FIFO vs LIFO: Differences, Advantages and Disadvantages, Applications, and More
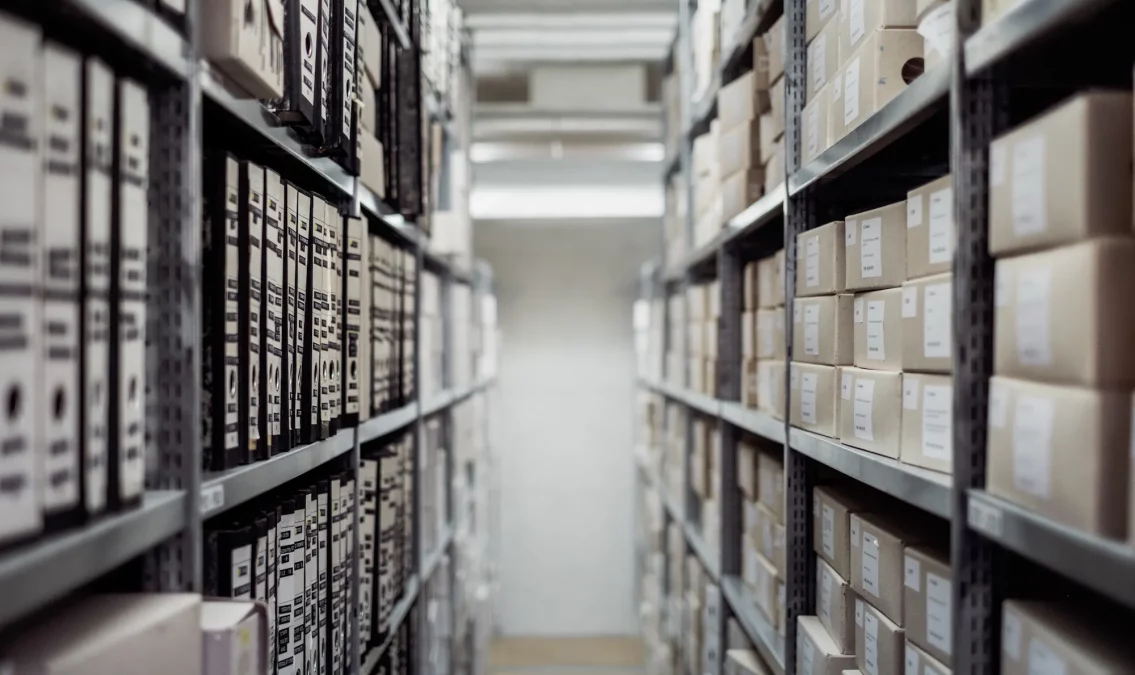
First In, First Out (FIFO) and Last In, First Out (LIFO) are two common inventory management methodologies. The two models are based on opposite methods, each with a few distinct advantages in certain industries and verticals.
So let’s dive into the key differences between FIFO vs LIFO.
First in, first out (FIFO) is an inventory management system that operates by using the first, or oldest, stock first and saving the most recently produced or received inventory until all other inventory has been used or shipped. The goal of FIFO is to ensure the oldest stock is used first to reduce costs associated with obsolete inventory. This inventory system also rotates stock and is used in a wide range of industries.
Some organizations combine FIFO with other inventory management models and inventory systems as part of an economic order quantity (EOQ) model to avoid stock-outs of products.
Last in, first out (LIFO) is an inventory management system used most often for non-perishable products or those with a low turnover rate, since it is the process used to sell or ship products manufactured or stored later first and those that are manufactured or acquired early last. LIFO is the opposite of FIFO, and it is useful in valuing inventory on hand at the end of a period as well as the cost of goods sold during the same period.
When it comes to the debate of whether to use FIFO vs LIFO, one of the most significant advantages of using first in, first out in your warehouse is that it solves your company’s problems with the fluctuating costs of inventory. Under FIFO, your inventory bottom line is more likely to approximate the current market value. Your company will find that your assumed flow of costs corresponds with the normal physical flow of goods and that your first deducted inventory costs are the oldest unit costs.
Other advantages of using the FIFO method include its ease of application and its acknowledgement of the fact that companies cannot manipulate income by choosing which unit to ship.
Because prices have risen nearly constantly for years, the FIFO method can make it appear as though your company has a greater cash flow than it does. Thus, the disadvantages of FIFO are the ways in which it makes it look, at least on paper, that companies are making a larger profit than they are. This larger-than-life profit, of course, leads to a heavier tax burden if FIFO is used during periods of inflation. Higher taxes from FIFO valuation diminish a company’s cash flows and growth opportunities.
Another disadvantage of using FIFO is that it typically fails to show an accurate picture of costs when material prices increase rapidly. Accounts using costs from months or years previous do not help managers spot cost issues quickly. Companies also miss out on the tax advantages of LIFO.
Companies that use the last in, first out method gain a tax advantage because the method assumes the most recently acquired inventory is what is sold. As inflation continues to rise, LIFO produces a higher cost of goods sold and a lower balance of leftover inventory. The higher cost of goods sold results in a smaller tax liability because of the lower net income due to LIFO.
LIFO is more difficult to maintain than FIFO because it can result in older inventory never being shipped or sold. LIFO also results in more complex records and accounting practices because the unsold inventory costs do not leave the accounting system. LIFO is not recommended if you have perishable products, since they may expire on the shelf before they are sold or shipped. LIFO also is not an ideal method for businesses expanding globally because a number of international accounting standards do not allow LIFO valuation.
The choice between FIFO vs LIFO inventory management methods is crucial for businesses and depends on various factors including industry type, economic conditions, and financial goals.
FIFO, which uses the oldest stock first, provides a more accurate representation of current inventory value and is ideal for perishable goods. It also aligns with the natural flow of most inventories. However, during inflationary periods, FIFO can lead to higher reported profits and consequently higher taxes.
On the other hand, LIFO, which uses the newest stock first, offers tax advantages during inflation by reporting higher costs of goods sold and lower profits. However, it may not accurately reflect the physical flow of inventory and is less suitable for perishable items.
Ultimately, companies must carefully consider their specific circumstances, regulatory requirements, and long-term objectives when deciding between FIFO and LIFO. It’s also worth noting that some businesses may benefit from a combination of both methods or other inventory valuation techniques to optimize their operations and financial reporting
Our sales engineers are experts in automatic asset tracking, tagging and identification,a nd can answer all your questions. Get in touch now.
Lets Talk ›Enter your information and get a free checklist of the top questions to answer and tips to plan a successful asset tagging project for any asset management or tracking system implementation.