50 Expert Facilities Management Best Practices and Tips
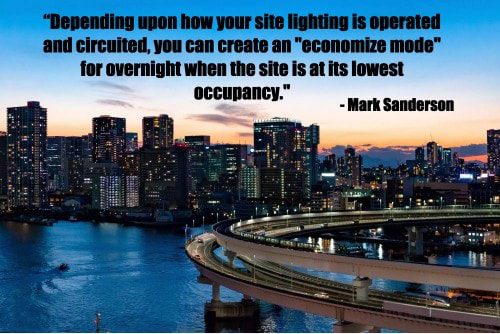
Whether you’re a celebrated and seasoned facilities manager or just an aspiring one, we all know that this is a job that requires continued education and plenty of sage advice, especially when it comes to the question of implementing new technologies.
Lucky for you, we’ve gathered 50 of the most helpful and applicable tips and facilities management best practices from the greatest minds in the field. Take some time to peruse these tips and tricks so that you too can do what you need to better manage your facility to make it as efficient, as modernized and as safe as possible.
We’ve organized the facilities management best practices by section, so you can easily find the tips that you need the most.
1. Cut night site lighting. “Depending upon how your site lighting is operated and circuited, you can create an ‘economize mode’ for overnight when the site is at its lowest occupancy. Keep perimeter site lighting on around your property and all entrances and main drives lit.
“You need to make certain that the lighting up close to the building and all entrance and exit doors will remain on along with any emergency fixtures lighting pathways. Look for the site lighting in between these zones and make accommodations in your lighting automation controllers to be able to shut off zones or circuits that are least occupied.”—Mark Sanderson, as quoted by Brandon Lorenz, Ten Tips For Facility Managers To Cut Energy Costs, FacilitiesNet
2. Replace older lighting with LEDs. “Memorial Sloan-Kettering Cancer Center chose LEDs to replace existing lighting in a parking garage open 24/7, halving the garage’s power consumption. Meanwhile, Mediapolis Community Schools in Mediapolis, IA, also embarked on a retrofit of LED exterior lighting.
“Most of our old lights were either 250 or 175 watts. Those were replaced with 30-watt LED. Our 70-watt lights were replaced with 20-watt LEDs and our 70-watt can lights were replaced with 10-watt LEDs. We’ll get a nice rebate from our electric company, plus monthly savings on our electric bill.”–Dennis Breuer, as quoted by Janelle Penny, Top 12 Strategies to Maximize Cost Savings, Buildings Magazine; Twitter:@BuildingsMedia
3. Implement a sustainable facility design plan. “Sustainable design is more attainable and affordable than it’s ever been, especially when you think in terms of years instead of days and weeks. It’s also worth noting that sustainable design is very well favored among the public, which is an extra incentive for companies interested in reinforcing their reputation as socially responsible and environmentally concerned.”–David Verner, Reducing Industrial Facility Costs with Sustainable Planning, Area Development; Twitter: @areaDevelopment
4. Know the total cost of all facility work done both directly and indirectly. “To the untrained eye, the facilities maintenance arm of a business appears to be a black hole of cost. The costs of these FM services add up, and unless discrepancies arise, that is where most of the business analysis ends. However, facilities maintenance managers, who are privy to all of the nuances that make up each work order, understand the complexities and overhead involved in this sector of business.
“There are a multitude of variables that affect the total cost of each service like trip charges and materials, in addition to the other direct and indirect operational costs associated with facilities management.”–Sean Hartnett, How to Calculate the True Cost of Facilities Maintenance, SMS Assist; Twitter: @SMSAssistLLC
5. Consider less obvious improvements that impact facility energy use. “Some energy-related projects will be more or less hidden from the users and primarily pursued to reduce energy demand, such as chiller and fan-unit upgrades. Such projects may end up providing the building users with better temperature control, but this is not the primary goal of the upgrade.
