What is Warehouse Automation? Why Is It Important?
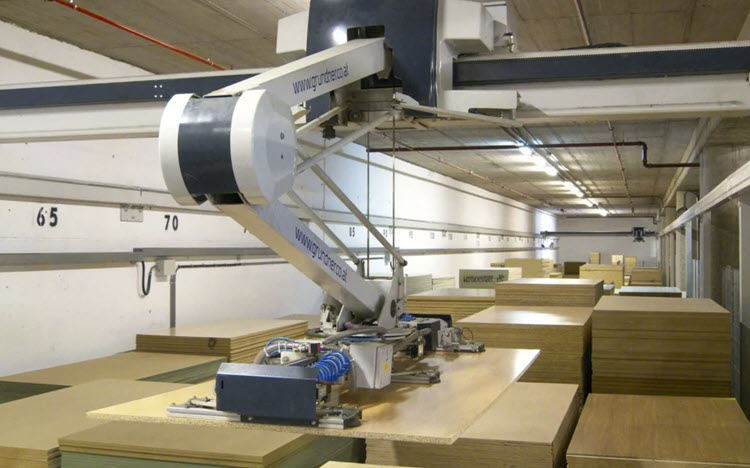
More companies are turning to warehouse automation to streamline processes, boost efficiency and reduce human error. But what is warehouse automation exactly, and how can companies implement it and also benefit from it?
This article will provide a comprehensive overview of what warehouse automation entails, the various types of automation technologies, how to effectively implement a warehouse automation system and the key benefits that companies can realize by implementing these solutions.
Warehouse automation is the use of advanced technologies and automated systems to streamline operations and improve efficiency in warehouse environments. As companies seek to boost productivity, reduce errors, and enhance customer satisfaction, the adoption of warehouse automation is on the rise.
Warehouse automation is widely touted as one of the most effective ways to boost ROI:
“One indisputable fact exists,” according to Supply Chain Management Review. “Warehouse automation is one of the last areas where long-term costs can be significantly reduced.”
But some think of warehouse automation as software, while others think about the idea of automating a warehouse as implementing automated storage and retrieval systems (AS/RS). In reality, complete warehouse automation entails automating a variety of aspects of operations, from automatic data capture to software systems, storage and retrieval, and more.
Still, according to a 2014 report from Monteage Technologies, 90% of warehouses worldwide today are either entirely manual or have implemented only low-level automation into their operations. And while the average logistics division might be looking at a period of four to five years before realizing a return on investment for automation innovation, the payoff is well worth the wait for those who make smart, strategic investments in automation.
At its core, automation revolves around identifying repetitive tasks that are process-oriented, time-consuming, or error-prone, and finding ways to automate them. And as anyone in the warehousing industry is well aware, warehouses are rife with repeatable, process-oriented, and error-prone tasks, ranging from manual documentation errors to picking and stocking errors, shipping and receiving errors, and much more.
For this reason, there are many aspects of warehouse operations that can be automated, including:
Relying on outdated, manual processes not only leads to errors and delays, but they are practically guaranteed to have a negative impact on the company’s bottom line. Out-of-stock conditions can lead to dissatisfied partners and customers, damaging brand reputation, and excess inventory that spends too much time sitting idle on racks and shelves continues to eat at bottom-line storage and operational costs. And when downtime occurs as a result of lost productivity or more serious errors, warehouses are either hindering growth or actively lowering profits.
Driven by the demand for less disruption, increased productivity, and improved visibility, Motorola predicted in 2014 that by 2018, just 12% of warehouses would still be relying on manual cycle counts, and that 65% of warehouses would have real-time access to a WMS system from mobile devices.
Warehouses can be automated in a number of ways, from automating operations like picking, barcode labels and scanning, and vehicles, to automating back-office processes. Any warehouse that needs to improve their bottom line can benefit from automation.
