15 Essential Warehouse Operations Best Practices
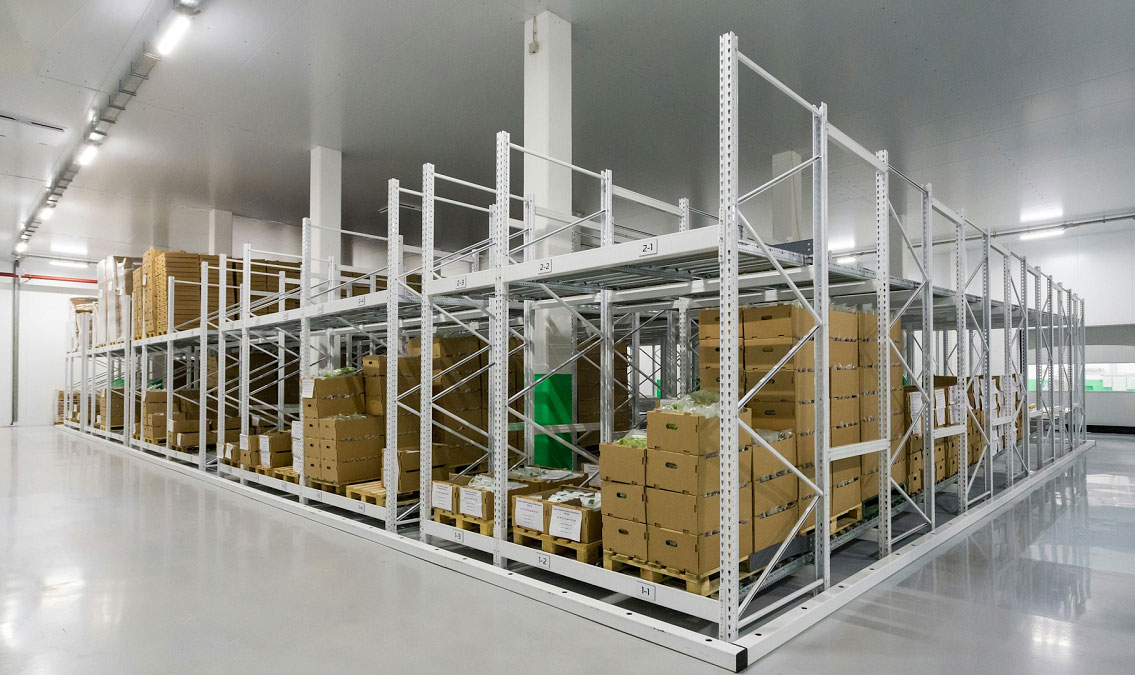
Labor, picking and packing procedures, storage, and unloading make up just a few of the essential processes that keep warehouses moving. These processes are already complex, but demanding customer expectations make warehouse optimization crucial for businesses.
Warehouse operations lie at the heart of an efficient supply chain, functioning as the engine that keeps products flowing seamlessly from suppliers to customers.
From inventory management and order fulfillment to automation and data analytics, effective warehouse practices boost efficiency, reduce costs, and elevate customer satisfaction. Success often comes down to minor but crucial adjustments to warehouse operations.
Learn about the key components of warehouse operations, its benefits, and how to create a streamlined, high-performing warehouse that unlocks greater productivity and growth.
Warehouse operations is an all-encompassing system that optimizes a warehouse’s processes and procedures to run as efficiently as possible. Operations includes workflows for receiving, storing, organizing, managing inventory, picking, packing, and shipping goods — all in one streamlined workflow across teams and locations.
The goal of warehouse operations is to optimize the day-to-day activities within a warehouse. In fact, warehouse operations can have a direct impact on a warehouse’s speed, accuracy, and expenses.
That’s why it’s so important for warehouse managers to optimize every facet of their facilities, whether in terms of labor, accuracy, or costs. Whether you’re managing a small fulfillment center or a sprawling distribution hub, a well-run warehouse operation is essential to achieving operational excellence and gaining a competitive edge.
Warehouse operations encompasses every process in a warehouse. It’s a broad discipline that includes components like:
Depending on your location and warehouse size, operations might also oversee safety standards, maintenance, cleaning and hygiene, and inspections or audits.
From productivity to lower costs, following warehouse operations best practices allows you to:
Optimized warehouse operations ensure timely deliveries, accurate orders, and efficient returns management, leading to a better overall customer experience and increased loyalty.
Efficient processes are the backbone of warehouse operations, but it’s impossible to manage all warehouse operations without a digital system. It’s no wonder why 82% of warehouses purchased technology in the last two years. These warehouse technologies streamline systems, improve accountability, and reduce costs:
Investing in the right technology can skyrocket warehouse performance. However, organizations need to ensure their investments are paying off, which is why tracking warehouse key performance indicators (KPIs) is crucial. These warehouse operations KPIs will highlight what you’re doing well and what needs to improve:
It’s normal for warehouse operations KPIs to fluctuate, especially if your business is seasonal. You should therefore leverage a warehouse management system to monitor KPIs over time, as historical context will help you better understand which trends are normal and when to make changes.
Bringing all of your facility’s warehouse processes into a single system is a good start, but warehouses require constant optimization. Follow these warehouse operations best practices to ensure your facility remains efficient and competitive over time.
Many warehouses work according to the 80/20 rule: 80% of their output comes from 20% of their inventory. In other words, most warehouse profit comes from turning over the same SKUs at a high volume. The more accessible these big sellers are, the less time your team will waste sifting through storage.