“Operational changes such as reducing the hours of HVAC and lighting operation, and changing setback temperatures, which require very little expenditure (if any at all) do not directly affect user experience, but can produce large reductions in electricity loads. In general, working with the building operations team to reduce energy use can produce impressive reductions in load.”–Jim Newman and Marcus Springer, Be a Hero With Lower Operating Costs in Your Building, FMLink; Twitter: @FMLinkGroupLLC
6. Don’t forget to look at your building’s insulation. “All commercial buildings are insulated; building codes make it mandatory to insulate up to a certain level. Unfortunately, because most buildings are put up under strict guidance to budgets, they are usually put up with only the minimal amount of insulation. And because the company putting up the building is rarely the one managing or owning it, the two have distinctly different viewpoints on budgets.
“Higher insulation means better efficiencies. Whenever possible, you can increase the level of insulation and have it make immediate differences in the overall comfort level of the building’s occupants. Common measures include installing energy efficient windows and lighting systems, and redoing the roof to minimize the solar impact on the building itself.”—Tips to Reduce Commercial Heating and Cooling Costs, Total System Services
7. Utilize a strategic sourcing approach to find the Right suppliers for facility work. “Finding the right suppliers to maintain your facilities can be difficult and time-consuming. From janitorial services, to groundskeeping and maintenance supplies, ensuring suppliers are providing apples-to-apples quotes, developing contracts with clear service levels, and validating that supplier quality of service and productivity levels are maintained are all critical to the success of any facilities maintenance project.
“Attempts to cut costs in the facilities maintenance category are tempered by the inability to endanger the standards for the safety and comfort of your employees. For many organizations, this results in their paying a premium to their facilities maintenance suppliers.”—Strategic Sourcing Strategies For The Facilities Maintenance and Facilities Management Category, Source One Management Services ; Twitter: @getsavings
8. Your boiler plant may be a major source of efficiency gain potential. “Boilers today can reach efficiencies of up to 96 percent using condensing technology; however, a typical building, including new buildings, uses atmospheric type boilers which, for all intents and purposes, are only slightly more advanced than a science lab Bunsen burner. This technology is reliable and it works, but it is expensive to operate. Typically, we see this technology installed to minimize construction costs with very little consideration for the long-term energy impact that the building’s operating budget is left to absorb.”–Ross Morley and Ed Porasz, Six Energy Audit Tips for Building Managers, REMI Network; Twitter: @REMINetwork
9. Schedule a professional energy audit. “An energy audit systematically identifies and develops opportunities to help reduce energy use in an institutional or commercial facility and, as a result, decrease building operating costs. Focusing the audit is imperative for maintenance and engineering managers.
“Determining the areas and systems to include in an audit depends partly on the resources an organization is willing to invest in energy efficiency, the facilities’ complexity, and the amount of detail and analysis desired from the audit. Understanding these factors will help managers select the audit level that fits the needs of the building and organization.”–David Cosaboon, Which Energy Audit is Right for Your Facility?, FacilitiesNet
10. Identify potential major efficiencies in your kitchen energy use. “Commercial kitchens are high energy users, consuming roughly 2.5 times more energy per square foot than any other commercial space, according to the US Environmental Protection Agency (EPA). Of that, as little as 40% is used in the preparation and storage of food, says the UK’s Carbon Trust; much of the wasted energy is dispersed into the kitchen.
“The technology exists for dramatic reductions in energy consumption, resulting in carbon-footprint reductions and significant cost savings. The EPA claims that restaurants that invest strategically can cut energy costs by between 10%-30%; Foodservice Consultants Society International (FCSI), the professional organization for design and management consulting services, estimates that energy savings can be as high as 40%, equating to 3%-6% of operating costs.”–Energy Efficiency in the Kitchen, Green Hotelier; Twitter: @green_hotelier
11. Consider the entire life cycle costs of a building. “Life cycle costs are a way to measure the cost of improvements to building infrastructure over time. This allows building and facility management professionals to determine whether the cost to improve a particular element of a building or a system in it against the cost savings over the same period. If the cost of an upgrade over its lifetime offers an advantage over the building operational costs it will save, then it’s generally considered a good investment.”—Answers to 8 Common Building Operation Cost Questions, Enervise
12. Measure your PM versus all maintenance activities. “Develop performance measures for your PM process with an emphasis on measuring the amount of PM that is work completed compared to all other work. Total PM hours should be the highest percentage of all the department’s maintenance work. This goal might seem impossible, but over time, it is very achievable.” –Michael Cowley, 5 Tips for Successful Preventive Maintenance, FacilitiesNet
13. Set a plan and stick to it. “Preventative maintenance is all about planning, plain and simple. Every piece of equipment or machinery at your disposal or under your care should have a schedule of what type of maintenance it requires and when it requires that check-up.
