What is Reliability-Centered Maintenance (RCM)?
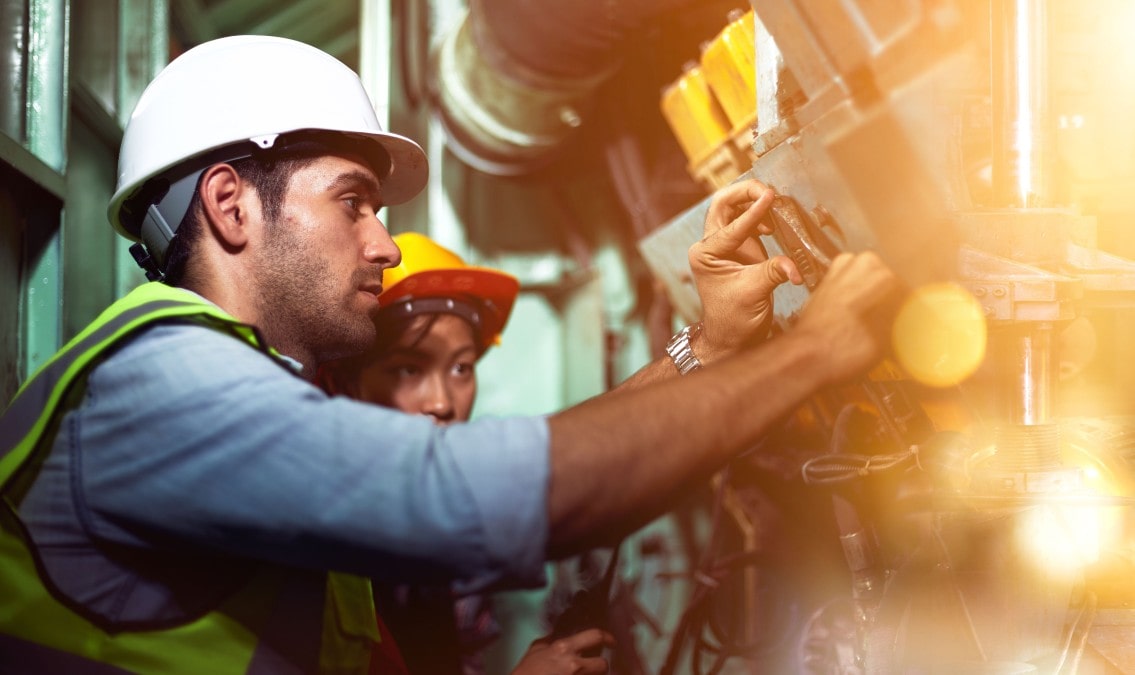
Oil and gas, construction, and manufacturing businesses rely on machinery to operate as efficiently as possible. This machinery makes complex processes more manageable, but even the most high-end machinery needs maintenance.
Instead of conducting maintenance every time there’s a breakdown, more businesses are embracing reliability-centered maintenance (RCM) to optimize the lifespans of their machines.
Four key elements of an RCM program are:
An RCM program is a very focused approach that is most often used for high-value and important assets. IT may not be as useful for subsystems and lower priority assets due to the intensive nature of failure analysis and follow-ups.
Reliability-centered maintenance is a great option to use with other approaches, such as preventive maintenance and predictive maintenance, as part of a company-wide maintenance program.
In this guide, we’ll explain reliability-centered maintenance, why it’s so beneficial, and how to implement RCM in your organization.
Every machine has a lifespan, but the more life you can get out of your machinery, the higher your return on investment (ROI).
All machines break down because of wear and tear, design flaws, and exposure to the elements. However, they could also break down without proper care and maintenance, which leads to a lot of downtime and lost earning potential.
According to a study by the U.S. Department of Energy, companies that implement RCM can see a 25-30% reduction in maintenance costs and a 15-25% increase in equipment availability.
Reliability-centered maintenance is a maintenance strategy that assesses the reliability of a piece of equipment or machine to conduct maintenance at the right time for that machine.
RCM is an organization-wide strategy that accounts for:
RCM is a proactive framework that keeps certain assets functioning for as long as possible. Unlike traditional reactive maintenance, RCM prioritizes the reliability of a machine to ensure it consistently performs to your standards without errors or failures.
