How to Perform a Better Utility Inspection
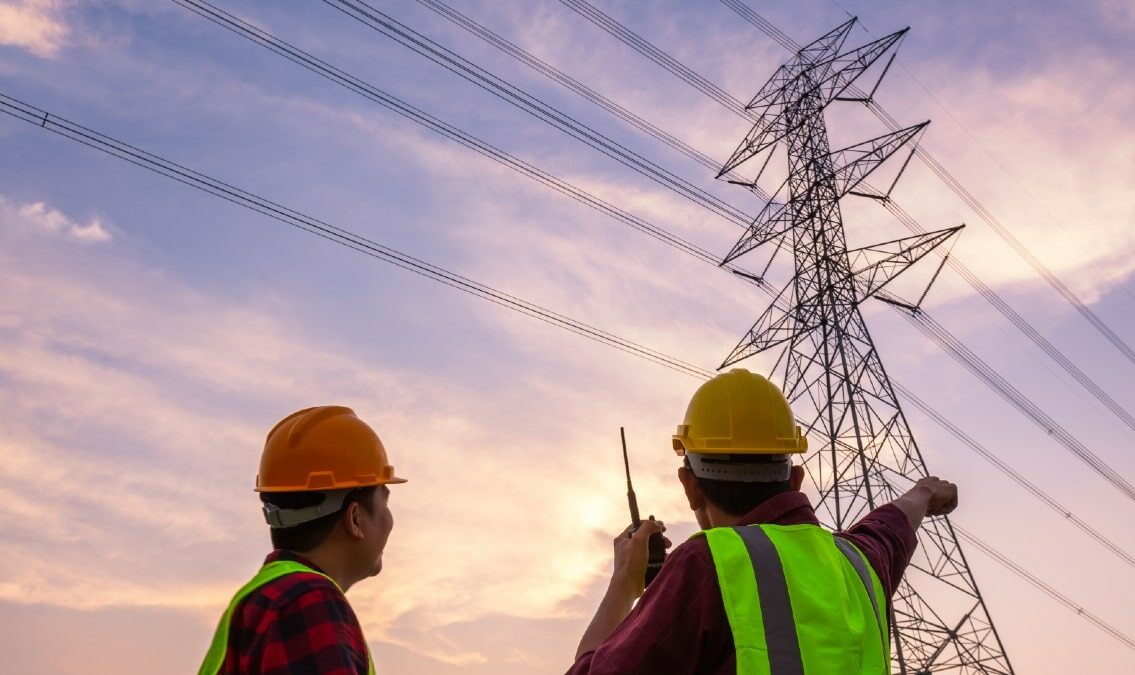
Utility infrastructure is the invisible engine of modern life. Natural gas pipelines funnel precious fuel across untold miles, bringing heat and warmth to far-flung towns and cities. Telephone poles hug the shoulders of nearly every main and secondary road in America.
All of this infrastructure is critical to the continued operation of the energy grid. And while Mother Nature is often the cause of disruptions to power and fuel deliveries, aging utility equipment also plays a factor in the infrastructure’s reliability. Neglect the physical assets comprising a utility operation and you could quite literally leave your customers cold and in the dark.
Utility inspections can dramatically reduce the odds of such scenarios, but these are often time-consuming, expensive, and irregular. So, how can you perform better utility inspections that are both more effective and affordable? Answering that question starts by determining what your utility inspections should be looking for in the first place.
An effective utility inspection should assess the infrastructure for a variety of possible risk factors, security concerns and performance issues.
Traditionally, these asset reviews are done in-person by utility inspection teams. Trained and employed by either the utilities companies themselves or by contracting agencies, inspectors travel the territory covered by their employer or client, working their way across the landscape to lay eyes on energy assets. Here’s what a qualified inspector should look for:
Of course, this is a generic list – specific utilities will require their own unique checklists when undergoing review. A municipal water line, for instance, will be inspected using a much different set of guidelines than a rural transmission tower. That leads us to our first point of advice for improving your utility inspections:
Because different utilities require different inspection approaches, you want to work with trained, qualified inspectors who are trained on the specific assets you need assessed. Someone trained to inspect gas pipelines likely lacks the qualifications and experience to do the same for green energy assets. Those familiar with assessing substations and transformers probably aren’t the best suited for determining the condition of neighborhood telephone poles.
