25 Best Maintenance Management Software (2025): CMMS and Maintenance Tracking
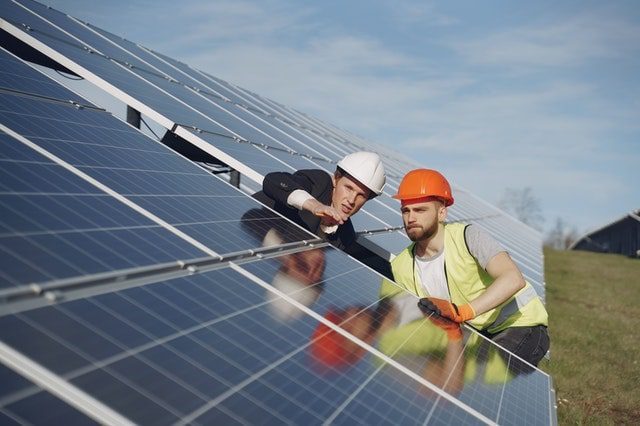
Maintenance management isn’t a new concept, but recent trends are encouraging the adoption of technologies that make maintenance even more efficient.
A recent survey conducted by UpKeep found that 66% of respondents are now using a computerized maintenance management system (CMMS). This is a significant increase from levels seen before the COVID-19 pandemic. Clearly, more organizations are placing a premium on efficiency in an increasingly competitive, changing world.
CMMS software is one of the best ways for organizations of all sizes to find efficiencies, better manage inventory, and enjoy near-immediate cost savings. Every solution comes with a learning curve, but any solid CMMS will equip your team with the features and data to do better work, faster.
There are countless CMMS solutions on the market, and it can be challenging to find the right option for your needs. This guide will help you jumpstart your search.
We’ll cover the basics of what a CMMS offers, the different types of maintenance management software, and how to implement maintenance management solutions. We’ll also share our list of the top 25 CMMS platforms of 2024. As always, weigh your needs, budget, and feature requirements with each software solution to find the right option for your organization.
A computerized maintenance management system (CMMS) is a software solution that helps organizations plan, track, and optimize the maintenance of their equipment and facilities. It helps organizations with a range of tasks, including:
CMMS software platforms integrate seamlessly with asset tags and barcode labels, too. This streamlines and automates the documentation of maintenance activities.
By tagging your equipment and high-value assets with durable barcode labels and using a leading maintenance management software solution, you’ll gain complete visibility into your maintenance processes with a central repository that provides easy access to the complete history of each asset, maintenance schedules, and more.
Check out the video below to learn more about CMMS solutions and how they work:
While CMMS is one of the most widely used maintenance management software solutions, it’s not the only type of maintenance management software. Understanding the different options and what they offer compared to your business’s requirements will help you narrow your options.
Type of Maintenance Management Software | Key Capabilities |
---|---|
CMMS (Computerized Maintenance Management System) |
Work order management Asset management Preventive maintenance Inventory management Reporting and analytics Integration capabilities Mobile access |
EAM (Enterprise Asset Management) |
Comprehensive asset lifecycle management Strategic asset planning Predictive maintenance Energy management Compliance tracking Advanced analytics and reporting Integration with ERP systems |
Predictive Maintenance Software |
Condition monitoring Predictive analytics Real-time data collection IoT integration Machine learning algorithms Automated alerts and notifications Historical data analysis |
Facility Management Software |
Space and occupancy management Maintenance scheduling Asset tracking Vendor and contract management Energy and sustainability management Reporting and compliance Mobile access |
Maintenance Planning Software |
Maintenance scheduling Resource allocation Budgeting and cost tracking Risk assessment Workflow automation Compliance management Integration with other systems |
Equipment Management Software |
Equipment tracking and monitoring Preventive and predictive maintenance Maintenance history Parts and inventory management Real-time data collection Reporting and analytics |
In the next section, we’ll cover some specific features and capabilities to look for when selecting maintenance management software.
Maintenance management software is an essential tool for businesses looking to streamline their maintenance processes and improve efficiency. With so many options available in the market, it can be overwhelming to choose the right software for your needs.
Here’s what to look for when evaluating and comparing maintenance management solutions:
Implementing maintenance management software can be a game-changer for businesses looking to streamline their maintenance operations and improve overall efficiency. Here are some steps to follow when implementing maintenance management software:
Before implementing any software, it’s important to have a clear understanding of what you hope to achieve with it. Identify your current pain points in maintenance management and set specific goals for what you want the software to help you accomplish.
There are many maintenance management software options available in the market, so take the time to research and compare different solutions. Look for software that aligns with your objectives and offers features that will benefit your maintenance team.
To ensure successful implementation, involve key stakeholders in the decision-making process. This could include maintenance technicians, supervisors, and other team members who will be using the software on a daily basis.
Get their input on what features are important to them and address any concerns they may have.
Durable barcode labels and asset tags are the foundation of any maintenance management program. Give all assets a unique ID and attach asset tags or barcode labels to those assets. These tags integrate seamlessly with CMMS and other maintenance software, streamlining the process of equipment tracking, maintenance management, and documentation.
