What is Material Handling? Examples, Types, Principles and More
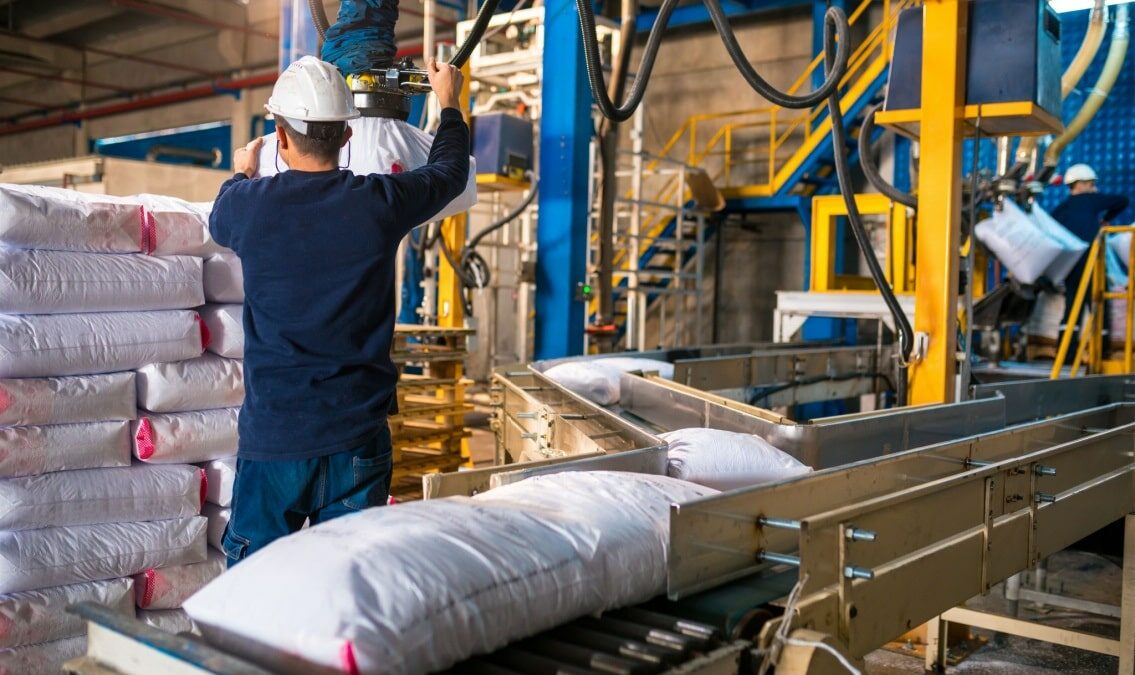
Logistics and supply chains play vital roles as products evolve from development to creation to shipment to delivery. Businesses need to monitor each phase of the process and improve it as much as possible in order to thrive. Material handling plays a key role in the process, providing the infrastructure needed to store and move items from place to place.
Material handling covers virtually any type of product, from raw materials to finished goods, and represents a large and growing business opportunity. In fact, the global material handling market is expected to grow at a compound annual growth rate (CAGR) of 8.3% and reach $127.26 billion in 2025.
The products are in various stages of development, from raw materials, to work in progress, to finished goods, as well as scrap material, rejected material, and packing material, in various sizes, shapes, and weights. Therefore, many devices, carts, conveyors, trucks, and ships, take part in the process.
As a result, the global material handling equipment market is also large and growing, rising from $38.2 billion in 2020 to $57.92 billion in 2027, a CAGR of 7.2%.
Because of the complexity of the interactions and the significant investments, corporations constantly try to improve how they handle materials. So, let’s take a closer look at what material handling entails and what improvements are possible. We’ll discuss:
Material handling is an umbrella term describing many activities, types of equipment, and locations that are part of business manufacturing and distribution processes. It is an integral, essential piece in any logistics or manufacturing project. Material handling involves the collection, storage, control, protection, and movement of products and material throughout manufacturing, warehousing, consumption, distribution, and disposal cycles.
Ensuring that materials are handled properly, efficiently, and efficiently is key to manufacturing, supply chain, and distribution success or failure. So, companies try to be systematic and scientific when creating, moving, packing, and storing materials.
Corporate material handling objectives include:
Material handling is a complex process, one that involves many moving parts. We will take a deeper look at its key elements.
A broad range of material handling equipment exists for use in these industrial tasks. The type and size of the material to be moved ultimately determines the most suitable type of equipment.
They fall into three broad categories:
Let’s take a look at some of the most common types of material handling equipment, but keep in mind that this is not an exhaustive list as many different types of equipment are used for moving and storing materials.
