Warehouse Racking Tips: 50 Expert Strategies, Tactics and Systems to Maximize Productivity
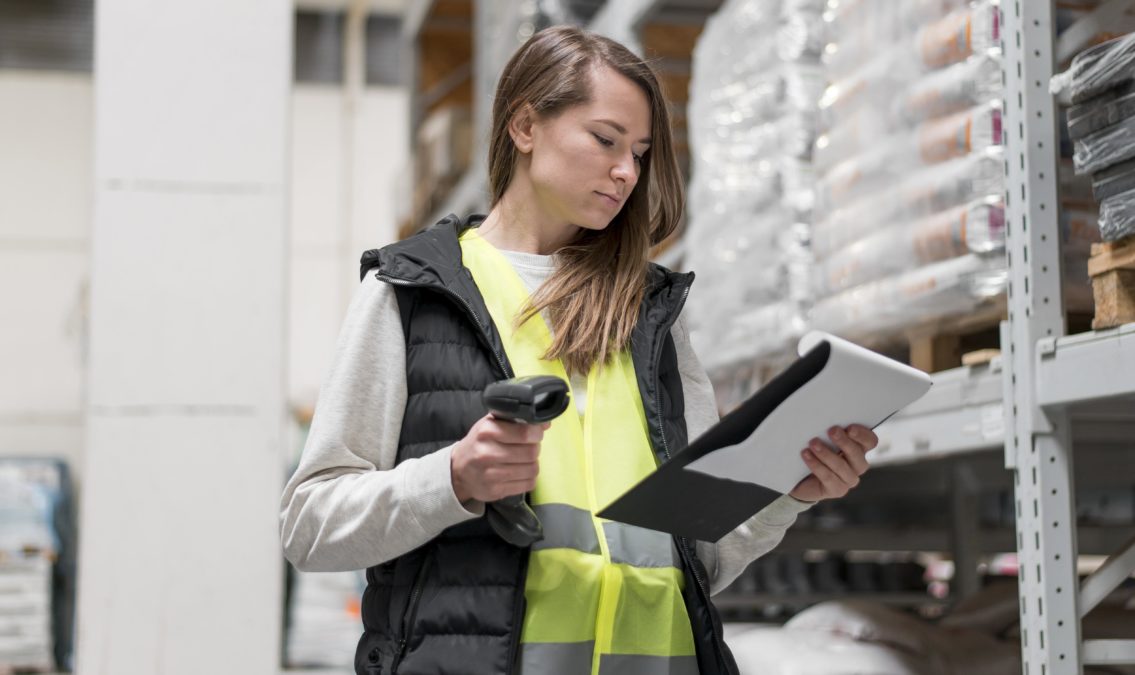
Warehouse racking is one of the foundational infrastructure components that facilitate seamless operation and optimal warehouse organization. Racks enable warehouses to maximize their use of space and organize products efficiently while allowing easy access for streamlined picking.
But racks are just one piece of the puzzle. Overall efficiency also depends on several other factors, such as the layout of the facility, the width of aisles, product demand, effective training to ensure the safe and efficient use of established racking systems, and much more.
We’ve put together this comprehensive guide to warehouse racking to provide warehouse operators with different perspectives and strategies on maximizing the use of space and infrastructure to boost profits as well as the key variables operators can manipulate in order to improve results.
1. Planning is the key to successful operations. “Plan your layout! Don’t just wander in and start throwing pallet racking here and there based upon whim and sudden desire. Your material handling company should have–SHOULD–have years of experience in laying out a warehouse facility. Rely upon their experience and knowledge. Tell them what you need done and then LISTEN to their suggestions closely.
“Your basic floor plan needs to take into account such things as where receiving and shipping will take place, where the staging areas are, where the warehouse manager’s office will be, where will your employees eat lunch, how the pallet racking will be accessed to determine type of forklift, if any.
“All of those things need to be planned in advance because if not, then as you move things here and there at your fancy, the more congested and hard to change the racking and overall flow of the warehouse will become.” – Chance Cook, Warehouse Set Up: 11 Tips That Will Help You Lay Out Your Warehouse, Jorgensen Material Handling
2. Budget your project. “The first thing to consider is the projected cost of your new racking – as well as the cost of designing and installing your solution.
“It’s not always about going for the cheapest. You still need to ensure that the racking you select will fulfill your requirements, but beware of cutting corners.
