What is Total Productive Maintenance? Why is It Important?
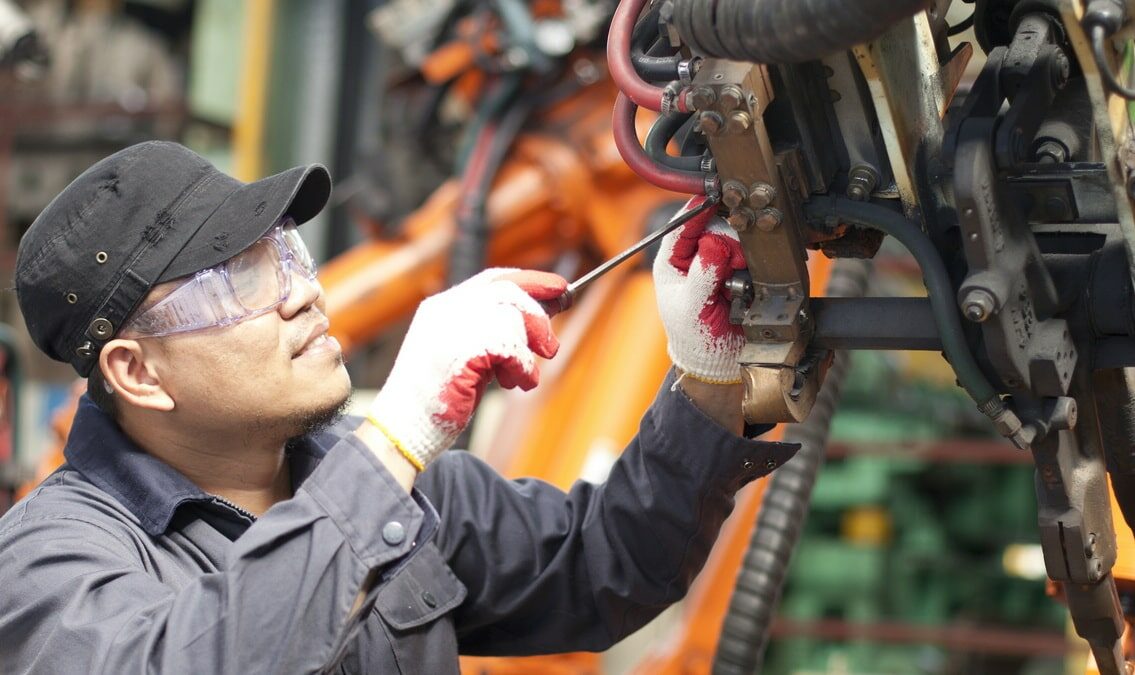
Machine reliability is critical for smooth plant operations. As a leader, it’s your job to support ongoing maintenance that boosts equipment lifespans and value.
But machines wear down and break over time. Unplanned downtime costs as much as $129 million per facility, so preventing downtime and its associated costs has never been more important.
The more efficiently your organization manages maintenance, the more productive and profitable you’ll be. That’s where total productive maintenance (TPM) comes into play.
TPM improves the reliability of machines in your facility. This innovative approach to maintenance emphasizes productivity over everything else, helping you get more value from your machines while maximizing maintenance resources.
In this guide, we’ll explain how total productive maintenance works, share key performance indicators (KPIs) for measuring success, and show you how to implement TPM in your organization.
Photo by Kumpan Electric from Unsplash
Total productive maintenance, or TPM, refers to the set of tools or techniques used to increase the productive output of the machine. You can do this by:
Total productive maintenance is a holistic approach to machine operation and maintenance that melds the two functions together instead of separating them. This approach incorporates the lean values of reducing waste, increasing customer value, and engaging employees in maintenance activities.
That isn’t how most organizations do maintenance. Most companies have regular operators who run their machines.
The company will also have a dedicated maintenance team performing routine and reactive maintenance. These job functions don’t overlap, so operators don’t handle maintenance activities.
But the TPM paradigm changes things. TPM dissolves the boundaries between operators, maintenance technicians, and managers. Instead, everyone in the organization works together to reduce waste and costs.
For example, if an operator hears unusual sounds or vibrations while using the machine, they can investigate the cause and replace parts if necessary. The organization gives them training, parts, and tools to take immediate action. With the TPM approach, operators can perform preventive maintenance rather than waiting for the maintenance team to perform reactive maintenance after the machine eventually breaks down.