Goods are in a constant state of movement, starting at inception to delivery and use. In some cases, individuals power the actions, and in others, the equipment does.
The oldest moving method, manual material handling occurs when workers physically transport materials. The actions include lifting, lowering, filling, emptying, and carrying items, like goods, boxes, and containers. Given its physical nature, this work can be hazardous and exposes employees to activities where they could be injured.
Inadequately designed material handling systems lead to accidents on the shop floor, body pains, and other health risks. Workers may suffer from sprains and strains in their lower back, upper limbs, and shoulders. Accidents are possible and can be hazardous and even fatal, so safety is a top consideration during the process.
In some cases, individuals use devices, like carts and other devices that have wheels and handlebars, to transport materials. Here, the mechanical systems perform the bulk of the action, but humans control the interaction.
Forklifts, also called Industrial trucks or lift trucks, cover a broad category of equipment designed to transport materials within a factory or warehouse. Equipment in this category is operated by a human worker but mechanically picks up and places materials, which eliminates the manual lifting and transporting work. Lift trucks also come in a range of sizes and configurations.
For instance, an order picker lifts operators high off of the ground and allows them to get to hard-to-reach materials.
Lift trucks have been around for many years, but they remain a popular material handling solution. According to Modern Materials Handling, 63% of companies in a 2022 survey reported plans to purchase additional lift trucks within the next 12-24 months.
Tools such as warehouse floor label kits and warehouse signs, such as retro-reflective warehouse barcode labels, enable forklift operators to easily navigate the warehouse and find the correct locations quickly, without wasting time or contributing to warehouse aisle clutter.
Automated material handling equipment replaces manual handling of materials. This equipment offers several benefits:
These systems include:
Conveyors are popular material handling solutions in many facilities. They effectively move goods quickly while minimizing the risk of damaging materials.
Autonomous mobile robots have advanced navigation technology, so they map out a facility and determine their path as they move. Their sensors allow them to identify obstacles and move around them.
Automated guided vehicles (AGVs) are driverless vehicles used to transport materials within a facility and offer a number of cost-saving benefits and other advantages. AGVs follow set paths using various navigation technologies. Furthermore, they have collision warning systems, so they do not crash.
An automated storage and retrieval system (AS/RS) often replaces the traditional pick and pack procedures followed in warehouses. They automatically store and retrieve materials.
Many of these systems have modern designs. Electric automated material handling solutions are fueling the growth of the global market due to a push for more environmentally friendly products and greater fuel efficiency. There are also government initiatives that are fueling growth in this area.
However, despite the many benefits of AS/RS, the adoption of such systems faces several roadblocks. For instance, implementing automated storage and retrieval systems can be costly. Humans adapt to many different work demands.
Machines are programmed to complete one task. But the ongoing improvements in machine programming, sensing, and robotics continually close the gap and provide higher levels of automation and spur additional adoption.
Storage and handling products hold materials when they are not being used or being moved. This category includes storage solutions such as racking, pallets, and shelves that make it possible to store materials in an organized manner.
Material often sits when they are about to enter the production cycle or waiting for transportation. This equipment includes racks, shelves, stacking frames, and mezzanines.
Many types of racks are used in facilities, including sliding racks, pallet racks, push-back racks and drive-through or drive-in racks. The racks are designed to house materials, keep them accessible, and save floor space.
Racks are typically equipped with warehouse rack labels to aid warehouse workers in finding the correct storage locations for material retrieval and putaway.
Shelves, bins, containers, and drawers are common and basic types of storage items. Drawers and bins are placed within the shelving and typically house small materials. Container, pallet, tote, and tray barcode labels make material identification easy for material handling workers.
As the name suggests, these items are placed on top of each other like blocks. Their main advantage is they allow fragile or crushable material stored in pallets to be stacked on top of each other.
A mezzanine is an indoor platform raised above the floor, similar to a second level. Some of the main types of mezzanines include building supported, modular, movable, rack supported, and free standing.
A major benefit to these pieces of equipment is that they allow a company to be more efficient. Efficiency increases if a company puts thought into their storage design. A warehouse’s production system relies on such equipment to provide staff with the ability to access and transport materials quickly.
Warehouses constantly strive to improve efficiency and meet every changing market demands. Companies have a strong need for greater inventory accuracy.
To maintain high standards, warehouse managers must constantly evaluate new improvements for their facilities. This process requires substantial planning and a careful balance among employees, technology, and work processes.
With an endless supply of new ideas and technologies, the best path forward for most facilities is to choose technology solutions that integrate easily into the existing environment and offer them room for future growth.
Businesses constantly strive to improve their material handling processes because they are so vital to their operations. Inventory management, safety, and automation are three areas of emphasis recently.
