What is Autonomous Maintenance? Benefits, Objectives, How to Implement
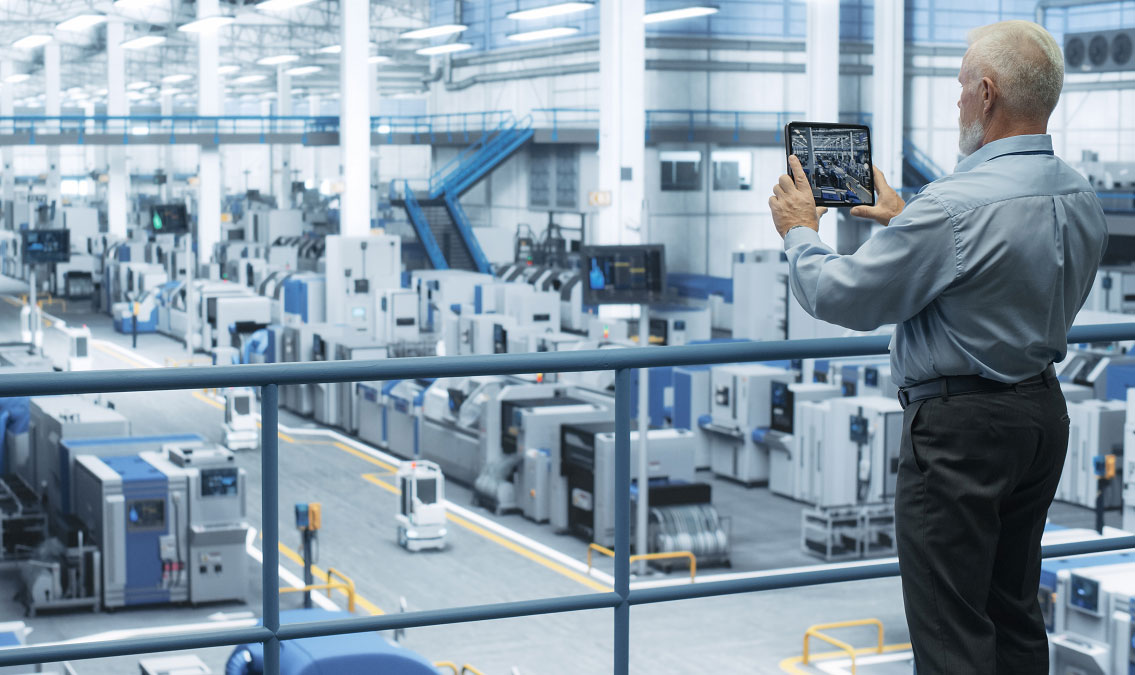
In an industrial setting, maintenance is often considered a specialized responsibility – something that’s primarily handled by specially trained technicians.
Autonomous maintenance (AM) flips the script: it’s a maintenance strategy that puts the onus on equipment operators for handling light-duty upkeep, leaving the trained service personnel to focus on more complex and unexpected repairs.
To understand why a manufacturer may adopt such a strategy, let’s take a closer look at the benefits of autonomous maintenance and how it can both empower staff and reduce equipment failures.
Autonomous maintenance is a maintenance strategy that empowers machine operators to take responsibility for the routine upkeep of the equipment they use. It is one of the eight pillars of Total Productive Maintenance (TPM), a methodology aimed at maximizing the operational efficiency of equipment.
There are several ways that an autonomous maintenance program can add value to a manufacturing operation. These include:
As we said above, autonomous maintenance is shifting power and responsibility for an asset’s basic service needs to the operator. This is in contrast to more conventional strategies, which are likely driven by managers, supervisors, or other higher-ranking stakeholders.
This explains the philosophy’s etymology: it’s not autonomous in the sense that a machine is self-cleaning or can automatically book its service needs, but that assigned users understand the basic needs of their equipment and can address them without input from management.
No one has to schedule a technician to perform something like a lubrication or a cleaning service because the operator is already doing these tasks themselves, as often as needed.
The result? Management has one less thing on their to-do list and technicians have that much more time to focus on more urgent service calls. This has positive ramifications for industries ranging from the food processing sector to military aviation.
Having a degree of ownership over their workspace can be empowering to employees. Operators are no longer simply operating the equipment to perform a task; with AM, they’re learning their machine’s intricacies and contributing directly to its trouble-free functioning.
Consider it like tuning your bicycle or changing your car’s oil – though these routine acts are fairly straightforward once learned, they help to build a bond between yourself and the machine. In a factory setting, this kind of bond can help drive engagement and heighten morale.