More businesses are embracing reliability-centered maintenance to:
Reliability-centered maintenance includes several maintenance strategies to mitigate the risk of equipment failure, including:
Step | Description |
---|---|
1. Create an RCM Committee | Assemble a cross-functional team to oversee the RCM program, including members from maintenance, operations, engineering, and management. |
2. Identify Failure Modes | Systematically analyze each asset to identify potential failure modes and their effects on the business. |
3. Rank Failure Modes by Severity | Prioritize the identified failure modes based on their potential impact on safety, production, quality, and cost. |
4. Develop Maintenance Strategies | Determine the appropriate maintenance strategies (e.g. preventive, predictive, condition-based) to address each failure mode. |
5. Implement RCM Software | Use specialized RCM software to centralize asset data, maintenance plans, and performance metrics. |
6. Monitor and Optimize | Regularly review RCM program performance and make adjustments to maintenance strategies as needed. |
Learn more about the basics of reliability-centered maintenance in the following video:
While it might sound like a new approach to maintenance, RCM first appeared in the 1960s. At the time, aircraft manufacturers embraced RCM as a way to address safety concerns and increasing maintenance costs.
Today, various organizations outside the aviation industry use RCM to mitigate risks and simplify complex systems.
While any organization can conduct reliability-centered maintenance, it’s most common in these industries:
RCM is unique because it acknowledges that some assets are more critical than others. RCM programs also consider that your company has limited resources to dedicate to maintenance.
Ultimately, RCM helps businesses distribute their resources more efficiently to boost reliability without increasing costs. It’s the perfect method for prioritizing maintenance.
Reliability-centered maintenance actually uses a variety of maintenance methods. According to the O&M Best Practices Guide, top-performing companies divide their RCM strategies into these categories:
It’s important to note that most of your resources will go towards predictive maintenance with RCM.
RCM aims to move your organization away from reactive maintenance, which is when you only conduct maintenance when there’s a critical issue. Reactive maintenance leads to more downtime and expensive repairs, hurting your bottom line over time.
While preventive maintenance can help detect issues and prevent asset degradation, its regularly scheduled maintenance checks make it less cost-effective.
With RCM, you perform predictive maintenance based on the asset’s status and importance to your operations, saving both time and money.
While it requires some initial work to set up, reliability-centered maintenance comes with a host of benefits.
Every machine will break down eventually, but you can extend the healthy lifespan of an asset for several years with the right maintenance strategies. With RCM, you make maintenance decisions based on equipment conditions instead of predetermined routines.
With this approach, you still perform the minimum level of upkeep necessary to prevent malfunctions and failures. However, instead of following the same routine for every machine, RCM software helps you determine the safe minimum level of upkeep for every machine’s unique use case and history.
By extending the lifespan of an asset with proper maintenance, you won’t need to order replacements as often, either. This is a great way to increase uptime and decrease costs.
Reliability-centered maintenance is growing in popularity because it reduces maintenance costs. After all, when you know where to direct your efforts, you avoid overspending on unnecessary maintenance. RCM cuts down on maintenance costs and also reduces other costs that are harder to quantify, like the financial impact of downtime.
Plus, a successful RCM program helps you set realistic expectations of how much time and money you should spend on maintenance. With this information, you can budget more realistically for future replacements and repairs.
No one wants workplace injuries, but they’re much more common in organizations that fail to properly care for their machinery. With RCM, your team keeps up with proper maintenance to reduce safety problems caused by malfunctioning machinery.
If you’re in a heavily regulated industry like defense or aerospace, RCM can also support your compliance and risk management programs. By predicting and preventing failures, you avoid the headaches and expenses that come with falling out of compliance.
Unplanned downtime is bad for business. In a worst-case scenario, it could take days or even weeks to repair broken machinery. While RCM can’t account for every potential breakdown, it can significantly reduce downtime and keep your facility online when it matters most.
It’s hard to get out of a reactive maintenance mindset. It might take some time, but embracing reliability-centered maintenance will help your team embrace proactive action. Instead of spending their time putting out fires and treating every task like it’s an emergency, your team will enjoy the peace of mind that comes with proactive maintenance.
Reliability-centered maintenance software provides a framework that helps your team identify and fix issues before they cause big problems. Follow these steps to implement reliability-centered mainenance and mitigate potential failures.
If you don’t already have one, create an RCM committee. It’s tempting to staff the committee only with your maintenance team, but cross-sectional teams are better.
This way, you have insights into engineering, operations, and management, as well as maintenance. It’s also a good idea to appoint an RCM manager to oversee the program and serve as the main point of contact.
Instead of treating assets as a group, RCM encourages you to look at every machine and piece of equipment as a separate entity.
There are variations even in identical machines, so evaluating machinery individually makes it possible to avoid future breakdowns. Consider how each asset should work, and how you know it’s successful.
This is also a good time to consider environmental or regulatory requirements. Make sure your RCM solution keeps the machines working at the right level to help you stay compliant.
Assets can fail for a variety of reasons. When you have an idea of what could go wrong, it’s much easier to make plans to address potential issues.
For example, a scale with a weight limit might break if you place something too heavy on it. Other machines will malfunction if they’re exposed to high temperatures or water.
