared but also retained within the organization.
Digital tools and platforms help to facilitate the sharing of documents, maintenance schedules, real-time data, and best practices among team members. By facilitating smooth communication and collaboration across different departments and teams, organizations can avoid the silos that often slow down response times and create inefficiencies in handling equipment maintenance.
Sharing knowledge widely also helps in standardizing practices and upskilling the workforce. New employees can learn from documented experiences and expertise, improving the overall skill level within the maintenance team.
Additionally, by having a robust system where issues and their resolutions are recorded and shared, the maintenance team can avoid reinventing the solution wheel. This leads to quicker fixes for common problems and reduces the time and resources spent on repeat issues.
A collaborative and well-informed workforce can also pivot more effectively to meet changing operational demands. In rapidly changing industrial environments, the ability to adapt and respond to new challenges is crucial.
The main objective of maintenance is to ensure that equipment and systems operate reliably and efficiently over their expected lifetimes. This involves preventing equipment failures, minimizing downtime, and ensuring that all assets perform at their intended capacity.
A maintenance checklist is a tool used to ensure that all necessary maintenance tasks are performed correctly and completely. It lists all the items needing to be checked, inspected, or replaced during maintenance activities and helps technicians ensure nothing is overlooked, enhancing safety and efficiency.
Maintenance generally refers to regular, routine actions taken to keep equipment running smoothly and prevent breakdowns (e.g., lubrication, cleaning, inspection). Repair, on the other hand, involves actions taken to fix equipment that is already broken or malfunctioning. Maintenance is proactive, while repair is typically reactive.
Maintenance is considered a high-risk activity because it often involves working with complex machinery, high voltages, chemicals, or moving parts. There is also the potential for exposure to hazardous conditions or materials. The risk is increased when maintenance is performed under time constraints or without proper safety measures in place.
A SMART goal for maintenance is specific, measurable, achievable, relevant, and time-bound. For example, “Reduce equipment downtime by 20% within the next 12 months through the implementation of a predictive maintenance program.” This goal is clear, quantifiable, realistic, directly related to maintenance performance, and has a defined timeframe.
Our sales engineers are experts in automatic asset tracking, tagging and identification,a nd can answer all your questions. Get in touch now.
Lets Talk ›Enter your information and get a free checklist of the top questions to answer to plan a successful asset tagging project for any maintenance tracking or facility management system.