Corrective Maintenance vs Preventive Maintenance: What’s the Difference?
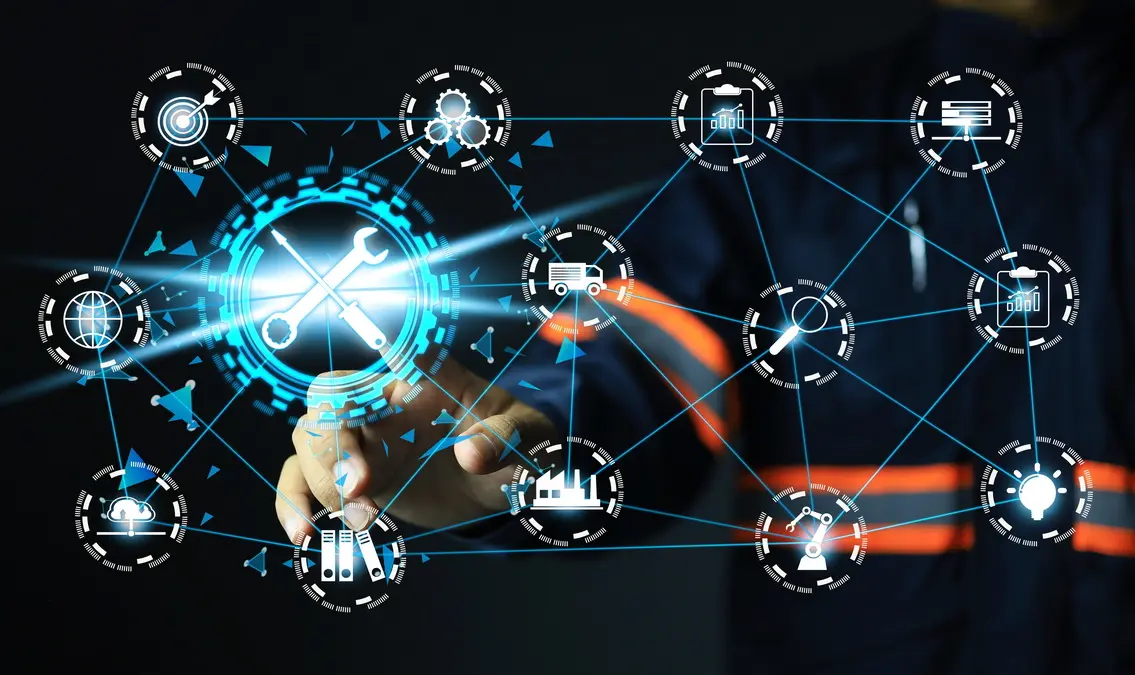
If you run a business, you know that maintaining your equipment is vital to keeping operations running smoothly. Should critical production or field assets fail to perform as needed, everything from breakdowns to bottlenecks to complete operational paralysis could occur.
Yet enterprise-level maintenance isn’t easy – it’s a complicated, intricate challenge that asset managers are constantly grappling with. Choosing the right servicing strategies can mean all the difference between coming in under your planned service budget for the year or being deep in the red.
This cost-driven, output-oriented environment explains the rise of corrective maintenance and preventive maintenance. However, when it comes to corrective maintenance vs preventive maintenance, the philosophies of each approach couldn’t be more different, yet both have their rightful place in the world of modern industrial servicing.
Understanding these strategies is a must for any asset manager. The best way to get started? With a closer look at what each strategy intends to accomplish.
The philosophy behind preventive maintenance can be boiled down to this: servicing an asset today in the hopes of preventing a breakdown tomorrow. In essence, preventive maintenance aims to perform routine, regular servicing in order to assess an asset’s condition and do basic, performance-enhancing procedures (such as fluid changes or calibrations) to keep it working as new.
The best example of preventive maintenance is an automotive oil change. This standard service is a requirement of all cars equipped with a combustion engine.
Even if your car is running fine, you regularly bring it to your mechanic nonetheless to drain the old lubricant and top it off with fresh oil. You do this because regular oil changes dramatically increase the life of your vehicle.
Never change the oil, and soon enough the engine will fail prematurely.
That mindset is at the crux of why many industrial asset managers have embraced preventive maintenance. Downtime is a costly business – by some accounts, an hour of downtime can cost a manufacturing facility $260,000. For another sobering statistic, consider that manufacturers around the globe spend a collective $50 billion every year dealing with unplanned downtime.