In fact, placing high-demand items in more accessible places can reduce picking time by as much as 50%.
Standardization and consistency ensure quality, regardless of your warehouse’s size. Instead of allowing employees or departments to follow their own checklists or processes, roll out the same procedures for everyone. WMS can help with this standardization by requiring employees to complete a digital checklist.
Standardization has a tremendous impact on warehouse operations. Following a batch-picking process can improve efficiency, while standardizing vendor processes also leads to a reduction in receiving time — not to mention fewer hassles for employees managing multiple vendors.
Larger warehouses tend to leverage automation more than smaller ones, but all warehouses can benefit from some form of automation. From automated picking systems and conveyor belts to robotics and AI-driven software, automation streamlines workflows and minimizes errors.
Pinpoint the most tedious or low-value tasks in your warehouse and identify which options are candidates for automation. This step saves time and reduces errors, allowing your employees to focus on more value-added tasks.
A well-trained staff is the backbone of an efficient warehouse. Many warehouses train new employees, but ongoing education is also necessary for existing employees. Certifications for specialties like forklift operation are legally mandated, but ongoing development for pickers, receivers, and administrators can also improve operations.
Whether it’s a lunch-and-learn or a mobile-friendly learning management system (LMS), create a digestible training program that keeps staff up-to-date on your processes and policies.
Moving your warehouse operations into a WMS will generate a bevy of data. This information is crucial, but warehouses shouldn’t gather data just for its own sake. Leverage data analytics to spot inefficiencies, monitor team performance, and make data-driven decisions.
Cycle counts ensure inventory accuracy. Plus, performing regular cycle counts reduces the need for more disruptive full physical counts, which can bring your warehouse to a grinding halt. Fortunately, software can do the heavy lifting for you. Your WMS should be able to continuously verify inventory data and quickly identify discrepancies or issues.
Communication is key to running an optimized warehouse, and facility labels are one of the best tools for keeping staff efficient, safe, and compliant. Rack labels, maps, and safety instructions are just a few ways management can communicate with employees on the warehouse floor.
From warehouse floor labels to specialized cold storage tags, Camcode’s labels keep your warehouse on the move. Our optimized labels and tags enhance picking, packing, and shipping processes while minimizing errors and improving warehouse productivity and accuracy.
Too much stock on hand ties up your funds in inventory, but running out of stock gives shoppers a poor experience. Strike a balance by following the principles of lean inventory management.
This approach minimizes excess stock while ensuring you have products available when needed. Going lean reduces carry costs, frees storage space, and improves cash flow.
Creating a warehouse layout is no small feat. However, a thoughtfully designed warehouse layout is the best way to maximize storage space and minimize movement during picking.
See if your WMS solution offers 3D warehouse layouts; this feature makes it a cinch to test multiple layouts before deciding on the most efficient option.
Reducing the number of times goods are handled throughout the warehouse process minimizes the risk of damage, lowers labor costs, and speeds up order fulfillment.
Streamlined workflows that eliminate unnecessary steps lead to greater operational efficiency, improved accuracy, and faster delivery times, ultimately enhancing customer satisfaction. Assess your current processes to see if you can eliminate any unnecessary touchpoints.
Lean inventory management is helpful, but it isn’t always a fit for seasonal businesses. Demand forecasting uses historical data and analytics to predict future demand. Most WMS solutions include this feature, which will help you optimize inventory levels in time for peak season.
Don’t require your team to return to a workstation to complete paperwork. Equip staff with mobile devices like handheld scanners and tablets so they can work from anywhere in the warehouse. This setup supports real-time updates and on-the-go task management, empowering employees to do more in less time.
More warehouses are moving away from static storage and embracing flexible solutions like modular shelves, collapsible racks, and adjustable bins. Flexible options allow you to adjust the warehouse layout if things change in the future.
Modular solutions often cost more upfront, but they future-proof your business in an increasingly uncertain market.
The average size of a warehouse is around 180,000 square feet. That requires an immense amount of energy, especially if you require temperature-controlled storage.
Implement energy-saving measures like:
See if your local government offers tax incentives for sustainable upgrades. Something as simple as changing out lightbulbs can have a tremendous impact on utility bills over time — and sustainable alternatives often pay for themselves in a few years.
Excessive packaging increases both costs and landfill waste. Switch to automated packing solutions, pre-sized packaging materials, and ergonomic workstations to simplify the packing process while trimming waste.
Warehouse operations keep busy warehouses moving. Efficient operations are critical to lower costs, improved customer satisfaction, and long-term profitability.
Regardless of your warehouse’s size or layout, optimizing your warehouse operations is a savvy decision that enables your business to adapt, scale, and provide superior service in a competitive landscape.
However, warehouse managers need the right tools for the job, and that’s where Camcode comes in. Our durable, long-lasting warehouse labels are perfect for everything from labeling racks to sharing safety information.
Camcode’s materials are rated to last up to 20 years in even the harshest environments, ensuring long-term readability and ROI. See the Camcode difference yourself: request your free warehouse label sample kit now.
The best warehouse operations best practices include:
Warehouse operations includes encompasses all essential functions that keep a warehouse moving, including:
There are several types of waste in warehouse operations that drain both time and money, including:
Our sales engineers are experts in automatic asset tracking, tagging and identification,a nd can answer all your questions. Get in touch now.
Lets Talk ›Enter your information and get a free checklist of the top questions to answer and tips to plan a successful asset tagging project for any warehouse management system implementation.