What is Corrective Maintenance? Why Is It Important?
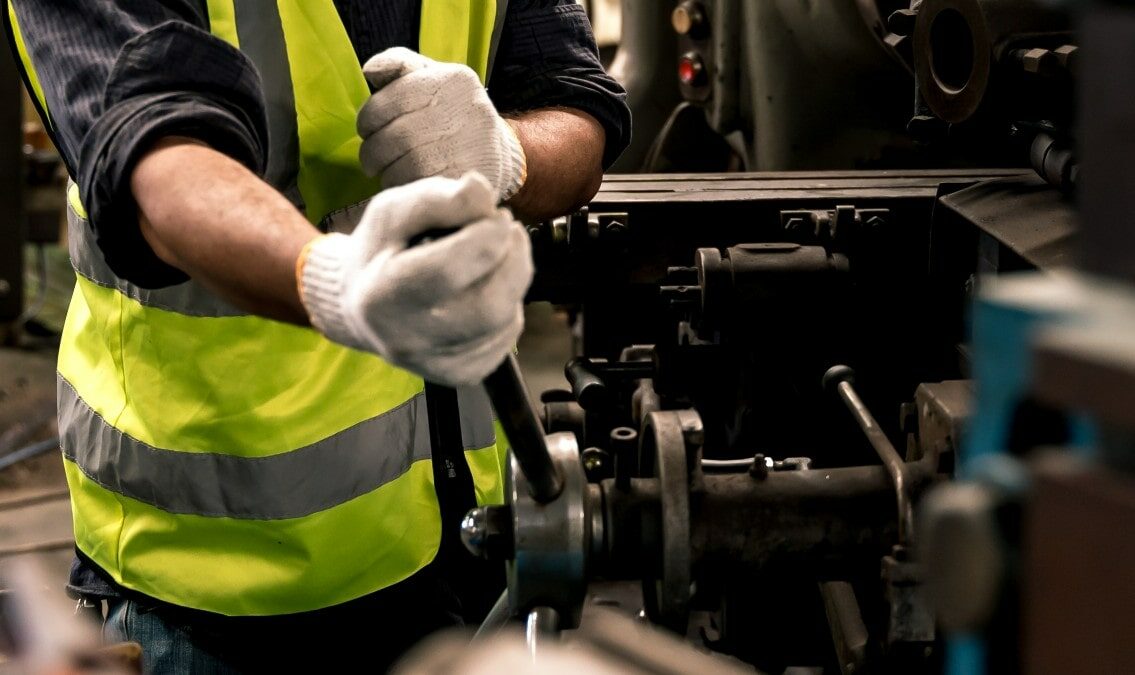
Unexpected maintenance events can occur at any time and having a plan of action in place for such instances may not always be possible. However, it’s essential to take corrective action right away.
Corrective maintenance is maintenance performed to return malfunctioning hardware or equipment to proper working order. It is is a critical component of any effective asset management strategy.
Corrective maintenance accounts for 20-30% of total maintenance activities in most organizations, according to industry estimates.
While often seen as a necessary evil, corrective maintenance plays a vital role:
While corrective maintenance is often viewed as a necessary evil, it plays a vital role in keeping operations running smoothly and minimizing the impact of unplanned downtime.
By understanding the key principles of corrective maintenance and implementing best practices, organizations can optimize this maintenance strategy to improve equipment reliability, reduce operating costs and enhance overall operational efficiency.
Corrective maintenance, also known as breakdown maintenance or repair maintenance, refers to the unscheduled maintenance activities performed to restore a system, component, equipment or asset to its operational state after a failure or breakdown has occurred. This process involves identifying and rectifying faults or defects that have caused the system to malfunction or cease to operate.
Type of Corrective Maintenance | Description |
---|---|
Deferred Corrective Maintenance | Postponing repairs until a more suitable time when the failure does not immediately impact operations |
Scheduled Corrective Maintenance | Planning and scheduling repairs during predetermined maintenance windows |
Predictive Corrective Maintenance | Using data analysis and condition monitoring to anticipate and address issues before failures occur |
The primary objective of corrective maintenance is to restore the functionality of the affected system or equipment as quickly as possible, minimizing downtime and associated productivity losses or disruptions.
It typically involves the following four steps:
Corrective maintenance is often reactive in nature, as it is triggered by a failure or breakdown event. However, it can also be proactive if potential failures or defects are identified through condition monitoring, predictive maintenance techniques, or routine inspections, allowing corrective actions to be taken before a complete failure occurs.
It is important to note that corrective maintenance is typically more costly and disruptive than preventive maintenance, since it involves unplanned downtime, spare parts procurement, and potential additional labor costs.
Effective maintenance strategies often aim to minimize the need for corrective maintenance by implementing preventive and predictive maintenance practices to identify and address potential issues before they lead to failures or breakdowns.
Corrective maintenance is an essential practice used by most organizations daily. With a comprehensive corrective maintenance program in place, facility management teams can prepare for the worst, even if they don’t know which mishaps might happen next.
These are just a few examples. Here are some additional examples of corrective maintenance focused on specific machines or equipment in a facility.