Pillar | Description |
---|---|
Autonomous Maintenance | Empowers operators to perform basic maintenance tasks like cleaning, lubrication, inspection, and repairs. |
Planned Maintenance | Focuses on proactive maintenance based on equipment lifecycles and failure rates. |
Quality Assurance | Prevents defects by addressing equipment-related issues through root cause analysis and corrective actions. |
Focused Improvement | Encourages cross-functional teams to identify and solve equipment-related issues collaboratively. |
Early Management | Implements maintainable equipment and processes from the design phase. |
Safety, Health, and Environment (SHE) | Integrates safety practices into all activities to eliminate hazards and promote safety. |
Training | Develops a comprehensive training program for operators and managers on TPM principles and practices. |
Administrative TPM | Applies TPM principles to administrative roles, promoting continuous improvement and cross-team communication. |
Total productive maintenance is a holistic approach to maintenance that flips traditional systems on their heads. The goal is to achieve perfect production with zero defects, breakdowns, or accidents. Follow the eight pillars of total productive maintenance for error-free operations.
Autonomous maintenance empowers machine operators to do basic equipment maintenance. It usually involves less complex but critical tasks like cleaning, lubrication, inspection, and minor repairs. With more autonomy, operators have the freedom to perform simple maintenance tasks and spot abnormalities earlier.
Total productive maintenance emphasizes proactive planned maintenance over reactive fixes. Schedule maintenance based on equipment lifecycles and failure rates instead of arbitrary dates. The goal is to minimize unexpected breakdowns and downtime by addressing potential issues before there’s ever a problem.
Quality assurance (QA) prevents defects by addressing equipment-related issues. Maintenance teams conduct root cause analysis to eliminate the source of defects. Not only that, but they take corrective action and monitor equipment afterward to make sure the fix addresses the problem.
TPM encourages employees to collaborate to identify and solve equipment-related issues. Like the Japanese concept of kaizen (constant improvement), TPM supports cross-functional teams that set shared goals and solve problems together.
Photo by TruckRun from Unsplash
This pillar focuses on implementing maintainable equipment and processes from the start. During the facility design phase, involve maintenance and production teams to identify potential issues while you can still do something about them.
Safety is paramount when working with any type of machinery. TPM integrates safety practices into all activities to eliminate environmental hazards and accidents. It requires conducting regular safety audits and promoting a culture of safety awareness.
TPM requires cross-trained teams, so your organization will likely need to train operators and managers on TPM. Develop a comprehensive training program with hands-on workshops to address any skills gaps. It’s also a best practice to offer continuing education workshops after your team completes their initial training.
Total productive maintenance isn’t just for workers on the factory floor. TPM also applies to administrative and other support roles. That means reducing waste, setting up systems that encourage cross-team communication, and building a culture of continuous improvement.
Total productive maintenance offers numerous benefits, regardless of company size or industry.
The more effective your equipment is, the better your factory will run. With total productive maintenance, you maximize the output of every piece of equipment. Scheduled and proactive maintenance minimize delays and slowdowns and reduce work defects, leading to higher-quality products and better equipment performance with fewer delays.
A single piece of heavy machinery costs anywhere from $25,000 to $80,000 a year in maintenance. All maintenance activities come with a cost, but total productive maintenance reduces these costs. It optimizes all resources, spare parts, and employee labor, preventing costly repairs and breakdowns.
Every manufacturer wants to be known for its quality. With TPM, you identify any issues with root cause analysis and prevent future problems. Reliable, consistent equipment also supports predictable production processes, which are a must for making a consistently high-quality product.
Over 5,400 fatal work injuries occurred in 2022, which is 5,400 injuries too many. Organizations that implement TPM tend to see a lower rate of safety incidents thanks to frequent inspections and a proactive approach to maintenance.
Photo by Homa Appliances from Unsplash
Total productive maintenance is a revolutionary way of approaching maintenance. Since it’s a different way of doing things, your organization will need to create a thoughtful strategy for embracing TPM across all departments and teams. Follow these five steps to implement total productive maintenance in your organization.
It’s always best to test TPM approaches in one area of your business, ironing out any issues and then rolling the new processes out to the broader organization. A systematic approach ensures fewer errors, helping you get more value from total productive maintenance.
Look for an area of your business that would benefit the most from TPM. For example, identify machines in your production line that frequently cause bottlenecks or delays.
Tagging the equipment assets that will be involved in your TPM program sets the foundation for consistent, effective maintenance management. After identifying a pilot area, choose the appropriate equipment labels and sync equipment data with your CMMS or other preventive maintenance software.
Tracking assets becomes difficult in a fast-moving facility due to the speedy wear and tear of labels. That’s why choosing durable CMMS labels, such as those made of Metalphoto® anodized aluminum, is key. The most durable CMMS tags will last throughout the lifespan of your assets.
In Camcode’s highly durable Metalphoto equipment tags, the image is sealed below the surface of the label. This creates an impenetrable barrier to sunlight, water, salt, dirt, chemicals, solvents and extreme temperatures (up to 650°F). These durable maintenance management labels have an exterior lifespan of up to 20 years.