“Our advice is to consider the ‘best solution cost’ rather than simply going for the cheapest standard pallet racking. If you require a more specialist storage solution, be prepared to spend a little more for systems such as ‘pallet flow’ or ‘push back’ racking as well as enlisting the help of planning and installation specialists.” – Choosing Warehouse Racking: a Ten Tip Checklist for Getting it Right First Time, Acorn Warehouse Solutions Ltd.
3. Enterprises such as IKEA gain efficiency by distinguishing between high-flow and low-flow products. “IKEA’s store operations are supported by high-flow facilities (focused on the 20% of SKUs that account for 80% of the volume) and low-flow warehouses that are more manual. In its high-flow warehouses, IKEA employs automatic storage and retrieval systems to drive down its costs-per-touch. Products stocked in a low-flow facility are not in high demand, and operations rely on manual processes since workers will not be shifting and moving inventory around too much.
“These strategies have made IKEA the world’s most successful furniture retailer with low operating costs and high product demand. This allows the company to stay competitive in the industry as it continually seeks more advanced methods to streamline supply chain management.” – Clara Lu, IKEA’s inventory management strategy: how does IKEA do it?, Trade Gecko; Twitter: @tradegecko
4. Consider the ways you could build up to increase your use of vertical space before investing in add-ons or building new distribution centers. “Setting up vertical storage units to house your inventory is often the best use of a warehouse’s square footage. Before you relocate your warehouse entirely or move to planning a new distribution center, consider building up instead. It can help avoid expansion costs and increase the efficiency of your picking process. Keep smaller items in view and larger items safe from damage, all while fully utilizing the space you already have.” – 5 Tips to Improve Warehouse Productivity, RackExpress; Twitter: @RackExpress
5. To quickly and efficiently design a layout, ignore existing obstructions. “Draw your initial shelving layout as if there are no columns or obstructions present in your building.
“After you’ve designed the most efficient layout for your space, then draw in the columns and obstructions and adjust your initial, highly efficient layout as little as possible to accommodate obstructions. Of course, there are always floor space obstructions.
“Columns may be positioned in awkward places…heaters, lights, drain pipes, and other hardware may clutter your headroom… and your safety engineer may have requirements that further complicate your layout task.
“That’s why creating an efficient shelving layout system always involves flexibility and compromise.” – Tom Jameson, President, ShelfPlus, Inc., How to Plan and Create an Efficient Industrial Shelving System, Spacesaver Industrial; Twitter: @Spacesaver
6. Arrange racks in long rows rather than short bursts to maximize space. “You may feel as though you have all of the space in the world, but the reality is there are some physical constraints. A few things you’ll need to avoid while planning your space include:
7. Consistently strive for optimization. “Looking from an overhead point of view, decide on the positioning of your storage units that will promote the greatest efficiency. Gauge which pallet racks, mezzanines, wire shelving, and other types of storage units will best benefit material handling and flow of shipments. By consistently striving for ways to optimize storage layout, your warehouse is bound for faster shipping and greater organization.” – Storage Techniques For Maximum Warehouse Efficiency, The Shelving Guy Blog; Twitter: @ShelvingDotCom
8. Supersize the receiving area. “When my partner Scott and I used to help clients design a new warehouse, the first thing we would do is draw up an obnoxious amount of space for the receiving function. We knew full well that the client was going to cut it down and throw up more product racks, but we wanted to stress the importance of the space. Receiving is the most critical function in the warehouse. One mistake here generally translates to ten additional errors before you get it corrected. Let me take a moment to translate. An error in distribution means a reduction to your net profit.
“Think about all the activities that a receiving team must do. They break down pallets. They count the items and reconcile with the manufacturer’s packing list. Sometimes they add barcoded labels. Occasionally, the manufacturer makes a shipping error and the team needs to stage the product. Items come in to fulfill customer back orders. We need a place to accommodate this type of cross docking activity. When we force the team to work in cramped quarters, mistakes will occur.” – Jason Bader, Managing Partner, Tips for Laying Out a New Warehouse, The Distribution Team; Twitter: @Distribution_Tm
9. Calculate storage efficiency. “Storage efficiency refers to the amount of space needed to store a single pallet. Whereas warehouses are measured in square feet, the amount of space a pallet consumes when stored using the full cubic height of the building is significantly less.
“The formula to calculate the amount of square footage consumed by a single pallet stored is as follows:
Length x width of the storage unit in inches divided by 144”. This gives the square feet of the storage unit.” – How to calculate storage efficiency, Simon Walker’s Big Concepts; Raymond Handling; Twitter: @RaymondHandling
10. There is no one-size fits all best approach to racking and organization. “How your warehouse is organized really is critical in how efficiently it operates. The way you organize it is your choice — choose the method that works best for you. You might want to stock materials by the order of the most frequent sales, or stock groups of items that tend to sell together. If you sell seasonal items, this is another organization option.
