The Expert’s Facility Maintenance Checklist (with PDF Download)
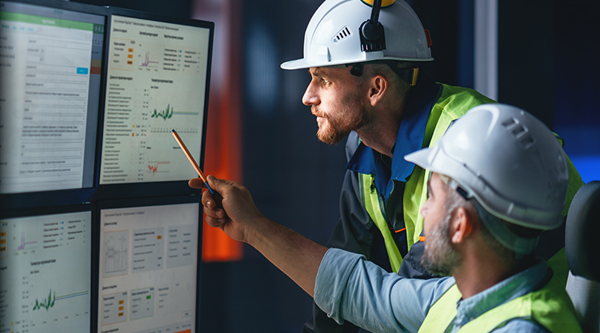
Facility maintenance is challenging and requires coordinating several resources within a building. Using a custom facility maintenance checklist can have a dramatic impact on your ability to prevent safety hazards and minimize equipment downtime.
One of the best ways to improve your maintenance plan is to use our expert checklist ideas as a starting point for discussions with your local team. The best checklists will be thorough and define necessary activities for every core component of the facility.
Most organizations rely on facility maintenance checklists to guide personnel through routine checks. Since the specifics of these checklists differ from organization to organization, businesses must create checklists tailored to their unique needs.
In this guide, we’ll explain the benefits of using a facility maintenance checklist, detail the most common facility maintenance checklist categories, and offer tips to help you implement your checklists effectively.
Photo by Emmanuel Ikwuegbu from Unsplash
Using a comprehensive facility maintenance checklist offers a range of benefits that can significantly improve the efficiency, safety, and cost-effectiveness of your operations.
A thorough facility maintenance maintenance checklist ensures employees regularly inspect and maintain all equipment before minor issues become big problems. By catching potential problems early, organizations avoid unexpected breakdowns that cause downtime.
A proactive approach keeps machines running more smoothly and minimizes interruptions, leading to significant cost savings and better productivity.
Regular maintenance, guided by a checklist, improves workplace safety. Well-maintained equipment is less likely to malfunction or cause accidents.
Since many industries have to follow strict regulatory standards, checklists give your team the benefit of documentation. They also ensure consistent maintenance activities, keeping you compliant at every turn by creating a much-needed paper trail that simplifies audits and minimizes mistakes. Take a look at the table below for a summary of the most common facility maintenance maintenance mistakes.
Mistake | Description |
---|---|
Not Scheduling Regular Checks | Failing to maintain a regular schedule for maintenance activities. |
Ignoring Data from Sensors or CMMS | Overlooking valuable data that can predict maintenance needs. |
Inadequate Staff Training | Not providing sufficient training on facility maintenance procedures and tools. |
Not Updating Checklists | Failing to update checklists as equipment and technology evolve. |
Inefficient Budgeting | Not allocating enough budget for comprehensive maintenance tasks. |
Maintenance and repair (M&R) budgets account for a large portion of a facility’s overall operations budget, so optimizing equipment lifetime whenever possible is important. Ongoing maintenance extends the life of machinery by ensuring it’s in optimal condition.
You can’t prevent all breakdowns, but regular maintenance prevents wear and tear that leads to premature replacements. Over time, facility maintenance translates into significant cost savings by cutting the frequency and cost of replacements. Plus, well-maintained equipment operates more efficiently, helping you cut production times and even utility costs.
Comprehensive facility maintenance maintenance checklists offer a detailed record of all maintenance activities. This documentation is crucial for tracking the maintenance history of every machine and piece of equipment. It helps you understand the lifecycle of all components, making it much easier to plan future maintenance needs.
Checklists simplify assigning tasks between maintenance teams or shifts, leaving no stone unturned. Good documentation also makes it much easier to troubleshoot issues by giving you better insight into past maintenance activities.
Facilities require a tremendous investment. All facility maintenance programs should have checklists just for the outside of the facility, which is the first line of defense against hazards.
