What is a Warehouse Management System? Types, Benefits and How to Choose the Best WMS
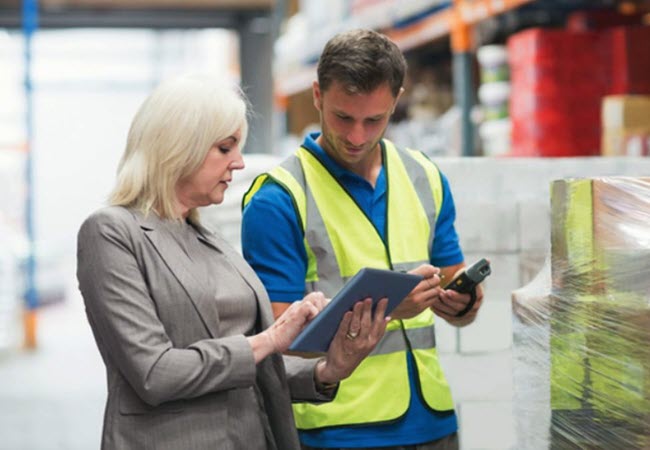
Are you considering investing in a Warehouse Management System (WMS) for your business? The vast array of features and capabilities make it difficult to know which system is best for your organization’s needs.
A Warehouse Management System (WMS) is a powerful tool used by many businesses to streamline their inventory management processes. It is an essential technology for managing and tracking goods within a warehouse.
WMS software has become increasingly popular in the past several years, as companies strive to reduce costs and ensure timely delivery of products. We will discuss everything you need to know about Warehouse Management Systems and how they can benefit your business.
A warehouse management system (WMS) is a software solution that streamlines daily warehouse operations. WMS solutions give managers a central location to manage tasks like inventory tracking.
Warehouse management system programs may be part of a larger Enterprise Resource Planning (ERP) system, or they may be standalone applications. WMS solutions range from simple to complex and provide warehouse managers with the information needed to control the movement of warehouse materials efficiently.
Warehouse managers use warehouse management systems to control and transfer inventory in a centralized system. Often, warehouse managers access the system on handheld devices or tablets so they can work in the warehouse or at their desk.
Many managers point to remote data visibility as a valuable benefit of using a WMS solution. Other benefits of implementing a warehouse management system include:
Some warehouse management systems aid executives in maximizing the use of their space and their workforce.
If you choose a WMS that automates routines for stock rotation and picking, workers will require less space, which will streamline your warehouse and make it more efficient. Indeed, some of the best WMS solutions improve space utilization by reducing safety stock levels and more efficiently locating items via receiving, assembly, packing, and shipping areas.
Warehouse executives who invest in warehouse management systems look for additional return on investment (ROI) opportunities as a result of their investment.
More often than not, a WMS solution delivers the ROI warehouse executives and managers expect to see because the program provides the visibility and transparency needed to better manage inventory and reduce safety stock levels; knowing real-time inventory levels leads to reduced lost product and overstocks.
Warehouse Management Systems (WMS) offer a wide range of functionalities that streamline and optimize warehouse operations. Here are some key features and functionalities of a modern WMS:
Order picking is a crucial function of WMS that ensures the accurate and efficient collection of items for customer orders. Advanced WMS solutions use technologies such as barcode scanning, voice picking, and pick-to-light systems to guide workers to the correct locations within the warehouse.
These systems significantly reduce errors and improve picking speed, enhancing overall order fulfillment efficiency.
WMS also plays a vital role in the packing and shipping process. Once items are picked, the WMS generates packing lists and shipping labels, ensuring that each order is correctly packaged and labeled for dispatch.
This automation reduces the likelihood of errors and accelerates the shipping process, leading to faster delivery times and improved customer satisfaction.
One of the most powerful features of WMS is real-time inventory tracking. By using RFID, barcode scanning, and IoT sensors, WMS can provide accurate, up-to-the-minute data on inventory levels.
