5 Asset Maintenance Management Best Practices
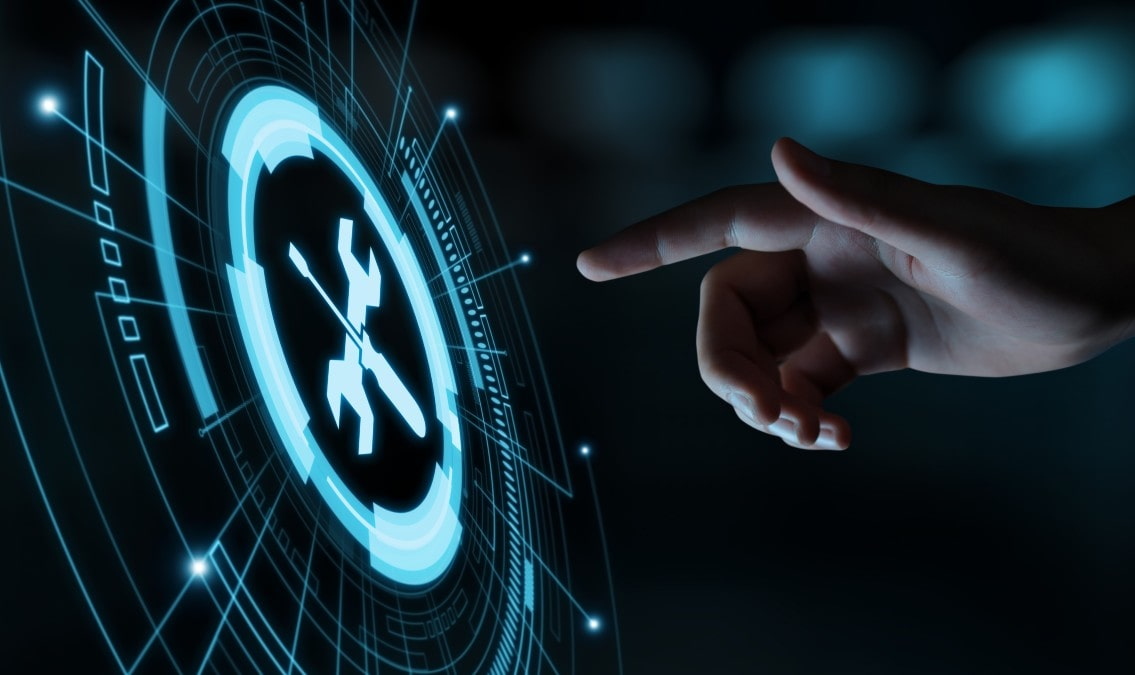
What do factories, machine shops, and warehouses all have in common? The need for asset maintenance management. In fact, managing the servicing cadence of a facility’s many tools, machines, and equipment is a major focus of any logistics or manufacturing firm.
Were it not, equipment could fail, work could be halted, and the supply of a firm’s goods or services could slow to a trickle. In short, poorly maintained equipment can cost a business much more in the long run than regular servicing ever would.
Performing timely maintenance on countless disparate assets can feel daunting, especially as pulling even just one piece of equipment off the floor for service can impact operations.
This is where asset maintenance management, or AMM, comes in. AMM is focused on finding efficient, cost-effective ways to balance an asset’s service needs with a company’s business demands.
The execution of this will vary depending on a company’s size, scale, industry, and other various factors, but several best practices are widely applicable no matter whether your business builds widgets, machines parts, or stockpiles goods.
If you’re looking to establish an AMM plan that saves your firm time and money, check out the following tips, strategies, and best practices.
Before you begin developing an asset management plan, it’s best to become familiar with the relevant, widely recognized standards governing the creation of such frameworks.
The authoritative literature on this topic is extensive, from foundational SAE International texts that cover concepts like reliability-centered maintenance to key standards published by the International Organization for Standardization, commonly known as ISO.
The ISO 5500 series standards may be the best place to begin your research. There are three core standards that nest within the series:
If you’re building a new AMM plan, read, learn, and know these standards, along with any other official literature relevant to your particular industry. Working off proven methodology is an excellent way to set yourself up for success.
KPIs, or key performance indicators, are benchmark metrics you can measure success against. Setting effective KPIs that can quantify and measure AMM performance is just as important to a business as establishing expectations around productivity, output, efficiency and other common success indicators.
