What is a Barcode Inventory System? How Does It Work
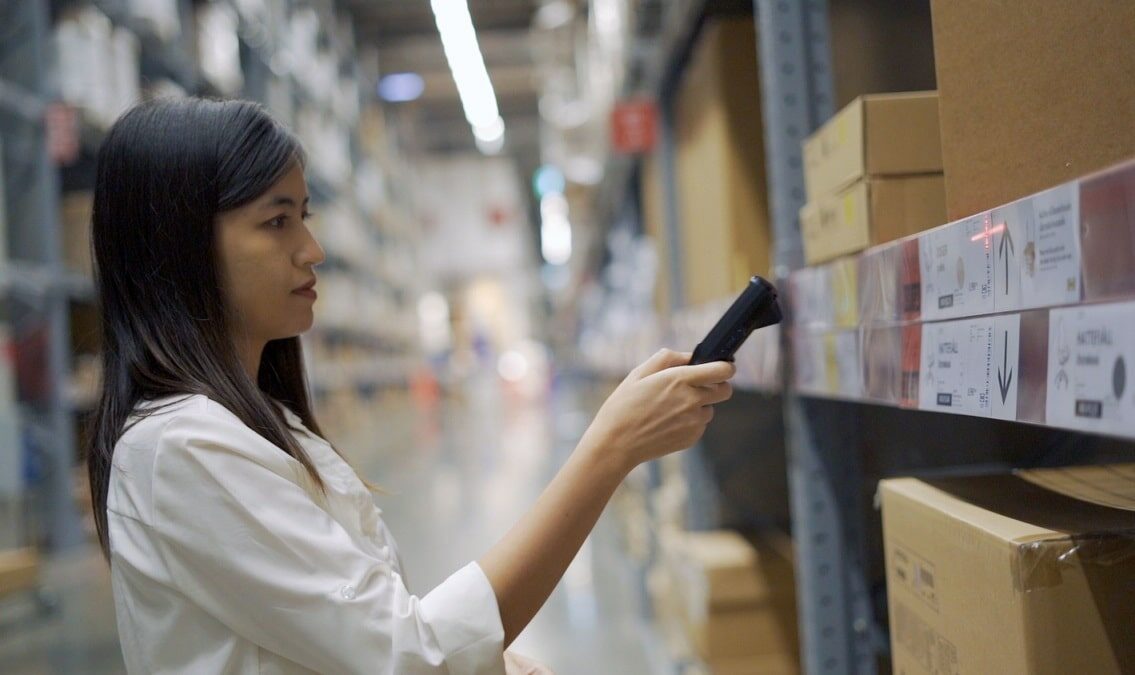
Enterprises collect, purchase, utilize, move, and distribute many products, goods, and equipment. Tracking these items has been an ongoing challenge, but technology has been evolving to ease the work. Barcode labels, scanners, and inventory management systems help organizations better track their physical assets.
Businesses want to create, market, and sell products. Managing inventory as items move from inception to delivery is a vital part of the operation. In this guide, we’ll discuss everything you need to know about a barcode inventory system.
A barcode inventory system is a digital method of tracking and managing inventory that uses barcodes, hardware, and software to automate inventory control and improve accuracy, efficiency, and productivity. These are the key components and functions of an effective barcode inventory system.
The system works by encoding data into a series of vertical bars and spaces that represent numbers or characters. When scanned, this information is translated into usable data for inventory management.
Benefits of using a barcode inventory system include:
A barcode inventory system can be customized for various industries and business needs, from retail stores to warehouses and manufacturing facilities. It allows businesses to automate many manual inventory control tasks, leading to increased productivity and more accurate stock management.
Retailers, manufacturers, warehouses, distributors, and logistics companies find that managing these systems is core to their operations. But just about every business finds itself keeping track of either the products it sells to others or equipment and other goods that are vital to their operations:
So, it is not just retailers, warehouses, manufacturers, and distributors that have to maintain precise inventory counts and need an effective barcode inventory system. Every enterprise has materials it must track to a degree.
Monitoring inventory is important because doing it well helps organizations in many ways, yet seldom do companies excel in this area. This work can be overlooked because management focuses on the core business, not internal logistics.
Also, businesses often find the process consuming and frustrating for many reasons. Traditionally, organizations managed their inventory manually. They entered information via pencil and paper or into an Excel spreadsheet, and some may have created paper labels that were printed on-site.
Then, the business conducted regular inventory counts to ensure that paper-and-pencil tracking and spreadsheet methods were somewhat accurate. The process was time-consuming and presented accurate information for only a short period (if at all), basically immediately after a count was completed.
