What is Predictive Maintenance, Why is it Important?
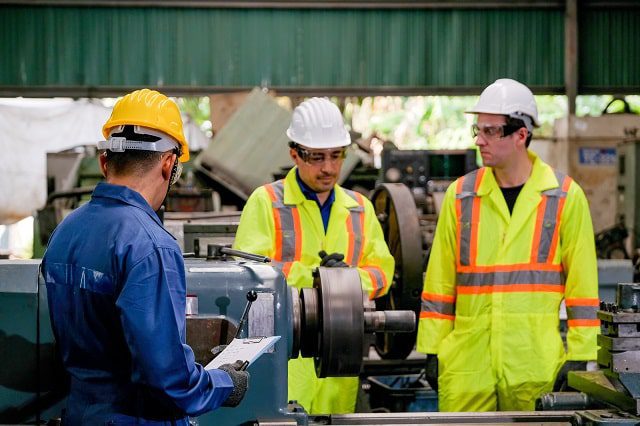
If your company relies on heavy machinery to operate, you need these tools to be available at all times. With unplanned downtime potentially causing production to fall behind, more businesses are embracing predictive maintenance to avoid this headache and the resulting financial losses that frequently accompany it.
Predictive maintenance software analyzes the condition of equipment through data collected by internet-connected sensors. If any piece of equipment needs attention, the system automatically alerts the maintenance team.
Predictive maintenance is the future. It has the potential to slash costs, optimize maintenance tasks, and keep your business running. In this guide, we’ll explain what predictive maintenance is, how it works, and how you can get more value out of predictive maintenance for your business.
Image by Kateryna Babaieva from Pexels
Predictive maintenance is a repair and upkeep strategy that uses tracking software to anticipate when equipment needs maintenance.
Any disruption in your workflow is detrimental to your ability to function; by implementing predictive maintenance, your company can continue functioning without sacrificing quality or safety.
The great thing about predictive maintenance is that it detects subtle changes in your equipment that the human eye doesn’t always catch. This is incredibly helpful for managing complex equipment that can easily fail if something is even slightly off.
It’s common to see businesses in these industries embrace predictive maintenance:
Predictive maintenance works through condition-based monitors that track various factors in real-time.
Applying a sensor to each piece of equipment allows you to monitor its status over time. The Internet of Things (IoT) and artificial intelligence (AI) can then track trends, set parameters, and alert maintenance staff of potential issues.
For example, a sensor on the machine can continuously monitor temperatures and alert your team if a machine is at risk of overheating. Your maintenance team can then review the data and make more informed decisions about repairing that machine.
From Industrial Automation to Predictive Maintenance, here are our Top 10 Industrial Internet of Things (IIoT) applications driving Smart manufacturing#IoT #manufacturinghttps://t.co/TfrT9eQDT5
— jimcaruso (@jimcaruso) July 31, 2023
Industry Metric | Value |
---|---|
Current Market Size | $5.5 billion (2022) |
Projected Market Growth | 17% CAGR until 2028 |
Adoption Rates by Region | 60% in Spain (2018), 54% in Germany (2018) |
Adoption Rates by Industry | 48% of plants use connected devices, 30% look to implement |
The global predictive maintenance market is experiencing significant growth, valued at USD 7.85 billion in 2022, with an expected compound annual growth rate (CAGR) of 29.5% from 2023 to 2030. This underscores the increasing adoption and investment in predictive maintenance technologies.
Additionally, 48% of plants already use connected devices to capture, analyze, and improve maintenance, with a further 30% looking into it
Advancements in artificial intelligence (AI), machine learning (ML), and the Internet of Things (IoT) are pivotal in predictive maintenance’s rise. These technologies enable real-time data analysis and the identification of equipment failure patterns, leading to more accurate, timely, and cost-effective maintenance interventions.
Ultimately, the goal of predictive maintenance is to know when you need to perform repairs or maintenance. It’s a cost-effective approach to maintenance that reduces unplanned downtime, especially for large facilities with complex equipment processes.
It’s important to understand that predictive maintenance is different from preventive maintenance. Both processes recognize the value of catching potential issues and repairing them before they create a bigger problem, but they aren’t the same.
With preventive maintenance, the maintenance staff follows a predetermined schedule and performs maintenance at regular intervals. They maintain the machines regardless of whether the equipment actually needs work or not.
Preventive maintenance usually relies on manufacturer recommendations for upkeep, not on actual data obtained from the equipment itself.
