How to Create the Ideal Preventive Maintenance Schedule: 8 Steps and Expert Tips
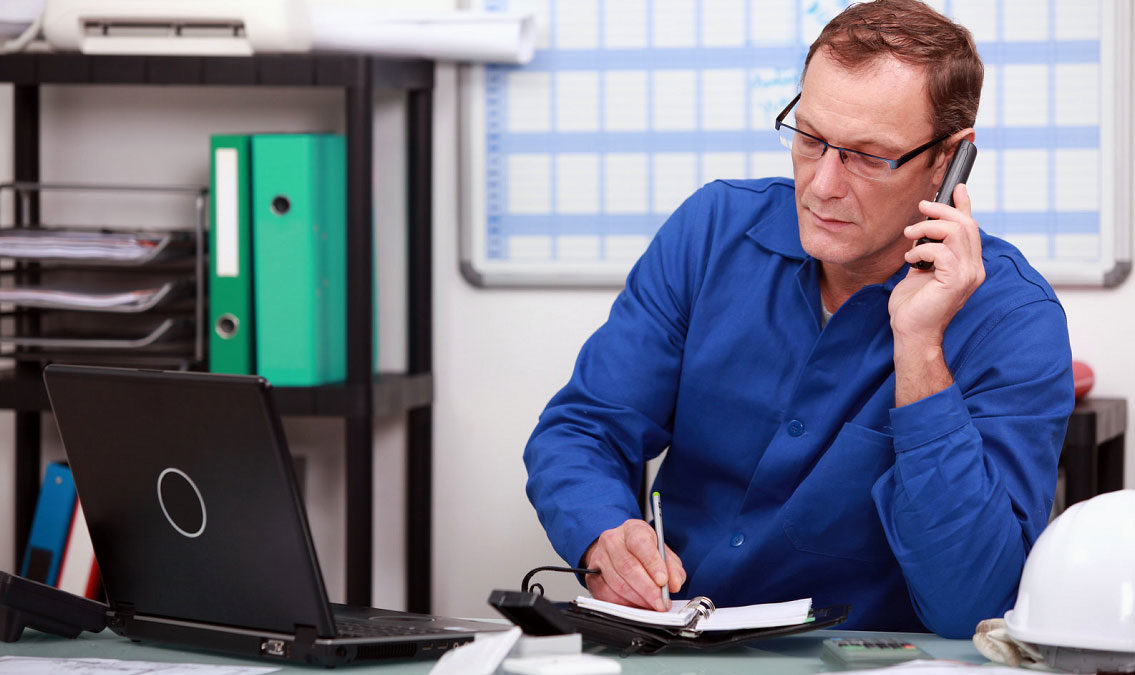
Preventive maintenance (PM) is a popular form of maintenance management that relies on scheduled interventions to maintain a high level of equipment performance. A proactive approach to maintenance helps to reduce the likelihood of equipment failures while giving a company control over how they manage their plan.
With a systematic approach, it is possible to develop a PM plan that is effective and improves the performance of managed assets.
In this post, we’re going to discuss how to create the ideal preventive maintenance schedule along with four important tips.
Keep in mind, one major risk with preventive maintenance is the potential to incur increased costs if too much work is performed than is truly required to maintain performance. This can be a difficult threshold to determine and requires attentiveness and patience while developing a preventive maintenance plan.
The suggestions presented in this post can help you leverage proven practices that have been shown to add clear value to maintenance planning.
A preventive maintenance schedule is a detailed plan that outlines the specific times and intervals at which maintenance tasks should be performed on equipment and systems. This schedule is a critical component of a preventive maintenance program, ensuring that all necessary inspections and servicing are conducted systematically to prevent equipment failures and extend the lifespan of assets.
Key aspects of a preventive maintenance schedule include:
By adhering to a preventive maintenance schedule, organizations can systematically manage their maintenance activities, leading to improved equipment reliability, reduced repair costs, and enhanced operational efficiency. A well-structured schedule helps in anticipating potential issues before they become major problems, thereby maintaining smooth and uninterrupted operations.
Now, let’s walk through the eight steps to create the ideal preventive maintenance schedule.