In addition, humans sometimes make mistakes, especially when counting and tracking hundreds, thousands, and tens of thousands of products. As a result, inventory management quickly became a major productivity drain. Employees spent lots of time on it but did not create impeccable records. Troubleshooting to discover the root cause of a discrepancy sometimes required repeating the entire process.
Tracking products has always been complex and become even more so as specialists emerged in areas like supply chain management, but as different companies throughout the supply chain use different computer systems, there remained a lack of visibility.
In addition, the movement of goods has become more dispersed. Small and large companies can sell their wares locally, in the immediate area, across the country, and even worldwide. As they expand to new markets, they must ensure that they follow the local guidelines.
As a result, storage space is often misused. A company facility or warehouse is filled with many items: display racks, banners, stands, literature, supplies, store fixtures, and goods in various stages of assembly. They are often scattered across the storage facilities rather than being efficiently housed.
One asset management mistake wreaks havoc on the supply chain, manufacturing process, and delivery. Whenever problems arise, work is delayed, and sometimes everything has to come to a halt because the team can’t move forward when each stage in the process depends on the prior step’s completion.
Other ripple effects arise. Teams are held up on one project, delaying the completion or delivery of products to other customers. Companies need to reorder the necessary supplies. They often rush to catch up and make other mistakes, ultimately lowering the quality and effectiveness of their work. They finish one project late and start the next one behind schedule too. Frustration and stress build, creating a tense work environment.
Inventory counts are inaccurate. If a customer’s order is delayed, complaints to the customer service reps increase, and customers turn to competitors. Too much inventory ties up storage space – and capital. In essence, the inefficiencies trickle down through the supply chain and negatively impact partners, retailers, service providers, consumers, and eventually stakeholders.
But inventory management is becoming much simpler because of advances in technology. Solutions like barcode labels and asset tags and inventory control tags help companies gain more insight and control over their goods.
A barcode label is a visual representation of an item. Typically, the code features numbers, letters, and symbols, with characters encoded in black and white.
A barcode inventory system assigns a distinct identifier to each product or piece of equipment. As a result, a company can associate several data points to the number, including the supplier, product dimensions, weight, and even variable data, such as how many are in stock.
The identifying number is stored in a database, and the system uses scanners to document and track where the item goes, whether it’s been used, and other data. Through the years, a number of standards evolved that established how the codes were constructed and what they mean so the scanners understand what they are looking at and what they see.
Technology has improved and become more intelligent. Nowadays, corporations have more information than ever before. Along with basic asset identification information comes its history, including maintenance and repairs, the original vendor, its current location, and where it is scheduled to be.
Another plus is barcode labels have adapted to real-world conditions. They now account for variables, such as exposure to harsh weather conditions, caustics, and chemicals. Consequently, different types of barcode labels have emerged for various use cases:
In addition to the many choices, vendors collaborate with customers to create barcode labels for their unique applications. For instance, Camcode worked with Displays2go to develop customized polyester rack labels for their warehouse. In addition to standard rack labels, the two devised a solution for easy scanning of high and low racks. Rather than have employees bend down to reach very low racks or stretch to reach higher ones, they deployed a double label system.
In this case, a rack label had a certain color and an arrow that points down for a lower level and a different color with an arrow that points up for the higher levels. The labeling made it easy for employees to scan and led to fewer mistakes because the different colors clearly identified the various levels.
Marking equipment with barcodes and deploying scanners and inventory management software is a good business decision. There are dozens of benefits to implementing a comprehensive barcode inventory system to streamline asset tracking and bolster inventory control:
Ultimately, the goal of these technologies is to gain more visibility into company workflows. Barcode tags improve inventory management by boosting inventory tracking and accuracy.
Nowadays, companies collect more information than ever before. By itself, data collection is of little value. But once inventory data is stored in a central database, companies gain a practically endless number of possibilities for leveraging it.
For example, exporting data to a spreadsheet for sophisticated analysis in another program is done easily. Individuals can sort assets by category and analyze expected versus actual lifespan. They can use that information to determine which vendor’s equipment is superior. Financial projections become more accurate because they are based on which assets require replacing or significant maintenance over a specific period. In sum, the abundance of data at their fingertips drives better decision-making.
Inventory management is a major pain point for many organizations, whose outdated processes and manual documentation slow down the process. Barcode inventory tags make it possible to automate many inventory processes that otherwise are time-consuming and inefficient. Automated processes relieve employees of often repetitive, mundane work, saving significant time that they can dedicate to more value-added activities. Automation also reduces human error in documentation.
The new capabilities transform production management from reactive to proactive. Traditionally, companies managed from behind: relying on historic information to understand performance and make changes. Now, they manage proactively, having the information in real time, so they adjust on the fly.
