What is Integrated Facilities Management (IFM)?
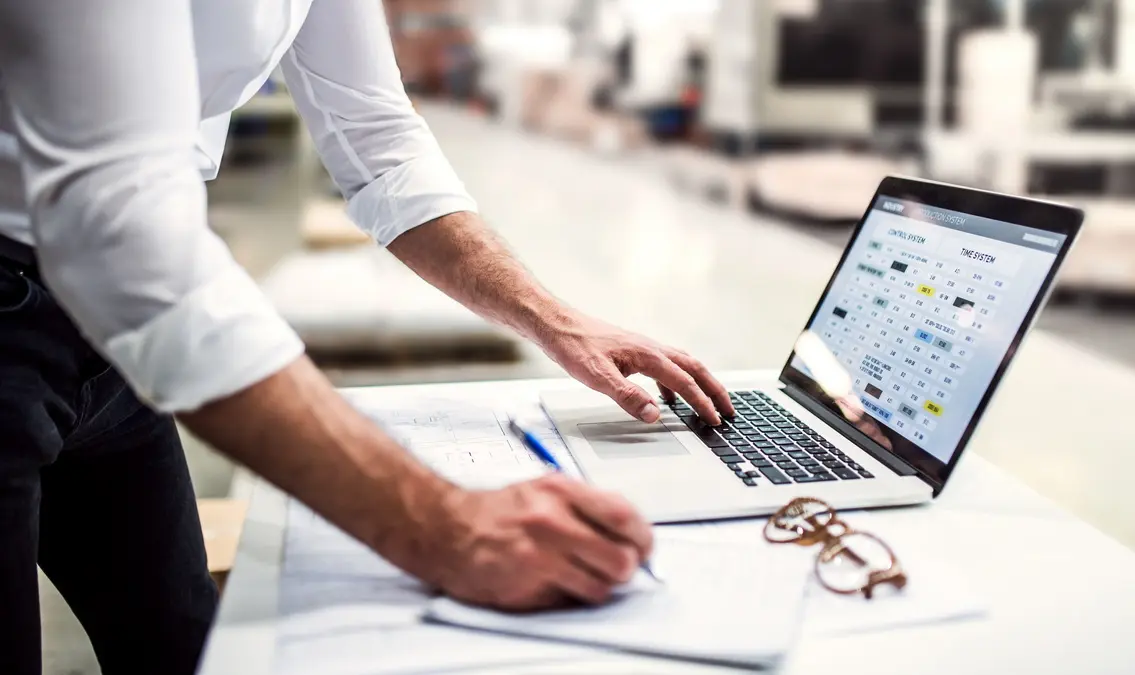
There are many moving parts to managing a facility, from hygiene to vendor management to energy usage. Smaller organizations can get by with piecemeal systems, but scaling up requires a more holistic approach that brings all facilities activities into a single view.
That’s where integrated facilities management (IFM) comes in. This more integrated version of facilities management brings every aspect of a facility into a streamlined software solution. IFM software helps organizations reduce costs, maintain a safe environment, and even increase productivity.
Whether you’re a facilities manager, business leader, or simply curious about optimizing organizational efficiency, understanding IFM can offer valuable insights into creating smarter, more connected workplaces. In this guide, we’ll explain what IFM is, why it’s beneficial, and how to maximize IFM for your organization.
Integrated facilities management brings all of a company’s facilities and related services into one system. Instead of managing disparate processes individually, IFM brings everything into a unified framework, resulting in a more streamlined approach that reduces costs, miscommunications, and rework.
This approach makes it much easier for organizations with multiple facilities to deliver consistent quality across locations.
Traditional facilities management (FM) allows facility managers to gain more control over maintenance, security, cleaning, and space management. However, this approach doesn’t always bring these services into a single view, which can cause miscommunications, errors, and higher costs.
Both FM and IFM are usually conducted in-house with a few outsourced vendors, while total facilities management (TFM) involves outsourcing all facility management to a single external provider. This option is more expensive but offers a turnkey solution for organizations without an internal facility manager.
Integrated facilities management encompasses all activities that keep a building in excellent condition. That includes various components such as:
Under IFM, a facility manager oversees everything from maintaining desktop computers to security cameras. It would be impossible to track everything manually, even in a small facility.
Facility management software is a must-have for staying on top of the numerous tasks required to keep a facility running. Not only does the software streamline facilities workflows, but it also measures the effectiveness of the facilities team and helps leaders spot areas for improvement.
Integrated facilities management may seem overwhelming, but this holistic approach reduces the burden of facilities management. There are so many benefits to consolidating multiple facility processes under one centralized system.
Hidden inefficiencies cost organizations thousands of dollars every year. The more integrated your facility’s data, the better your chance of spotting and addressing inefficiencies.
More streamlined facility processes equal fewer wasted materials, man-hours, and space. Plus, integrating services can reduce the costs associated with outsourcing to multiple vendors.
With IFM, there’s a single point of contact for all facility management needs. There’s a single source of truth for every aspect of the facility, which reduces duplicate information and miscommunications.
This benefit is especially important for large or multi-location organizations because it ensures consistent quality across all locations.
IFM platforms collect data across all facility operations, so instead of checking multiple systems, you have a single source of truth that provides actionable insights into facility performance.
In fact, some platforms now use artificial intelligence (AI) to automatically generate these insights in less time, helping you make better decisions.
Some leaders fear expansion because of the difficulty of managing multiple facilities or a larger facility. Following the principles of integrated facilities management makes it much easier to upscale your facilities, which, in turn, can allow you to quickly respond to your business’s changing needs – regardless of size.
