5 Ways To Reduce Facility Maintenance Costs
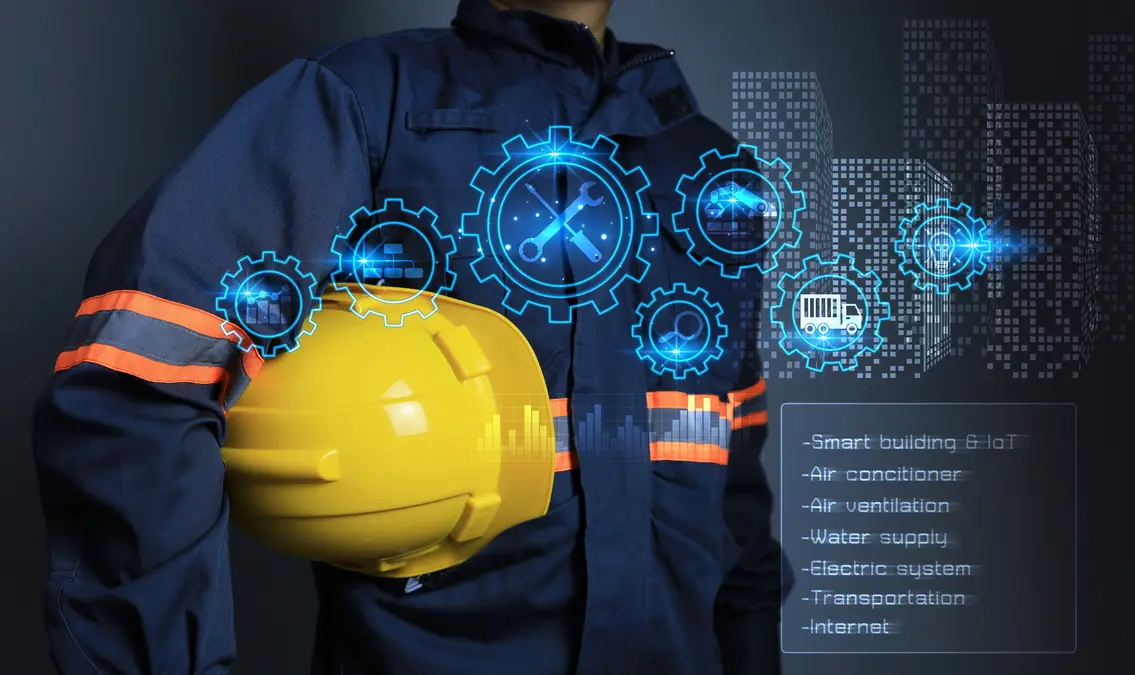
Facility maintenance is mandatory to keep your organization’s facilities running smoothly. However, improperly managed maintenance programs can become a significant expense.
It’s critical for businesses to strike a balance between maintaining assets in good condition and controlling costs. That’s why many organizations follow facility maintenance expense management best practices, which maximize maintenance efficiency while reducing costs.
Check out this guide to better understand average facility maintenance costs and how organizations of any size can minimize these expenses.
Facility maintenance is the regular upkeep of a building or property. The ultimate goal is to keep the facility safe, efficient, and functional. Every facility is different, but most use a mixture of these maintenance strategies:
While corrective and emergency maintenance might appear more affordable at first, they can result in additional unexpected breakdowns that cost more in the long run.
Preventive and predictive maintenance help you stay ahead of these concerns.
However, organizations sometimes overdo it with these maintenance strategies, paying more for parts and repairs than necessary. Regardless of your maintenance strategy, you still need a plan to maximize value and reduce expenses.
It can cost millions of dollars to keep facilities running efficiently. Organizations should budget for these everyday maintenance tasks:
Keeping a facility clean and functional is expensive. Maintaining additional equipment, such as heavy machinery, increases these costs even more.
Facility maintenance costs add up quickly, but proactive planning helps you manage and reduce these expenses. Follow these best practices to control facility maintenance costs.
It’s impossible to manage all facility maintenance tasks and assets manually. Sign up for an asset-tracking tool to monitor asset performance, maintenance history, and downtime.
These tools also streamline operations, prevent unnecessary spending, and make it easy to plan equipment replacements.
Instead of purchasing different equipment for the facility, always buy the same model or from the same manufacturer. Standardization allows you to keep just one set of replacement parts for each system.
It also means facility teams only need to follow instructions for a single manufacturer, which reduces miscommunications.
Communication is key to managing facility maintenance effectively. Camcode’s durable labels and tags improve asset tracking and maintenance schedules by providing easy-to-read, scannable information.
With scannable, human-readable tags, your teams know exactly where the equipment is and what repairs are due. Plus, opting for durable labels saves money by avoiding frequent replacements and ensuring consistent performance over time.
Many facilities rely on third-party contractors for lawn care, HVAC, plumbing, and more. While it’s important to establish long-term relationships with quality vendors, you should still negotiate their rates.
Use enterprise planning software (ERP) to track vendor contracts and negotiate rates. Many providers are happy to cut you a deal for longer-term contracts or bundled services.
Complex tasks like plumbing and electrical work belong to certified professionals, but you don’t need to call these expensive experts for every project.
Empower your in-house staff to handle minor repairs and inspections. This way, they can resolve issues immediately and reduce the company’s reliance on expensive external providers.
Reducing facility maintenance costs requires a strategic approach that combines proactive maintenance, effective asset tracking, and smart investments in durable materials.
Ultimately, thoughtful planning and adopting best practices help businesses control maintenance expenses, improve operational efficiency, and avoid costly downtime, ensuring a more sustainable and well-managed facility.
Solutions like Camcode’s durable labels and tags improve communication, streamline asset tracking, and ensure maintenance tasks are completed efficiently. See the Camcode difference: request your free Camcode label and tag evaluation kit now.
Poorly managed facilities use more energy, frequently experience unplanned downtime, and pay higher insurance premiums. Poor maintenance can also lead to lower property value and unexpected expenses when assets fail prematurely.
Review vendor contracts annually to ensure you’re getting the best value. Comparing service providers and renegotiating terms helps facilities secure better pricing and service-level agreements. However, review these contracts before your renewal period so you have time to request quotes from other providers.
Facility managers use maintenance management systems to track and rank tasks based on urgency, asset value, and operational impact. For example, prioritizing preventive tasks for critical systems, such as HVAC or electrical, prevents costly emergency repairs.
Our sales engineers are experts in automatic asset tracking, tagging and identification,a nd can answer all your questions. Get in touch now.
Lets Talk ›Enter your information and get a free checklist of the top questions to answer to plan a successful asset tagging project for any maintenance tracking or facility management system.