“Settings a schedule not only ensures that your equipment stays in tip-top shape for the duration of its projected lifespan, but it also helps you plan for staffing needs and stay within budget. Once you have the plan ready, never deviate from it.”–Lisa Richards, 7 Preventative Maintenance Tips for Your Facility, MAPCON; Twitter: @MAPOCONtech
14. Focus on specific failure models. “Failure modes are defined as “how something fails.” Let’s use a flat/membrane roof to show an example of what a failure mode is. On a flat/membrane roof, one failure mode may be “penetration of roof membrane,” and the causes of this failure mode could be many. Knowing the failure mode(s) of a specific maintainable item such as a membrane roof and its causes can be key to early detection of roof failure (not meeting the intent of the end user) so the repair can be made before it affects an operation.“–Ricky Smith, Five Tips For Optimizing A Facility Preventive Maintenance Program, Engineered Systems Magazine; Twitter: @esmagazine
15. Do a proactive walkthrough to find “small” problems. “Catch small problems now before they become big ones. Addressing small details can add up to huge improvements in appearance and functionality. Ask your facilities services provider, janitorial company, and/or handyman to walk through with you, focusing on details you’d normally overlook. Some things to inspect for repair/replacement are: doors (door sweeps, door stops, sticking locks, etc.), corner guards, tile and grout, light switches and face plates, ceiling tiles, countertops and shelving, cabinets and hinges, and fire extinguishers.
“And don’t forget how much fresher everything looks with new caulking and a new coat of paint on the walls – the warmer weather can make Spring a great time to give new aesthetic life to your facility.”–Bob Clarke, 6 Spring Maintenance Tips for Facilities, Buildings Magazine; Twitter: @BuildingsMedia
16. Know the difference between predictive, preventative, and reactive maintenance. “There are generally three approaches to building maintenance used by facility managers:
The most common type of maintenance employed by facility managers is the “reactive” approach. According to a post by Akita Box on preventative maintenance planning, 85 percent of total maintenance spending is on reactive maintenance. The reason for this is simple: It’s the cheapest—or at least it seems to be the cheapest. The reality is that it’s only the cheapest when everything is running smoothly. But, as we all know, things don’t always run smoothly.”–Neal Peters, Top Ways to Reduce Maintenance Costs for Your Facility, DPM Care; Twitter: @dpmcare
17. Understand the difference between work time and idle time. “You may schedule preventive maintenance based on meter readings on an equipment. However, equipment meters usually do not differentiate between work time and idle time. So a machine that is idle for 20% of the time may have preventive maintenance scheduled more frequently than necessary. If the idle time is predictable it may make sense to schedule preventive maintenance based on bigger meter intervals.”—7 Tips To Plan Equipment Preventive Maintenance, SM Global
18. Ensure that your preventative maintenance tasks are beneficial to your equipment. “Greasing the rack and pinion of a beam saw, for instance, can cause grease and saw dust to solidify inside the gears over time, eventually preventing them from moving. If you’re unsure which tasks are beneficial to each piece of equipment, ask your equipment representative.”— 10 Tips for Preventative Maintenance, Stiles Machinery; @StilesMachinery
19. Anticipate future spare parts inventory needs. “Having spare parts and supplies around the time of a major preventive maintenance schedule is absolutely critical. Asset management software allows you to check the availability of the spare parts for dates when the work orders are due. This report can help you identify parts that are insufficient for the required work orders in the future. If you know which parts you are falling short on, you can order them in advance from suppliers rather than waiting till re-order limits are reached.”—7 Tips for Better Equipment Preventive Maintenance, Nexgen Asset Managment; Twitter: @nexgenam1
20. Use different methods of communication. “Appropriate repetition and reinforcement are necessary. The average person is bombarded with more than 300 messages while at work, and multiples of that outside of work, Finney says. Getting a message to land with an audience might take as many as 12 repetitions, in some cases, he says.”–John Finney as quoted in Facilities Maintenance Decisions Magazine, For Good Facility Management Communication, Keep Three Points in Mind; Twitter: @maintenance_mag
21. Optimize the use of available workspace. “Space costs money. Knowing that we are moving towards a working environment consisting of virtual or mobile workers, investing time in developing new workplace designs that can suit these new ways of working while increasing space utilization rates can result in impressive cost savings. Flexible workstations, distributed workplace strategy and mobile workplace strategy are just a few ways of maximizing the value of current properties. Reinvestment can with advantage be allocated to less space, but better space propositions.”—7 Ways to Grow Competitiveness in the Facility Management Industry by 2020, Service Futures; Twitter: @issworld