Companies need to monitor the flow of materials through the supply chain and be able to accurately track them as they evolve, a complex undertaking and becoming more so every day. Traditionally, tracking consisted of manual, paper processes, but manual methods have many limitations.
For instance, a recent inventory management survey performed by Stitch Labs found that 62% of companies identified human error as the leading cause of fulfillment issues.
Computers offer companies the ability to offload manual, repetitive tasks to intelligent machines, so they are playing a bigger role in the process. In fact, automated technologies are changing how materials move in warehouses. Increasingly, businesses rely on solutions like inventory management software and barcoding to help track items.
However, it takes effort to create a truly efficient inventory management platform. Software and hardware must be optimized and combined with a fast network to reduce lag time and prevent connection errors. Investing in quality equipment and materials such as labels, tags, and signs is also important.
Performing routine system performance checks can help prevent maintenance surprises, and regular training for employees will ensure they are taking advantage of all the system features. An inventory management platform is the primary information-sharing resource within most warehouses and should not be taken for granted.
With such tools, they can better monitor the flow of goods through the supply chain.
According to OSHA, the fatal injury rate for warehousing is “higher than the national average for all industries.” Because of this fact, agencies like OSHA pay extra close attention to common warehouse operations pitfalls, including improper licensing/training procedures, faulty infrastructure, poor recordkeeping, facility maintenance issues, and more.
Establishing and following safety rules ensures that the health of the associates and the business remain secured.
There’s a growing trend towards adoption of automated material handling solutions in the global market. Companies are implementing such solutions to improve the material handling process.
The aim of implementing automated material handling and storage solutions is to improve efficiency and provide a cost-effective solution for material handling needs in warehouses and facilities.
The COVID-19 pandemic disrupted the global material handling equipment market, forcing companies to restructure their plans to cope with the pandemic. Demand grew for automated storage and retrieval systems in areas like e-commerce, due to the onset of COVID-19.
A rising number of startup companies are developing robotic solutions for warehouse automation, which should spur further adoption.
Strong material handling procedures offer companies many potential business benefits.
One common issue companies face is the lack of proper storage systems and the presence of equipment that mishandles materials. These missteps lead to products being damaged or even wasted during storage and transportation, leading to increased costs as well as unhappy clients.
So, companies with strong procedures have higher yields, which lowers expenses and improves profitability.
Lowering material handling costs is a primary goal for every company using material handling equipment. The production process relies heavily on procuring, moving, and storing materials.
These aspects of the action can cost a company a significant amount of money, especially when their material handling systems are inefficient. If the material handling solutions cannot handle the flow of materials efficiently, stoppages occur, leading to new costs, lower profitability, and a growing number of inefficiencies.
Often, materials enter a facility in a raw form and exit as completed products or goods. If a facility has multiple steps in its production process, the material needs to flow smoothly. Not having the proper warehouse equipment leads to slowdowns and production stoppages.
For instance, materials handled poorly or with an inadequate material handling system can lead to product damage or delay the transport of materials to where they’re needed.
Material handling is a critical component of modern business operations, playing a pivotal role in the efficiency and effectiveness of manufacturing, warehousing, and distribution processes. As industries continue to evolve and face new challenges, the importance of robust material handling systems becomes increasingly apparent.
The growing trend towards automation, driven by advancements in technology and the need for greater efficiency, is reshaping the landscape of material handling. From automated guided vehicles to sophisticated inventory management software, businesses are leveraging these innovations to streamline operations, reduce costs, and improve overall productivity.
Looking ahead, the future of material handling promises even greater integration of smart technologies, data analytics, and sustainable practices. As companies strive to meet the demands of a rapidly changing market and increasingly complex supply chains, they will need to invest in flexible, scalable material handling solutions that can adapt to evolving needs.
The ongoing focus on safety, efficiency, and sustainability will continue to drive innovation in this field, leading to the development of more advanced equipment and processes. Ultimately, businesses that prioritize effective material handling strategies will be better positioned to thrive in an increasingly competitive global marketplace, delivering improved customer satisfaction and maintaining a strong competitive edge.
Examples of material handling include:
The three main types of material handling are:
The main function of material handling is to ensure the safe, efficient, and cost-effective movement, storage, control, and protection of materials throughout the manufacturing, warehousing, distribution, and disposal processes.
It aims to optimize workflow, reduce costs, improve productivity, enhance safety, and streamline operations across the supply chain
Our sales engineers are experts in automatic asset tracking, tagging and identification,a nd can answer all your questions. Get in touch now.
Lets Talk ›Enter your information and get a free checklist of the top questions to answer to plan a successful asset tagging project for any maintenance tracking or facility management system.