Predictive maintenance, on the other hand, uses data on your unique operations and machines to route resources only to equipment that needs attention. It needs a lot of data to make accurate predictions, but once you have this information, the system predicts potential failure points and tells your maintenance staff where to intervene.
Instead of paying to repair equipment that doesn’t need attention, you can route your maintenance staff to more important projects.
Image by Chevanon Photography from Pexels
Moving away from preventive to predictive maintenance will help you make the most of your time, maintenance staff, and resources. Businesses that embrace predictive maintenance enjoy a host of benefits ranging from cost savings to operational efficiency.
Benefit | Improvement |
---|---|
Reduced Maintenance Costs | 12% decrease |
Improved Asset Availability | 9% increase |
Reduced Repair Time and Downtime | 91% of businesses see improvements |
Improved Aging Infrastructure Maintenance | 93% of businesses see improvements |
It takes a lot of financial resources to maintain heavy machinery. Knowing when to replace parts or perform maintenance can trim the costs associated with operating specialized equipment.
In fact, predictive maintenance lowers maintenance costs by an average of 25%. It also takes the guesswork out of maintaining large facilities and complex machinery.
Finally, 91% of businesses report reduce repair time and unplanned downtime after implementing predictive maintenance.
Stop spending time and money unnecessarily on parts and labor and enjoy lower costs with a predictive approach to maintenance.
Equipment availability is a must for operating at a high level. Business disruptions drastically decrease as your equipment and machinery become more available. In fact, predictive maintenance decreases unexpected breakdowns by 70% and increases equipment uptime by as much as 20%.
Equipment failure is a major concern with heavy machinery. Predictive maintenance makes your equipment more reliable by giving you a data-driven tool for decision-making.
Predictive maintenance provides a reliable process for equipment maintenance that allows facility managers to rest a little easier. The system will alert you to any issues so you can make strategic decisions before a major breakdown.
A single disruption can have grave downstream consequences for your business. However, with predictive maintenance, you constantly collect data in your maintenance management system.
The maintenance team responds to any fluctuations in this data in real-time, preventing catastrophic breakdowns and the disruptions they cause.
Image by Gustavo Fring from Pexels
With predictive maintenance, you apply internet-connected sensors to all of the equipment or machines in your facility. These sensors are condition-based, which means they monitor, collect, and analyze equipment data, such as vibration patterns and sounds.
Predictive maintenance relies heavily on IoT technology. Thanks to these internet-connected sensors, the software can spot patterns and trends in your data to identify issues in real-time. Using IoT sensor data and AI algorithms, the system will gather and analyze data to predict which machines need maintenance right now.
With predictive maintenance software, you specify the parameters for how the equipment should perform. When the real-time data is outside of your acceptable parameters, the software will notify your maintenance crew so they can fix the problem before you have a major failure.
Implementing a successful predictive maintenance program requires a strategic, data-driven, and collaborative approach. Organizations need to carefully plan and execute each phase of the implementation process to ensure the program delivers the desired outcomes.
To help organizations successfully adopt and implement predictive maintenance, here are the four key steps to consider:
The first step in implementing predictive maintenance is to develop a well-defined strategy that aligns with your organization’s operational and business goals. This should involve:
Effective predictive maintenance relies on the ability to collect, aggregate, and analyze large amounts of equipment data from various sources. This requires:
To turn equipment data into actionable insights, organizations should leverage advanced analytics and artificial intelligence/machine learning (AI/ML) capabilities. This includes:
Predictive maintenance should be integrated into your overall maintenance management strategy, which involves:
By following these best practices, organizations can successfully implement a comprehensive predictive maintenance program that delivers tangible operational and financial benefits.
Looking to learn more about how to get started with a predictive maintenance plan? Check out the video below.
Image by Andrea Piacquadio from Pexels
Predictive maintenance has so many applications, but condition monitoring is the most common use case.
This feature measures your equipment’s vibration levels and frequencies. Each machine has a different vibration pattern when it operates at peak performance. But when something is wrong, the vibration pattern will usually change.
Some handheld devices can detect abnormal vibrations, but predictive maintenance helps your maintenance team spot these anomalies much more quickly. Vibration analysis is also great for detecting misalignment, loose parts, or motor problems.
Thermal imaging detects fluctuations in machine temperatures. As you use a machine, its parts will eventually wear out over time. Unfortunately, it’s sometimes difficult to know when the time has come to replace these components.
Overused parts release more energy and run at higher temperatures, which predictive maintenance systems can identify quickly. They display this data as infrared images to visualize hot spots on equipment.