22. Be the master of your company’s physical assets. While other managers may work to manage clients or staff, your job is to manage facilities and all that occurs in them. Your corporation’s physical assets are just as important as your human resources, and you are the expert in this field. Whether it’s collating data or contributing to the organization’s bottom line, your input is a valuable part of corporate decision-making. If you’d like to change buying practices or convert to more energy-efficient heating, make a statement and back it up with your data and your years of facilities management experience.–James McDonald, 5 Things Facilities Managers Must Do to Gain Respect & Clout, iOffice; Twitter: @iofficecorp
23. Set clear definitions for facilities work practices. “Workplace inclusion has to be clearly defined before any initiatives can be pushed forward. One useful definition of an inclusive office is a workplace in which all staff are treated with respect and have equal access to resources and opportunities. Facility managers should build on this high-level description to create an idea of what concepts like equal access, diversity and fairness look like in their own facilities. Including these definitions in your company’s core values will help you to set clear goals and build concrete policies.”–Nick Mason, A Facility Manager’s Guide to Inclusive Workplaces Office Space Software; Twitter:@OfficeSpaceSw
24. Use a design that plans for social time and spaces. “Let’s get together: when you’re designing your facilities, design social spaces for your employees. These might be lunch or break rooms, games rooms, gyms, or even community gardens. When you provide places where employees can relax and socialize in a less-structured atmosphere, you may find that new connections emerge between departments and between different levels of management.”–Tiffany Bloodworth Rivers, 7 Tips to Help Facilities Managers Make The Workplace A Stress Free Zone, iOffice; Twitter: @iOfficeCorp
25. Consider moving some basic activities from outsourcing to in-tasking. “Another possibility for cutting costs, say experts, is not just moving staff around, but moving work around also. This means carefully examining all outsourcing contracts to see if they can be scaled back and the work completed by in-house staff. Bechtol says she’s actually been doing this for years — completing tasks like painting and cleaning with in-house staff and overtime — but it’s even more valuable now in tough economic times.”–Nancy Bechtol as quoted by Greg Zimmerman, Facilities Maintenance Decisions Magazine; Twitter: @maintenancemag
26. Create a formal in-house process for developing employee skills. ”We are focused on ‘building a bench’. This concept is broadly used to describe our attempt to formally identify in-house talent in many of our labor shops. We identify talent through a competitive selection process based on potential vs. skills and promote our selected personnel to the worker and helper level while training them to achieve appropriate full mechanic level with associated certifications/licenses.”–Robin Morey as quoted by Higher Ed Facilities Forum, Dealing with an Aging Facilities Management Workforce, Twitter: @HEFForum
27. If outsourcing your FM, work with an agile partner who adapts to your needs. “This is one of the single biggest advantages that smaller providers have. They can allow their frontline staff to be creative and actually make changes to processes and implement them. This directly leads to the client receiving a more fit-for-purpose solution and ultimately receiving greater value which grows a greater relationship.”–Andrew Hulbert, as quoted by Kevin Stanley, The Art of Delegation, FMWorld; Twitter:@fm_world
28. Sell your department wisely during budget presentations. “We always present our budgets by leading with how the proposal responds to a real problem. In other words, there has to be a compelling reason based on our mission for why we would submit budgets for anything.” By presenting specific information on how and why you’ve chosen your budget numbers, you can help the C-suite see that your budget is well within reason.”–Tim Woodley, as quoted by David Spence, 5 Budgeting Tips for Facilities Managers, Office Space; Twitter:@officespacesw
29. Automate the work order process. “When you automate the work order process, you remove human error associated with it. Essentially, you’re taking the people out of the process and ensuring nothing gets missed or overlooked. Doing this allows you to create, track, edit and automatically communicate work orders for your facility. This is number one on the list, because it’s one of our favorite habits – and arguably the most important! Don’t let problems with employees slow down your operation or increase workplace stress for others.”—The 7 Habits of Highly Effective Facility Managers, 24/7 Software; Twitter:@247_software