Creating an effective preventive maintenance schedule is crucial for ensuring the reliable operation and longevity of critical equipment and assets. The eight key steps involved in developing a comprehensive preventive maintenance schedule are outlined in the table below. Another effective solution is to build a preventive maintenance checklist.
By systematically working through these steps, organizations can proactively identify maintenance needs, optimize resource allocation, and minimize the risk of unexpected breakdowns.
Step | Description |
---|---|
1. Take inventory of assets | Identify all the critical equipment, assets, and infrastructure that require preventive maintenance. |
2. Prioritize assets | Determine which assets are most vital to business operations and have the highest maintenance needs. Focus on assets that are critical, have high repair costs, or are prone to failure. |
3. Determine maintenance triggers | Decide whether to base the maintenance schedule on time (e.g. monthly), usage (e.g. operating hours), or condition monitoring. This will depend on the asset type and available data. |
4. Identify maintenance tasks | List out all the specific inspection, servicing, and other maintenance tasks required for each asset based on manufacturer recommendations and historical data. |
5. Prioritize maintenance tasks | Rank the maintenance tasks by priority based on factors like asset criticality, safety risks, and operational impact. This will help manage workload. |
6. Assign responsibilities | Designate the specific employees or teams responsible for completing each maintenance task. Consider skill levels and scheduling constraints. |
7. Document the schedule | Create a structured preventive maintenance program and schedule, potentially using a CMMS or calendar system, to track all the tasks, frequencies, and assignments. |
8. Review and refine | Monitor the effectiveness of the preventive maintenance schedule and make adjustments over time based on performance data and feedback. |
Now that you’ve developed your preventive maintenance schedule, let’s some tips to help you streamline your plan to your company’s unique needs.
As most of us know, there’s a world of difference between ‘good’ and ‘good enough,’ and preventive maintenance (PM) plans are no different. You can put together a basic preventive maintenance schedule fairly easily, but to design one that’s effectively matched to your specific asset mix is another challenge altogether.
Despite the greater attention to detail required to optimize your maintenance plan, the results are well worth any additional time and expense. At its best, a PM schedule can maximize asset life, reduce downtime for both planned and unplanned maintenance, and mitigate the risk of partial or complete failure.
The better tailored these service roadmaps are to your business, the more impactful their benefits will be.
To help you realize these benefits, we’ve compiled seven of the highest-impact strategies you can incorporate into your company’s plan.
The nerve center of any modern asset-based preventive maintenance schedule is digital management software. These applications differ in form and scope, but all share the same basic premise: capitalize on artificial intelligence, cloud connectivity, and digital recordkeeping solutions to provide complete insight into a company’s assets down to each individual machine.
Examples of such software include Computer Maintenance Management System (CMMS), Enterprise Asset Management (EAM), and Reliability Centered Maintenance (RCM) programs.
All can support a high degree of data collection and analysis, which then allows the software to send upcoming maintenance reminders, automatically schedule work orders and more. The result? More data-driven insights and less time wasted.
Software has dramatically changed how specific asset information is accessed and stored. Not too long ago, records were paper-based – hard-copy work orders and physical maintenance logs, all usually stuffed into department filing cabinets.
Now, companies using an EAM or CMMS have digitized their records entirely.
Doing so results in much-improved data accessibility for all parties. For example, in the office, it’s easy for relevant stakeholders to access records and documentation. Meanwhile, on the shop floor, technicians and equipment operators can simply scan a machine’s asset tags to log real-time updates regarding completed services or other updates.
With the flow of information streamlined and brought online, an asset’s status is easily available, conveniently time-stamped and easily traced. The benefits are hard to overstate: data organized in this fashion can help expedite decisions, reduce the risk of lost documentation, and keep your preventive maintenance schedule on track.
The Plan, Do, Check, Act (PDCA) model is a popular preventive maintenance tool for creating clear policies for working with equipment. This acronym can inform your PM schedule and make it easier to develop effective policies and procedures. The PDCA model is defined as:
Unfortunately, the benefits of streamlining information can be reduced or even nullified completely if individual teams are too siloed from one another. Put simply, people need to feel comfortable reaching out to key contacts on other teams. It’s as critical for preventive maintenance as it is for so many other business functions.
