What Is Facility Management in the Construction Industry?
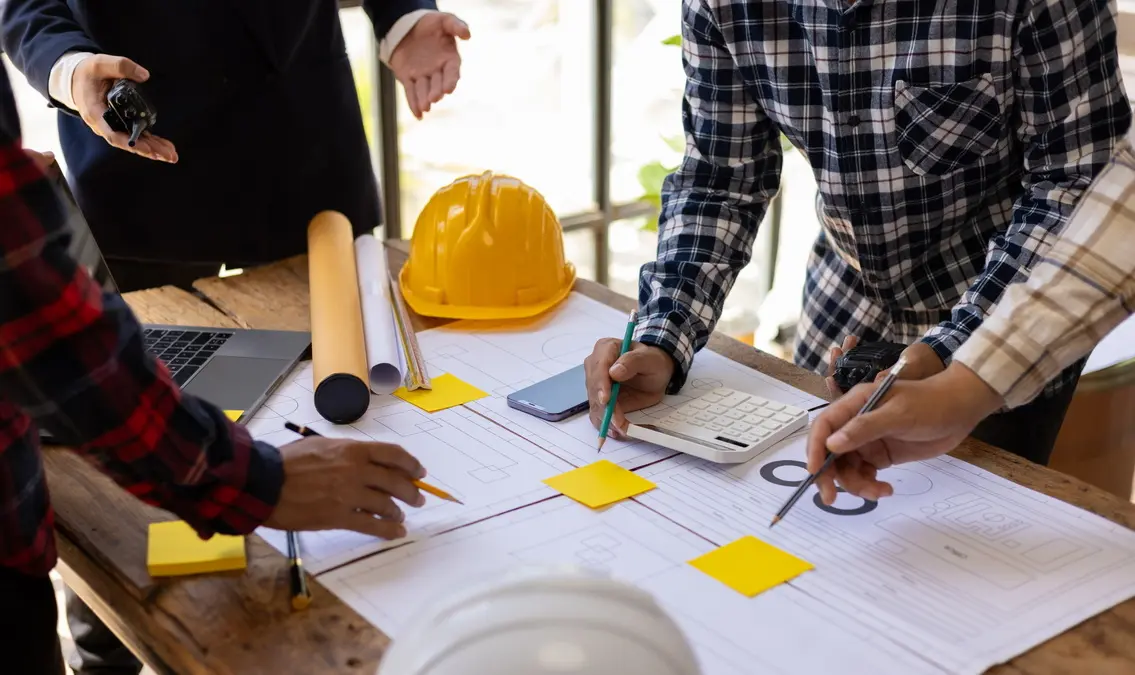
Successful construction companies know how to balance employee labor, budgeting, timeline management, and safety in all projects. However, high-quality service doesn’t end after the building is complete.
The construction process plays a crucial role in facility management, ensuring that buildings operate efficiently long after construction ends.
Facility management in the construction industry provides a proactive, experience-first approach to optimize a facility’s longevity. The discipline requires proactive maintenance, energy efficiency, compliance, technology, and user experience.
Learn how facility management plays a role in construction and three best practices for integrating facility management with every construction project.
Facility management is a key consideration during the construction process. Builders who consider the facility’s management create a space designed for optimal operations and maintenance after construction ends.
From that point on, facility management tends to the building, ensuring its systems and physical spaces function well and last a long time.
Facility management in construction covers a wide range of responsibilities, including:
Failing to consider facility management during construction can lead to a slew of issues. For example, if the client has difficulties maintaining a poorly designed HVAC or plumbing system, they’re unlikely to recommend the construction company.
In some cases, poor design requires additional fixes, driving up the cost of building the new facility — which the client may sometimes ask the construction business to cover.
The best approach is for construction providers to consider all aspects of facility management. Clients should communicate their needs early on, ideally during the design phase, to ensure effective facility management, although construction teams are also responsible.
Facility management should be a primary concern during the design and construction phase. Follow these best practices to ensure the facility is easy to manage for years to come.
Construction providers must work with their clients to ensure the built environment accommodates simple, hassle-free maintenance. The easier it is for maintenance teams to keep up with a building, the longer its systems will last.
For example, that might require installing PEX plumbing over traditional metal pipe, which is more complex and expensive to maintain over time. Opting for smooth walls that are easier to wipe down also makes sense in food service or healthcare.
Facility labels are crucial for tracking equipment and tools, but they’re also helpful for providing directions, organizing equipment, and sharing safety information. Labeling may seem minor, but it’s the best way to ensure employees understand how to navigate their new building.
Camcode’s durable labels and tags are perfect for any environment, whether you’re building a school or a marina. Not only do we make tags out of durable materials, but our fasteners and adhesives ensure your labels last up to 20 years.
Building technology is relatively new, but it’s an exciting addition during the construction process that can streamline facility management. That might include adding leak detectors in critical areas, which help facility managers identify leaks much sooner.
Some facilities now include “report card” screens, which display the building’s carbon emissions, water usage, and other sustainability metrics.
Facility management is a crucial part of keeping buildings in peak condition. New construction is the perfect opportunity to design long-lasting buildings with proper management in mind.
Follow the best practices in this guide to keep facility management top-of-mind in all of your construction projects, ensuring client satisfaction and employee safety.
Labels and tags help employees navigate buildings, share instructions on using heavy machinery, and track assets. These tags make it simple to quickly identify equipment, which reduces errors and improves employee safety.
Integrating technology, like facility management software, allows for real-time maintenance tracking, workflow automation, and equipment monitoring. This improves decision-making, reduces costs, and streamlines operations.
Facility managers regularly conduct audits to comply with building regulations. They also inspect equipment, like fire extinguishers, to ensure they’re effective and well-maintained. Implementing safety signage and labels helps workers quickly identify hazards and comply with safety protocols.
Our sales engineers are experts in automatic asset tracking, tagging and identification,a nd can answer all your questions. Get in touch now.
Lets Talk ›Enter your information and get a free checklist of the top questions to answer to plan a successful asset tagging project for any maintenance tracking or facility management system.