The Expert’s Preventive Maintenance Checklist (with PDF Download)
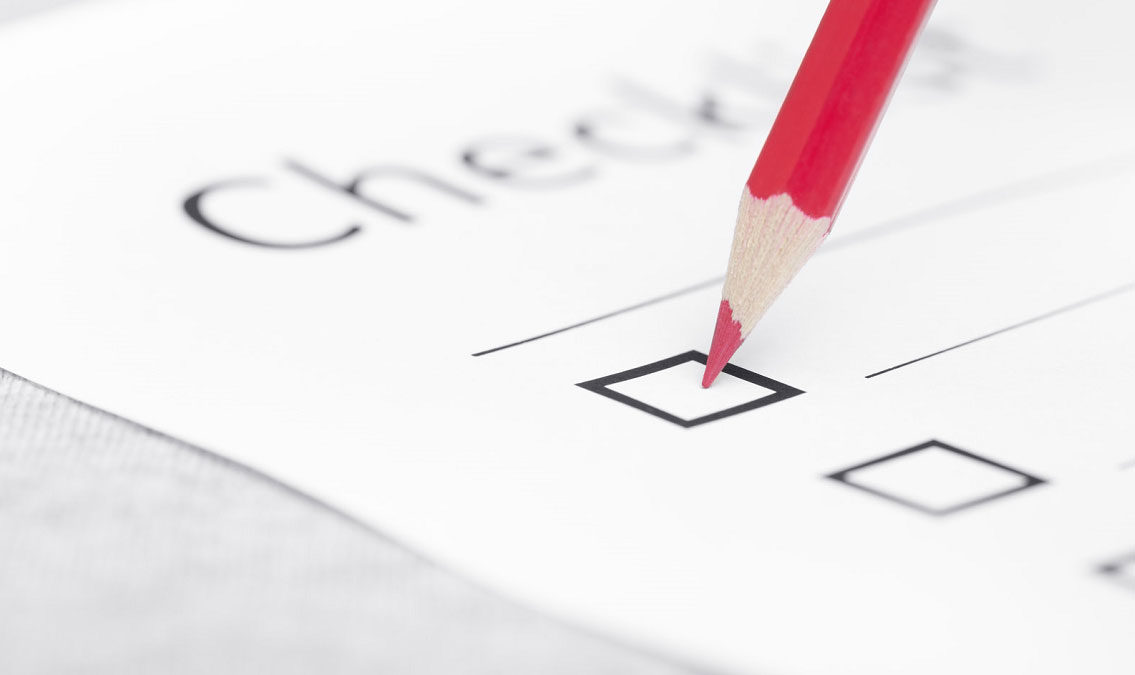
Almost all equipment needs some level of upkeep if you want to maximize its useful life. Axles require routine greasing. Fluids need to be changed at designated intervals. Even hand tools may need periodic oiling or adjustment.
For any given asset, following the manufacturer maintenance recommendations can reduce the chances for unexpected repairs, in turn reducing the likelihood of unplanned downtime, production stoppages, and even workplace injuries. However, effectively performing preventive maintenance requires a plan – or, better yet, a checklist.
To help you build a preventive maintenance checklist – also known as PM checklist – we’ve created the following step-by-step guide. Before we dive in, let’s briefly recap the importance of a PM checklist and why staying proactive on maintenance matters.
It’s no secret that failure to maintain a piece of equipment – be it vehicles, machinery, or even simple tools – reduces its reliability, performance, and safety. It also has serious financial implications: one source found that running equipment to the point of failure could cost up to 10 times as much as a preventive approach.
An even starker statistic is that unplanned downtime costs an estimated $50 billion every year.
Incorporating preventive maintenance strategies can help reduce unexpected production stoppages and mitigate their consequences. One of the best methods for this is to create PM checklists for your firm’s different equipment families or systems.
By using these inspection guides, technicians can quickly test for key conditions or variables that may indicate a need for more robust servicing.
Before creating the actual checklist, take a step back and ask yourself: which goals would you like to achieve with the help of a PM guide?