RCM considers the why, when, and how behind equipment failures. It looks at failure modes, which are the components, systems, or processes within equipment or machinery that cause a failure.
Understand which failure modes present the biggest threat to your company and identify each potential failure mode for every asset.
What could happen that would cause each failure mode? The most common causes are wear and tear, poor engineering, and electrical issues. The goal of RCM is to prevent failures in the first place, so identifying the underlying reasons behind each failure will give you the information you need to prevent future failures.
Failures are bound to happen, but some of them take higher priority than others. Some failures create small problems, while others can shut down your entire facility.
Look at how each failure mode would affect your business. Rank them by severity so your RCM software understands how to route maintenance crews to projects based on importance.
Finally, reliability-centered maintenance makes a plan for how you’ll address every potential failure. Regular inspections, condition monitoring, predictive maintenance, and design changes are all proactive fixes to common problems.
Reliability-centered maintenance plans should change over time, especially as your business changes its equipment or processes. Regularly review your RCM metrics to see whether your new strategies are paying off or if something needs to change.
No RCM program is perfect, but tracking your performance over time will help you find more opportunities for optimization.
RCM is only as good as the maintenance strategies supporting it, so it’s ciritical to follow a series of tried and true bests practices.
Why? A survey by the Society for Maintenance and Reliability Professionals found that organizations using RCM software reported a 20% reduction in unplanned downtime and a 15% increase in equipment reliability.
So to ensure success for your program, follow these best practices to get the most value out of reliability-centered maintenance.
It’s impossible to do reliability-centered maintenance without the right technology. RCM software keeps all of your asset and maintenance information in one location. It displays this data in dashboards and reports and will even alert you when there’s a critical issue.
Maintenance software is a must, but that’s just the tip of the iceberg. You also need tags, barcodes, and labels, such as facility management asset tags and maintenance management asset tags, to complement this software.
For example, QR codes share a lot of information about a machine in a small amount of space. Similarly, RFID tags automatically collect information from your machines and transmit it to your RCM software, making it much easier to keep tabs on your machine’s performance.
RCM can’t succeed unless your entire team is on the same page. Conduct change management to explain why you’re embracing reliability-centered maintenance. From there, educate and train your employees on how RCM will work, and why it will make their jobs better.
There might be some resistance, but training your team will help the program go off without a hitch. Host workshops and invite employee feedback to create a culture that supports sustainable RCM.
Reliability-centered maintenance programs monitor a lot of data. Without the right systems in place, your teams might become overwhelmed or overlook critical maintenance tasks.
The best way to stay organized with RCM is to use quality tags and labels for all your machines. Tagging your assets is a smart way to share critical information, like safety protocols or regulations, with employees on the factory floor.
Human-readable labels also make it much easier for your team to quickly understand which machines need maintenance.
You want tags that last the lifespan of your assets. Camcode’s durable asset tags and labels survive in even the harshest environments, withstanding exposure to water, salt, dirt, chemicals, solvents, and high temperatures.
RCM is an ongoing process that continually improves your organization. After implementing an RCM program, your team should regularly review and update your maintenance plan.
Review your maintenance-related data to see if your program is meeting your initial benchmarks. Look at the condition of assets over time, how often they break down, and maintenance costs. Ideally, you should see a downward trend with both breakdowns and costs.
Machinery, equipment, and other assets are a big investment for your company. Reliability-centered maintenance prolongs the life of these assets while reducing maintenance costs. RCM empowers you to adopt a more proactive approach, minimizing downtime while optimizing your resources.
However, RCM can only succeed with the right systems in place, and durable labels and tags are a must for any successful RCM program. Reliable tags ensure efficient asset tracking, streamline maintenance operations, and maximize the benefits of your reliability-centered approach.
Camcode’s labels are designed to support maintenance tasks in even the most extreme environments.
See the Camcode difference: request free tag and label samples now.
A failure mode is all the ways a piece of machinery can fail. It’s important to identify failure modes because this makes it possible to prevent equipment failures in the future. Natural wear and tear, software errors, corrosion, and environmental conditions are common failure modes.
RCM reduces costs by identifying points of failure and fixing any issues that could cause breakdowns. This strategy reduces the cost of unexpected repairs and the expenses associated with unplanned downtime.
The four major components of Reliability-Centered Maintenance (RCM) are:
The main differences between Reliability-Centered Maintenance (RCM) and Total Productive Maintenance (TPM) are:
Our sales engineers are experts in automatic asset tracking, tagging and identification,a nd can answer all your questions. Get in touch now.
Lets Talk ›Enter your information and get a free checklist of the top questions to answer to plan a successful asset tagging project for any maintenance tracking or facility management system.