As for how to find the right inspector for your needs, don’t be afraid to dig into a candidate’s qualifications. Many utility inspectors boast specialized certifications related to their specific field of interest, while other inspection service providers and utility companies require their staff to take relevant safety and training courses.
Potential classes and certifications worth vetting for include:
These are four of countless courses and certifications that are relevant to the utility inspection industry. With a bit of research, you’ll find the certifications relevant to both the inspection you’re looking to perform and your state or region.
One last point: although certified inspectors may cost more upfront – whether through in-house training efforts or contracted service fees – they represent a caliber of better-trained, more effective professionals that can be trusted to deliver detailed, accurate, and timely results. As a result, that extra investment is worth every penny.
Modern technology has transformed how physical utility inspections are completed. In the old days, inspection teams had to visit every standalone energy asset physically. That could have meant a helicopter ride up the side of a mountain or a long, desolate drive into the remotest deserts. And while visits to far-flung, hard-to-reach and remote utility facilities haven’t totally disappeared, the task has gotten far easier with the advent of modern tools — particularly drones.
When equipped with the right cameras, a well-piloted drone can get up close and personal with an asset and record its condition in high-definition. That footage then gets reviewed by human operators, who’ll judge whether or not a tower requires further in-person inspection.
Drones are everything a human inspector is not: cheap, fast, objective, observant, and not afraid of heights. If you’re an electric utility provider and need to inspect a series of towers strung along a mountain pass, do you hire a trained team to spend a few days flying or hiking in order to scale each one? Or, do you use a drone operator to complete the same task in a safer and more effective manner, all in the span of a single shift? For most utility managers, the answer is an easy one.
It’s important to note that drones and other technologies work best when paired with physical asset tags as part of an asset management strategy. These tags not only provide pertinent information, such as the date of the last inspection or asset serial number, but they can also play an important role in public knowledge and safety.
For example, if a power company receives a report that a tree has fallen on nearby power lines, they can share the information taken from the nearest pole tag with their utility representative. The utility pole identification system makes it easy for the dispatcher to send a maintenance crew to the right location. Maintenance crews can also easily confirm that they’re working on the correct asset and document the maintenance and repairs completed without time-consuming manual documentation.
By augmenting proven solutions like asset tags with the latest digital technology, utilities can perform better inspections while saving money and reducing the number of expensive, time-consuming, in-person site visits. It’s the ultimate win-win.
Lastly, set a regular cadence for inspections. Exact laws governing how often to perform inspections vary based on state regulations, utility type, and other factors, but it’s imperative from a legal and safety standpoint that you abide by these relevant guidelines. If a neglected section of pipeline fails, any resulting damage could lead to legal trouble. And even if there’s no collateral damage, such a failure could lead to increased scrutiny, fines, audits, and other repercussions – not to mention the ethicality of letting critical utilities go too long without a routine inspection.
To combat this, devise a schedule for reviewing your utility assets that’s in compliance with local laws. You should also consider factors like an asset’s expected lifespan, its susceptibility to natural forces like vegetation, weather, or erosion, and its relative importance within your utility’s greater infrastructure ecosystem. A telephone pole may only need to be inspected every ten years, while a transformer or substation will want to be assessed more frequently.
Whether you’re assessing solar panels or testing pipeline performance, by implementing all the strategies outlined here, you’ll be well on your way to better utility inspections.
Our sales engineers are experts in automatic asset tracking, tagging and identification,a nd can answer all your questions. Get in touch now.
Lets Talk ›Enter your information and get a free checklist of the top questions to answer and tips to plan a successful asset tagging project for any asset management or tracking system implementation.