Of course, the obvious answer is to reduce expenses and downtime related to equipment failure, but there’s more nuance to it than that. Is your company looking to improve production efficiency? Has there been a concerning uptick in workplace injuries that needs addressing? Have there been failed audits or inspections that are prompting a closer look at internal maintenance strategies?
Variables such as these can impact how you design your checklist. You can incorporate specific line items tailored to these concerns, or build an entire checklist around concepts like safety, compliance, or efficiency. Here’s an example of what some checklist items might look like, based on the hypotheticals presented above:
Corporate Goal | Checklist Item #1 | Checklist Item #2 | Checklist Item #3 |
Improve Production | Ensure proper temperature and humidity control for optimal production conditions. | Review sanitation logs to ensure equipment is being regularly cleaned. | Verify and optimize production line speed and throughput. |
Improve Workplace Safety | Assess workstations and equipment setups for ergonomic improvements to reduce strain and fatigue. | Ensure work areas are clean and organized to prevent slips, trips, and falls. | Verify that safety guards and interlocks on machines are in place and operational. |
Improve Audit & Regulatory Compliance | Inspect and maintain equipment according to manufacturer guidelines and industry standards. | Review prior action plans to ensure findings from failed inspections have been addressed. | Confirm personnel have all certifications necessary to legally operate equipment. |
With the broader goals established, you can begin to create asset or equipment classes. Do this by working off an equipment inventory, which can help you establish the categories of assets you plan to create PM checklists for. Finalized groups may include the following:
3D printers & CNC machines | Molds and casting equipment |
Hydraulic equipment | Safety equipment |
Electrical systems | HVAC systems |
Light-duty vehicles | Heavy-duty vehicles |
The goal is to categorize assets into groups that can share a PM checklist. For instance, heavy-duty trucks may be materially different from light-duty vehicles in both their usage and upkeep. As such, it may make sense to use a different checklist for each vehicle class rather than one that’s all-encompassing. Think along these lines as you group your assets.
Once you have your equipment categorized, start pairing relevant tasks or checklist items with each asset group. Several resources can help you determine appropriate tasks, such as:
Remember, these tasks are the meat of your checklist, so take your time finalizing each line item. The more specific you can get, the more indicative the results will be. It’s also important to establish the frequency of each checklist task – different components or services will follow different maintenance intervals.
The following example, which is purposely broad so as to be applicable across multiple industries, illustrates this:
System | Tasks | Frequency |
HVAC systems | Clean or replace air filters | Monthly |
HVAC systems | Inspect and clean condenser coils | Annually |
HVAC systems | Lubricate motor bearings | 6 months |
Production machinery | Conduct regular inspections for signs of wear and damage | Regularly |
Production machinery | Clean and lubricate moving parts | Quarterly |
Production machinery | Schedule professional calibration | Annually |
Company vehicles | Change engine oil and filters | 5,000 miles |
Company vehicles | Inspect tire pressure and tread depth | Monthly |
Company vehicles | Check and top-up fluid levels | As needed |
Once you know what needs to be done and when, who is actually responsible for performing the work? Without having a list of contacts, names, titles, or teams finalized ahead of time, work may never get off the ground, and that could become an issue when it comes to addressing certain audit findings or completing more specialized line items on your PM checklist.
Some processes may require outsourcing as well. For instance, if a forklift needs service, it’s possible that an outside technician will need to be brought in to perform the repair. It’s a similar story for repairing or even inspecting HVAC hardware, advanced manufacturing equipment, and the corporate vehicle fleet, to name just a few subsets of the business.
For asset groups where this is the case, you’ll want to have a repository of vetted, approved vendors and service providers you can call at a moment’s notice.
You’ll also want an optimized CMMS or EAM program on your side, which can track, schedule, and monitor maintenance needs across all company assets. Through the use of advanced asset tags and barcode labels on physical equipment, these maintenance systems log service history in real time, and most can also automatically generate work orders when necessary.
The above steps will help you get a new PM checklist up and running, but these checklists aren’t static documents – they should be modified, adjusted, and revised as your business grows and changes. New equipment, new processes, and new compliance standards are just some of the factors that can quickly turn any maintenance guide obsolete.