“Stocking by barcode or RFID does help, but take this a step further and keep your materials in an order that works. This will save you a great deal of time and money during order filling and inventory procedures.” – Jerry Matos, Product Specialist at Cherry’s Material Handling, The Manufacturing Warehouse: 5 Material Handling Tips To Make It More Efficient, The Digitalist by SAP; Twitter: @digitalistmag
11. Don’t plan the space based on reusing existing equipment. “Since the original space was planned, the storage requirements have likely changed in terms of the number of SKUs, SKU size, quantity, available storage space and in some cases, regulations. As such, the planned space must be configured to accommodate current needs at a minimum. This will inevitably mean different sizes and types of storage solutions than previously used. It’s important to plan accordingly to the last detail. Once there is agreement on the current plan, make sure to review what was in place to see what, if any, items can be reused. This might lead to a higher budget, but in the end, it will prove to be a less costly, more efficient long-term storage space.” – Dave Salus, 6 tips to consider when designing and organizing storeroom and warehouse space, Metro
12. Take cues from big-box retailers to gain productivity. “If you manage a larger warehouse, it’s not a bad idea to make the whole place look like a Lowe’s or a Home Depot store when you first walk into it. This means that it’s OK to hang signs at the ends of aisles in your warehouse – in fact, it’s a great organizational tactic that can help you maintain organization.
“Products relating to one category will always be stored in aisle X, for example, and they will never be found anywhere else. It makes it easy for you and everyone working in your warehouse to remember where things are, and it makes training new employees easier and more time-efficient since they won’t have to struggle with looking up where to find a product if they can just look up and see it on a sign by an aisle. Plus, warehouse sign solutions are easy to find and relatively inexpensive to purchase, and even easier to implement.” – Tips for Organizing and Managing Your Warehouse Inventory, Max Material Handling; Twitter: @MaxMaterial
13. Consider application-specific requirements, such as the need to rotate perishable items. “The best advice in the effective use of a dry goods storeroom is: rotate, rotate, rotate. Date all foods and food containers. Stored foods cannot get any better than what originally went in, but they can certainly get worse. The first food in should be the first food out: FIFO. It takes a bit of imagination and craft to position foods within a storeroom to best implement this principle. Keep a handy and readily visible record of the ‘use by’ and ‘sell by’ dates of the received foods and the shelf life in general.” – Robert W. Powitz, Ph.D., MPH, 7 Simple Rules for Effective and Hygienic Dry Goods Storage, Food Safety Magazine; Twitter: @FoodSafetyMag
14. Standard pallet racks are the most common warehouse rack options; however, these racks require an aisle in order to allow forklift access. “Once the general flow of the warehouse has been determined, racks must be chosen to make best use of the available floor space. Since almost all material shipped by truck is stored on pallets, different variations of pallets racks are used in most storage facilities.
“Standard pallet racks are the default choice for any facility that has high turnover and many different products. Every pallet on a pallet rack is accessible to the forklift driver. This ensures that absolutely no parts will be buried or lost for years. Each storage location can be labeled and referred to on a master list, whether electronic or simply on a piece of paper. The material handler can easily follow a grid schematic, tracking rows and columns until he reaches the location where material is to be stored.
“This benefit of accessibility comes at a cost. An aisle is needed between each set of pallet racks, so the forklift can get to the pallet. In many cases, however, this degree of accessibility is not necessary. Sometimes, entire trucks deliver the same product. These skids don’t necessarily need to be individually accessible. Since they are all the same, they could be stored in rows, with the back ones buried until the front ones are removed.” – Warehouse Layout – How to Use Racking to Optimize Warehouse Space, Industrial Warehouse Racks
15. Deep lane pallet racking enables multiple pallet storage. “There are two ways to store multiple pallets in racking (deep lane pallet storage): put pallets in the rack and have them move inside the racking using gravity or have the lift truck enter completely (drive-in) or in part (deep reach) to store and retrieve the pallet. Now there is a third way.