This visibility helps warehouse managers to track the movement of goods within the warehouse, identify discrepancies, and make informed decisions about inventory replenishment and order fulfillment.
Optimizing the physical layout of the warehouse is another key functionality of WMS. By analyzing data on item velocity, order patterns, and storage requirements, WMS can recommend optimal storage locations for different products. This optimization minimizes travel time for pickers, maximizes space utilization, and enhances overall warehouse efficiency.
Modern WMS leverage AI and robotics to automate various warehouse tasks. AI algorithms can predict demand, optimize inventory levels, and improve labor scheduling. Robotics, such as Automated Guided Vehicles (AGVs) and Autonomous Mobile Robots (AMRs), are used to transport goods within the warehouse, reducing the need for manual labor and increasing operational efficiency.
These technologies not only enhance productivity but also improve workplace safety by taking over repetitive and physically demanding tasks.
Incorporating these advanced features into warehouse operations can lead to significant improvements in efficiency, accuracy, and overall performance, making WMS an essential tool for modern supply chain management.
There are several different types of warehouse management systems (WMS), each with its own features and benefits. Here are some of the most common types:
The size of the warehouse often determines whether the organization needs a standalone system or a WMS as a module of an ERP system or supply chain management suite. Some software developers also gear their WMS systems toward the industry for which they are intended, so look for a warehouse management system that is tailored to your industry, whether it is eCommerce, retail, or enterprise.
With so many warehouse management system options available today, it can be quite a difficult and confusing task to choose one.
The first step an organization should take when choosing a WMS is to evaluate your needs and determine which WMS best addresses them. Generally, there are a few criteria that make a WMS worthy of your investment:
Step | Key Considerations | Details |
---|---|---|
Assessing Business Needs | Inventory Volume, Order Volume, Number of SKUs, Peak Seasons, Future Growth | Evaluate current and future operational requirements. |
Evaluating System Features | Barcode Scanning, Mobile Compatibility, Automated Workflows, Reporting, Ease of Use, Scalability, Customization | Identify essential features and capabilities needed in a WMS. |
Considering Costs and ROI | Upfront Costs, Ongoing Costs, Integration Costs, Training Costs | Calculate total cost of ownership and potential return on investment. |
Vendor Evaluation | Vendor Reputation, Customer Support, Implementation Timeline, Future-Proofing | Research and assess potential vendors. |
Integration with Existing Systems | Compatibility, Data Flow, Integration Costs | Ensure smooth integration with existing enterprise systems. |
Change Management and Training | Communication, Involvement, Support, Comprehensive Training | Develop strategies for managing change and training staff effectively. |
Implementing a Warehouse Management System (WMS) can bring significant benefits to a business, but it also comes with various considerations and challenges that need to be addressed for a successful deployment. Here are some key factors to consider:
The cost of implementing a WMS can vary widely depending on the system’s complexity, the size of the warehouse, and the specific needs of the business. Costs can include software licenses, hardware such as barcode scanners and RFID readers, and the infrastructure required to support the system.
Additionally, businesses should consider ongoing costs for system maintenance, updates, and potential customizations. It is crucial to conduct a thorough cost-benefit analysis to ensure that the investment in a WMS will provide a satisfactory return on investment (ROI).
As businesses grow, their warehouse operations become more complex, requiring a WMS that can scale accordingly. Scalability is a critical consideration when selecting a WMS, as the system must be able to handle increased volumes of inventory, more intricate order processing, and additional warehouse locations.
Cloud-based WMS solutions often provide greater scalability, allowing businesses to adjust their resources and capabilities as needed without significant additional investments in hardware or infrastructure.
The successful implementation of a WMS requires comprehensive training for warehouse staff. Employees need to be proficient in using the new system to perform their tasks effectively. Training programs should cover all aspects of the WMS, from basic navigation to advanced features such as inventory tracking and order management.
Investing in thorough training can help minimize disruptions during the transition period and ensure that staff can leverage the full capabilities of the WMS.
