5 Steps to Effective Warehouse Location Mapping
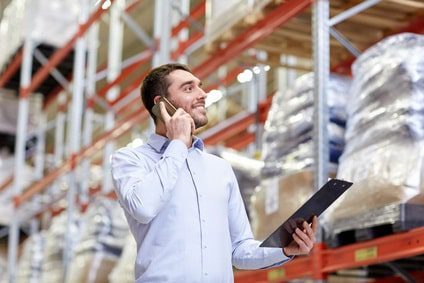
You might be distributing the best product in the world, but you can easily sabotage its success by implementing a thoughtless warehouse location mapping strategy. Because speedy fulfillment is currently the name of the game, devising a plan that takes a range of important considerations into effect is key.
But, before we get too ahead of ourselves, let’s first focus in on defining the basics of warehouse location mapping.
Warehouse location mapping is a systematic approach to identifying, organizing, and labeling all storage areas, product positions, work zones, and travel paths within a warehouse facility. It creates a structured system that assigns unique “addresses” to each location, much like a street address for a home.
This mapping system typically involves:
The primary purpose of location mapping is to enhance inventory management, streamline picking and packing processes, and improve overall warehouse efficiency. It provides a clear, visual representation of the warehouse layout, allowing staff to quickly locate items and optimize storage space.
A well-implemented warehouse location mapping system offers several benefits:
Modern location mapping often utilizes specialized software that provides interactive, visual representations of the warehouse layout. These digital tools can offer real-time inventory tracking, threshold alerts for stock levels, and integration with other warehouse management systems.
While location mapping in a warehouse is a process that takes time for planning and implementation, there are a series of steps that all operations can take to get things moving on the right foot.
While select warehouse managers may know their layouts and operational flows well enough to begin a plan without their boots touching the floor, most experts suggest commencing the warehouse location mapping process by walking through the warehouse to better inform the assessment. Carry a pen and a pad of sticky notes with you, labeling highly-trafficked and trouble areas as you go.
Take note of the travel paths that constitute the most streamlined routes and compare the shelving unit locations to your current picking strategy. These preliminary notes will act as the groundwork for your latest location plan.
Whether you are implementing a warehouse location mapping plan in a brand new operation, or you are in the midst of performing an overhaul on an established facility, it’s important that you gain first-hand knowledge from those who work on the floor and with your inventory. These are the associates who will be able to challenge the theoretical by providing you with the direct input that you need to formulate a well-researched plan.
Get a particularly keen sense of the movements of your pickers, taking note as to the lengths of their routes, whether or not they double back many times to retrieve products, and if the most popular SKUs are placed in the most accessible zones available.
Now that you have gained a clearer sense of strategic location mapping for your warehouse, create location names for your various inventory and equipment that fits well into your overarching organizational structure.
Here’s what should be included in the plan:
Once all locations are strategically named and mapped, it’s time to add durable, scannable, and easy-to-read labels to each location.
Camcode offers a range of warehouse label options that are designed to work within even the harshest of warehouse environments. To determine the warehouse location labels that are best of your operation, consider the temperature, climate, and wear and tear to which your infrastructure is exposed.
For a heavy-duty permanent option, opt for the Premium Polyester, and for temporary options to be used on transitional racks, consider the Magnetic label option. Proper labeling of aisles, docks, and other areas is essential for warehouse efficiency.
Don’t put in all of this hard work only to track your warehouse location mapping plan with an Excel spreadsheet, or worse yet, an archaic paper and pen system. Instead, take the time to integrate your locations into your current software solution. Most warehouses use, at the very least, a rudimentary WMS (warehouse management system) to track their inventory, procedures, orders, and to gain end-to-end visibility within their supply chains.
Now that all locations are effectively mapped for optimized efficiency, it’s important that all software systems reflect the changes before the new mapping plan goes live.
Implementing an effective warehouse location mapping strategy is a crucial step towards optimizing warehouse operations and enhancing overall efficiency. While the process may seem daunting at first, the long-term benefits far outweigh the initial investment of time and resources.A well-executed warehouse location mapping plan offers numerous advantages:
Remember that warehouse location mapping is not a one-time task but an ongoing process. Regular reviews and updates are essential to ensure the system continues to meet the evolving needs of your operation. As your business grows and changes, be prepared to reassess and refine your mapping strategy.
The three key factors to consider are:
The 6 key benefits of implementing a warehouse mapping system include:
Warehouse mapping software provides a visual representation of the warehouse layout, offering a dynamic and interactive way to view inventory locations. It allows users to create detailed maps, label areas, use barcodes, and set thresholds for inventory management.
Warehouse mapping should be updated:
Our sales engineers are experts in automatic asset tracking, tagging and identification,a nd can answer all your questions. Get in touch now.
Lets Talk ›Enter your information and get a free checklist of the top questions to answer and tips to plan a successful asset tagging project for any warehouse management system implementation.