Having a short list of specialists you can rely on for specific concerns is a strong place to start, but creating more organic collaborative opportunities can help foster a long-term symbiosis that will only benefit all involved.
Relationships like these matter when disparate individuals have to suddenly work together to address unexpected equipment downtime, specialized servicing, or other typical servicing woes. It’s also invaluable to simply share knowledge, tips, and ideas across divisions or teams.
A more communicative company is ultimately a more versatile, creative entity – something that will reflect in your PM planning.
If you’re looking for tips on how to improve communication between your teams, check out the video below:
The best technology and equipment is only as good as its primary user base. If protocols aren’t being followed as they should by operators or technicians, the effectiveness of solutions such as EAM or CMMS software will be negated.
The key to mitigating this risk is implementing scalable, replicable best practices that are minimally disruptive to those on the front lines of your business. These are protocols that can be followed regardless of variables such as staff changes, management shake-ups, and even new equipment purchases. They should provide guidance on responsibilities like reporting mechanical issues, logging service visits, performing safety inspections, and so on.
Asset tags are often at the crux of best practices. Why? Because they are easy to use, easy to install, and incredibly durable and resilient, even in the toughest environments.
Depending on your needs, you can create barcode labels, operating-procedure tags, and much more. These tags tether your physical equipment with your online operations, making a quality asset label a must-have solution.
When it comes to your preventive maintenance schedule, an easy way to streamline and minimize downtime is to group asset service needs by the consequences of postponing certain maintenance items.
Take a company work truck, for example. Perhaps the service manual calls for a timing belt change at 65,000 miles. The risk of not performing this service is a potentially catastrophic engine failure should the old belt give out; this could sideline the vehicle for weeks or even force the purchase of a new truck.
The risk level is high, so the service should be prioritized.
Now consider an engine or cabin air filter replacement for the same truck. While these services are necessary, they don’t carry nearly the same risk as something like a timing belt. Ultimately, there’s little impact if you go 500 or 1,000 miles beyond the recommended service mileage before upgrading the filters.
By thinking along these lines, you can better cluster maintenance visits and ensure critical services aren’t needlessly delayed – a move that could easily become an expensive lesson in how to prioritize industrial service needs.
Accounting for the changing service needs and expected ROI metrics for older assets is an easily overlooked aspect of maintenance planning. After all, every machine eventually wears out.
It’s not worth the risk of a sudden failure that’s inherent with older equipment, even for your most trusty workhorses that have been properly maintained.
By considering these factors proactively, you can make a data-driven assessment when determining whether to replace or repair an asset. On an enterprise level, staying cognizant of the cost and risk threshold to trigger a replacement rather than a repair can help avoid unexpected downtimes related to breakdowns.
Forward-thinking asset management like this will save time, money, and headache for all parties involved.
The above strategies are an excellent place to build and also customize your preventive maintenance schedule. They can also be a starting point from which to create an entirely new set of asset management standards.
Either way, remember that effective service plans are malleable and ever-changing. An adept leader will continually revisit and revise their strategy as equipment changes, new technologies are introduced, and operations scale.
Stay flexible, stay aware, and try to stay one step ahead of your maintenance needs by working smarter, not harder.
Camcode’s labels and tags can help make tracking your assets’ location and servicing needs a breeze, but don’t just take our word for it—order your free Camcode label sample kit now and see the difference for yourself.
Determine the optimal frequency for preventive maintenance tasks by considering equipment specifications, usage intensity, and manufacturer recommendations. Balancing regular maintenance to prevent breakdowns without causing excessive downtime is crucial.
Prioritize tasks based on asset criticality, safety implications, and historical failure data. Allocate resources to high-impact tasks first to minimize downtime risks and maintain operational continuity.
For a truly effective preventive maintenance schedule to be successful, you’ll need to access comprehensive asset histories, maintenance records, and performance data. Utilize specialized maintenance management software to streamline scheduling, monitor tasks, and analyze trends for informed decision-making.
Our sales engineers are experts in automatic asset tracking, tagging and identification,a nd can answer all your questions. Get in touch now.
Lets Talk ›Enter your information and get a free checklist of the top questions to answer to plan a successful asset tagging project for any maintenance tracking or facility management system.