Many potential hazards affect a facility’s exterior, including storms, sunlight, and other weather conditions. When designing a checklist for facility maintenance, incorporate routine checks for critical equipment and designated areas outside the building. This protects the facility, improves security, and makes it easier for employees and visitors to access building resources.
Camcode’s expert facility maintenance checklist focuses on the major facility systems at most locations, and you can customize it as needed. Not all equipment systems are created equal, and the typical facility will require a mix of daily, weekly, monthly, quarterly, and annual checks.
Follow this maintenance checklist to maintain the exterior of your facilities.
Roofing
Parking Lots and Garages
Windows and Doors
Lawns and Facility Grounds
The interior maintenance of a building can be complex. Fortunately, a well-organized interior maintenance checklist can make this run more smoothly. It’s helpful to assign owners for specific areas of the building or its subsystems, such as HVAC systems, that require regular maintenance.
The below facility maintenance checklist is a good starting point, but each facility is unique. These maintenance checklists are basic recommendations you should customize with input from your team.
Electrical & Energy Utilization
Plumbing
HVAC
Equipment
Elevators
Security
Fire Safety
Photo by Nuno Silva from Unsplash
In addition to a facility maintenance checklist defined by your facility’s infrastructure, it’s also helpful to define seasonal maintenance inspection items at certain times of the year. The contents of your checklist will vary depending on the nuances of your location, but these ideas should be enough to help you kick off seasonal planning. Incorporate these ideas into existing monthly, quarterly, or annual checklists as needed.
Spring/Summer
Fall/Winter
Photo by Dan Loran from Unsplash
Creating a facility maintenance checklist is the first step in improving the lifespan of your assets. However, organizations still need to implement these checklists to see real change. Follow these tips to make the most of your checklists.
Step | Description |
---|---|
Integrate with CMMS or Maintenance Software | Digitize checklists for real-time updates and automated reminders. |
Improve Accountability with Durable Asset Tags | Use durable tags to streamline documentation and maintain accurate maintenance history. |
Train Maintenance Staff | Conduct regular training on checklist usage and associated tools. |
Regularly Review and Update Checklists | Keep checklists relevant by incorporating changes in technology and industry standards. |
Track and Analyze Data | Use collected data to identify trends and optimize maintenance efforts. |
Facility management (FM) software and computerized maintenance management systems (CMMS) allow facility managers to digitize maintenance workflows with a comprehensive asset-tracking system.
Choose software that fits your organization’s size and complexity. It should allow for easy integration of your existing checklists and offer customizable features to suit your needs. Digitize all facility maintenance checklists within the software so they’re easily accessible and updated in real time. This reduces paperwork and the likelihood of errors or lost documents.
Most FM and CMMS systems allow you to set up automatic reminders and alerts, which are the best way to keep your maintenance tasks on schedule. Never overlook a critical task again—plug everything into the software to ensure implementation and create a helpful paper trail in the event of an audit.
By tagging assets and equipment with durable barcode labels and asset tags, such as Camcode’s metal equipment tags and facilities management asset tags, you can streamline documentation and maintain an accurate maintenance history for every asset. This approach optimizes both short and long-term maintenance planning.
Photo by Guilherme Cunha from Unsplash
Conduct regular training sessions to familiarize all maintenance staff with using the checklists and any associated software or tools. The program should include training on interpreting checklist items and correctly recording data. Developing a user manual or guide specific to your facility maintenance checklist and system is also a good idea.
This provides a handy reference for staff to ensure consistent application of the maintenance tasks.
Don’t be afraid to embrace change. Regularly reviewing these checklists ensures they stay relevant and comprehensive, which will help you save time, trim costs, and remain compliant.
Incorporate changes in technology, equipment, and industry standards into the checklist as necessary. This ensures that the maintenance tasks are up-to-date and reflect current best practices.
Encourage staff feedback on the usability and effectiveness of your checklists. They use these checklists regularly, so trust their feedback to make adjustments that improve the process.