To ensure this doesn’t happen to you, review your checklist regularly and make updates as needed. These tweaks can be small – say, an extra line item to account for a new compliance standard issued by a regulatory body – or large, such as the wholesale revision of a section due to your company’s latest automation and technology initiatives.
Whatever might be driving the latest innovations in your industry, adapt your maintenance strategy accordingly. A relevant maintenance guide is one that will continue to add value, deliver results, and help keep your operations running without a hitch, no matter how things change.
Want to learn a little more about preventative maintenance checklists? Check out the short video below:
While these five steps serve as an excellent starting point, tracking preventive maintenance is a critical next step that leads to better asset management, operational efficiency, and cost-effectiveness.
More specifically, benefits can be seen in the following key areas:
Increased Equipment Lifespan: Regular maintenance keeps equipment in optimal working condition, preventing premature failures and extending the lifespan of assets.
Cost Savings: Preventive maintenance is often less expensive than emergency repairs or replacements. It helps avoid costly breakdowns and downtime.
Improved Efficiency: Well-maintained equipment operates more efficiently, consuming less energy and resources, which leads to lower operating costs.
Safety: Regular maintenance helps identify and rectify potential safety issues, reducing the risk of accidents and injuries.
Compliance: Many industries have regulatory requirements for equipment maintenance. Keeping track of preventive maintenance helps ensure compliance with these standards.
Reduced Downtime: Preventive maintenance schedules help plan and perform maintenance activities during non-peak times, minimizing disruptions to operations.
Data and Insights: Tracking maintenance activities provides valuable data that can be analyzed to identify trends, predict future issues, and make informed decisions about asset management.
Quality Control: Regular maintenance ensures that equipment produces goods or services at consistent quality levels, which is crucial for customer satisfaction.
Resale Value: Properly maintained equipment often has a higher resale value, as it is perceived to be in better condition and more reliable.
Environmental Impact: Efficiently running equipment typically has a lower environmental footprint, reducing waste and energy consumption.
Using unique labels with barcodes or QR codes makes tracking preventive maintenance possible by providing a distinct identifier for each item. This allows for precise documentation of maintenance activities, history, and schedules. Technicians can quickly scan the barcode or QR code to access the item’s maintenance records, ensuring accurate updates and consistency.
This method reduces errors, streamlines record-keeping, and enhances efficiency. Additionally, it facilitates easy retrieval of information, aids in scheduling timely maintenance, and supports data-driven decisions, ultimately improving the reliability and longevity of equipment.
Camcode offers barcode and QR labels for a wide range of assets and equipment, regardless of the environment. To learn more, call us today at 1-800-627-3917. Alternatively, to see the Camcode difference for yourself, order your free sample kit today.
To streamline your maintenance planning and ensure that all critical tasks are performed consistently, we are offering a comprehensive preventive maintenance checklist available for download in PDF format. This checklist is designed to help you keep track of routine maintenance activities, prevent equipment failures, and extend the lifespan of your assets.
To get started with your preventive maintenance program, download our comprehensive checklist by clicking the link below:
[Download Preventive Maintenance Checklist (PDF)]
By using this checklist, you can ensure that your facility remains in optimal condition, reducing downtime and enhancing overall productivity.
This will vary, depending on the specific industry and organization. Generally, the checklist should encompass critical machinery, equipment, systems, and facilities that, if neglected, could lead to significant downtime, safety hazards, or costly repairs.
Establishing the appropriate interval depends on factors like the type of equipment, its age, operating conditions, and manufacturer’s recommendations. Striking the right balance between too frequent and too infrequent maintenance is crucial to maintain optimal performance and avoid unnecessary costs.
With limited resources and time, it’s essential to prioritize maintenance tasks based on their criticality and potential impact on operations, and maintenance efforts should be directed towards the most crucial areas first. Prioritization can be determined by factors such as safety risks, equipment reliability, historical failure data, and the importance of the asset to overall operations.
Our sales engineers are experts in automatic asset tracking, tagging and identification,a nd can answer all your questions. Get in touch now.
Lets Talk ›Enter your information and get a free checklist of the top questions to answer to plan a successful asset tagging project for any maintenance tracking or facility management system.