30. Utilize software to help facilities managers organize and access information.
“There are many different software options out there than can aid FMs in organizing and streamlining their everyday tasks. This ranges from software designed to help manage all maintenance activities to logging and tracking facility visitors for security purposes.
There are also several comprehensive facility management software options available. One popular option in this area is NetFacilities, a web-based software that aims to centralize the many things FMs need to manage—from vendors and work orders to asset management and preventative maintenance—in one convenient place.”–Neal Peters, Top Technology Tools for Facility Managers, DPM Care; Twitter: @dpmcare
31. Utilize modern smart sensor solutions to reduce costs and enhance capabilities. “By populating buildings with such smart sensors, operating costs are dramatically reduced, productivity is enhanced, and occupants’ comfort is improved. Specifically, detailed information about occupants’ presence, location, count, and activity can now be used to significantly optimize facility management. Hot desking, meeting rooms booking, optimized space planning, and energy savings are some of the immediate use cases.”–Itamar Roth, Facility Management Is Facilitated By Smart Sensors, Facilities Executive; Twitter:@facilityexec
32. Manage HVAC remotely using software tools. “One of the most exciting features of Facilities Management software is the ability to manage heating and cooling remotely, or set a programmable thermostat to move set temperatures up or down throughout the day. Facilities planners love the ability to analyze and explore energy use from heating and cooling systems. Leaders can use the ‘business intelligence’ delivered by the software to set thermostats and controls for maximum savings in energy costs. Some of these tools can even be ported to smartphones to help remote managers do their jobs from wherever they happen to be.”—10 Ways Software Can Help with Facilities Management, SelectHub; Twitter:@selecthub
33. Use your software to double-check your compliance. “Maintenance and facilities administration systems must frequently abide by national and global regulatory requirements. All maintenance administrators face occasional random or audits inspections by regulatory authorities. Maintenance software enables you to prove regulatory conformity and decrease the amount of paperwork and preparation that is needed for an audit. Maintenance administrators can simply create reports showing the maintenance work done on essential machinery. This makes conformity traceable and minimizes the risk of non-compliance penalties.”—7 Steps to Successful Facilities Management, Fasttac; Twitter: @fasttac
34. Facilities management KPIs should highlight errors and opportunities. “KPIs allude to opportunities and errors in your company. Paired with the Internet of Things (IoT) and energy management systems, KPIs can be used to highlight missed maintenance tasks, greater traffic area of your business or problems with machinery. Take, for example, using a percentage KPI of planned maintenance against reactive maintenance. In other words, is preventative maintenance saving more money than repairing equipment when it fails?”—7 Tips for Creating Facilities Management KPIs, Entouch Controls
35. Use building information monitoring to monitor system performance. “Closely monitoring energy and water use to reduce building-operating costs is another benefit. By allowing owners to monitor and analyze the performance of multiple systems—air-conditioning levels, lights on automatic dimmers, water usage—BIM can lead to more thoughtful energy use, lowered expenses, and increased asset value.”–Michael Schley as told by Jeff Link, BIM for Facilities Management: 4 Tips to Improve Lifecycle Performance and Reduce Costs, Autodesk; Twitter: @autodesk
36. Consider advanced automated building entry solutions. “A feature that’s gaining a lot of ground is using facial recognition technology to let people in and out of the building. It’s more secure than key fobs or cards, and unlike cards and fobs, you can’t forget your face at home. It’s like batting a triple, or killing three birds with one stone. Automated building entry removes the need to grant special access to the building, replace missing key fobs or cards, or issue new ones to new employees.”–Michael Moulton, 5 Tech Features Facilities Managers Can’t Live Without, Teem