Oftentimes, routine maintenance may have lessened the impact of – or even entirely mitigated – a downtime event related to asset failure. As this knowledge has become more commonplace across the industry, preventive maintenance strategies have proven increasingly popular and relevant.
Corrective maintenance is also known as reactive maintenance, and for good reason: it’s a reactionary strategy that entails running an asset until it fails. Only once it malfunctions or breaks down are efforts made to address the situation and perform repairs.
While on first blush it may not appear as strategically sound as preventive maintenance, reactive service is still very much relevant in modern industries – the key, though, is to use it in support of the appropriate asset mix.
Take your facility’s lighting, for instance. Replacing these fixtures won’t be done routinely, as that would ultimately cost more money and drain more bandwidth than makes sense. Instead, once a light burns out, you’ll simply have a maintenance lead replace it.
It’s assets like these – easy to diagnose, service, and fix – where a run-to-failure strategy makes more sense than a preventive approach. Importantly, assets being maintained reactively should also have immaterial consequences to overall operations and output if and when they fail.
Asset classes that meet these parameters for reactive maintenance could include:
Check out the video below for a quick overview of corrective maintenance
To best understand the differences between these two strategies, we’ve compiled the primary features of both here.
This side-by-side breakdown illustrates the key ways in which they diverge – and also underscores their complementary nature. Because they’re so different, one plan’s weakness is the other’s strength, and together they can help you achieve your holistic asset management goals.
If you’re implementing a reliability-centered maintenance plan, this wide-lens perspective is important to keep in mind.
Attribute | Preventive Maintenance | Corrective Maintenance |
Service Philosophy | Performing proactive, pre-scheduled servicing. | Performing service only once repairs are needed. |
Costs | Upfront costs to create a preventive service plan may be significant, but long-term savings will likely be realized. | There are no upfront costs incurred, but may cost more long term due to unplanned downtime and potentially higher costs of expedited emergency servicing. |
Difficulty | Requires more upfront and ongoing effort. Demands effective short- and long-term asset planning. | Because it is reactionary in nature, there is no planning or strategic work to complicate asset management efforts. |
Goals | To increase asset longevity and reduce risks of surprise asset breakdowns and unplanned downtime. | To save money and time by minimizing maintenance costs and focusing on performing repairs only when necessary. |
Best For | Assets that are critical to operations, expensive, complex, long-lived, new, etc. | Assets that are secondary to operations, easy to fix or repair, slated to be retired or sold, etc. |
Implementing corrective and preventive maintenance in an organization requires a strategic approach to ensure equipment reliability and operational efficiency.
Combining these approaches ensures a balanced maintenance strategy that minimizes disruptions and optimizes asset performance.
It’s easy to think that preventive maintenance is always preferable to a reactive approach, but that’s not always the case. Beyond these strategies being complementary, it’s important to remember that every one of your critical assets will likely fail or break down at some time or another.
When that happens, you’ll want to have a plan in place: which technicians to call, where to source parts from and how to adjust your operations to compensate for the disruption. A well-optimized reactive maintenance plan accounts for these variables so that repairs can be made as timely as possible.
By managing your assets to account for reactive maintenance, while also incorporating the latest preventive technologies – such as advanced asset tracking or even predictive maintenance tools – you’re fortifying your operations against potentially crippling service issues.
The result? Lower costs, better-running machines, and a business that’s ready to handle any maintenance or repair challenge that comes its way.
Corrective maintenance, often referred to as “breakdown maintenance,” is a reactive approach to equipment upkeep. It involves fixing assets only when they fail or show signs of malfunction. This strategy can be cost-effective in the short term, but it may lead to unexpected downtime and higher repair costs over time.
Preventive maintenance is a proactive strategy aimed at preventing equipment breakdowns. It involves regular, scheduled inspections and maintenance tasks to keep assets in optimal working condition. By addressing potential issues before they become major problems, preventive maintenance minimizes downtime and reduces long-term repair costs.
The key difference lies in their timing and approach. Corrective maintenance reacts to failures, while preventive maintenance anticipates and addresses issues before they cause failures. Preventive maintenance can be more cost-effective and reliable in the long run, as it minimizes disruptions and prolongs the lifespan of equipment, whereas corrective maintenance can lead to unexpected downtime and higher repair expenses.
Our sales engineers are experts in automatic asset tracking, tagging and identification,a nd can answer all your questions. Get in touch now.
Lets Talk ›Enter your information and get a free checklist of the top questions to answer to plan a successful asset tagging project for any maintenance tracking or facility management system.