5 Aircraft Maintenance Best Practices for the U.S. Air Force
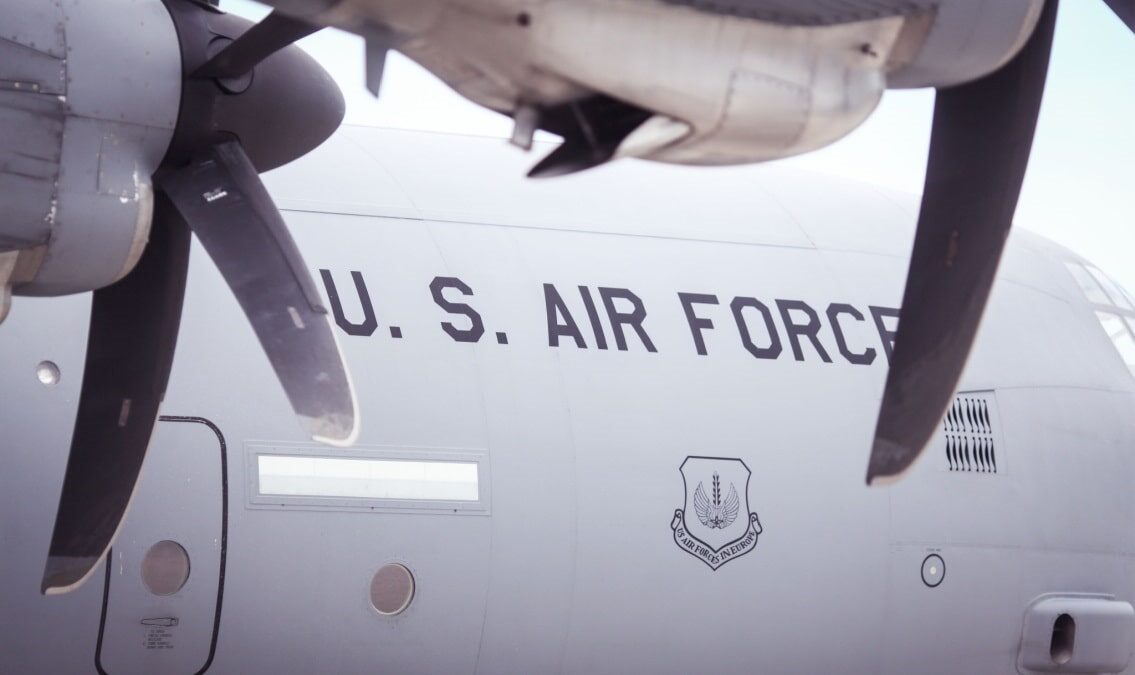
The United States Air Force (USAF) oversees the world’s most complex fighter fleet. Each plane costs tens of millions to hundreds of millions of dollars. Aircraft maintenance is a complex process, one that requires individuals with special skill sets and unique tools. Given the significant investments, here are five best practices to keep the aircraft flying safely.
Military planes are unique pieces of equipment, consisting of thousands of parts and featuring highly automated, state-of-the-art, integrated electrical, fuel, and software systems. Each model is unique and has its own capabilities and requirements. The planes are quite expensive, with prices ranging from tens of millions to hundreds of millions of dollars.
In addition, they are complex and delicate machines and require ongoing maintenance to ensure that they operate as expected. The cost to maintain these systems ranges from $50,000 to $150,000 per flight hour.
These five aircraft maintenance best practices enable the Air Force to maintain these systems as efficiently and cost-effectively as possible.
Aircraft feature special components as well as special maintenance tools. The flight crews need to organize their work gear. So, proper labeling best practices are needed.
The Military Standard 130 (MIL-STD-130) provides a detailed set of requirements and specifications outlining how US military property is marked and identified. The standard provides individuals, government departments, and third parties with consistent engineering and technical requirements.
Its Item Unique Identification (IUID) requires that all military and contractors place specific markings on their equipment. The specification ensures that unique numbers are assigned to government-owned and government-purchased devices. The UID marking must be applied to the asset for its lifecycle to ensure that tracking is possible throughout its lifespan.
The Air Force has a technician personnel problem. A 2019 Government Accountability Office report said that aircraft maintenance is the largest enlisted career field in the service, with more than 100,000 active and reserve maintainers. However, the Air Force has struggled with staffing. Simply put, they do not have enough techs and continually lose their experienced wrench-turners. Why?
The job is high-stress. Because these groups are short-staffed, these individuals are often overworked, increasing pressure on their professional and family lives.
Also, technicians work with very sophisticated equipment that must be finely tuned. Its importance cannot be understated because properly tuned planes can literally be the difference between pilots’ life and death. Because of budgeting issues, technicians often lack the needed parts and equipment to service the aircraft and sometimes need to do workarounds.
So, the military and third parties must put best practices in place to help these technicians balance their workload and home lives. Better scheduling, supplementing the workforce, and providing the techies with the proper tools would improve the work environment.
Maintenance departments commonly deploy autonomous solutions for different pieces of equipment. As a result, technicians must bounce from one system to another as they perform their work. The need to continually search for information increases maintenance times.
To stay ahead of potential issues, the Air Force can leverage digital solutions for aircraft maintenance tracking to centralize documentation, streamline inspections, and improve coordination between various maintenance teams.
Best practice solutions, like asset management systems, centralize equipment and tool information. Such software creates a holistic view of not only the assets but also staff, maintenance processes, and systems. The quick and easier access to data enables technicians to address problems faster and get more work done.
Plane maintenance is a manual, time-intensive, inefficient procedure. The rise of new technology, such as the Internet of Things (IoT), enables the Air Force to collect information from many components, which they are doing, but collecting information is only a first step to leveraging it to streamline maintenance processes.
Next, a best practice is to use artificial intelligence and machine learning systems to take the information and streamline processes, such as alert generation, that previously were done by individuals. Traditionally, technicians sit at terminals; monitor items, like response times; and search for anomalies. An AI solution examines the data, recognizes any change in patterns, creates an alert, and automatically sends it to the appropriate person. Therefore, productivity rises, and maintenance personnel spend more time troubleshooting and fixing problems and less time looking for them.
Most maintenance events are conducted on a set schedule. Items are tuned daily, weekly, monthly, and yearly. Other checks are triggered when a plane has been in the air for a certain number of hours or flown a preset number of miles. Such an approach is dubbed preventative maintenance. The idea is to tune the system before rather than after a problem arises.
With the emergence of IoT solutions, the Air Force gains more insight into how its equipment is functioning. A best practice, dubbed predictive maintenance, leverages that information and improves maintenance processes. IoT solutions provide real-time visibility into system wear and tear.
Rather than a best guess of when a device may wear down (found with preventive maintenance), they now have accurate readings about what condition equipment is in. They make changes as needed rather than after the fact or with a best guess.
Because of the potential benefits, interest in such solutions has been rising. The global predictive maintenance market accounted for $3.93 Billion in 2019 and is expected to reach $13.83 Billion by 2026, growing at a Compound Annual Growth Rate (CAGR) of 23.4%.
The Air Force operates a sophisticated, expensive, and sensitive fleet of aircraft. They have trouble maintaining them for a variety of reasons, including their sophistication and a lack of personnel. Implementing strong labeling, deploying asset management, and embracing automation and predictive analytics are best practices that maximize the return they receive on these assets.
Our sales engineers are experts in automatic asset tracking, tagging and identification,a nd can answer all your questions. Get in touch now.
Lets Talk ›Enter your information and get a free checklist of the top questions to answer and tips to plan a successful asset tagging project for any asset management or tracking system implementation.