Implementing a WMS often involves significant changes to existing processes and workflows. Effective change management is essential to address the resistance that can occur when introducing new technology. This includes clear communication about the benefits of the WMS, involving key stakeholders in the planning process, and providing support throughout the implementation phase.
Successful change management can help ease the transition, reduce resistance, and ensure that the new system is adopted smoothly across the organization.
For a WMS to deliver its full potential, it must integrate seamlessly with existing enterprise systems such as Enterprise Resource Planning (ERP) and Transportation Management Systems (TMS). Integration ensures that data flows smoothly between systems, enabling better coordination and more informed decision-making.
Businesses should assess the compatibility of a WMS with their current systems and plan for any necessary integration work as part of the implementation process.
Every warehouse operates differently, and a one-size-fits-all approach may not work for every business. Therefore, it is important to choose a WMS that offers customization and flexibility to meet specific operational requirements. Customization might involve modifying workflows, creating specific reports, or integrating with unique hardware setups.
Ensuring that the WMS can be tailored to fit the unique needs of the warehouse can lead to more effective implementation and better overall performance.
A quality Warehouse Management System (WMS) is crucial for modern warehouse operations. It minimizes losses across various processes and provides warehouse managers and staff with real-time visibility into inventory levels, reorder points, and optimal stock quantities. This enhanced control and efficiency directly contribute to improved customer satisfaction by enabling faster order fulfillment, reducing backorders, and minimizing errors.
As the WMS market continues to evolve, driven by advancements in AI, robotics, and cloud-based solutions, businesses across industries must adapt to remain competitive. With the global WMS market expected to grow at a CAGR of 19.5% from 2024 to 2030, now is the time for businesses to invest in advanced WMS solutions. These systems not only enhance operational efficiency and reduce costs but also position companies to meet the growing demands of the digital economy.
By implementing a robust WMS, businesses can streamline their warehouse operations, improve inventory accuracy, and ultimately deliver better service to their customers. As supply chains become increasingly complex, a well-chosen WMS will be a key differentiator in maintaining a competitive edge in the market.
A WMS is crucial for larger warehouses and distribution centers to compete in today’s supply chain. It helps maintain high efficiencies, reduce costs, improve accuracy, and enhance visibility of inventory WMS solutions are essential for managing complex warehouse operations and meeting customer compliance requirements
A WMS operates based on a variety of data and rulesets, including information on inventory SKUs, productivity, and locations. It uses this database to guide inventory through receiving, put-away, inventory management, picking, and shipping while optimizing these processes
The cost of a WMS can vary widely depending on the type of system and the size of the operation. Cloud-based solutions for small to mid-size warehouses can be significantly less expensive than traditional on-premise systems.
For example, Foysonis offers an all-inclusive premium plan at $999/month for five users, with additional users at $99/month. However, costs can be higher for larger operations or those requiring extensive customization.
SAP and WMS (Warehouse Management System) are different software solutions that serve distinct purposes in business operations:
SAP (Systems, Applications, and Products): SAP is a comprehensive Enterprise Resource Planning (ERP) software that integrates various business processes across an organization. It covers a wide range of functions including finance, human resources, sales, procurement, and supply chain management. SAP provides a centralized system to streamline operations, reduce costs, and improve efficiency across multiple departments.
WMS (Warehouse Management System): A WMS is a specialized software solution focused specifically on managing warehouse operations. It’s designed to optimize inventory handling, tracking, and movement within a warehouse. WMS systems typically handle tasks such as inventory management, receiving, putaway, picking, and shipping of goods.
Key differences:
It’s worth noting that SAP does offer its own Warehouse Management (WM) and Extended Warehouse Management (EWM) modules as part of its suite of solutions. These can be used either as part of the larger SAP ecosystem or as standalone warehouse management solutions.
Our sales engineers are experts in automatic asset tracking, tagging and identification,a nd can answer all your questions. Get in touch now.
Lets Talk ›Enter your information and get a free checklist of the top questions to answer and tips to plan a successful asset tagging project for any warehouse management system implementation.