The 6 Types of Warehouse Storage Systems
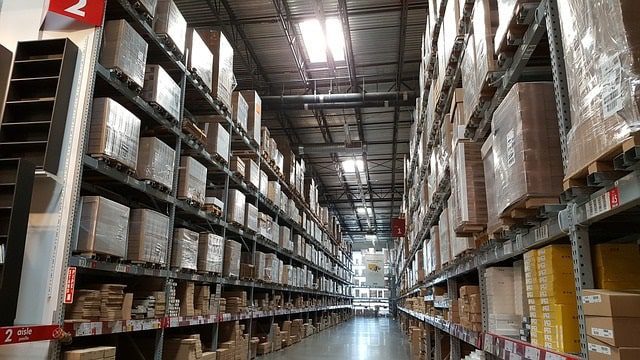
One of the first steps that must be taken in order to craft a warehouse that’s functional and organized is to select your storage system (or systems). Naturally, this is not a choice that should be taken lightly; warehouse storage systems are a major capital investment that, depending on the design and the way they fit into your warehouse floor plan and processes, can either help or hurt your throughput.
Because there are several different categories of warehouse storage systems on the market today, it’s key to get acquainted with the options before being sold on one that might not complement your layout or support your need for flexibility.
As the name suggests, static shelves are storage mechanisms that are designed to stay in one place. For the most part, they are meant to hold inventory that is fairly lightweight (a few hundred pounds per shelf). It’s commonly used for storing inventory that needs continuous replenishment.
Because they’re not compatible with forklifts, static shelving is generally used with inventory that must be manually picked, placed, and/or organized. For your larger inventory, invest in a wide-span shelving system, which can hold more weight and can be used in higher-elevation configurations.
Similar to static shelving, mobile shelving is a completely adjustable solution that is meant to hold your manually-picked items, but the difference here is that many of these systems are designed to hold more items in less space.
With mobile shelving, shelves or cabinets are mounted on carriage and rail systems, eliminating fixed aisles and increasing productivity by making inventory more accessible, even when space is tight.
Mobile shelving designs typically include level tracks that can either be manual or mechanized. Some even come equipped with locking systems to control access to inventory.
For the busiest and largest warehouses, pallet racking systems are usually treated as the centerpiece of the operation.
Typically, pallet racking systems are made out of wood, metal, or plastic and hold inventory that is received in large boxes. Depending on the height, the boxes are placed on the pallet racking system with the help of a forklift or an automated mechanism.
There are several different sub-categories of pallet racking systems, including:
Most often, warehouses will choose systems based on weight limits, flexibility, and whether or not the system demands a change in infrastructure.
Learn more about warehouse racking in our article on “What is Warehouse Racking?”
A great choice for large stocks of items that have small unit sizes, multi-tier racking is a system that is designed to capitalize on vertical space. Because no warehouse is one-size-fits-all, many multi-tier racking options are flexible, with the ability to add or remove tiers depending on your current needs.
Mostly, multi-tier racking concerns relatively lightweight items that are picked and organized manually.
To get the most out of this warehouse storage system, organize each tier strategically and pack items as densely as possible, while at the same time paying attention to weight limits and ceiling-to-rack height compliance guidelines.
If you have the budget and your strategic warehouse layout allows for it, mezzanine flooring is an effective and space-saving storage option. Essentially, mezzanine flooring is a second (or third, or fourth) floor that is constructed above the main warehouse floor.
Because of the intrusive nature of the build, this is likely one of the more expensive options that a warehouse can choose, but it also has the most potential for customized features, such as lighting, lift-systems, and conveyors.
While mezzanine flooring is one of the more high-tech options, wire partitions are on the other end of the spectrum. Wire partitions are, effectively, strategically-placed wire cages that are meant to be installed and torn down quickly and easily.
Often, the inventory that is housed within wire partitions are the items that may need special security. Some warehouses are even known to use wire partitions to construct makeshift, temporary offices for managers who work on the floor.
As you can see, there is a wide range of warehouse storage systems available and, as we move into the future, warehouse storage systems are only getting more lightweight, affordable, and technologically-advanced.
As mentioned, don’t be sold on a system that doesn’t fit your needs; instead, select one that possesses enough flexibility to support your operation as it flourishes and grows.
Our sales engineers are experts in automatic asset tracking, tagging and identification,a nd can answer all your questions. Get in touch now.
Lets Talk ›Enter your information and get a free checklist of the top questions to answer and tips to plan a successful asset tagging project for any warehouse management system implementation.