Next, decide how to implement the eight pillars of total productive maintenance. Create internal processes based on:
Loss | Description |
---|---|
Equipment Failure | Unexpected equipment breakdowns and failures can halt production and result in lost production time. These failures require maintenance to repair them. |
Setup and Adjustments | This includes the time lost due to equipment changeovers, setup and adjustments, and calibrations, such as the time taken to switch equipment from producing one product to another. These losses can be significant if the switching process is complex or equipment must be switched frequently. |
Idling and Minor Stoppages | Short stops caused by temporary issues such as equipment jams, blockages, or minor adjustments. These stoppages temporarily halt production but don’t require extensive repairs. |
Reduced Speed | Losses due to equipment operating below its optimal speed. This can include slow cycles and reduced machine speed compared to the speed at which it’s designed to operate. |
Process Defects | Losses caused by producing defective products that must be discarded or reworked. This often occurs due to equipment malfunctions or improper equipment settings. |
Startup Losses | Losses occurring during startup and shutdown processes. This can include waste generated during warmup periods and losses occurring with unstable processes. |
All machinery requires cleaning and maintenance, but it’s best to kick off total productive maintenance with a clean slate. Thoroughly clean and inspect all equipment in your pilot area to identify and fix potential issues.
Address wear and tear, replace worn-out parts, and lubricate all moving components. Log this information in your computerized maintenance management system (CMMS).
TPM processes and technologies are helpful, but they can’t deliver value to your organization if employees fail to execute the new processes. Provide comprehensive training on TPM principles and practices to all employees. Empower operators to take responsibility for basic maintenance tasks and involve them in continuous improvement activities.
Total productive maintenance also encourages a more collaborative way of working that your team may not be used to, so training and culture-building are essential. Encourage collaboration between operators, maintenance personnel, and management. Create cross-functional teams to work on TPM projects and share progress in regular meetings.
Key Performance Indicator (KPI) | Description |
---|---|
Availability | Percentage of time the machine is available for use. |
Performance | Improvement in machine performance and uptime. |
Quality | Metrics such as rate of quality products, first pass yield, and number of defects per million opportunities. |
Machine Enhancements | Tracking machine enhancements and the number of innovation projects. |
Operator Training | Monitoring operator training and success to ensure effective implementation of TPM. |
Measuring key metrics provides more visibility into your TPM activities. After all, you can’t control or manage what you don’t measure.
Every organization has different priorities, but these metrics say a lot about TPM success:
According to TPM principles, you can meet your facility goals by changing the mindset of the people who keep your organization running.
The key to effective TPM is measuring and tracking suitable metrics. Effective asset tracking with durable maintenance management asset tags for a CMMS plays a significant role in measuring the effectiveness of TPM and implementing continuous improvement.
But tracking assets in a fast-moving facility is hard, especially if you see wear and tear on your equipment labels. Durable labels are a wise investment because they can help you accurately track assets at scale. Camcode’s Rigid Metalphoto® Labels, for instance, are designed to withstand the harshest indoor and outdoor environments. Made of Metalphoto® photosensitive anodized aluminum, these labels offer excellent resistance to chemicals, abrasion, solvents, extreme cold, heat, and UV, offering an expected exterior lifespan of more than 20 years.
Camcode’s Teflon™ Coated Metalphoto® Barcode Labels, also made of anodized aluminum, are coated with a non-stick surface to shed paint, acids, strong caustics or other chemicals. Like our Rigid Metalphoto® labels, their expected exterior lifespan exceeds 20 years. In addition to CMMS labels, Camcode also offers data collection, data validation and reconciliation, and label installation services to streamline the implementation of your maintenance management program. Contact Camcode today and discover how our durable labels can improve your facility’s maintenance and operations processes.
Traditional maintenance approaches typically separate the roles of machine operation and maintenance, with operators focusing on running the machines and maintenance teams handling repairs and upkeep. TPM, on the other hand, integrates these roles, empowering operators to perform basic maintenance tasks.
Instead of reacting to issues as they come up, this proactive and collaborative approach prevents breakdowns and improves overall equipment effectiveness rather than just reacting to issues as they arise.
Yes, you can apply TPM principles to other industries. Any company that relies on equipment can use TPM.
Healthcare, logistics, and utility companies are just a few examples. The key is to adapt the eight pillars of TPM to fit your industry’s specific needs and challenges.
Total productive maintenance is much more effective with the right technology:
Our sales engineers are experts in automatic asset tracking, tagging and identification,a nd can answer all your questions. Get in touch now.
Lets Talk ›Enter your information and get a free checklist of the top questions to answer to plan a successful asset tagging project for any maintenance tracking or facility management system.