Employees more attuned to their machines will have a heightened awareness for degraded performance or other issues. These operators will know when a more thorough servicing may be needed, an intuition that can augment even the best computer maintenance management systems or predictive maintenance solutions.
By identifying the early stages of an impending equipment malfunction, proactive service efforts can be made – a move that’s cheaper, easier, and simpler than reacting to a total failure.
Allowing operators to perform light-duty maintenance will help keep machines running at or near peak performance. Why? Because routine small services can address wear-and-tear issues like dusty cooling ports, slackened belts, and dull blades before they ever become serious.
Being proactive about this can go a long way in improving efficiency and workplace safety.
All the benefits discussed thus far help support the ultimate goal of every manufacturing plant: to lower costs and improve productivity.
Cleaner, better-maintained machines will last longer. Empowered employees working in a safer environment can lead to higher morale and reduced staff turnover.
Simplified maintenance scheduling frees bandwidth for both technicians and managers. In short, there are countless ways that an AM plan can help you save money and boost production.
Check out the video below to learn about the history of autonomous maintenance:
If you’re ready to implement AM into your plant operations, there are seven steps you need to follow. From start to finish, these are:
To begin, you need to train your equipment operators about what proper maintenance looks like on the machines they run. These classroom trainings will get your staff up to speed on what they need to know, such as lubrication best practices or mandatory safety precautions like lockout/tagout policies.
Before you can begin AM in earnest, you need to get your machines back into as close to factory-fresh condition as possible. This means a thorough revitalization inside and out, so your employees can begin practicing their newly learned responsibilities on a machine that’s as good as new.
Contamination in this context is any factor that may revert a machine to the well-used, less-than-perfect state it may have been in prior to Step 2. Having operators perform routine cleaning and maintenance can partly reduce contamination risk; other strategies can be as simple as covering equipment when not in use or prohibiting food and drink at workstations.
To make sure that operators are maintaining equipment sufficiently, develop standards and best practices using input from trained technicians, equipment manuals, and other relevant sources. Leveraging a seasoned technician’s experience or manufacturer’s suggested maintenance plan can help you establish robust long-term best practices.
You’ll know if the guardrails established in Step 3 and 4 are adequate during routine inspections and monitoring, especially in the beginning stages of AM. By performing regular inspections of equipment – and by utilizing tools like logs, asset tags, and asset maintenance software – you can verify that your staff is meeting the standards set in Step 4.
This step is all about refining the visual cues that operators have to ensure the equipment is being operated safely and correctly. Labels, lights, and gauges can help satisfy these requirements of an AM plan, as you want to make sure there are fail-safe ways for operators to measure and observe fluid levels, pressure values, or other key performance metrics.
Maintenance is always a moving target, and new strategies are frequently found. New machines have different service needs, while retooled production lines repurpose old assets in ways that demand updated maintenance regimens. Step 7 is simply a reminder to stay nimble and be willing to adjust your AM plan to account for industry changes, facility updates, or other factors that can often force managers back to the drawing board.
The benefits of autonomous maintenance range from the financial to the intangible. By empowering your staff to participate in maintaining facility equipment, you’ll build employee engagement, help reduce the likelihood of breakdowns on the shop floor, and streamline your plant’s servicing ecosystem.
AM is also the first step to implementing what’s known as Total Productive Maintenance, or TPM – another cornerstone maintenance philosophy.
Ultimately, AM is a winning, proven formula that can benefit your facility for years to come. Use it alone, in tandem with TPM, or simply as part of your preventive maintenance strategy.
However AM manifests in your plant, we’re sure you’ll be glad it’s part of your asset management strategy.
Autonomous maintenance is a fundamental pillar of Total Productive Maintenance (TPM), where operators take responsibility for routine maintenance tasks on their equipment. This proactive approach empowers frontline workers to perform tasks like cleaning, inspecting, and minor repairs, reducing downtime and fostering a culture of equipment ownership.
Autonomous maintenance enhances equipment reliability and longevity, minimizing unexpected breakdowns and production disruptions. It also engages employees, improving their skills and morale while promoting a culture of continuous improvement and teamwork within the organization.
To implement autonomous maintenance successfully, a company should train and empower operators to perform maintenance tasks, establish clear Standard Operating Procedures (SOPs), and provide the necessary tools and resources. Regular audits and feedback mechanisms ensure ongoing improvement in the autonomous maintenance process.
Our sales engineers are experts in automatic asset tracking, tagging and identification,a nd can answer all your questions. Get in touch now.
Lets Talk ›Enter your information and get a free checklist of the top questions to answer to plan a successful asset tagging project for any maintenance tracking or facility management system.