Durable asset tags such as Rigid Metalphoto® Labels and Teflon™ Coated Metalphoto® Barcode Labels are designed to withstand harsh operating conditions to remain readable throughout the lifespan of your assets.
With maintenance management asset tags, maintenance professionals can simply scan the barcode or asset tag with a handheld scanner to retrieve detailed information about the asset, such as the manufacturer, spare parts vendors, spare parts inventory, maintenance history, maintenance checklists, scheduling, and more.
Proper training is essential for the successful implementation of maintenance management software. Provide thorough training for all users to ensure they are comfortable with the new system and know how to utilize its features effectively.
If you are transitioning from a manual or outdated system, you will need to migrate your existing data to the new software.
For example, if you have a database of your assets and their maintenance history, you’ll want to migrate that data to your new software system and ensure that your maintenance management asset tags and barcode labels have the appropriate identification.
This can be a complex process, so make sure to plan ahead and allocate enough time and resources for data migration.
Before fully implementing the software, conduct thorough testing to identify any potential issues or bugs. Test different scenarios to ensure the software works as expected and meets your requirements.
Instead of implementing the software across the entire organization at once, consider rolling it out gradually. Start with a small pilot group and gather feedback before expanding to other departments or locations.
Once the software is implemented, monitor its performance and gather feedback from users. Regularly evaluate how well the software is meeting your objectives and make any necessary adjustments or improvements.
By following these steps and taking a strategic approach to implementation, you can successfully integrate maintenance management software into your operations and reap the benefits of improved efficiency and productivity.
To help you evaluate new approaches to your maintenance programs, we’ve gathered a list of the 25 best CMMS software platforms for maintenance management and tracking activities.
You’ll find a mix of traditional CMMS software platforms that can be installed on-site and completely web-based solutions. We’ve also highlighted key features of each system.
Axxerion is a facility and maintenance management platform that tracks preventive, corrective, and predictive maintenance work. As an all-in-one solution, Axxerion strives to provide all the necessary tools within a single user interface.
The software can also be used as a complete enterprise asset management (EAM) system to track valuable equipment and supporting systems. Best of all, it’s a modular system that allows you to add and remove features and capabilities as needed.
Key Features:
Azzier is an advanced CMMS with mobile support for any device, computer, or tablet with internet connectivity. The software makes it easy to manage requests, work orders, and procedures from a reliable and centralized location.
The built-in project management module allows you to track milestones for complex maintenance and facility projects.
Key Features:
Brightly CMMS focuses on sustainable asset performance. It includes several tools for data-driven maintenance, allowing you to streamline your labor costs and parts inventory.
The tool also captures team knowledge and guides you to optimize asset management over time. Streamline work orders, manage assets and facilities, and schedule preventive maintenance in a mobile-friendly CMMS.
Key Features:
Corrigo CMMS, from JLL Technologies, has an intuitive layout with a dashboard that displays custom KPIs for your organization. The platform features work order automation and has several AI-driven tools for streamlining maintenance work across all facility locations. Its mobile app makes Corrigo a good choice for complete remote connectivity.
Key Features:
Megamation’s DirectLine is a full suite of maintenance management tools suitable for manufacturing, healthcare, and other structured environments. This fully customizable platform includes RFID tag support, enhanced security, and excellent software support.
The software is available for a simple monthly service fee, and the company offers a 60-day cancellation guarantee to ensure customers are satisfied with the product.
Key Features:
The EAM/CMMS platform eMaint boasts over 150,000 worldwide users and has proven itself as a reliable maintenance management resource. It’s highly configurable, and users can customize settings such as data fields, themes, workflows, and dashboards.
eMaint also supports advanced capabilities such as condition monitoring and data visualization.
Key Features:
Eptura’s CMMS and maintenance tracking solution combines the ease of automated maintenance with inventory control. It also gives you the power to manage rooms and facilities alongside maintenance schedules for a truly all-in-one building management solution.
Key Features:
eWorkOrders is a highly rated CMMS/EAM software suite that gives companies complete control over their resources. This platform tracks each asset’s lifecycle, assigns work orders, and manages vendor relationships.
One of the best features of eWorkOrders is the user-friendly service request interface, which makes it easy for anyone to submit maintenance requests.
Key Features:
FaciliWorks CMMS, from CyberMetrics, is a complete all-in-one solution for facility maintenance management. The software can be deployed as a vendor-hosted, on-site server, or web-based solution based on your unique needs.
With features that cover all aspects of maintenance, vendor, and asset management, this is a great option for improving efficiency.
Key Features:
Fiix, from Rockwell Automation, is a capable CMMS with a modern design and interface. The mobile Fiix app is especially useful for quickly scanning equipment barcodes and attaching documents, photos, and task lists.
Tracking and reporting capabilities are easy to set up, and users can create AI-generated reports at any time.
Key Features:
FMX is an easy-to-use maintenance management software for improving operations and extending asset lifetimes. The maintenance calendar provides a visual resource for assigning, viewing, and editing all planned work for your facility.
Closing maintenance work orders is also easy, and technicians can include supporting information such as cost and hours worked with each job.