From there, your maintenance team identifies the faulty parts and replaces them before they fail.
Instead of replacing parts too early or too late, you replace them just before there’s a problem. This is a cost-effective way to balance the need for replacements while also keeping maintenance costs low.
With oil analysis, your system identifies particles in a machine’s oil that might indicate a leak or malfunction. Oil analysis is a popular tool in predictive maintenance because it’s easy to set parameters: it usually just requires an initial test to get a baseline.
Changes in consistency, water quantity, or particle contaminants aren’t always noticeable, and your workers might not realize there’s a problem until it’s too late. Predictive maintenance uses sensors to detect these small changes so you know the moment something isn’t right.
Some sounds, like equipment parts running together, aren’t always audible to the human ear, but specialized acoustic sensors can easily detect these changes. Unusual noises indicate that the components of a machine are beginning to wear down.
Ultrasonic acoustic monitoring tells you to lubricate equipment or replace parts long before there’s an issue.
The sensors used in emissions testing analyze a machine’s emissions. The levels of pollutants in emissions can indicate excess oil burning, fuel sludging, or an overworked machine that needs upkeep.
You can use predictive monitoring to analyze several types of emissions, including:
Partial discharge analysis identifies when a machine starts emitting electrical sparks. It’s a helpful feature for monitoring:
Predictive maintenance sensors collect this data continuously and compare it to the preset parameters to see if a machine is close to failure. When the electrical discharge on a piece of equipment is outside the safe range, the software alerts your team to take swift action.
Image by Life of Pix from Pexels
Predictive maintenance decreases unscheduled downtime and reduces costs but still requires skilled operation. If you want to implement a predictive maintenance plan, creating a solid strategy is important before investing in a predictive maintenance system.
Follow these best practices to make the most of your investment in predictive maintenance.
Predictive maintenance cuts costs in the long run, but even then, it costs money to set up the processes. Plus, you need to train employees on predictive maintenance, which requires both time and money.
Predictive maintenance should be useful, but if you buy software before fully understanding your needs, you might not see a significant return on your investment.
This is a big investment, so do a thorough needs assessment before committing to any particular software. Do a cost-benefit analysis, run financial projections, and visualize your plan before you spend a dime.
Predictive maintenance evaluates the condition of equipment over time. Although it’s a powerful tool for managing equipment in the moment, you still need a way to evaluate the success of the program in the long run.
High-quality labels and tags make this much easier. Every time you perform maintenance, the data goes back to your predictive maintenance system to ensure the anomaly has been resolved.
Maintenance workers can then easily identify and track all activity performed on your assets with a quick scan of a barcode or QR code.
Quality labels and tags complement your predictive maintenance strategy, tracking all moving parts and demonstrating that the solution is actually providing a return on your investment.
Designed to survive in harsh conditions, Camcode’s durable facility management asset tags and labels work well for both indoor and outdoor applications. All labels are software-compatible, too, which makes it easy to track physical assets with a simple tag.
RFID labels or RFID tags are also a smart option for real-time tracking.
Shifting from a reactive or preventive maintenance strategy isn’t easy; transferring everything at once can feel overwhelming. It’s a best practice to identify the most critical machines in your facility and roll out predictive maintenance on these machines first.
Once you set it up, review the program’s success and refine it as necessary. Make sure the software is helping you save time, reduce costs, and streamline operations.
After you have proof of concept, feel free to expand the predictive maintenance program to more machines over time. This phased approach will help you iron out any issues on a smaller scale and provide a smoother transition.
Condition-based monitoring is a successful strategy that provides many benefits for any organization that uses heavy equipment. The combined power of IoT sensors, AI, and predictive maintenance software takes things to the next level and helps your company stay ahead of repairs.
While predictive systems will tell you where to go, your maintenance staff still needs an easy way to identify equipment. Maintenance management is even easier with Camcode’s durable labels and tag solutions. With proper labeling, you’ll know the status of every piece of equipment and machinery for smoother operations.
Order a free sample kit from Camcode to see how ready-to-use labels are the perfect addition to predictive maintenance.
Predictive maintenance works by:
A company implements predictive maintenance by:
Predictive maintenance is useful in so many ways. Companies use it for:
Our sales engineers are experts in automatic asset tracking, tagging and identification,a nd can answer all your questions. Get in touch now.
Lets Talk ›Enter your information and get a free checklist of the top questions to answer to plan a successful asset tagging project for any maintenance tracking or facility management system.