5 Problems in Warehouse Operations (and How to Solve Them)
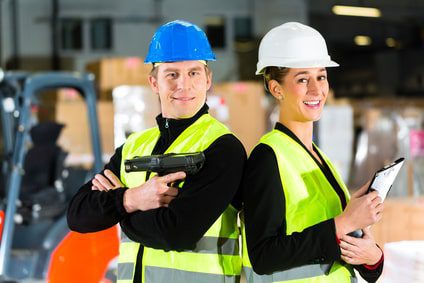
Modern-day warehousing operations are blessed to be given the gift of automation, cutting-edge software, and visibility galore. But, perks aside, we are now living in the day and age of rapid fulfillment rates that are dictated by some of the richest, most opportunity-driven global companies in history, which can cause problems in warehouse operations.
Suffice it to say, the number of warehousing operating in the United States is on a steady increase, as consumer expectations for speedy fulfillment are currently at an all-time high.
While this has created a ‘mini-Gold Rush’ for warehouses working in the segment, it can also be risky as we continue into uncharted operational territories. Fortunately, many of today’s warehousing experts and thought leaders are willing to share their best practices and predictions, allowing for even the most modest of warehouses to gain better control over their operations.
Today, we’ll discuss 5 of the most pressing problems in warehouse operations experienced in today’s warehouses so that each can be explored — and, better yet, solved.
The issue of pickers taking “too many steps” is a very common one in warehouse operations, especially in facilities that are scaling or during times of peak. It usually becomes most apparent when pickers are constantly zig-zagging the warehouse floor to reach the designated inventory, are consistently having trouble hitting their goals, or are finding themselves getting distracted throughout the day.
How to solve it: Depending upon the nature of this problem, there are several ways to fix it, starting with the development of optimized picking routes and/or techniques. Your current WMS should support any changes and might even be able to give you customized advice on which technique might work best, (i.e., wave picking, batch picking, etc.).
Another reason for this problem may be poor and/or outdated location mapping. Perhaps you are keeping multiple SKUs in one location, leading to confusion and errors, or perhaps your most frequently-replenished items are located in a remote part of the warehouse. Either way, this ineffective planning could be forcing your associates to take extra steps, which can be a real time suck.
Of course, it may also be time to invest in automation that either does the moving for the workers or assists them with it. This technology can be in a variety of different forms, including automated carts, AS/RS, robotic order picking, and more.
Cleanliness and organizational issues happen to the best of us from time to time, whether they be due to poor management, ineffective training, or unexpected changes in workflow. But whatever the reason may be, disorganized warehouses can, at best, cause lowered efficiency, and at worst, cause property damage or even bodily harm, which can result in a costly fine.
How to solve it: In an article for Business2Community, Lee House suggests allocating an hour per week to tidying up the warehouse, ensuring that all inventory is in its proper locations and that all debris, garbage, and unnecessary paper has been disposed of properly. Hold your associates responsible for any trash created and be sure to provide enough waste reciprocals where you can.
If excess inventory and insufficient storage is causing your problems in warehouse operations, adopt lean inventory practices for a more long-lasting, clutter-free solution. This way, you will only be working with the inventory that you actually need, freeing up space for the institution of better organizational models.
Any seasoned operations manager will tell you that busy warehouses go through batteries at high rate, especially when it comes to vehicles, like forklifts. This can end up being costly and time-consuming, ultimately affecting your bottom line.
How to solve it: To solve this battery drainage problem, Marcus Warner with Inbound Logistics suggests making the switch to lithium ion batteries wherever possible. These specialized batteries boast faster charging times than the alternative lead-acid batteries and require absolutely no maintenance either. Although Warner does acknowledge that these batteries are more expensive, experts, like the ones from Solar Micro Grid, say that lithium ion is the clear winner.
When you first established your operation, you and your colleagues may have poured your hearts and souls into building a sleek and strategic layout for your warehouse, but now the space seems to be working against you, not for you.
How to solve it: There’s lots of sage advice for all operational personnel dealing with an outdated layout. Experts suggest assessing the design at least once a year and re-slotting the warehouse to accommodate your business model. By taking a more flexible approach to your physical design layout, you can then take advantage of helpful features in your WMS that promote dynamic slotting.
Your operation has spent valuable time and far too much money on warehouse labels and asset tags that don’t seem to stay put or keep their integrity, thus leading to frequent scanning errors and overall problems in warehouse operations.
How to solve it: Learn how to choose the right warehouse label system. You’ll get acquainted with the sturdy tag material options that fit your warehouse’s environment best, as well as the scanning accessories needed to ensure that you are getting the most out of your labels.
When it comes to warehouse management, the key to maintaining a strategically-run warehouse is to continually identify your weak points — and find ways to improve upon them. With the overwhelming amount of information and support that is available to warehouse and operational managers today, failure in that matter is always a choice.
Our sales engineers are experts in automatic asset tracking, tagging and identification,a nd can answer all your questions. Get in touch now.
Lets Talk ›Enter your information and get a free checklist of the top questions to answer and tips to plan a successful asset tagging project for any warehouse management system implementation.