There are several KPIs that can be used to gauge the efficacy of an AMM, both at the general and asset-specific level. Three examples include:
Asset Age vs. Performance: A metric that plots asset age against their utility. It’s useful to help determine if an aging asset should be repaired or replaced.
Emergency Maintenance Rate: Does it seem like some machines in your facility unexpectedly break down more than others? The EMR, which tracks the frequency of unplanned maintenance, can either prove or refute that hunch.
Mean Time Between Failures: The MTBF measures exactly what the name suggests: the average elapsed time between any kind of breakdown or failure. Like the EMR, it helps quantify asset reliability and can help you identify unreliable equipment.
Check out the video below to learn a little more about asset KPI’s.
For many companies, most of their assets can likely be categorized into one of a handful of asset classes. A fleet of fifty different trucks may bucket into a ‘vehicles’ category, for instance.
It’s a similar story for any like-kind machinery or equipment. Classifying assets like this can help you better track the maintenance needs and KPIs for a specific set of machines. After all, the company trucks have very different servicing needs than warehouse forklifts or factory tooling equipment.
For effective classification, group assets with an eye toward data collection and maintenance simplification. Usually this means grouping by asset type, like our truck example above. The benefits of doing so can include better lifecycle planning, performance tracking, and cost control.
If there’s one takeaway from this piece, let it be this: digitize and automate as much of the maintenance management process as you can.
There are several tools to make doing so a cinch, including computer maintenance management systems, telematics software, and enterprise asset management programs.
These all-in-one solutions can track data against your KPIs, send out maintenance reminders, schedule work orders, and even improve regulatory compliance. Many can do all this almost on autopilot, saving you significant time and money.
You don’t have to upgrade your existing machinery to play well with asset management software, either – all you need is a high-quality asset tag with a unique identifier that can be affixed to each machine.
By embossing each label with a barcode or QR code, equipment users or technicians can simply scan the tag and digitally add or update any records. The system will build a real-time log for each asset that can quickly be accessed by management when needed.
This just scratches the surface of what these systems can do. If you’re still tracking service and repairs manually on Excel, buy yourself back countless hours of time and upgrade to one of these game-changing software solutions.
Preventive and predictive maintenance are two popular strategies in the AMM toolbox.
Why? Credit their proven success in minimizing unexpected repairs and increasing asset life. It’s just like the old adage says: an ounce of prevention is equal to a pound of cure.
Manufacturing companies understand this well, as 88% use preventive maintenance. Predictive maintenance is just as important, with the market for it projected to reach $23.5 billion by 2024.
What’s the difference between the two approaches?
In short, preventive maintenance focuses on completing services according to an asset’s recommended maintenance schedule. Predictive maintenance uses real-time indicators from sensors, analytics, and other technologies to try and predict when maintenance or repairs are due.
The two strategies complement each other; preventive maintenance helps establish baseline reliability, while predictive maintenance can help mitigate surprise repairs and downtime. Both have a place in the AMM strategy book.
Your AMM plan will ultimately be as unique as your business itself, but you’ll find your best success by implementing what we’ve suggested here. These tips all draw from strategies that have been made popular for good reason: they work, and can often help firms save money, find efficiencies, and lengthen asset lifespans in the process.
Establishing your maintenance plan may not be as arduous a process as you might expect, either: you can get started with some top-rated asset tags, a quality software solution, and a well thought-out game plan. Before you know it, you’ll have supercharged your maintenance game.
Asset Maintenance Management Best Practices involve preventive maintenance, predictive maintenance, and condition-based monitoring. Prioritizing safety, reliability, and efficiency, it includes regular inspections, timely repairs, and data-driven decision-making to extend asset lifecycles.
Start by documenting asset information, setting maintenance schedules, and utilizing computerized maintenance management systems (CMMS). Train your staff, establish KPIs, and continually analyze data for process improvement.
Implementing these practices can reduce downtime, lower operational costs, increase asset reliability, and enhance safety. It also aids in regulatory compliance, optimizes resource allocation, and supports sustainability goals.
Our sales engineers are experts in automatic asset tracking, tagging and identification,a nd can answer all your questions. Get in touch now.
Lets Talk ›Enter your information and get a free checklist of the top questions to answer to plan a successful asset tagging project for any maintenance tracking or facility management system.