“Pallet shuttle, Radio shuttle, Pallet Mole or Pallet runner are all examples of automated deep lane pallet storage. This system has a small slave robot that enters drive-in style racking on a second rail beneath where the pallet is stored. The robot (shuttle) lifts the pallet a few inches of the edge racking the pallet is stored on and transports it into the system.” – Pros and Cons of Pallet Racking, Warehouse IQ; Twitter: @WarehouseIQ
16. Pallet racking systems allow for better use of vertical space. “Some of the most successful businesses like Costco and Sam’s Club would quickly diminish without the use of pallet racking systems. This method of organization is beneficial for any business, small or large:
“DIFFICULTY OF IMPLEMENTATION: Moderate. It may be a large initial investment for a company to switch over to a pallet racking system, however, the results are unquestionably cost-effective and worth it overall. In addition, implementing a pallet racking system may also initially require quite a bit of extra labor; but for the most part, you only need to deal with this major transition one time. Once the investment has paid off and the guidelines of the pallet racks have been established and engrained, maintenance becomes very low.” – 7 Ways to Organize Your Warehouse, PHS Wire
17. Multi-level structures are increasingly popular as warehouses and distribution centers seek to take advantage of every inch of available space. “Engineered systems that incorporate multi-level structures are the hot ticket item right now for Western Pacific Storage Solutions, where Mike Guerrero, vice president of engineering says his team is getting involved in more and more of these projects. ‘This is one of the most interesting trends I’ve seen in the last eight years,’ says Guerrero. As companies incorporate these multi-level storage structures into their warehouses, he says most also want to go higher than ever—a goal that’s been enabled by the evolution of wire-guided, man-aboard orderpickers.
“‘We’re making systems that are 20- to 30-feet tall,’ says Guerrero, who notes that man-aboard orderpickers are usually tailed for rack systems (i.e., with the worker picking full cases from a rack). With the rapid rise of omni-channel fulfillment, however, more firms want to be able to pick split cases or discrete components from tall/high-bay shelving.
“‘We’ve been seeing more and more of these applications over the last year or so,’ he adds. To accommodate such requests, Western Pacific makes RiveTier Boltless Shelving (applicable for two-level systems) and Deluxe steel shelving options that can incorporate three- and four-level options.” – Bridget McCrea, Rack, shelving and storage looks vertical, Modern Materials Handling; Twitter: @modernmhmag
18. Your racking infrastructure will vary based on product size. “Racking infrastructure will vary by product size. Many warehouses keep large products in bulk stacks or pallet racks. While with small products, picking efficiency may be increased by storing smaller products in flow racking or static shelving.” – Top 10 “Must Have” Warehouse Management Systems (WMS) Features, iCepts Technology Group; Twitter: @iCepts
19. Consider bulk storage racks for products too large for shelving. Bulk storage racks are useful in several settings beyond the warehouse, such as storerooms for maintenance and repair departments. “Bulk-storage racks are available in a range of lengths, depths, and heights. These racks can store parts too large, bulky or heavy for shelving. Products such as air filters, flexible ductwork, longer air or hydraulic cylinders, midsize gearboxes, conveyor belts, speed reducers, gear motors, and motors generally are stored on bulk-storage racks.
“Crossbeams placed just above floor level enable parts storage off the floor. Or supervisors can store pallets on the floor under pallet racks to hold heavier, larger motors, gearboxes and machine parts.” – Frank Murphy, CPMM, Inventory Management: Storage Considerations, FacilitiesNet; Twitter: @BldgOpMgmt
20. Moveable pallet rack systems are valuable space-saving tools in many warehouses. “Moveable pallet rack systems operate on mobile carriages that eliminate unused aisle space and can nearly double you storage capacity. There are virtually no limits to the size, bulk, weight or shape of items that can be stored on moveable pallet racking. This includes almost anything that can be moved by forklift, truck, or crane. Flexible and adaptable, moveable systems work within almost any building support or ceiling restrictions and can be reconfigured easily if needs change. They work particularly well for the 80% of inventory which is slow-moving or seasonal.” – Tom Jameson, President, Pallet Rack: How to Avoid Costly Errors in Planning & Installing, ShelfPlus, Inc.