During a routine inspection, the facilities team notices that one of the forklifts is leaking hydraulic fluid. They immediately take the forklift out of service and create a corrective maintenance work order to diagnose the issue, replace the faulty hose or seal, and restore the forklift to full operating condition.
The building manager receives a report that one of the elevators is not responding to calls and is stuck on a floor. The facilities crew responds quickly to investigate the problem, which turns out to be a malfunctioning control board. They perform the necessary corrective maintenance to replace the faulty component and get the elevator back in service.
During the winter months, the facilities team notices that the boiler system is not maintaining the desired temperature in parts of the building. They initiate corrective maintenance to inspect the boiler, identify the root cause (e.g. faulty thermostat, clogged filters), and make the required repairs to restore proper heating functionality.
While performing preventive maintenance checks on the HVAC system, the facilities team discovers that one of the compressors is not operating at full capacity. They initiate a corrective maintenance project to safely remove and replace the faulty compressor to restore the system to peak performance.
Any type of unplanned maintenance that results in getting the broken-down equipment back to working order can be defined as corrective maintenance. The key is having the right processes, tools, and expertise to quickly diagnose and resolve equipment failures.
Corrective maintenance offers many advantages to businesses. Implementing corrective maintenance strategies allows decision-makers to control costs and save on human capital.
Key Stats to Consider:
When an organization wants to get the most out of their resources should consider the ways that corrective maintenance can improve their operational efficiencies:
Eliminating the need for pre-planning allows businesses to reduce costs by removing the need for preventative maintenance strategies. Although fixing or purchasing new equipment has associated costs, reactive maintenance strategies don’t require ongoing investments until failures occur.
Corrective maintenance is naturally simple and allows businesses to reduce the complexity of their asset management strategies. By reducing the amount of overhead required for management, corrective maintenance makes deploying equipment easier and less time-consuming.
Even with preventive maintenance, failures still occur. This reality can leave businesses investing in outdated equipment that’s no longer effective. Optimizing performance after failures allows businesses to mitigate unwanted costs associated with other maintenance strategies.
While corrective maintenance has many benefits, it can also lead to disruptions in operations and the inability to deliver timely service.
The benefits of corrective maintenance don’t always outweigh the costs. Applying only corrective maintenance, businesses can be left without the proper infrastructure for providing goods or services to end-users.
According to industry reports, businesses that rely primarily on corrective maintenance can see maintenance costs up to 3-5 times higher compared to those with a balanced preventive/corrective approach.
With less oversight, more expenses, and the potential for equipment failures, corrective maintenance might not always be the right solution for your business.
Corrective maintenance might be needed at any time. This unpredictability makes it difficult for decision-makers to make the best decisions about how funds and other resources should be allocated. Failures could mean unexpectedly high costs, which could put operations in jeopardy.
Performing ongoing maintenance and repairs saves money in the long term, and a lack of proper maintenance causes equipment to degrade faster and leads to inefficiencies. This degradation can hurt the business and its ability to deliver service to end-users.
For most businesses, equipment failures can mean the difference between success and failure. When equipment isn’t properly maintained, it can lead to interruptions in production. This downtime can create an unsafe environment and can damage the organization’s reputation over time.
While corrective maintenance is often a necessary response to unexpected equipment failures, there are proven best practices that can help organizations optimize this method of reactive maintenance strategy.
By following these best practices, organizations can optimize their corrective maintenance programs to improve equipment reliability, reduce costs, and enhance overall operational efficiency.
For the best results when relying on corrective maintenance strategies, businesses should consider using equipment asset tags with a comprehensive maintenance management solution.
Camcode’s Metalphoto® Anodized Aluminum equipment tags are designed to meet your application’s specifications, with the durability to withstand harsh environmental conditions — both indoors and out — and remain readable throughout the lifespan of your assets.
With the right asset tracking solutions and maintenance plans in place, you’ll have all you need to manage your essential equipment when failures occur.
Corrective maintenance is a response to maintenance events such as decreased production or other performance issues as they occur with the goal of restoring the equipment to its optimal working order. It aims to address performance issues before equipment actually breaks down, reducing the risk of business disruption.
Corrective maintenance enables businesses to identify issues, pinpoint the source of those issues, and take immediate action to repair or mitigate the problem.
The differences between corrective and preventive maintenance are as follows.
Corrective maintenance is a reactive approach that involves restoring equipment to working condition after a breakdown or unexpected failure has occurred.
This is in contrast to preventive maintenance, which is a proactive strategy focused on scheduled inspections, servicing, and repairs to avoid issues before they happen. Preventive maintenance, on the other hand, aims to keep equipment running smoothly, while corrective maintenance is about getting equipment back up and running after a problem arises.
Other maintenance strategies like predictive maintenance use condition monitoring to predict when maintenance will be needed.
Source: https://www.diva-portal.org/smash/get/diva2:1668825/FULLTEXT02
Our sales engineers are experts in automatic asset tracking, tagging and identification,a nd can answer all your questions. Get in touch now.
Lets Talk ›Enter your information and get a free checklist of the top questions to answer to plan a successful asset tagging project for any maintenance tracking or facility management system.