As you change the checklists, document all revisions and provide the updated versions to all team members. You want everyone working with the most current information, so archive outdated checklists and store them where they’re out of reach for most employees.
Utilize the data collected from a completed facility maintenance checklist to identify trends, recurring issues, or areas for improvement. Generate reports based on checklist data to evaluate the effectiveness of your facility maintenance efforts.
Drawing conclusions from the data justifies investments in maintenance and identifies areas where you could optimize resources. Data analytics predicts future maintenance needs, which allows you to create plans for reducing downtime and extending equipment lifespan.
Facility maintenance safeguards assets, ensures safety, and enhances operational efficiency. Facility preventative maintenance is more than a routine—it’s an ongoing process that adapts to a facility’s evolving needs and operations.
By integrating these checklists with cutting-edge CMMS or maintenance software, facilities can leverage technology to streamline processes, enhance accuracy, and improve accountability.
However, bridging the gap between digital checklists and the reality of what’s happening on the ground with your facilities and assets is challenging. Opting for high-quality labels and tags from Camcode sets you up for success, regardless of whether you follow preventive, predictive, or reactive maintenance strategies.
Choosing durable equipment tags and labels is crucial to ensuring they remain readable throughout the lifespan of your assets. This eliminates the need to invest the time and money into re-labeling your assets multiple times. Camcode offers a variety of facility management labels to suit the needs of your applications, from Extra High Temperature Labels that can withstand exposure to temperatures up to 1200 degrees Fahrenheit to Premium Polyester Plus Labels with Heavy Adhesion Strength for less-demanding applications that require heavy adhesion strength.
Camcode’s Metalphoto® anodized aluminum labels, such as Foil Metalphoto® Labels and Rigid Metalphoto® Labels, offer excellent resistance to chemicals, abrasion, solvents, extreme cold, heat, and UV. These durable facility management labels have an expected exterior lifespan of more than 20 years.
Facility maintenance is a crucial component of facility management, but accurate documentation about every individual asset and its maintenance requirements is challenging without the help of durable asset tags for your equipment and fixed assets. Camcode’s equipment tags enable your maintenance and operations staff to quickly and easily document maintenance activities by scanning a barcode.
In addition to durable facility management labels, Camcode also offers data collection, data validation and reconciliation, and label installation services to get your facility maintenance program started quickly. Get in touch with Camcode to learn how our durable facility management labels facilitate faster data collection and improved conditions monitoring.
To streamline your maintenance planning and ensure that all critical tasks are performed consistently, we are offering a comprehensive facility maintenance checklist available for download in PDF format. This checklist is designed to help you keep track of routine maintenance activities, prevent equipment failures, and extend the lifespan of your assets.
[Download The Facility Maintenance Checklist (PDF)]
Our facility maintenance checklist covers a range of essential tasks across various facility systems, including:
To get started with your facility maintenance program, download our comprehensive checklist by clicking the link below:
[Download The Facility Maintenance Checklist (PDF)]
By using this checklist, you can ensure that your facility remains in optimal condition, reducing downtime and enhancing overall productivity.
The most common mistakes include:
Addressing these mistakes is crucial for designing an effective facility maintenance program.
Yes, facilities maintenance can lead to significant energy savings. It minimizes energy consumption by ensuring that all equipment runs efficiently without any issues.
Regular maintenance also prevents inefficiencies, friction, and increased power demands from poorly maintained machinery, reducing your utility bills and carbon footprint.
Organizations should meticulously document and manage maintenance records with a CMMS. These records should include details like:
Well-managed records are essential for tracking performance over time, planning future maintenance, and ensuring regulatory compliance.
Our sales engineers are experts in automatic asset tracking, tagging and identification,a nd can answer all your questions. Get in touch now.
Lets Talk ›Enter your information and get a free checklist of the top questions to answer to plan a successful asset tagging project for any maintenance tracking or facility management system.