There are several ways to automate warehouses. We explore a few of the more common types of warehouse automation below:
The benefits of warehouse automation are multi-fold. For warehouse managers just delving into automation, one of the first benefits you realize is a reduction of manual errors. As some studies show, the cost per error ranges from $50 to $300; when you multiply the error cost by the 1%-3% error rate, you realize the significant impact it has on your company’s profits.
Other benefits of warehouse automation include:
All of these benefits translate into improved return on investment (ROI) for warehouses. In terms of a timeframe, many companies aim for a ROI payback period of 2 years or less for simpler automation solutions, while more complex systems may have a 5-year or less payback period. The exact ROI timeline depends on the specific automation technology, scale, and other factors.
Here’s a method to calculate the ROI of warehouse automation, using the direct costs and the benefits that can be realized from an automated system.
ROI Component | Calculation | Annual Value | Number of Years | Total Value |
---|---|---|---|---|
Equipment Costs | Cost of automation hardware and software | $_________ | _______ | $_________ |
Implementation Costs | Integration, engineering, installation, training | $_________ | _______ | $_________ |
Energy and Maintenance | Power, maintenance, spare parts | $_________ | _______ | $_________ |
Labor Savings | Reduced labor costs (wages, benefits, overhead) | $_________ | _______ | $_________ |
Increased Throughput | Additional orders processed per year | $_________ | _______ | $_________ |
Reduced Errors | Cost savings due to fewer errors | $_________ | _______ | $_________ |
Space Savings | Reduced storage or leasing expenses | $_________ | _______ | $_________ |
Improved Inventory Control | Carrying cost savings, less overstock/stockouts | $_________ | _______ | $_________ |
Effectively implementing warehouse automation involves a strategic, multi-step approach. Here are the key steps to consider:
By following these steps, companies can effectively implement warehouse automation solutions that streamline operations, boost productivity, and enhance their overall competitiveness in the modern supply chain landscape.
When it comes to a effective warehouse automation, the hardware and software go hand-in-hand:, ie the WMS and the data capturing with a warehouse labeling solution.
Barcode labels provide a fool-proof method for storing valuable data, but barcode scanning devices are necessary to decode barcode symbols and standards and transmit the data to a WMS.
The WMS, in turn, aggregates data about inventory, vendors and suppliers, parts, ordering information, manufacturers, and every necessary detail about an item in a centralized database.
Compatibility is a key consideration when selecting barcode labels, hardware, and software solutions to support warehouse automation. Barcode scanners come in a range of options with varying capabilities such as:
Choosing the right barcode scanning system depends on a number of factors including, but not limited to:
Likewise, there are dozens of warehouse management software solutions, which range in features and functionality based on several factors. Some are targeted to specific industries, for instance, with specialized reporting capabilities that can aid in regulatory compliance, while others are better-suited to support certain warehouse automation functions.
Some key considerations include:
When implementing a warehouse label solution, along with the hardware and software components to complete the foundation, you’ll want to ensure that these elements are fully compatible and will work seamlessly together to enable your warehouse to function as the well-oiled machine it should.
We mentioned AGVs earlier, but they’re worth a deeper dive. AGVs are a relatively newer innovation, and offer direct savings on labor costs and also improve the efficiency and reliability of storage and retrieval processes.
AGVs are essentially robots that rely on markers on the floor of the facility, wires, or laser vision technology to navigate through the building and are able to perform functions such as:
There are an increasing number of AGV options for warehouses to choose from, with varying capabilities. For instance, there are automated carts which can move products on an assembly line or transport goods from warehousing to manufacturing plants.
Because these carts are guided by magnetic tape, setting up the initial flow or reconfiguring the route as necessary is simple. Transponder tags are used to convey when the cart should stop or perform a specific action, such as increasing or decreasing speed, or lifting or lowering.
Some companies offer a range of options spanning everything from standard, basic configurations to completely custom-built AGVs that can be designed to meet highly specialized application requirements.
In the middle of the spectrum are dual-use AGVs, which can operate either manually or as a fully-functional AGV. For some warehouses, dual-use options are a smart investment that can ease the transition from manual to automated processes.
