What is Asset Management? Why is It Important?
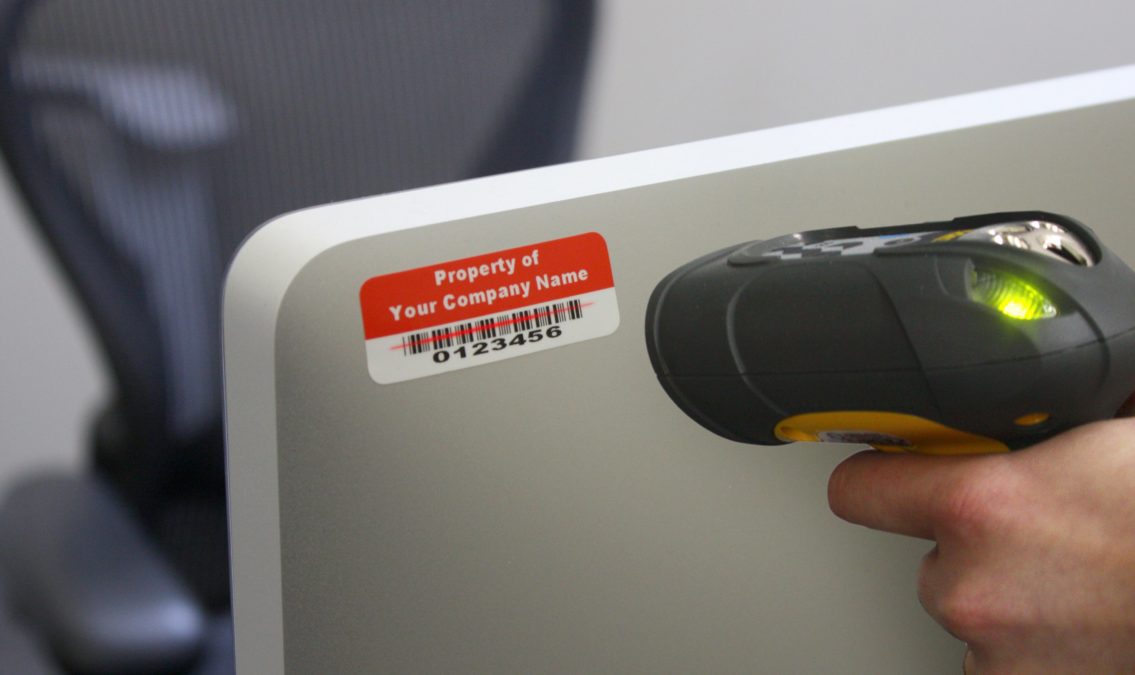
In today’s competitive business landscape, organizations are constantly seeking ways to maximize efficiency and minimize costs. One crucial aspect of achieving these goals is effective asset management. From equipment and machinery to software and intellectual property, assets form the backbone of any organization.
But what exactly is asset management, and why is it so important?
This article delves into the world of asset management, exploring its definition, key components, and the significant impact it can have on an organization’s operations, compliance, and bottom line.
Asset management is a process for tracking and monitoring a company’s fixed and/or moveable assets for financial accounting, preventive maintenance, and theft deterrence purposes. Asset management is important for compliance and managing the bottom line, but it becomes especially complex for organizations with multiple locations, fleets, field service workers, or other complex asset situations.
Effective asset tracking solutions are critical for efficient location monitoring, inventory counts, and oversight of maintenance, asset condition, and depreciation for high-value and business-critical assets.
Organizations may adopt asset management practices such as asset management software solutions, automated tracking methods with fixed scanners and bar codes, or asset tags with portable bar code readers that produce reports to help them manage their assets. Implementing effective asset management solutions while a company is small fosters seamless growth, particularly with the comprehensive, scalable solutions available today.
Small companies and new organizations may overlook the need for comprehensive asset management solutions and delay implementation. In many such cases, these same organizations may find that they become overwhelmed with manual documentation and asset tracking processes as the company grows and accumulates a greater volume and variety of assets.
In some industries such as healthcare and government, regulations mandate that certain assets be carefully monitored and managed. Understanding industry regulations is essential for developing effective asset management programs that ensure ongoing regulatory compliance and selecting industry-specific asset tracking solutions that meet regulatory specifications.
In other industries such as utilities, regulations do not always dictate how assets should be tracked or managed. In these industries, however, it’s common that best practices recommend the use of comprehensive asset management programs to optimize performance, maintain consistent service levels, and manage overhead costs.
Beyond regulatory compliance, many organizations need to depreciate high-value assets, monitor the performance of equipment, machinery and other valuable property, be able to quickly locate parts and determine the last date of maintenance, among a multitude of other scenarios that make effective asset management a necessity for modern companies. Keeping track of various statuses and operational documentation across several different systems, documents, or applications makes it challenging to consolidate data for reporting.
In addition, failing to integrate data systems leaves missed opportunities for uncovering ways to optimize performance, enhance productivity, and boost the company’s bottom line. A centralized, comprehensive asset management program solves these challenges and offers a competitive advantage for today’s organizations through greater visibility and the ability to identify performance improvement and cost-cutting opportunities.
When asset management is handled correctly, organizations reap the benefits. For example, organizations that correctly handle asset management realize the savings and see an increase in efficiency and productivity. Specifically, accurate asset management often yields substantial tax savings in depreciation deductions. Organizations that utilize asset management best practice also have an easier time complying with GASB 34 and GASB 35 standards.
Not only does proper asset management help companies to better control their finances and productivity and enable greater efficiency and profitability, but it also improves asset tracking and inventory procedures. For example, comprehensive asset management software systems collect information on fixed asset performance and integrate with company databases so inventory managers and asset managers can track assets and inventory separately yet compare procedures in warehouses. When asset and inventory barcodes work together, operations become smoother and accountability improves.
There are quite a few things that organizations can do to better manage their assets. A few of the most important asset management best practices include…
Asset management enables greater visibility, accuracy, and reporting. Capturing accurate data with asset management systems as part of asset management programs helps organizations to streamline operations, improve finances, save on taxes, and improve their overall bottom line and productivity
Our sales engineers are experts in automatic asset tracking, tagging and identification,a nd can answer all your questions. Get in touch now.
Lets Talk ›Enter your information and get a free checklist of the top questions to answer and tips to plan a successful asset tagging project for any asset management or tracking system implementation.