What is Warehouse Operations? How Does It Work?
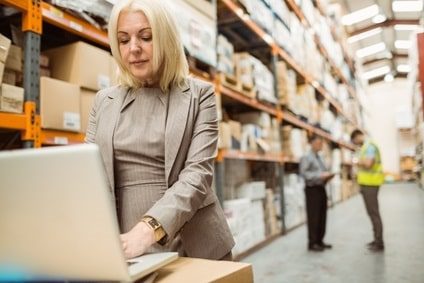
When it comes to warehouse operations, we are officially living in the golden age of speedy fulfillment. This means that the world’s warehouses have their work cut out for them.
According to data gathered by Statista, the number of warehouses operating in the United States has been on a steady incline in the past decade, peaking at nearly 18,000 facilities in 2017.
As competition increases and consumer expectations run into uncharted territories, it’s becoming more and more important for retailers, suppliers, and distribution managers to learn the ins and outs of the ever-evolving field of high-tech modern warehousing.
But, just because recent automated technologies have changed the landscape of the overarching customer experience doesn’t mean that those new to the field can skip out on learning the fundamentals. Developing a keen awareness of warehouse operations should be the first step for any enterprise entering today’s fulfillment race.
Let’s take a quick dive into the meaning, challenges, and best practices associated with warehouse operations.
Rick Stinchcomb of the University of Oklahoma Press defines warehouse operations as such: “The goal of warehouse operations is to satisfy customers’ needs and requirements while utilizing space, equipment, and labor effectively. The goods must be accessible and protected. Meeting this goal requires constant planning and ongoing change.”
Breaking it down, warehouse operations covers a number of important areas, from the receiving, organization, fulfillment, and distribution processes. These areas include:
Of course, the aforementioned points represent just a fraction of what many modern warehouse operations managers face. That said, they constitute the fundamentals of warehousing, elements that serve as the building blocks for all warehouses, big and small.
While many factors come into play when considering warehouse operations, ostensibly, today’s key factor concerns customer experience. Since the rise of Amazon and its nearly autonomous fulfillment centers, consumers have grown accustomed to two-day, one-day, or sometimes even hourly shipping times.
These expectations force warehouse operations to keep customers’ needs at the forefront. Operations can achieve this by investing in a software system, like a WMS, WES, or CRM that give all members of the supply chain, including customers, a picture of the retailer’s inventory levels.
The operations manager, along with planners and other management, can use the purchase data to organize the warehouse floor in such a way that the most popular or quick-moving SKUs are strategically placed. Once the inventory and infrastructure plans have been inked, management must also consider factors like new technology integration, picking routes, safety, personnel management, and more.
Attention must also be paid to the organization’s fleet, whether it be internal or otherwise. It is the job of the warehouse operations personnel to ensure that all inventory is picked, packed, and ready to be loaded for shipment in the most efficient way possible.
Maintaining a reliable, safe, and modern warehouse can be possible for operations of all sizes and budgets, provided that the basic best practices are followed. These include:
In today’s fast-paced and interconnected business environment, seamless integration and connectivity between warehouse operations and other systems are crucial for achieving end-to-end visibility and optimizing the entire supply chain.
Warehouse operations must be tightly integrated with systems such as:
ERP systems serve as the central hub for managing business processes, including inventory management, order processing, and financial operations. Integrating warehouse operations with ERP systems ensures real-time data exchange, enabling accurate inventory tracking, efficient order fulfillment, and streamlined financial reporting.
TMS solutions optimize transportation planning, execution, and freight management. By integrating warehouse operations with TMS, businesses can coordinate inbound and outbound logistics, optimize transportation routes, and reduce transportation costs while improving delivery times.
For businesses with an online presence, integrating warehouse operations with eCommerce platforms is essential for efficient order processing, inventory management, and timely order fulfillment. This integration enables real-time updates on product availability, order status, and shipping information, enhancing the overall customer experience.
The benefits of seamless integration and connectivity in warehouse operations include:
As businesses strive for agility and responsiveness in today’s dynamic market, the integration of warehouse operations with other systems becomes a critical enabler for achieving operational excellence and maintaining a competitive edge.
Effective warehouse operations rely on continuous monitoring, measurement, and optimization of key performance metrics. By leveraging data-driven insights and analytics, businesses can identify areas for improvement, make informed decisions, and drive operational excellence.
Some of the critical performance metrics in warehouse operations include:
Order Accuracy and Fulfillment Rates: Measure the percentage of orders that are picked, packed, and shipped correctly and on time. These metrics directly impact customer satisfaction and loyalty, making them crucial for businesses focused on delivering exceptional service.
Inventory Accuracy and Cycle Counting: Inventory accuracy is essential for maintaining optimal stock levels, reducing stockouts or overstocking, and ensuring efficient order fulfillment. Cycle counting, a process of regularly counting and verifying a subset of inventory, helps maintain inventory accuracy and identify discrepancies.
Labor Productivity and Utilization: Labor is a significant cost factor in warehouse operations. Monitoring labor productivity and utilization metrics, such as orders processed per hour or lines picked per hour, helps optimize workforce allocation, identify training needs, and implement process improvements.
Space Utilization and Slotting Optimization: Efficient space utilization and slotting optimization ensure optimal use of available warehouse space, reducing wasted space and improving picking and putaway efficiency. Metrics like cubic space utilization and travel distance can guide layout optimization and slotting strategies.
Transportation and Logistics Costs: Monitoring transportation and logistics costs, including inbound and outbound freight costs, helps identify opportunities for cost savings and optimizes the overall supply chain network.
To effectively leverage these metrics, businesses should implement robust data collection and analytics tools, such as warehouse management systems (WMS), business intelligence (BI) dashboards, and data visualization platforms. These tools provide real-time visibility into warehouse operations, enabling data-driven decision-making, continuous improvement, and proactive problem-solving.
As you can see, modern warehouse operations have evolved into a rather involved field, but that doesn’t mean that the basics have changed. Always put the customer first, focus on fulfillment times, and keep a regimented study on facility safety and organization. By following these steps, you, too, will have the tools you need to run an efficient enterprise.
the key principles of efficient warehouse operations are:
These three core operations – receiving inbound goods, fulfilling orders by picking and packing, and shipping outbound orders – form the backbone of most warehouse operations.
Our sales engineers are experts in automatic asset tracking, tagging and identification,a nd can answer all your questions. Get in touch now.
Lets Talk ›Enter your information and get a free checklist of the top questions to answer and tips to plan a successful asset tagging project for any warehouse management system implementation.