For those already in the trenches of automation or those with specialized applications, the growing availability of customized AGV solutions is a valuable option.
AGVs, of course, play a role in automated storage and retrieval systems, but they’re not the only automation option when it comes to these functions. Automated storage and retrieval systems (AS/RS) have actually been around since the 1950s, having first been introduced in Europe, Japan, and the United States. AS/RS consist of a few key components:
Pallet lifting and lowering devices are among the most commonly used AS/RS devices. These fixed aisle storage and retrieval machines move pallets into and out of storage locations, and they can be configured to match SKU density profiles, varying load types, and delivery speeds.
There are also case and load handling devices, which are a scaled-down version of pallet lifting and lowering devices used to handle smaller storage containers.
Newer varieties of case and load handling devices that make use of shuttle cars and robots are known as goods-to-person systems.
The use of AS/RS offers a multitude of benefits, including:
In addition to these benefits, warehouses implementing AS/RS realize long-term cost savings through improved efficiency, the ability to keep up with increased consumer demand, lowering risks, and boosting throughput and increasing overall inventory accuracy.
According to Westfalia, the average lifespan of an AS/RS is 25 to 30 years, while payback periods are typically between just three and five years.
There are a range of common challenges warehouse encounter when trying to implement automation which include:
1. Integration with Legacy Systems
One of the main hurdles is integrating the new automation technologies with a company’s existing legacy systems, such as Enterprise Resource Planning (ERP), Warehouse Management Systems (WMS), and Transportation Management Systems (TMS). These legacy systems may not be compatible with the new automation solutions, requiring complex integration efforts.
2. Scalability
As a business grows and order volumes increase, the warehouse automation system needs to be able to scale accordingly. Ensuring the automation solutions can handle higher data volumes and transaction loads without compromising performance is crucial.
3. Workforce Adjustment
The introduction of automation can impact the existing workforce, as many tasks previously performed by human workers are now automated. This can lead to resistance to change and concerns about job security. Effectively training employees and fostering a culture of adaptability is essential.
4. Maintenance and Reliability
Warehouse automation systems consist of various electronic and mechanical components that require ongoing maintenance and support to ensure reliable operation. Unplanned downtime or system malfunctions can significantly impact productivity and customer satisfaction.
5. Data Management and Security
Warehouse automation generates a large volume of data that needs to be properly managed, secured, and leveraged for decision-making. Ensuring data integrity and accuracy is critical, as poor data quality can negatively impact the company’s financial performance.
6. Cost-Effectiveness
Implementing warehouse automation can involve significant upfront investments. Ensuring the chosen solutions are cost-effective and provide a favorable return on investment is a key challenge for many organizations.
Automating a warehouse, particularly a warehouse once operated entirely manually, is a serious undertaking, but one that pays off in dividends when automation is evaluated, analyzed, and planned taking all available data into consideration.
According to Path Guide, warehouses operate most successfully when seven key fundamentals are addressed:
The three main levels of warehouse automation are:
The key distinction across the three levels is the progression from manual operations to automated decision-making to automated physical handling of goods within the warehouse.
the future of warehouse automation is characterized by the following key trends:
Warehouses are moving towards more flexible and intelligent automation solutions, including:
Artificial Intelligence (AI) and Machine Learning (ML) will play a central role in warehouse automation, enabling:
Warehouses will see a rise in collaborative robotics, where humans and robots work together to leverage their respective strengths:
Warehouse automation solutions will prioritize flexibility and scalability to adapt to changing business needs:
The future of warehouse automation is centered around creating a more efficient, flexible, and data-driven supply chain through the strategic integration of cutting-edge technologies and human-robot collaboration.
Our sales engineers are experts in automatic asset tracking, tagging and identification,a nd can answer all your questions. Get in touch now.
Lets Talk ›Enter your information and get a free checklist of the top questions to answer and tips to plan a successful asset tagging project for any warehouse management system implementation.