21. Custom industrial shelving solutions can often solve challenges once you identify problem areas. “In many cases, a full warehouse is simply a disorganized warehouse with inadequate shelving. By identifying problem areas, you will find the opportunity to improve efficiency while using every bit of room. Floor space is finite, but vertical storage can offer a huge increase in the amount of product that can be stored. Vertical storage requires the right type of shelving for the products with a focus on safety and easy access. Using available warehouse space poorly is a common problem, and it is easily resolved with custom industrial shelving systems.” – Alex White, Senior Marketing Officer at Western Pacific Storage, How to Maximize Warehouse Space and Efficiency, The Network Effect
22. Choose warehouse racks that offer durability for a long lifespan. “Assess the type of racking, shelving and storage you need for the products to be kept in your warehouse. Purchase robust racking / shelving to allow for the maximum lifespan and wear and tear possible. Make sure it is securely attached to walls and floors, to prevent injury to staff and damage to products. Finally ensure that there is plenty of space between the units so that all stock is easily accessible.” – Snapfulfil, Ten tips on setting up a warehouse, by Snapfulfil, Supply Chain Digital; Twitter: @SupplyChainD Learn more about “setting up a warehouse“
23. Consider the load. “An important tip on pallet racking to keep in mind is to consider the load. What are you planning on storing? This will have a bearing on whether you would select:
“The capacity of the racks must correspond to the load it will be bearing. The weight of the cargo on each shelf should never exceed the maximum capacity of the pallet; you should never overload the shelves, even if the rack seems to be able to bear the heavy load for the moment. It’s also important, when considering load or capacity, to ensure that your rack is not ‘top-heavy’; this means that light cargo should be placed on top (high), and heavier cargo should be placed on the bottom (low).” – Tips on Pallet Racking, Pallet Racks and More
24. The right warehouse racking system is essential for ensuring safety. “Uneven stacks can be unstable and unsafe. When warehouse items are stacked improperly, you risk single items or even whole stacks falling and potentially injuring somebody. Make sure that all stacking is done evenly, with the heaviest items on the bottom. Investing in high-quality racking equipment that meets current safety standards is critical to the safety of your employees.” – 5 Essential Warehouse Safety Tips, Material Handling Exchange
25. Make sure that you implement strong and stable warehouse racking systems. “First and foremost, before we get down to the nitty, gritty details, we need to make sure that your reliable pallet racking systems are up to the task. It’s important to make sure your pallet racking system is strong enough to withstand the sheer number of products they’ll be forced to hold. December and January are two of the busiest months in the old and new year. December brings you the rush of the Christmas shopper, desperately trying to remember to buy products for their friends and family, while January brings the crush of the sales.
“The last thing you want is to find your shelves can’t cope with the sheer weight. To combat the threat of tired shelves, make sure you place your heavier products on the bottom shelves.” – Tips for Warehouse Transportation Safety, ShelfSpace
26. Modular edge racking systems improve accessibility and worker safety. “The modular edge is a variant of systems of pallet racking and is the preferred choice among warehouse storage services. This system enhances worker accessibility and ensures safety. The storage capacity of the system can be enhanced by using accessories like frame protectors, anti collapse systems, steel mesh racks, deck panels and extra supports.
“Organizations may choose from amongst the various kinds of pallet racking solutions. It is however advisable to consider the following factors while selecting the appropriate one:
27. The right layout and rack options depend largely on product mix. “Warehouses need to maximize storage space and somehow get product out the door on a timely basis. To accomplish this, experts suggest that planners think strategically.
“‘It’s really dependent on the mix of product,’ says Tompkins’ Hudock. When his firm consults with customers, he needs to know information such as what the hold time on the various products are, as well as the lot or batch sizes involved.
“Often, racking solutions depend on the type of businesses the facility caters to. For a foodservice company that is delivering specialty items to restaurants, experts recommend shallow racking. ‘Those type of products don’t sit on the shelves very long,’ says Curry. ‘Those types of operations should consider single-deep, selective rack or two-deep pushback.’
“The bulk storage facilities that quickly turn around mass quantities of goods, like frozen french fries, should use some deep storage and vary that with two-deep racking for SKUs that are variations on the same theme, like crinkle cut french fries, steak fries, etc.” – Brian Schiavo, Maximizing Space Vs. Accessibility, Food Logistics; Twitter: @FoodLogistics
28. The first step in designing an effective system is to consider the opposing forces of storage density and product selectivity. “The first step in designing an effective and superior pallet storage system is to optimally combine the critical (but often opposing) functions of storage density and product selectivity. The factors to be considered for a balanced storage system include: the total number of SKU’s which are palletized, the number which have threshold inventory quantities of more than one pallet load and up to or more than 20 pallet loads, rotation‐of‐stock (F.I.F.O.) requirements, and the methods by which product selection and replenishment will occur. High density storage enhances space utilization, but minimizes individual SKU pallet‐load access. Direct ‘face’ access (selectivity) to all individual pallets typically requires more aisle floor space than high density storage arrays.” – Patrick Thibault, Designing Optimization: Creative Solutions in Pallet Storage Rack, Wynwright
29. Always arrange racks to be as long as possible. “Using an example area of a 56 foot by 72-foot room, there are a few things you need to avoid in your design.
