6 Best Practices for Warehouse Inventory Tracking
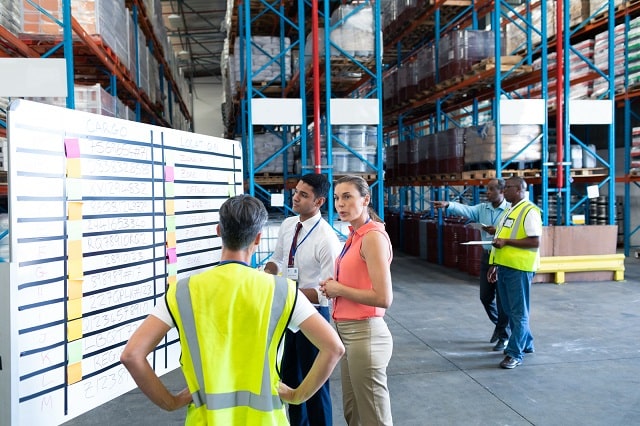
As warehouses strive for improved efficiency to meet market demands, there continues to be a need for better warehouse inventory tracking accuracy. To maintain such high standards, warehouse managers must constantly evaluate new improvements for their facilities. This requires substantial planning and a careful balance between employees, technology, and work processes.
With an endless supply of new ideas and technologies, the best path forward for most facilities is to choose technology solutions that integrate well into the existing environment.
The implementation of automated technologies in warehouses has dramatically changed the way that many operations process their inventory. A recent inventory management survey performed by Stitch Labs found that 62% of respondents identified human error as the leading cause of fulfillment issues.
Even though many operations have already implemented inventory management software, barcoding, and other technologies, there is still a lot of room for improvement. In this post, we’ll share a few excellent best practices for warehouse inventory tracking that continue to make a positive impact on businesses worldwide.
Cross-docking is used to transfer incoming inventory from supplier deliveries directly to outgoing shipments with minimal time spent in the warehouse. This is not an effective method for every operation but can dramatically decrease costs and improve efficiency in the right situations. It is especially useful for products with a short shelf life or those with specialized handling requirements, such as products that must be kept in cold storage. This is also an excellent method to use for bulk pallet deliveries that must be broken down and shipped to multiple destinations in a short time.
It is likely that some products within the warehouse will be delivered and shipped at a much higher rate than other inventory items. Taking time to review sales and order data to identify these items makes it easier to choose optimal storage locations. Placing the best-selling items in a location that is convenient for pickers and clearly labeling those locations with hanging warehouse signs, warehouse floor labels, and warehouse rack labels can reduce travel time within the warehouse and speed up fulfillment cycle times.
It takes some effort to create a truly efficient inventory management platform. Software and hardware must be optimized and combined with a fast network to reduce lag time and prevent connection errors. It is also important to invest in quality equipment and materials such as labels, tags, and signs. Performing routine checks of system performance can help prevent maintenance surprises, and regular training for employees will make sure they are taking advantage of all the system features. An inventory management platform is the primary information-sharing resource within most warehouses and should not be taken for granted.
Manual inventory record-keeping can contain significant errors, and it’s often hard to verify the data after the fact without an electronic history. When inventory can be tagged with barcodes and RFID tags, it is significantly easier to scan items in and out of the system. Using an electronic tagging process also reduces the need for handwritten entries and labels. Many companies choose to use a combination of fixed and mobile tags and labels for a complete warehouse solution that provides coverage for unique inventory types and specific use cases. It is also important to carefully plan the layout of your warehouse racks and barcode label placement to choose orientations that facilitate efficient scanning.
Modern inventory management systems can provide a high level of visibility for monitoring all activities within a warehouse facility. It is important to take advantage of the advanced metrics and reporting tools that most software solutions offer. Management can build custom reports and review key inventory metrics aligned with the unique performance goals of each location.
Another recommendation is to create a set schedule for reviewing metrics such as weekly, monthly, and quarterly so that important changes are not missed. Also, conduct necessary warehouse inventory audits.
Warehouses play an important role in the supply chain for B2B and B2C fulfillment. This gives warehouse management an opportunity to work closely with suppliers, distributors, and other business partners to better streamline operations and improve supply chain efficiency. Developing close relationships can help identify inefficiencies related to handoffs, deliveries, and inventory identification. With careful coordination, it is possible to reduce handling time and make deliveries faster and more convenient for customers.
Warehouse inventory must be carefully managed to reduce errors and maintain critical quality metrics. When warehouse management works closely with suppliers, integrators, and vendors, you can identify new improvements that can drastically improve operations.
Implementing inventory best practices can help any warehouse achieve new levels of performance and optimize its inventory management processes.
Our sales engineers are experts in automatic asset tracking, tagging and identification,a nd can answer all your questions. Get in touch now.
Lets Talk ›Enter your information and get a free checklist of the top questions to answer and tips to plan a successful asset tagging project for any warehouse management system implementation.