4 Best Practices for Oil and Gas Asset Management
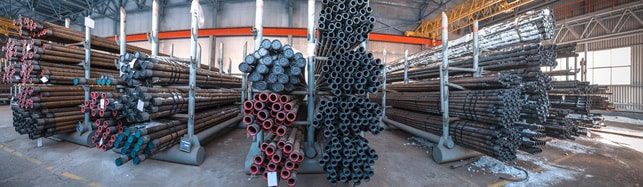
If your company deals in oil and gas, then you know just how challenging it can be to track and manage every asset efficiently – especially considering assets in the gas and oil industry tend to be a) very pricey and b) heavily regulated. Having said that, the two aforementioned points serve as prime reasons for why thorough, honest, and, most of all, holistic oil and gas asset management is key to the health of your business.
Implementing an asset management plan for your unique oil and gas company takes careful planning and custom-fit strategies, both of which can be sketched out when you take key best practices into consideration, which fall into the realm of an asset register, barcode and label solutions, specialized software, and beyond.
To shore up your oil and gas company’s current asset management system, get acquainted with these 4 asset management best practices.
There’s no point in spending the time to improve your asset management if you don’t first focus on the nitty-gritty –the asset register. From accountants to external regulators to operations/maintenance personnel, and beyond, keeping a thorough asset register means that jobs can be performed to the fullest extent right now so that you can more strategically manage your capital in the future.
To ensure that your register is complete, double-check that your company’s includes all of these points:
Once you’ve established your equipment hierarchy in your asset register, it’s now time that you settle on a system that allows you to move the locations of your identical equipment assets without later questioning whether or not their information is correct. For instance, if your piece of equipment is moved around or between various facilities, it’s smart to assign it a completely unique set of location data so as not to confuse it with another piece of identical equipment.
In addition to specific location data, it’s also important that you decide whether or not it makes sense for your company to record activity and costs against equipment in your asset register. As you can see from the above strategy, this is usually only effective when dealing with high-value assets and/or equipment assets that move around a fair bit.
Lastly, let’s take a look at components and parts. Unless a specific component or part falls into the category of being either high-value or relocated constantly, treating them as separate entities in your register will likely just become confusing in the long run.
This means that parts and components should fall towards the bottom in the asset register hierarchy; though detailed information regarding purchase date, warranty, and maintenance should be kept and recorded, the document may be easier to reference if all are included in the equipment column.
When it comes to effective oil and gas asset management, gas and oil companies like yours have to deal with a double whammy when it comes to your assets–most are a) high-value and b) operate under strict regulatory measures. This means that issues such as leak detection and repair (LDAR), in particular, can become a serious problem if not controlled properly.
One of the most efficient ways to tackle LDAR, specifically, is by installing barcode labels or asset tags that allow your LDAR technicians to more easily manage their regulated process equipment. By automating this detection process, your company will always be prepared to undergo reviews because your barcode and labeling system will already have helped you to identify, tag, and monitor potential leaks.
Eliminating these regulatory headaches will safeguard you from incurring hefty fines or lost assets due to completely preventable leaks.
Chances are you’re already ahead of the curve and have invested in asset tracking software of some kind, but just because you have that base covered doesn’t mean that it’s the best option for your business’ assets.
To ensure that yours is, make sure that the software allows you to input complex, comprehensive information about your assets, including the locations, equipment, and components. In addition to the hierarchy, also guarantee that these specifics can be easily altered in real-time to reflect changes in maintenance schedules, updates on depreciation, and all other relevant info.
For the best in asset tracking security, opt for a software that includes GPS technology, especially if your equipment assets move around often. Making use of GPS capabilities makes it so that your most high-value assets are always locatable, even if a theft is in progress.
In the oil and gas industry, keeping close tabs on every valuable company asset is crucial for your company’s bottom line, not to mention a necessity if you want to get the maximum usable lifespan out of those costly assets. Following these oil and gas asset management best practices ensures greater visibility into every company asset, asset locations, value, maintenance schedules, and everything you need to know about your most valuable physical assets.
Our sales engineers are experts in automatic asset tracking, tagging and identification,a nd can answer all your questions. Get in touch now.
Lets Talk ›Enter your information and get a free checklist of the top questions to answer and tips to plan a successful asset tagging project for any asset management or tracking system implementation.