30. Mobilize your racks and shelving for greater accessibility. “How does mobilizing pallet racks and shelving work? By placing your existing or new pallet racks or shelving on carriages that are attached to floor tracks, you can compact them together and create movable aisles. What does it do for you? It not only freezes your warehouse footprint, it recoups over 50% of your warehouse storage floor space, which means you can double your existing storage capacity or use that space for something else entirely. Watch this video to learn more about mobilized pallet racks and shelving.” – Efficient Space Saving Tips: Freeze Your Warehouse Footprint, Southwest Solutions Group
31. If your employees are spending hours searching for the right product, you’re losing the cost battle – no matter how efficient your rack system is in theory. “Once you have simplified receiving materials, products must be stored in the most efficient manner possible. If employees are spending hours locating and retrieving items, you are losing the cost battle. By using the right inventory system, your workers can know exactly where to look for each item when placing them into storage or picking them for shipment. Programs can also be designed to group items by location, preventing hours of back-and-forth trips by employees or lift trucks.
“You also need to make the best use of warehouse storage. Shelving racks are no longer a one-size-fits all application. If you have an overload of products in one location with contents spilling on to the floor, and empty racks on the other end of your warehouse, your method is not working.
“A customized storage solution will keep your materials organized. By using the right options, you can also eliminate the need for expanding your warehouse space. Fluctuating inventories should not create an overload. If you need to search for more space on a regular basis, you should invest in a better system.” – Jeff Maree, Applying Lean Principles to Warehouse Management, Manufacturing Transformation; Twitter: @Apriso
32. Ensure easy product availability by arranging racks and shelving units in a system of aisles and cross-aisles. “Ensure quick product availability by having a system of aisles and cross aisles that make it easier to move around your warehouse. Long and continuous aisles can make it difficult in getting from one part of the warehouse to another. However, cross aisles that allow access to the main aisles, help create a grid that is more efficient and easier to navigate.
“The goal of the warehouse layout is to optimize your warehousing functions and achieve maximum efficiency and space utilizations.” – Improving the Layout of Your Warehouse, Adaptalift; Twitter: @aalhyster
33. Distribute weight evenly, and train employees to do the same. “A new, inexperienced employee may think everything is fine as long as the load is placed on the pallet. In reality, all loads need to be placed on the rack in the right evenly because a small shift in weight can throw the whole pallet off balance.
“This is where safety training comes into play. It is wise to have drivers be certified in forklift operations to ensure safety. Companies may also want to require training in maintenance and operational training when it comes to pallet racking and forklifts.” – Tips for Warehouse Pallet Racking, Insight Works; Twitter: @DMSInsightWorks
34. Be sure to secure your shelves. “Commercial shelving is often meant to store bulkier items and therefore, must be durable enough to hold heavier weights, but also built in a way where they will not tip or sway. Choose the material of your shelving based on what you want to store or use wall mounting brackets to secure the shelves in place.” – Top 5 Warehouse Shelving Safety Tips, Action Wholesale Products; Twitter: @Action_WP
35. Racks have a few advantages over shelves, including airflow. “Pallet racks have a minimal impact on the integrity of a warehouse, even when built into the building as part of the foundation. The racks themselves are light and consist of fewer components than other storage systems. And, as such, pallet racks are significantly cheaper than a full-shelved storage system. The racks themselves can also be built higher than equivalent shelving.
“On top of this, pallet racks offer great visibility of your stock, as well as excellent ventilation and airflow.” – The Benefits of Pallet Racking, Fantastic Man Magazine
36. Consider the expected time to pick (ETP). “Sometimes it is difficult to see the warehouse for what it really is—a collection of pallet positions where inventory is put away and picked at varying frequencies. The key to distribution efficiency is making better use of warehouse real estate, according to Terry Harris, managing partner, Chicago Consulting.
“Companies often put away inventory without considering how that position impacts future processes. Without directed putaway, decisions are left up to the operator, or the use of a traditional zone structure.
“Warehouse real estate demands a more common-sense approach to visualizing inventory turns within the facility—a term that Harris refers to as expected time to pick (ETP).
“In most warehouse operations, picking is more time-consuming than putaway. That’s where labor generally resides. Warehouses need to optimize slotting to ensure pallet positions and storage profiles match the flow of goods within a specific facility.
“Harris’ premise is that traditional zone picking and putaway conventions do little to increase speed or efficiency within a facility. They force companies into using a protocol for prioritizing inventory that doesn’t go far enough.