Whether it’s local health codes or strict compliance rules for your industry, your business has to comply with a patchwork of regulations. Managing compliance can be difficult, especially across multiple systems and processes.
IFM reduces the headaches of compliance by bringing all systems into a single view. In fact, some IFM platforms come with built-in checklists for health, safety, and regulatory standards to reduce your risk.
IFM brings all vendor contracts into a single system. Not only that, but it can also track expenditures, document communications, and monitor service level agreements (SLAs).
This data allows facility managers to maximize the value of vendors and even negotiate better contract terms.
Managing facilities manually just isn’t realistic, and facilities managers from organizations of all sizes rely on software solutions to make sense of the dozens of disparate systems in their organizations.
IFM software usually includes the following key technologies.
CAFM helps facility managers optimize their existing space through floor planning and space utilization. These systems can generate 3D renderings of a facility, making it much easier for facility managers to test new configurations.
IWMS systems focus primarily on the physical facility. These solutions help facility managers manage space, track assets, log energy usage and act as a centralized repository of all facility assets.
IWMS sounds similar to CAFM, but it handles a broader range of activities, making it a better option for multi-location or enterprise businesses.
All facilities require maintenance, and CMMS tracks all maintenance activities, from cleaning boilers to changing lightbulbs. The system logs all maintenance activities and provides work orders, schedules preventive maintenance, and tracks replacement parts.
Smart buildings are the future, and BAS makes it possible to automate HVAC, lighting, and security, helping organizations cut costs while boosting performance and safety.
Implementing BAS into an IFM platform makes it possible to centralize, control, and monitor all automations without switching between platforms.
Integrated facilities management solutions track a lot of data. Monitoring key performance indicators (KPIs) and metrics tells you whether your facilities are running optimally or if you need to rethink your approach.
But which data points are actually helpful? These key KPIs will help you measure and improve the effectiveness of IFM:
Integrated facilities management is a game-changer for multi-location facilities. However, facility managers must follow the right processes to see value from IFM. Follow these best practices to maximize the value of IFM in your organization.
The right software will automate and streamline IFM. Use Integrated Workplace Management Systems (IWMS), Computer-Aided Facility Management (CAFM) software, Building Automation Systems (BAS), and IoT devices to bring all of your facilities data into a single cohesive view.
Take advantage of free trials and demos to find the most intuitive platform for your team.
IFM software does a lot of the heavy lifting for facilities teams, but it can’t do everything. For example, it’s up to employees to scan or log information in the IFM system, and the reliability of the entire system hinges on the quality of data gathered in the field.
That’s why more organizations invest in labels and tags and scannable barcodes and QR codes are a must for implementing IFM processes and tools.
For example, Camcode’s labels and tags simplify maintenance tracking with clear, durable labels that last in even the harshest environments. Whether it’s barcode tags for your warehouse or maintenance QRs on heavy machinery, heavy-duty labels show the physical reality of your facility in your IFM software.
Software can’t do everything, and facilities teams need to understand facility processes and how to leverage IFM software to streamline their workflows.
That requires upfront and ongoing training to stay up-to-date with the latest standards, technologies, and legal requirements. Lunch-and-learns, annual classroom training, or digital microlearning platforms are effective ways to upskill facilities teams.
Best practices will get you far, but ultimately, effective implementation is the key to successful integrated facilities management. Follow these practical tips for a smoother IFM implementation.
What do you need your IFM processes and software to do? Every organization is unique, so it’s best to start with a needs assessment to outline your must-haves. This approach will help you pick the right technologies and solutions for your needs.
Identify what your system is doing well right now and any areas for improvement. If you plan to outsource to vendors, it’s also a good idea to define the scope of service you need.
It might sound like an extra step, but a needs assessment ensures you only pay for what you use and make the most of your resources.
Integrated facilities management just isn’t possible without the right software, but all software comes with a learning curve. Fortunately, you can minimize rework and confusion by asking your IFM software vendor for help with the implementation.
That might include employee training, on-site assistance, or 24/7 support. Leveraging the vendor’s expertise will help you see a faster time to value and minimize employee confusion.
Data is the lifeblood of effective IFM, and the benefit of an integrated solution is the ability to monitor all facility systems and processes in real time.
Some IFM software offers readymade dashboards off the shelf, but creating a custom dashboard with the metrics you care about most is always best. These customized real-time dashboards alert you about potential issues ASAP, helping to reduce unexpected downtime and damage from time-sensitive issues, like plumbing leaks.
Integrated facilities management is a powerful strategy for streamlining facility operations and reducing costs. Unlock the power of your organization’s work environment and better align facilities management with your broader business goals by following the principles of IFM.
Innovative tools are essential to IFM success. That’s why organizations rely on Camcode’s durable labels and tags. Track assets, manage inventory, and stay compliant with our high-quality labels rated to last up to 20 years.
You can see the Camcode difference for yourself: request your free label and tag sample kit today.
Integrated facilities management (IFM) centralizes all facility processes under one framework. It usually requires both in-house and external vendors. On the other hand, total facilities management (TFM) outsources all aspects of facility management to a single vendor.
Integrated facilities management services centralize all facility-related services into one department, team, or vendor. They include maintenance, cleaning, security, sustainability, and space planning. The goal of IFM is to consolidate all processes into a single platform to reduce costs and improve productivity.
According to the International Facility Management Association (IFMA), facility management integrates:
Our sales engineers are experts in automatic asset tracking, tagging and identification,a nd can answer all your questions. Get in touch now.
Lets Talk ›Enter your information and get a free checklist of the top questions to answer to plan a successful asset tagging project for any maintenance tracking or facility management system.