How to Design a Warehouse Racking Layout: 10 Steps to Efficient Planning
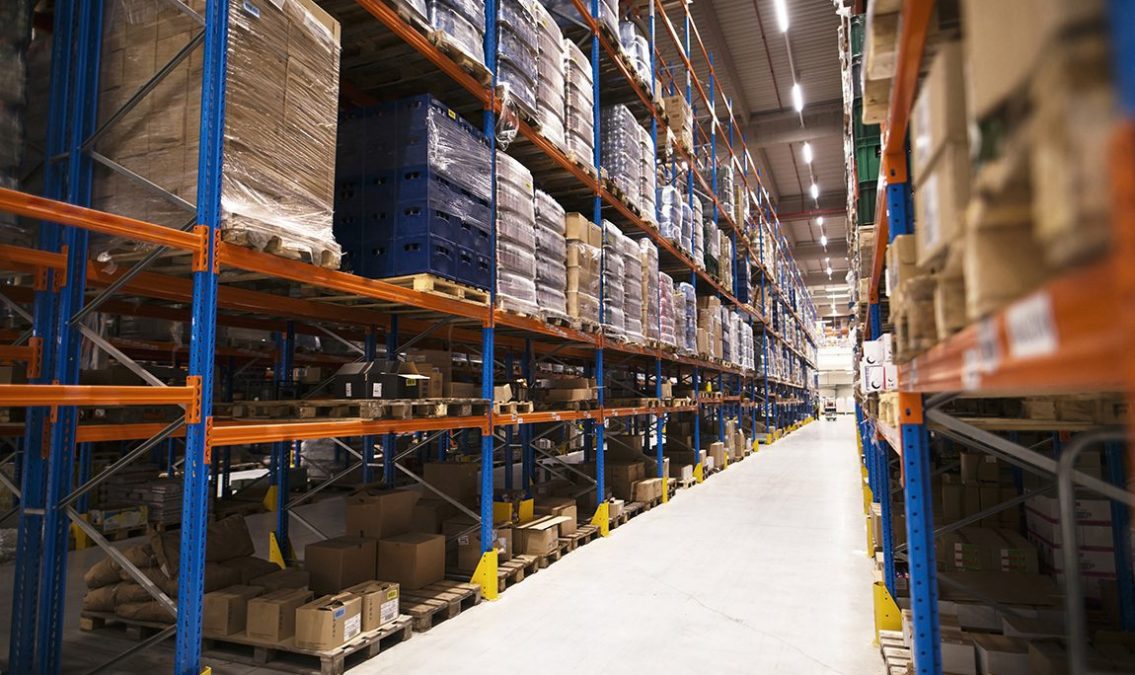
Efficient warehouse design relies on a complex balance of infrastructure, equipment, and inventory to facilitate organization and seamless operations.
One of the most important considerations: warehouse racking. An efficient racking layout is essential to your overarching warehouse infrastructure and design, since your racking system will, in large part, determine related factors, including your use of floor and vertical space, inventory access, docking locations, shipping areas, and other components.
With so much riding on your warehouse racking layout, it’s clear that brainstorming an efficient solution requires time and excellent planning.
You may be tempted to jump straight into planning your warehouse racking layout, but that would be a mistake. Before you begin, talk to knowledgeable contractors (like your material handling company), your warehouse manager(s), and even your drivers: They have years of experience in warehouse facility operations and planning, not to mention experience in your specific warehouse. Explain your goals and requirements, and then listen to their suggestions.
Racking starts with your storage system. What’s your pallet racking design? Are you storing large pallets packed with large goods, or do you favor smaller pallets with individual or small products? Do you carry both high-flow and low-flow products? Racking should adjust to your storage requirements, not your storage requirements to your racking.
An empty warehouse may look like a gaping maw, but the reality is that there are physical constraints on your storage space. Your job, when designing an efficient racking system, is to make the best use of finite space.
Start by arranging your racks in long rows – not short bursts – to get maximum use from your space. Don’t stack your pallets against the wall, as this limits efficiency, and scrap the hard-to-navigate L-shaped warehouse layout. Prioritize product access and warehouse navigation. Work to fully optimize your warehouse storage (including floor space and vertical storage).
If there’s a good chance you’ll someday want to increase your warehouse storage space, start planning for that now by choosing a modular racking solution, which is easily adjustable, versatile, and expandable. That said, developing a customized storage solution today can eliminate (or reduce) the need for future expansion, by accurately predicting storage needs to prevent overflow.
Not tech-mobile, but physically mobile: Moveable pallet racking systems can almost double your storage capacity via mobile carriages that maximize unused aisle space. Even better, almost any warehouse item can be stored on this mobile racking – even items that require heavy equipment, e.g. a forklift, to move.
Racking, storage, and shelving are not a small investment, so make the most of your money by investing in a durable, made-to-last racking system. Consider product weight (ex. light-duty racking cannot exceed 660 lbs.) and the kind of wear and tear most common to your warehouse, and then opt for a racking system with a good cost-lifespan balance.
Several types of racking systems are available – selective racks (ex. for narrow aisle racking), drive-in racks and drive-through racks (ex. for high-density storage), push back racking (ex. for bulk storage), and flow racks (ex. for high-density storage) – and the type you choose depends on your warehousing needs. You’ll want to consider factors like available floor space, ceiling height, pallet type and size, fork truck type and lift height, and budget, among other factors.
Once you understand your basic racking system needs, one of the first considerations is budget: the total cost for racking equipment, plus design and installation. Don’t cut corners: the goal is not the cheapest total, but rather the “best cost solution,” – the racking product and layout that best fits your warehousing needs. Once you’ve defined your needs and developed an ideal racking layout, then you’re ready to price-shop for the best deal.
Before you buy, map your warehouse layout. Account for all the considerations above, and add to them other important concerns, like shipping and receiving areas, the employee lunch room, managers’ offices, etc. A physical map will force you to consider all unmovable or unchangeable factors – columns, doors, and other obstructions – that you must design around, as you plan an efficient racking system.
An efficient racking system doesn’t do you any favors if your employees don’t know where things are stored. A good warehouse management system will keep your inventory and operations as well organized as your new racks.
And there you have it – 10 steps to building an efficient warehouse racking layout. For more tips from pros who have been-there-done-that, check out our 50 Expert Warehouse Racking Ideas, Strategies and Systems to Maximize Productivity.
Our sales engineers are experts in automatic asset tracking, tagging and identification,a nd can answer all your questions. Get in touch now.
Lets Talk ›Enter your information and get a free checklist of the top questions to answer and tips to plan a successful asset tagging project for any warehouse management system implementation.