“‘Zones create groups of positions,’ Harris says. ‘The theory is that every position in that zone has the same real estate value, but that’s rarely the case. By contrast, you can differentiate down to the pallet position within that zone. It’s the logical extension.'” – Joseph O’Reilly, Innovative Warehouse Strategies: Four Walls, Three Takes, Inbound Logistics; Twitter: @ILMagazine
37. Batch picking enables workers to pick more than one order at a time, but for large batches with multiple orders, it’s best to have software to ensure accuracy. “This strategy involves picking more than one order at a time and can be achieved with both manual and automated picking. With a manual picking environment, a simple batch picking process allows the picker to pick SKUs required for multiple orders at one time, minimizing travel time. This type of manual batch picking works best with smaller SKUs, as manual picking with larger SKUs leaves a greater risk for error. When batch picking more than a few orders at a time, it’s best to integrate software to maintain accuracy rates. The software can optimize picks, direct the worker to the picking location, and verify the quantity to pick.” – Types of Picking Strategies to Maximize Productivity in Warehouse Operations, Southwest Solutions Group
38. FIFO rack systems are an intuitive solution for optimizing warehouse workflows. “First-in, first-out, or FIFO, is a type of inventory management that allows inventory placed into a rack system first to be removed first. FIFO rack systems are ideal for customers requiring rapid stock rotation, have a high turnover rate for inventory, or store items with expiration dates. For example, FIFO food storage applications allows for constant product movement, safeguarding that no inventory spoils or goes to waste.” – FIFO Rack Systems, REB Storage Systems International; Twitter: @REB_Storage
39. Block stacking is a cheap-to-implement method and a good choice for some warehouses. “Block stacking refers to unit loads stacked on top of each other and stored on the warehouse floor in lanes or blocks. The pallets are stacked to a specific height based on a number of criteria such as pallet condition, weight of the load, height clearance and the capability of the warehouse forklifts.
“The pallets are retrieved from the block in a last in, first out (LIFO) manner. This does not allow for removing stock based on date basis or FIFO. Removal of stock can cause honeycombing to occur where empty spaces occur that cannot be filled until the whole lane is empty.
“This method is cheap to implement as it involves no racking and can be operated in any warehouse with open floor space.” – Martin Murray, Pallet Storage Methods in the Warehouse, About Money; Twitter: @AboutMoney
40. Don’t hesitate to re-slot product often. “Re-slot your pick positions as often as necessary. Up to 60% of a picker’s daily activity can be involved in travel time (afoot or on a forklift or walkie), so reducing that time-spend is an excellent idea. A good product slotting strategy can reduce travel time thereby reducing picking labor. Always weigh the time and cost of a complete re-slot against the costs of it. Busy operations re-slot their fast moving, high-profit SKU’s every day. Slotting the facility once and leaving it that way for years is typically a recipe for wasted time and money.” – Scott Stone, Best Practices for Warehousing – 13 Tips for Productivity, Cisco-Eagle; Twitter: @CiscoEagle
41. Pareto your inventory for analysis. “Gather sales and inventory in dollars by item. Construct two Pareto charts. For the first chart, classify your items into A, B, C, and D (80%, 15%, 5%, 0%) based on sales. Then calculate your inventory for each group. Do your A items represent 50% of your inventory? If not, you may not have enough inventory for these items. A significant amount of inventory on low demand items may indicate problems with product run-outs, transitions, engineering change management, and managing obsolete inventory.
“For the second chart, classify your items based on inventory. Then calculate the sales for each group. Again, do your A inventory items represent at least 50% of your sales? If not, inventory may be out of balance. These charts are an excellent way to begin looking at your inventory. After gathering this information, you have the makings of a supply chain data warehouse for further analysis.” – Chuck LaMacchia, The Progress Group, LLC, Ten Ways to Reduce Inventory, While Maintaining or Improving Service, ShelfPlus
42. Wide aisle racking is a popular approach allowing easy access to each stored, palletised load. “Easy to install, versatile and cost-effective, wide aisle racking is definitely the most popular warehouse pallet storage system and directly allows access to each stored palletised load. Adjusting beams, accommodate re-configurable warehouse layouts. Therefore the versatility comes from allowing the type of goods that are stored to change with the business model. Wide aisles give the space needed to allow all forklift traffic easy access throughout the Racking layout. This Wide Aisle style renders specialised handling equipment unnecessary.” – Stuart, Efficient Warehouse Storage Solutions – ‘Our 10 Step Pallet Racking Guide’, Workplace Products; Twitter: @WorkplaceProd
43. Remember that racking is one component of a multi-faceted process. “For many businesses, striving to achieve more efficiency in the warehouse is an on-going task. Many businesses implement Warehouse Management Systems, others improve workflow by upskilling staff and employing floor supervisors to ensure that work gets done and processes are followed.
