6 Ways to Improve Warehouse Inventory Control
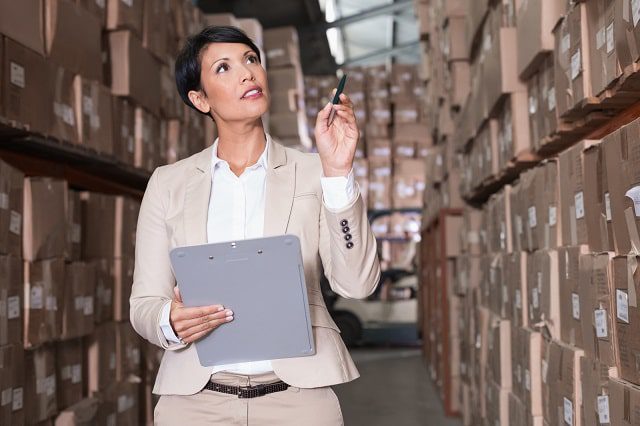
Warehouses are under constant pressure to maintain accurate inventory counts (i.e. “warehouse inventory control”) while processing hundreds or thousands of units on any given day. Maintaining complete control of operations requires warehouse managers to develop proper practices for streamlining workflows and reducing errors in inventory counting and warehouse management processes.
To process orders in an efficient manner, each warehouse should properly track the stocking level, condition, and locations of each inventory item they manage. To help organize their work, most warehouses implement a Warehouse Management System (WMS) that centralizes all of their important data, including inventory management information.
In this post, we’ll explore some important tips for improving inventory control. These techniques cover many different aspects of the warehouse and can improve the efficiency of important inventory processes such as stocking, picking, and cycle counting.
When it comes to warehouse inventory control, automation has become a priority due to the many efficiencies that can be gained from these new technologies. There are many hardware and software options available, most of which can be optimized based on a particular warehouse layout.
Some examples include conveyor belts, robotics, barcode scanners, and warehouse rack labels (including cold storage rack labels and rack placards), container labels, pallet barcode labels, and RFID tags. Replacing manual item entry tasks can drastically reduce errors and lead to more accurate cycle counts and inventory levels.
The warehouse manager is an essential role that oversees processes for maintaining proper inventory controls. One of the biggest challenges for any warehouse is achieving complete visibility of the inventory status, maintenance activities, and logistics flow in and out of the facility.
The warehouse manager is at the center of all these warehouse inventory control activities and is also the point person for addressing local issues and managing the day-to-day needs of staff and suppliers. Delegating proper authority to this person and their team can help speed up troubleshooting and the adoption of local solutions.
Utilizing a WMS platform helps to centralize all important warehouse workflows and information, but the local staff must find ways to organize the system and keep it up to date. A comprehensive inventory history makes it easy to troubleshoot issues and verify past product movements within the building.
Each item should have a unique serial number that is listed in the WMS with additional tracking for lots and other bulk storage identifiers. Any electronic system is only as good as the information you enter into it, and data accuracy is key to maintaining proper warehouse inventory control.
Another improvement that can benefit most warehouses is to conduct a complete review of the warehouse layout and organization plan. As a very active work environment, even the slightest confusion on the warehouse floor can lead to lost items, injuries, and delays.
Clearly labeling warehouse racks, travel lanes, and equipment will provide a safer work environment and help keep your staff focused on fulfilling orders and performing their most important work tasks.
It is also a great exercise to choose optimal locations for safety signage, barcodes, and labels so that employees can easily interact with these important notifications throughout the day. For example, long-range retro-reflective barcode labels and signs allow for long-range scanning, which can reduce the time needed for warehouse workers to find the correct storage locations.
Warehouse aisle signs and outdoor warehouse signs offer clear markings and identification for aisle numbers, dock locations, and other areas for easy navigation.
In addition to focusing on warehouse efficiency, there are a number of other important metrics that should be reviewed on a regular basis as part of effective warehouse inventory control.
Today’s WMS systems have excellent reporting features that allow you to integrate various data inputs and create customizable charts and reports. It is also possible to review real-time data for many inventory metrics, making it easy to quickly identify any issues, as well as generate reports for periodic inventory audits.
Regularly reviewing the performance of each department within the warehouse can help improve decision-making and is the single best way to drive improvements over time. Changes made on the warehouse floor should be designed so that they have a positive impact on your key performance indicators (KPIs).
To maintain an accurate inventory, it can be helpful to create an aggressive schedule for cycle counts. Verifying inventory levels only on an annual basis or other long timeframes can lead to issues with inventory accuracy.
Even with regular inventory counts, it is still difficult to verify whether the actual inventory levels match those within the electronic system, especially when tracking thousands of SKUs.
Cycle counts have become a popular method for verifying inventory levels because they can be performed continuously at set intervals and add a level of reliability to existing inventory practices.
Managing arrivals, cycle counts, and omnichannel logistics for the modern warehouse is a dynamic job when it comes to warehouse inventory control, one that relies on many important resources and tools. The improvements mentioned in this post are a great reminder that focusing on fundamental practices can lead to breakthroughs in warehouse efficiency.
Managing a warehouse is truly a team effort and, with proper controls in place, it can be a reliable resource for even the most complex logistics operations.
Our sales engineers are experts in automatic asset tracking, tagging and identification,a nd can answer all your questions. Get in touch now.
Lets Talk ›Enter your information and get a free checklist of the top questions to answer and tips to plan a successful asset tagging project for any warehouse management system implementation.