37. Provide a customer facing software solution for reporting improvements and tracking requests. “Offering simple solutions for your customers will keep them happy – and your buildings running smoothly. A quality customer facing solution will equip customers to report issues around your facility and track the progress of their requests. Not only does a customer portal help your clients feel heard as you keep them up to date on progress. A digital customer request system simplifies the work order and assignment process for your facilities management team as well.”—Top Facilities Management Tips for Long-Term Success, AssetWorks; Twitter: @AssetWorks
38. Thermal imaging technology can help identify and fix unseen problems. “Performing facility maintenance and engineering tasks is like sailing among icebergs. What technicians can’t see will sink them — or their facilities. Thermal imaging technology gives technicians the ability to see the unseen, making it easier to spot failing motors and electrical components, HVAC condensate leaks, bad ductwork, and leaky roofs. Technicians then can fix problems before they become large headaches, as well as reduce heating and cooling costs as part of sustainability initiatives.”–John Anderson, Putting Thermal Imaging to Work in Facility Maintenance, FacilitiesNet
39. Integrate a facilities management software system. “A surprising number of facilities managers have no true system in place for managing their space. More than a quarter of everyone interviewed – 28 percent – say they currently do not use any type of facilities management system. A further 23 percent of participants use pen and paper methods for their facilities management. While this is slightly better than no system at all, it still makes it very difficult to collect data, keep accurate records, or gain much insight from the information they have.”—The Importance of Facilities Management Systems, Team Support; Twitter:@teamsupport
40. Leverage your software system to make EH&S benchmarks transparent. “Facilities Management software is specially designed to help make health and safety benchmarks and outcomes transparent. It may help significantly with compliance with various industry standards, such as HIPAA in the healthcare industry and Sarbanes-Oxley in the financial field. It can help to document best practices for avoiding accidents, or in the worst case scenario, document the facts around a workplace accident. Various types of health and safety features can save a lot of time and effort for busy management teams, and help the company to benefit from a better reputation.”—10 Ways Software Can Help with Facilities Management, Select Hub; Twitter: @selecthub
41. Have an equipment criticality matrix to prioritize work. “This method identifies how critical a piece of equipment or maintenance task is to your business and will ultimately show you where it should land in your prioritization process. Criticality measurements should be standardized by assessing how seriously a single piece of equipment would disrupt operations in the event of a failure.“–Ashok Sharma and Barry Lawrence, 5 Essential Tools for Facilities Managers, eLearning Industry; Twitter: @elearnindustry
42. Smartsheet software can add unique collaboration features to everyday spreadsheet use. “Smartsheet is a spreadsheet that you share with your co-workers, but its features go far beyond Excel. This tool combines the traditional spreadsheet with project management tools, templates, and forms and allows you and your colleagues to access spreadsheets on mobile devices and work on them collaboratively.”–Tiffany Bloodworth Rivers, 9 Easy-To-Use Tools That Will Help Any Facilities Team Collaborate, iOffice; Twitter:@iOfficeCorp
43. Adaptive workflow tracking allows you to track activity throughout a diverse workforce. “The business world is increasingly embracing a larger remote workforce. Offices are used as areas to collaborate, develop, and design new ideas. The day-to-day work can be, and often is, done from home. That means you’ll need the ability to track workflows and project tasks across a diverse workforce. Emailing details back and forth regarding a project gets hectic, and it’s easy to lose an important piece of a proposal to your inbox.