Key Features:
FSI is a unique cloud-based CMMS designed for healthcare maintenance management. It’s a leading choice for hospitals and other healthcare facilities looking to maintain compliance while streamlining their asset management. The FSI platform is also well suited for education, public sector, and industrial applications.
Key Features:
FTMaintenance is a well-known CMMS designed for managing assets, inventory, and work orders. This secure platform makes it easy to capture information for each work assignment and asset while maintaining a complete history for auditing purposes. The company also offers extended implementation services and support for each deployment.
Key Features:
Limble is a mobile CMMS platform that also has a complete module for enterprise asset management. Limble automatically syncs maintenance work orders across all devices for real-time data visibility.
Use the interactive calendar to schedule preventive maintenance requests with automated alerts upon completion or after changes to work status.
Key Features:
MaintainX is an excellent platform for operations and maintenance management that supports complex facility networks. Automatically generate work orders from new requests in the queue within MaintainX.
This software also supports barcode scanning for easy access to asset and parts information at any time.
Key Features:
MaintiMizer, from Ashcom Technologies, is a powerful CMMS that includes the mobile MaintiMizer work request app for iOS and Android devices.
The core software comes in three configurations, including the Blackbox 2 all-in-one software and hardware bundle. You can also purchase a completely online SaaS deployment or the convenient web edition.
Key Features:
Maxpanda CMMS is an enterprise-ready maintenance platform that includes multiple dashboards. It offers a shared preventive maintenance and task laboratory to help you build, share, and standardize preventive maintenance routines, and the platform itself is customizable to meet your needs.
Maxpanda is a web-based operations tool, so you can easily access it from any internet-connected device. The service team at Maxpanda is also available 24/7 to help with training needs and technical support.
Key Features:
MicroMain is a total maintenance and operations solution with core CMMS features that are familiar and fully customizable. This platform is built for IoT connectivity and also supports the scanning of custom QR codes and barcodes. It includes extensive reporting capabilities, with built-in templates for tracking equipment downtime and maintenance histories.
Key Features:
MPulse is an intuitive CMMS software system with complete maintenance and operational support. It has a modern interface that you can adapt to view on just about any device, including desktops, smartphones, and tablets.
MPulse divides feature sets among three software plans to cover the needs of professionals, advanced tracking applications, and enterprise deployments.
Key Features:
Q Ware is a CMMS platform for complete facility management. The simple design of the software user interface makes it easy for employees to interact with the numerous apps available within the system.
Three primary app suites feature work order management, work scheduling, and inventory management.
Key Features:
ServiceChannel is a leading facility management platform providing real-time visibility of service data across locations, enabling businesses to optimize the performance of their assets. From asset management to work order management, preventive maintenance, spend optimization, and provider performance management, the company offers a comprehensive suite of tools to streamline your maintenance management processes.
Providing a single source of truth, ServiceChannel is a robust platform giving you unprecedented visibility and control to manage and understand the performance of every location.
Key Features:
The Asset Guardian is an easy-to-scale maintenance management solution with powerful software and technology integration. The interface is easy to manage and allows you to set up dedicated portals for management, technicians, and customers.
TAG’s primary functions include labor management, asset management, and maintenance scheduling.
Key Features:
Tofino Maintenance Management is a mobile-first platform with an intuitive preventive maintenance scheduling tool. You can save time building your maintenance management plan by copying maintenance work plans and applying them to multiple assets.
This software also features excellent reporting tools, including customizable operational excellence reports.
Key Features:
UpKeep provides excellent support for maintenance activities through this Asset Operations Management platform. The fully-featured mobile app makes it easy for technicians and field staff to access work schedules and asset information.
This solution also has excellent connectivity with IoT sensors for real-time asset monitoring.
Key Features:
Zoidii is an ROI-focused CMMS that streamlines the entire maintenance management process. The software features modules for work order management, preventive maintenance, and inventory management for complete control over maintenance workflows.
The Zoidii mobile app is very easy to use and allows uploads and integrated barcode scanning from nearly any mobile device.
Key Features:
The cost of CMMS software can vary widely based on the features offered, the size of the organization, and your specific needs. The average range is $29 to $70 per user per month, although some CMMS platforms have a minimum user requirement.
There are usually onboarding costs in the $600 to $2,500 range. Know how many users need access to the software and ask your provider about implementation and maintenance fees. They should be able to generate a quote for setup and ongoing monthly fees to give you a better idea of costs.
Yes! Every solution is different, but many CMMS can automate:
CMMS and enterprise asset management (EAM) software overlap in some places, but they have different purposes. A CMMS focuses on maintenance management, while EAM encompasses a broader range of asset management activities, including asset lifecycle planning.
EAM also focuses more on financial, operational, and risk management. Many organizations start with a CMMS and later transition to an EAM for a more holistic view of their assets and business performance.
Our sales engineers are experts in automatic asset tracking, tagging and identification,a nd can answer all your questions. Get in touch now.
Lets Talk ›Enter your information and get a free checklist of the top questions to answer to plan a successful asset tagging project for any maintenance tracking or facility management system.