“Another way to achieve a more streamlined work process is to make use of the correct equipment. This encompasses a range of items, from the type of shelving and racking you have, to the lifting equipment like forklifts to move materials.” – Improve Warehouse Efficiency Today with These Easy Tips, Krost Shelving & Racking; Twitter: @Krost_Shelving
44. The random organization method makes better use of all available space. “The Random method places inventory where ever it fits. The fixed method, on the other hand, has designated locations for each product. This second system can be more organized, but can also produce a lot of wasted space.” – Modern Rules of Warehouse Efficiency, Pallet Rack Now; Twitter: @PalletRackNow
45. ABC grouping helps to optimize product placement. “E-commerce retailers can very likely identify a small portion of their inventory that is more frequently picked and shipped than the rest. These golden tickets to profit are being shipped more often, and need to be in stock more consistently, than the vast majority of the remaining catalog. To make picking and counting these items easier (especially when using cycle counting), group your inventory into three categories: A for your top sellers, B for your above-average sellers, and C for your below-average sellers. Then, arrange your picking floor so that your team has the easiest access to A SKUs, then B SKUs, and finally C SKUs.” – 5 Warehouse Organization Tips for Ecommerce Retailers, SKULabs; Twitter: @skulabs
46. Ensure that fast-moving products are within an arm’s reach. “The second strategy to deploy for efficient warehouse operations is to use the right storage options. Seldom would you think that the storage containers holding your merchandise could, in fact, be slowing down your operations. Yet, when employees have to dig through storage containers and bins as products tip off shelves, there has to be a better way to store your items. Fast-moving items that move in bulk can be kept in cartons and pallet racks on the floor level for easy handling when placed into the store or out to delivery trucks. Items that are slow movers can be put in the appropriate bins on shelves.
“Always select the storage options that are the best fit for the types of products that you sell. Also, keep in mind that warehouse staff can have a faster time fulfilling orders for in-demand products when the items are in arm’s reach. Storing merchandise at waist level allows the staff to “grab and go” when filling multiple orders. However, keep in mind that the weight of the item will also dictate where it is placed, as heavier products will need to be put on lower shelves or on pallets.” – Denny Hammack, President, Patterson Pope, Top 5 Ways for a More Efficient Warehouse Operation, Supply Chain Brain; Twitter: @SCBrain
47. Focus on reducing handling and touches. “The fewer times that your workforce has to touch the product, the lower your overall costs of fulfilling orders is. Work on streamlining your processing in order to lower your costs.” – Tips and Tricks for Saving Money In Your Warehouse, Used-PalletRack.com
48. When you think you’re at your working capacity, you’re probably not. “Working capacity is how much storage a space can hold based on the configuration of the physical space and inventory characteristics, such as the size and shape of items. Most businesses think their storage facility is running at full capacity when in reality, it’s probably around 60 to 80 percent. Failure to run a warehouse at full working capacity costs a business money, especially if a second facility is purchased or rented to handle overload from a warehouse that isn’t even at working capacity.” – Effective Warehouse Space Matters to the Bottom Line, Brendamour Warehousing
49. Even the best racking systems can become inefficient if not maintained. “Keep it organized and clean. Junk must not be allowed to accumulate in your warehouse. Setting a cleaning schedule, on top of demanding a clean warehouse allows quicker and easier movement for both your employees and your machines. You may even find some missing or misplaced orders.” – 5 Tips for a More Efficient Warehouse, Lift Incorporated; Twitter: @Liftincorpor
50. Keep your warehouse in logical order after initial setup with ongoing optimization and prioritization efforts. “An orderly warehouse is a profitable warehouse. Picking operations, whether run from your garage business or a multi-location operation, are the lifeblood of your business. With less traditional businesses taking up brick and mortar retail spaces, and more organizations opting to sell only online, a logically laid-out warehouse can lessen cost and bolster the bottom line. Re-assess your process and warehouse configurations for efficient order picking and shipping.
Our sales engineers are experts in automatic asset tracking, tagging and identification,a nd can answer all your questions. Get in touch now.
Lets Talk ›Enter your information and get a free checklist of the top questions to answer and tips to plan a successful asset tagging project for any warehouse management system implementation.