These new solutions will not eliminate the need for periodic inventory counts and audits, but they do make the process simpler and less frequent. Without inventory labels, companies begin the process blind: they have little to no insight into what they are using. With it, they do not have to spend as much time counting resources manually. Instead, they quickly scan their inventory and check its accuracy.
Businesses must keep records for various compliance regulations, like financial and tax reporting. They must know how much inventory they had on hand at different times. Barcodes enhance visibility, reducing the time necessary to calculate these important details.
Too much inventory leads to waste and increases overhead costs for long-term storage. Labels help you readily track data points around your inventory and more accurately predict a variety of variables, such as how much inventory is needed for the next few weeks, the next month, or the upcoming quarter.
Better asset visibility provides companies with more accurate, more timely pictures of their material flow. They can add more items if needed and find ways to mitigate the impact of any delays. The visibility enables them to better schedule personnel and maximize the returns on their labor costs.
Advanced data analytics provides them with accurate projections, so they lower system costs. In essence, these capabilities boost the bottom line by making more efficient use of company resources.
Because of the many benefits, the barcode Scanner Market is growing: it was valued at $ 6.34 Billion in 2020 and is expected to grow at a CAGR (Compound Annual Growth Rate) of 7.5% through 2021 to 2027, reaching nearly $ 10.52 Billion.
Every company needs a barcode inventory system. What features should they require?
Barcode systems provide information to a number of other applications: manufacturing systems, warehouse management systems, and facility management solutions. The system must have a broad suite of open Application Programming Interfaces (APIs) that connect to leading solutions.
The barcode system must be flexible. The solution should support angle scanning that can be read at distances of a few dozen feet, such as retro-reflective warehouse barcode labels.
Implementing a barcode inventory system can revolutionize the way businesses manage their stock, streamline operations, and improve overall efficiency. This modern approach to inventory management leverages technology to automate tracking, reduce human error, and provide real-time insights into stock levels and movement.
Here’s a handy table to walk you through the process of implementing a barcode inventory system.
Step | Action | Description |
---|---|---|
1 | Choose barcode type | Select UPC, QR codes, or industry-specific barcodes |
2 | Select hardware | Invest in barcode printers, scanners, and mobile devices |
3 | Implement software | Choose inventory management software compatible with barcodes and existing systems |
4 | Generate barcodes | Create unique barcodes for each product with relevant information |
5 | Label inventory | Print and apply barcode labels consistently to all products |
6 | Set up database | Enter product information into software, linking to corresponding barcodes |
7 | Establish procedures | Define processes for scanning, updating stock, and conducting inventory counts |
8 | Train staff | Educate employees on system use, scanning techniques, and data entry |
9 | Test and refine | Conduct a trial run, identify issues, and make necessary adjustments |
10 | Integrate processes | Connect barcode system with order fulfillment, purchasing, and financial reporting |
By following these steps, you can successfully implement a barcode inventory system that improves accuracy, efficiency, and productivity in your business operations.
Businesses rely on a wide variety of equipment in order to run smoothly. The range includes items used internally as well as products they deliver to customers.
Tracking items as they move through various cycles has been challenging, but new barcode solutions streamline the process. They provide companies with greater visibility into their business processes, reduce supply chain waste, and improve profit margins, making the business more formidable.
Companies often lack the expertise needed to deploy these solutions and need help from third-party experts. Camcode offers comprehensive inventory management services from an experienced, industry-leading team. You’ll get an expert analysis of your applications and requirements to help you develop a completely customized asset tracking solution for better inventory management.
Get in touch with Camcode today to learn more.
A barcode system functions as a comprehensive tool for automating data collection and enhancing inventory management. It enables quick and accurate data entry, real-time inventory tracking, and efficient asset management.
By streamlining processes like purchasing and order fulfillment, barcode systems significantly improve operational efficiency and reduce human error. They provide up-to-the-minute information on stock levels, facilitate better decision-making through data analysis, and integrate seamlessly with other business systems.
This technology not only enhances accuracy and reduces costs but also improves customer service by ensuring quick access to precise inventory information. Across various industries, barcode systems play a crucial role in boosting productivity and maintaining competitive edge in today’s fast-paced business environment.
The main advantages of using barcodes in inventory management are:
Enhanced customer satisfaction: By reducing errors and improving efficiency, businesses can fulfill orders more accurately and quickly, leading to happier customer
Yes, there are several free apps available for scanning barcodes and managing inventory, such as:
The best barcode type depends on your specific needs, but common options include:
Choose based on the amount of data you need to store, scanning equipment compatibility, and industry standards.
Our sales engineers are experts in automatic asset tracking, tagging and identification,a nd can answer all your questions. Get in touch now.
Lets Talk ›Enter your information and get a free checklist of the top questions to answer and tips to plan a successful asset tagging project for any asset management or tracking system implementation.