Again, we’ll turn to automation – adaptive workflow tracking software that shows real-time project progress via a cloud-based platform will be the norm in a few short years. Products such as Trello or Asana are great examples of adaptive workflow tracking integrating with high success into businesses of all sizes.”–Michael Moulton, 5 Tech Features Facilities Managers Can’t Live Without, Teem
44. Keep your facilities management documents consistent and accurate. “If you’re a responsible facilities manager, you have to know what you’re responsible for. You cannot do your job properly without the correct information. If you don’t have proper records on the state of your facilities, you can’t do your job as a facilities manager. Without accurate documentation, you can’t even get a good bid from a vendor for work on your building. The first thing they will ask is, Where are the As-Built drawings? Without the As-Builts, the bid could be much higher.”—7 Tips on Reducing Facilities Maintenance Costs and Risks, SKYSITE; Twitter: @skysiteproject
45. Implement a consistent asset tagging process. “Verify assets from a minimum of two data points, such as the barcode and the item’s serial number. When disposing of assets, this step is crucial to ensure an “accurate and verifiable chain of custody,” which can help to mitigate data breaches (particularly for the disposal of IT assets) and also help to maintain compliance with regulations.
“Implementing a consistent asset tagging process flow ensures that all assets received by your company are consistently classified and tracked, making it easy to locate assets throughout the company, implement regular maintenance schedules, and maintain accurate record-keeping for auditing and accounting purposes. Developing clear policies and procedures and training your team members on approved asset tagging procedures streamlines processes and can ultimately have a positive impact on your bottom line, allowing you to improve resource utilization, reduce unnecessary duplication of assets, and get more usable life out of your investments.”–Varsha Saha, 6 Steps in Asset Tagging Process Flow, Camcode; Twitter: @camcode
46. Keep assets updated and clearly define essential vs. non-essential assets. “After collecting data and developing a maintenance schedule for your assets, you need to plan for the long-term maintenance of your asset inventory. Specifically, put a plan in place that revolves around updating and decommissioning assets. In some cases, you may find that a particular asset, even if updated, isn’t serving your organization in the best way, making it a non-essential asset that you don’t need to continue holding. Similarly, by having a working inventory list and accompanying data, dealing with critical needs and unexpected asset failures will be easier because you know exactly what needs to be done and when it needs to take place.”–Luke Perkerwicz, The Beginners’ Guide to Facility Asset Management, AkitaBox; Twitter:@Akitabox
47. Track and dispose of decommissioned assets. “However good asset management and maintenance planning is, there comes a time when an asset reaches the end of its useful life and should be disposed of. On a practical level, all assets disposed of must be recorded on the asset register/software, to ensure they are not included as part of the organization’s portfolio. An equipment disposal form will allow the asset ‘owner’ to explain how the asset was disposed of and identify any residual value.”–Gary Watkins, Effective Asset Management for Facilities Managers, Service Works; Twitter: @service_works
48. Do an asset assessment and document those conditions. “If you’re trying to get a handle of your documents, the first thing you should do is an asset assessment. Detail the condition of all the main equipment and systems, and document those conditions. No technology can help you unless you document what you have. After the assessment, you should create and begin a proactive maintenance program, as well as an equipment replacement plan—that should be a 3-year to 5-year plan. Even if the piece of equipment is 30 years old, you need to know when you need to replace it.”—7 Tips on Reducing Facilities Maintenance Costs and Risk, SKYSITE; Twitter:@skysiteproject
49. Consider a strategic asset management approach. “Strategic asset management integrates key relationships between planning and delivery activities. The framework that underpins the decision-making process of those activities is key, as it allows informed decisions and correlation between strategic goals and delivery outcomes. It also acts as the integration mechanism between a singular project and an organization’s wider portfolio of projects.”–Mark Jordan, An Asset Management Approach to Facilities Management, FM Magazine; Twitter:@FMmagazine_au
50. Maximize vertical space in your warehouse. “A warehouse has a set amount of square footage to utilize, making innovative, optimized layouts appealing for today’s warehouse managers who are faced with storing increased product volume in a static amount of space. In 2016, consider making better use of the vertical space in your facility, but don’t neglect layout optimization best practices. Maximize your use of vertical cubic footage by placing seasonal products or those that move less frequently in harder-to-reach vertical storage areas.”–Varsha Saha, 6 Tips for Better Warehouse Inventory Management in 2017, Camcode; Twitter: @Camcode
Our sales engineers are experts in automatic asset tracking, tagging and identification,a nd can answer all your questions. Get in touch now.
Lets Talk ›Enter your information and get a free checklist of the top questions to answer to plan a successful asset tagging project for any maintenance tracking or facility management system.